All Features
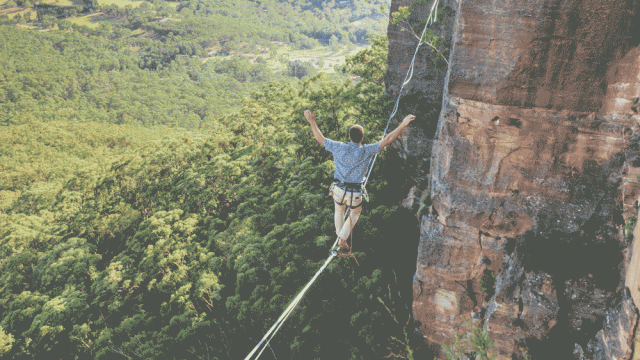
Michael Mills
Risk-based thinking—it sounds easy. How hard can it be to think about risk? But did you know that the phrase “risk-based thinking” was only invented in 2015?
Did you know that the ISO says “risk-based thinking” is one of the foundations of quality management, but never defines it? Or that it…
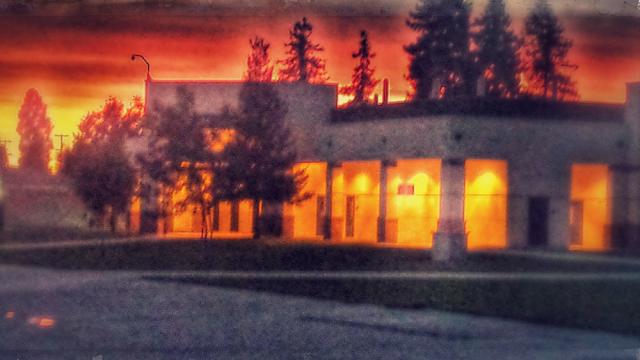
William A. Levinson
The International Accreditation Forum (IAF) and ISO have published a joint communiqué to require organizations to “consider” climate change in the context of risks and opportunities relevant to the management system.
Although this is pursuant to the London Declaration, which has goals for…
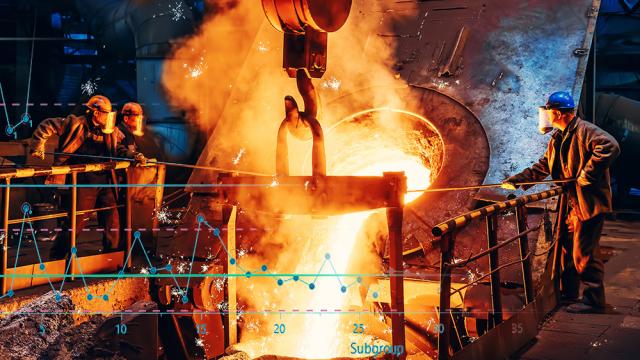
Scott A. Hindle
Walter A. Shewhart is lauded as the Father of Statistical Process Control (SPC) and is perhaps best remembered for the SPC control chart. The first record of Shewhart’s control chart is found in a Bell Telephone Laboratories internal memo from May 16, 1924, making today the 100th anniversary of…
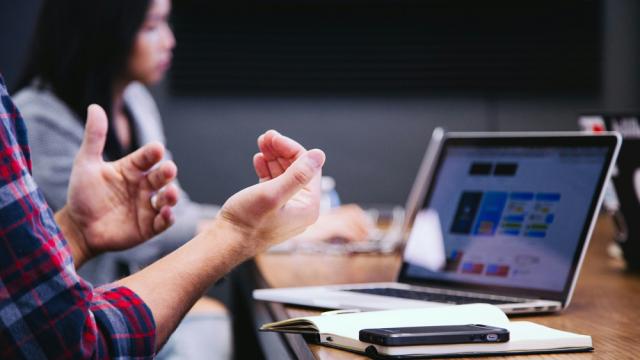
Stephanie Ojeda
An analysis of U.S. Food and Drug Administration (FDA) warning letters by the Food and Drug Law Institute reveals a perhaps not-so-surprising link between training gaps and FDA violations.
It’s one of several factors motivating companies to switch to automated training management software. The…
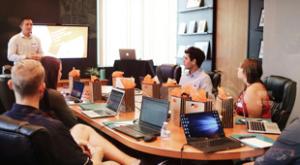
Mark Rosenthal
Continuing on the theme of value stream mapping (and process mapping in general) from my article “Where is your value stream map?”, I outlined the typical scenario: The map is built by the continuous improvement team, and they are the ones primarily engaged in the conversations about how to close…
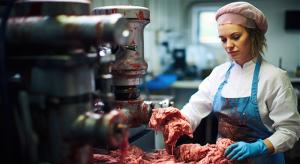
Scott A. Hindle, Douglas C. Fair
So far in this series our focus has remained on statistical process control (SPC) in manufacturing. We’ve alternated between more traditional uses of SPC that remain relevant in this digital era and discussing uses of SPC and its related techniques that are enabled by the marvels of modern…
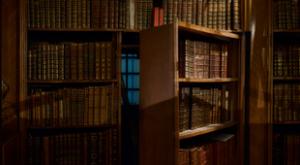
Adam Grant
Nano Tools for Leaders—a collaboration between Wharton Executive Education and Wharton’s Center for Leadership and Change Management—are fast, effective tools that you can learn and start using in less than 15 minutes, with the potential to significantly affect your success and the engagement and…
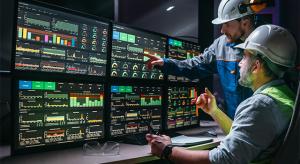
Scott A. Hindle, Douglas C. Fair
You are assigned a new task to demonstrate that an existing process will have the capability to meet newer and tighter specifications. The change in specifications for critical-to-quality characteristic P is due to new regulatory requirements; hence, the specifications must be met. The task is…
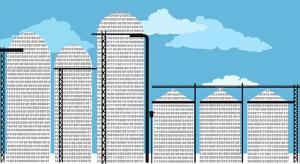
Douglas C. Fair, Scott A. Hindle
Just a few decades ago, today’s personal technology was a science fiction pipe dream. Powerful computers (smart phones) that fit in our pockets; global positioning satellites for our traveling convenience; and homes where lights, security systems, and locks can be controlled remotely. It’s all just…
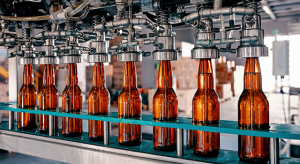
Scott A. Hindle, Douglas C. Fair
Parts 1, 2, and 3 of our series on statistical process control (SPC) have shown how data can be thoughtfully used to enable learning and improvement—and consequently, better product quality and lower production costs. Another area of SPC to tap into is that of measurement methods. How do we ensure…
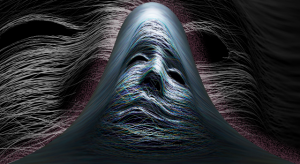
Donald J. Wheeler
Fourteen years ago, I published “Do You Have Leptokurtophobia?” Based on the reaction to that column, the message was needed. In this column, I would like to explain the symptoms of leptokurtophobia and the cure for this pandemic affliction.
Leptokurtosis is a Greek word that literally means “thin…
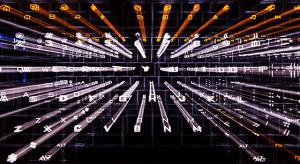
Douglas C. Fair, Scott A. Hindle
Data overload has become a common malady. Modern data collection technologies and low-cost database storage have motivated companies to collect data on almost everything. The result? Data overload. Unfortunately, few companies leverage the information hidden away in those terabytes of data.
There…
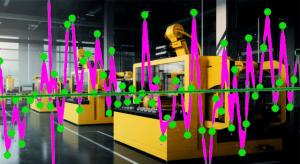
Scott A. Hindle, Douglas C. Fair
We are one year away from the 100th anniversary of the creation of the control chart: Walter Shewhart created the control chart in 1924 as an aid to Western Electric’s manufacturing operations. Since it’s almost prehistoric, is it now time to leave the control chart technique—that started out using…
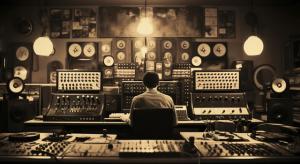
Donald J. Wheeler
In last month’s column, we looked at how process-hyphen-control algorithms work with a process that is subject to occasional upsets. This column will consider how they work with a well-behaved process.
Last month we saw that process adjustments can reduce variation when they are reacting to real…
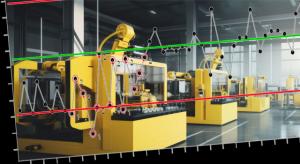
Douglas C. Fair, Scott A. Hindle
Today’s manufacturing systems have become more automated, data-driven, and sophisticated than ever before. Visit any modern shop floor and you’ll find a plethora of IT systems, HMIs, PLC data streams, machine controllers, engineering support, and other digital initiatives, all vying to improve…
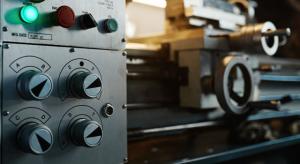
Donald J. Wheeler
Many articles and some textbooks describe process behavior charts as a manual technique for keeping a process on target. For example, in Norway the words used for SPC (statistical process control) translate as “statistical process steering.” Here, we’ll look at using a process behavior chart to…
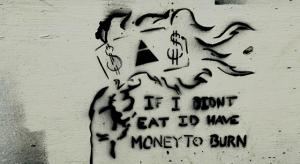
William A. Levinson
Inflation is a serious national issue. Credit agency Fitch Ratings just downgraded the U.S. credit rating—as in the “full faith and credit of the United States”—from AAA to AA+.1 This doubtlessly reflects the fact that our national debt exceeds $31 trillion, or almost $100,000 for every American,…
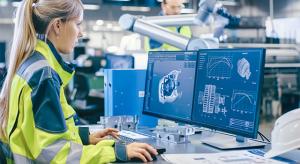
Donald J. Wheeler
As we learned last month, the precision to tolerance ratio is a trigonometric function multiplied by a scalar constant. This means that it should never be interpreted as a proportion or percentage. Yet the simple P/T ratio is being used, and misunderstood, all over the world. So how can we properly…
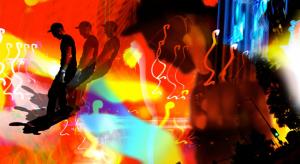
Donald J. Wheeler
The keys to effective process behavior charts are rational sampling and rational subgrouping. As implied by the word rational, we must use our knowledge of the context to collect and organize data in a way that answers the interesting questions. This column will show the role that sample frequency…
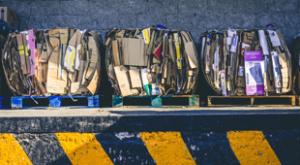
Paul Laughlin
Continuing our thinking about ways for data leaders to save money during a recession, this article drills into saving on your data usage. Following my last post reminiscing on the lessons I learned during past recessions, the early environmentalist slogan “reduce, reuse, recycle” has stayed in my…
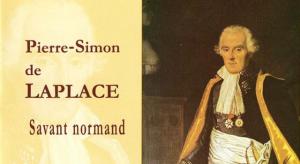
Donald J. Wheeler
As the foundations of modern science were being laid, the need for a model for the uncertainty in a measurement became apparent. Here we look at the development of the theory of measurement error and discover its consequences.
The problem may be expressed as follows: Repeated measurements of one…
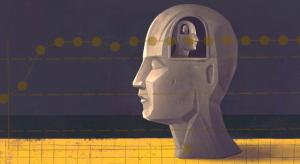
Donald J. Wheeler, Al Pfadt
In memory of Al Phadt, Ph.D.
This article is a reprint of a paper Al and I presented several years ago. It illustrates how the interpretation and visual display of data in their context can facilitate discovery. Al’s integrated approach is a classic example not only for clinical practitioners but…
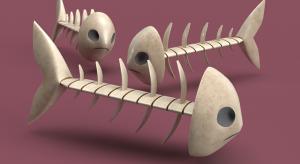
Alan Metzel
Almost seven years ago, Quality Digest presented a short article by Matthew Barsalou titled “A Worksheet for Ishikawa Diagrams.” At the time, I commented concerning enhancements that provide greater granularity. Indicating that he would probably have little time to devote to such a project,…
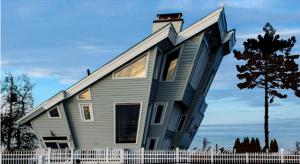
Donald J. Wheeler
The computation for skewness does not fully describe everything that happens as a distribution becomes more skewed. Here we shall use some examples to visualize just what skewness does—and does not—involve.
The mean for a probability model describes the balance point. The standard deviation…
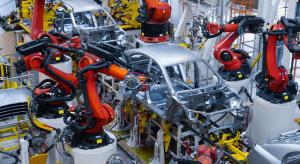
William A. Levinson
Corrective action and preventive action (CAPA) is probably the most important process in any quality management system because so much else depends on it. This includes not only its traditional role as a response to defects, nonconformances, customer complaints, and audit findings, but also outputs…
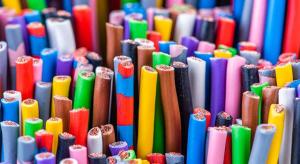
Donald J. Wheeler
The cumulative sum (or Cusum) technique is occasionally offered as an alternative to process behavior charts, even though they have completely different objectives. Process behavior charts characterize whether a process has been operated predictably. Cusums assume that the process is already being…
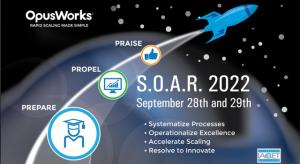
OpusWorks
Over two days, engage in eight unique best practice sessions with 11 process improvement and thought leaders at S.O.A.R. 2022, OpusWorks’ annual virtual conference.
Designed to present highly actionable information and game-changing strategies from highly experienced and inspiring human beings, S.O…
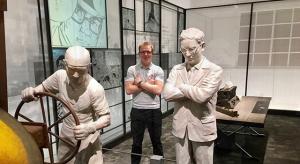
Harish Jose
In today’s column, I’m looking at the Ohno Circle in light of German philosopher Martin Heidegger’s ideas. I’ll try to stay away from the neologisms used by Heidegger and will only scratch the surface of his deep insights.
One of the best explanations of the Ohno Circle comes from one of Taiichi…
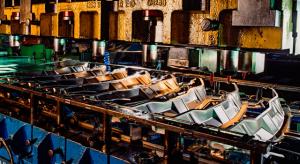
Richard Harpster
On Dec. 7, 2021, Ford Motor Co. updated its IATF 16949—“Customer specific requirements” (CSR), which require the use of reverse FMEAs (RFMEA) on new equipment (“tooling”). The first sentence of the reverse FMEA requirement reads: “Organizations are required to have a process in place that ensures…
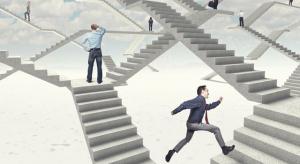
Donald J. Wheeler
Many different approaches to process improvement are on offer today. An appreciation of the way each approach works is crucial to selecting an approach that will be effective. Here we look at the problem of production and consider how the different improvement approaches deal with this problem.…
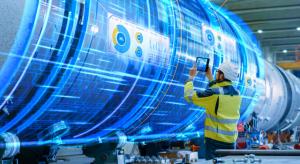
James J. Kline
Big data is a relatively new phenomenon. Its use is increasing in many organizations. But, as with many new processes, its use cuts both ways. It has positive benefits to both the organization and customers. It also has its potential downside. This piece looks at both with respect to the quality…
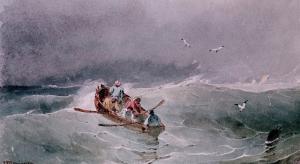
Donald J. Wheeler
Students are told that they need to check their data for normality before doing virtually any data analysis. And today’s software encourages this by automatically providing normal probability plots and lack-of-fit statistics as part of the output. So it’s not surprising that many think this is the…

Brittney McIver
At some point, every medical device company will encounter an issue that requires an internal investigation. Whether it’s due to a nonconformance, complaint, CAPA, or an audit issue, you’ll have to conduct a failure or root cause investigation to pinpoint why the issue occurred in order to resolve…
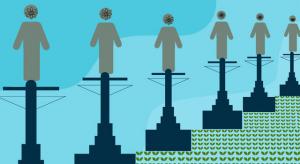
Anthony Tarantino
In 2007, Nassim Taleb described black swans as highly improbable events that had dramatic or even catastrophic effects on markets and economies. Until recently, it seemed that such events were indeed rare.1 There’s now a major rethinking with the world entering the third year of the Covid-19…
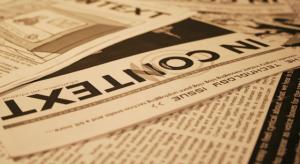
Scott A. Hindle
In 2010, new to the world of statistical process control (SPC), I was intrigued by Don Wheeler’s statement that “No data have meaning apart from their context” (from his book, Understanding Variation—The Key to Managing Chaos, SPC Press, 2000, available on Amazon). For a while, I didn’t really get…
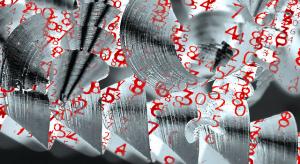
V R Vijay Anand
As the world moves toward a new, post-pandemic normal, industries must leverage digital transformation at an accelerated pace. This is already happening. According to IBM, 67 percent of manufacturers have accelerated digital projects since Covid-19.
Although improved operational efficiency is…
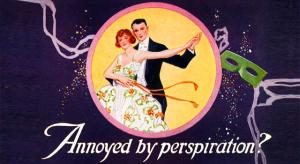
Donald J. Wheeler
Last month we looked at analyzing observational data. Here we will consider experimental data and discover a weakness in the way they are obtained that can contribute to the problem of nonreproducible results.
Background
The discipline of statistics grew up in agricultural and biomedical research…
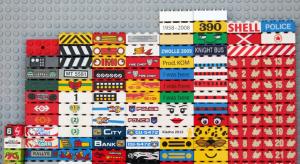
Donald J. Wheeler
Most of the world’s data are obtained as byproducts of operations. These observational data track what happens over time and have a structure that requires a different approach to analysis than that used for experimental data. An understanding of this approach will reveal how Shewhart’s generic,…
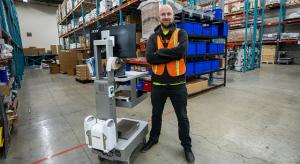
Cameron Shaheen
With the holidays fast approaching, manufacturers, distribution centers, and e-commerce providers are working to meet growing customer demand, while also navigating severe supply-chain disruptions and mounting labor shortages. At this point, we all had hoped to have the devastating effects of the…
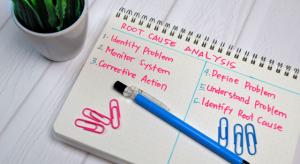
David Isaacson
Within every organization, problems or incidents arise that can affect the quality of your operations. Take for example, food recalls due to improper food labeling that not only could cause sickness in humans, but also result in a hit to a company’s reputation. Or, automotive product recalls due to…
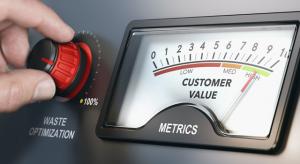
David Cahn
Lean Six Sigma has improved manufacturing operations and processes for years now. Now the effect of the methodology is extending to supply chain and operations to help eliminate waste and reduce variation. Using lean to eradicate waste and Six Sigma to eliminate defects by reducing process…
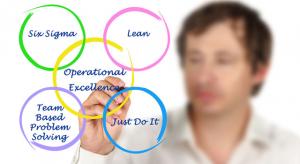
James Wells
I was talking recently with a friend who runs an academic program at a major U.S. university. She was telling me about solving a problem in her department and how the solution was obvious so she just did it. She then related how one of her colleagues protested that she should have used some Six…
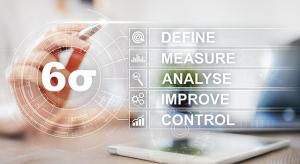
Gregg Profozich
Welcome to the third installment of our series on lean and Six Sigma. As we saw in the first article, lean and Six Sigma are complementary continuous improvement methodologies that reduce the overall waste and variability, respectively, in production processes. The second article went into some…
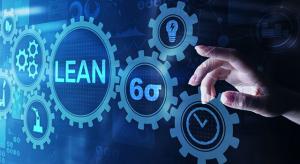
Gregg Profozich
The manufacturing world, across industry sectors, has witnessed significant improvements in productivity and competitiveness during the past couple of decades as a result of continuous improvement (CI) methodologies. Two of these methodologies that are recognized as having broad applicability are…
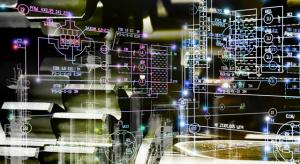
Jay Arthur—The KnowWare Man
There are two ways to increase profits: increase sales or reduce costs. Although most data analysis seeks to find more ways to sell more stuff to more people, addressing preventable problems is an often overlooked opportunity. Preventable problems consume a third or more of corporate expenses and…
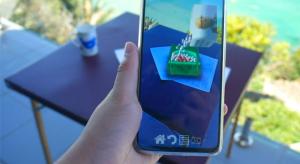
Anthony D. Burns
Augmented reality (AR) means adding objects, animations, or information, that don’t really exist, to the real world. The idea is that the real world is augmented (or overlaid) with computer-generated material—ideally for some useful purpose.
Augmented reality has been around for about 30 years.…
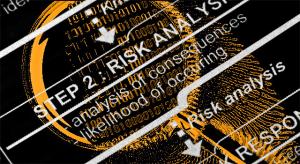
Tom Taormina
After more than 50 years as a quality control engineer and having worked with more than 700 companies, it is my observation that the vast majority of quality professionals hold their prime directive to be reducing defects to the lowest acceptable level by minimizing process variability. Most of us…
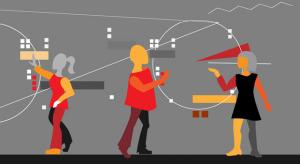
Michael Popenas
Product development (PD) is the life blood of a company’s success and is the process for innovation. Today, product life cycles are shrinking due to an ever-increasing number of competitive and disruptive products coming to market quicker.
To stay in business, a company’s PD needs to become more…
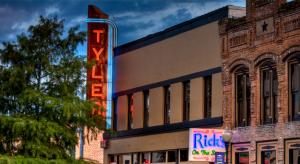
James J. Kline
In today’s coronavirus environment, governments at all levels are under greater fiscal pressure. For instance, Oregon’s governor has told state departments to prepare for a 12-percent reduction in their budgets. Given this environment, perhaps it is time to reexamine an established approach to…
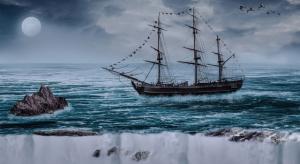
Greg Hutchins
My recent epiphany was that the lens for all work and even for everyday living during the next few years will be risk-based. Why do I make this case?
In January 2020, my company was selected to participate in the largest pitch fest in the Northwest, TechfestNW, which was originally scheduled for…
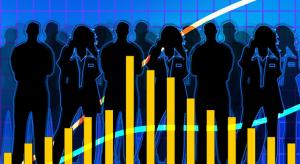
Ryan Ayers
Data are valuable assets, so much so that they are the world’s most valuable resource. That makes understanding the different types of data—and the role of a data scientist—more important than ever. In the business world, more companies are trying to understand big numbers and what they can do with…
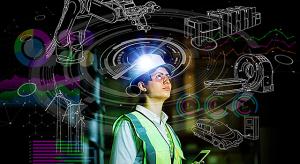
Taran March @ Quality Digest
What is quality intelligence, exactly? It’s more than marketing spin. More, even, than the sum of its many control charts. It’s not collecting data simply to further go/no-go actions. And it doesn’t mean turning the cognitive wheel entirely over to artificial intelligence, either—far from it.
We…
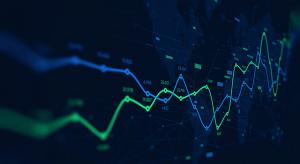
Ryan E. Day
An organization can achieve great results when everyone is working together, looking at the same information generated from the same data, and using the same rules. Changes can be made that affect a company’s bottom line through operational improvements, product quality, and process optimization.…
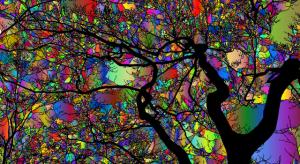
Ken Levine
Lean Six Sigma (LSS) professionals have an enormous opportunity to add value to organizations and to our communities during this coronavirus pandemic. We have the objective orientation, methods, and tools to help. Process improvement is currently more important than ever in this “new normal”…
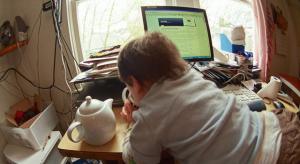
Gleb Tsipursky
So many companies are shifting their employees to working from home to address the Covid-19 coronavirus pandemic. Yet they’re not considering the potential quality disasters that can occur as a result of this transition.
An example of this is what one of my coaching clients experienced more than a…
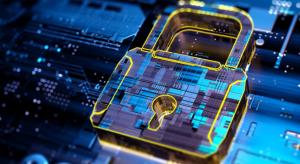
Celia Paulsen
Nobody likes business to be slow. If you’re in a fast-paced world like manufacturing, seeing your machines or employees idle can drive a person insane. If you’re used to your production line working to capacity and suddenly business slows down, it can be a frustrating time.
When I was in the U.S.…

Donald J. Wheeler, Al Pfadt
Each day we receive data that seek to quantify the Covid-19 pandemic. These daily values tell us how things have changed from yesterday, and give us the current totals, but they are difficult to understand simply because they are only a small piece of the puzzle. And like pieces of a puzzle, data…
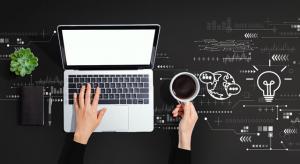
Ken Maynard
When educational and public sectors consider applying a proven method like lean Six Sigma, the perception persists that this “manufacturing program” will not work in a nonmanufacturing environment. Along with that limiting assumption, there is an underlying expectation within the service industry…
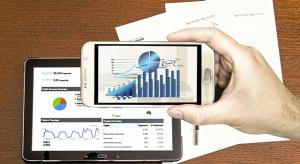
Jody Muelaner
The seven basic tools of quality are a standard set of graphical methods for improving quality. They can help with understanding variation and determining the root cause of errors in processes. The seven basic tools are most commonly used within lean manufacturing. All of the tools are graphical…
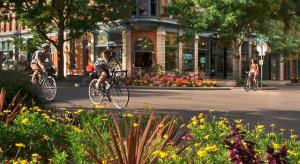
Dirk Dusharme @ Quality Digest
Government bureaucracies are inefficient. They waste taxpayer dollars, and they have no incentive to improve. We’ve all heard and probably repeated these axioms about wasteful government spending.
And it’s often true; you don’t have to look far to find examples of government overpaying for products…
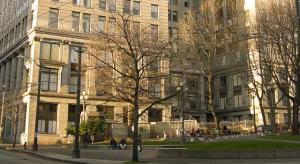
Ryan E. Day
Lean: an employee-championed method of waste reduction. Six Sigma: a robust method of defect reduction. Embracing both methods provides organizations with multiple tools for continuous improvement. Developed for manufacturing, lean Six Sigma has now been recognized by government agencies as a…
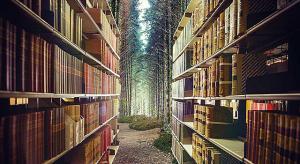
Taran March @ Quality Digest
At the University of California at San Diego, lean concepts have taken hold. Along with its process improvement curriculum, the university applies what it teaches through initiatives around campus. Projects both complex and simple tackle the snags, waste, and bottlenecks of academic life. Students…
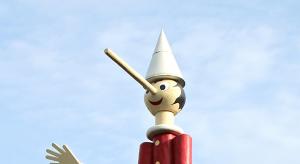
Ryan E. Day
Lean looks at ways to reduce waste and improve flow. The principles are relevant to virtually every organizational sector and vertical. It’s no surprise, then, that so many organizations tout lean and devote resources to lean initiatives. But, too often, there is a tendency for a company to promote…
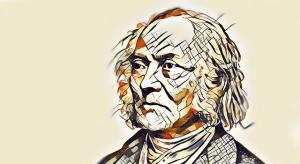
Harish Jose
In today’s column, I’m looking at Weber’s Law. It’s named after Ernst Heinrich Weber (born June 24, 1795, died Jan. 26, 1878), a German physician who was one of the pioneers of experimental psychology. I highly recommend the Numberphile YouTube video that explains this in detail.
A simple…
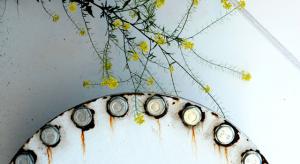
William A. Levinson
The Automotive Industry Action Group’s (AIAG’s) and German Association of the Automotive Industry’s (VDA’s) new Failure Mode and Effects Analysis Handbook (AIAG, 2019) offers significant advances over FMEA as practiced 15 or 20 years ago.1 The publication is definitely worth buying because the new…
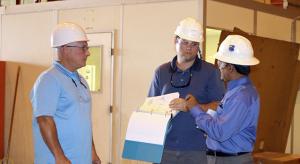
Paul Foster
If you’re new to layered process audits, it’s critical to make sure everyone on your team is on the same page with basic terms. Here we provide a guide of 16 essential terms to know when launching your LPA program and getting your team up to speed. Don’t forget to directly download your own copy of…
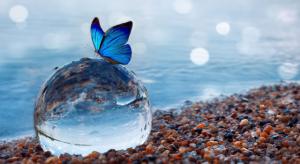
Dirk Dusharme @ Quality Digest
What a year.
No matter your job, your industry, or your political beliefs, this year has been a heck of a ride. The (still ongoing) trade war with China, manufacturing gains (and losses), the 737 MAX, Hong Kong riots, North Korea, Brexit, impeachment. What a mixed bag of ups and downs that has…
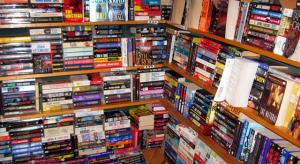
As usual with Quality Digest’s diverse audience, this year’s top stories covered a wide range of topics applicable to quality professionals. From hardware to software, from standards to risk management, from China trade to FDA regulations. It’s always fun to see what readers gravitate to, and this…
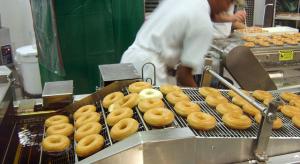
Harish Jose
It has been a while since I have written about statistics, and I get asked a lot about a way to calculate sample sizes based on reliability and confidence levels. So today I am sharing a spreadsheet that generates an operating characteristic (OC) curve based on your sample size and the number of…
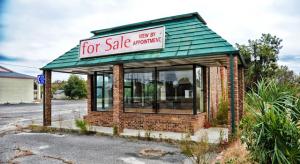
Frances Brunelle
Just as baby boomers on the manufacturing plant floor are getting ready to retire, so are the owners. More than 5,000 small manufacturing operations (with annual revenues between $2 and $20 million) will either close their doors or find new owners during the next five years.
Some of these owners…
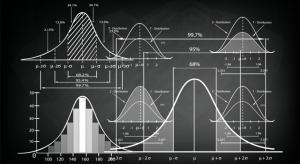
Donald J. Wheeler
In the past two months we have looked at how three-sigma limits work with skewed data. This column finds the power functions for the probability limits of phase two charts with skewed probability models, and compares the trade-offs made by three-sigma limits with the trade-offs made by the…
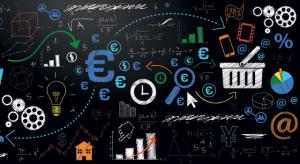
Anthony D. Burns
You’ve set aside Sunday afternoon to bake some cookies, but you discover you have run out of eggs. Your partner in marital bliss has gone out and taken the car. You call a couple of mates, and they tell you to try bananas, vegetable oil, or applesauce as egg substitutes. You decide to have some fun…
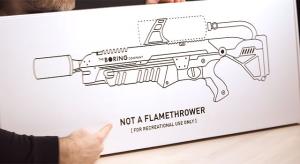
Harish Jose
Today I’m looking at design from a cybernetics viewpoint. My inspirations come from cybernetics and design theorists Ross Ashby, Stafford Beer, Klaus Krippendorff, Paul Pangaro, and Ranulph Glanville. I was curious about how the interface of a device conveys the message to the user on how to…
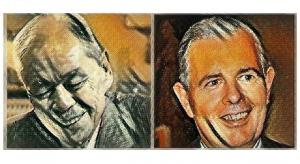
Harish Jose
One of my favorite equations from Factory Physics, by Wallace Hopp and Mark Spearman (Waveland Press, third edition, 2011) is Kingman’s formula, usually represented as “VUT.”
The VUT equation is named after Sir John Kingman, a British mathematician:
The first factor represents variability and is…
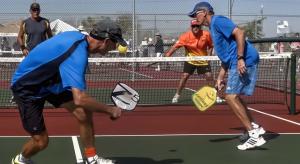
Steve Moore
Pickleball is arguably the fastest-growing sport in the United States, especially among baby-boomer retirees. This game is similar to tennis, but is played on a smaller court (44 ft × 20 ft) with a solid paddle and a perforated polymer ball much like a wiffle ball.
Pickleball’s popularity may be…
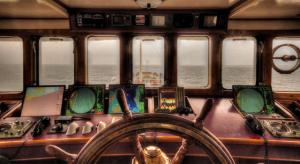
Harish Jose
After reviewing Mark Graban’s wonderful book, Measures of Success (Constancy, 2018), I started rereading Walter Shewhart’s books, Statistical Method From the Viewpoint of Quality Control (Dover reprint 1986, originally edited by W. Edwards. Deming), and Economic Control of Quality of Manufactured…
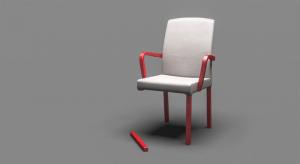
Jody Muelaner
In a general sense, capability is the ability to do something. Within manufacturing, capability is given a much more specific definition. It is an expression of the accuracy of a process or equipment, in proportion to the required accuracy.
This can be applied to production processes, in which…
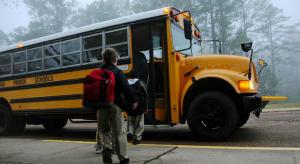
Rohit Mathur
Whatever the process or type of data collected, all data display variation. This is also true in software development. Any measure or parameter of interest to our business will vary from time period to time period, e.g., number of incidents per week or month, time taken in resolving incidents,…
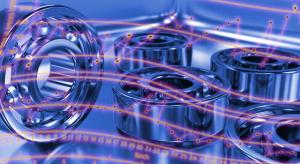
Scott A. Hindle
In everyday language, “in control” and “under control” are synonymous with “in specification.” Requirements have been met. Things are OK. No trouble.
“Out of control,” on the other hand, is synonymous with “out of specification.” Requirements have not been met. Things are not OK. Trouble.
Using…
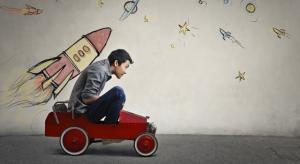
Brian Lagas
‘Why are our changeovers taking so long?”
If you’ve asked this question on the shop floor, more than likely you were met with blank stares by your employees. Open-ended questions like this are overwhelming, so employees try to find quick answers that don’t really address the problem. They don’t…
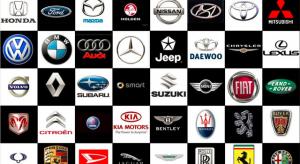
Chad Kymal, Gregory F. Gruska
During the early 1980s, GM, Ford, and Chrysler established the Automotive Industry Action Group (AIAG), a not-for-profit organization with the mission “To improve its members’ competitiveness through a cooperative effort of North American vehicle manufacturers and their suppliers.” In the late…
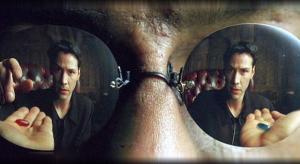
Harish Jose
I must confess up front that the title of this column is misleading. Similar to the Spoon Boy in the movie, The Matrix, I will say, “There is no lean problem or a Six Sigma problem. All these problems are our mental constructs of a perceived phenomenon.”
A problem statement is a model of the…
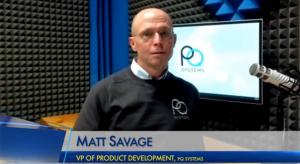
Ryan E. Day
Current business conversation often focuses on data and big data. Data are the raw information from which statistics are created and provide an interpretation and summary of data. Statistics make it possible to analyze real-world business problems and measure key performance indicators that enable…
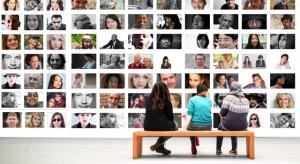
Nicola Olivetti
According to a report by PwC, industrial sectors worldwide plan to invest $900 billion in Industry 4.0 each year. Despite these growing technology investments, only a few technologies are significantly mature to drive measurable quality impacts. Digital visual management (DVM) is one of them, being…
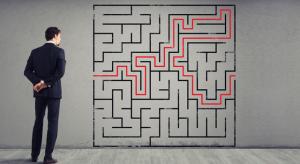
Shobhendu Prabhakar
Someone recently asked me why quality failures and safety incidents continue to occur despite organizations communicating their quality and safety visions to the workforce, developing and implementing quality and safety management systems, and campaigning day in and day out about quality and safety…
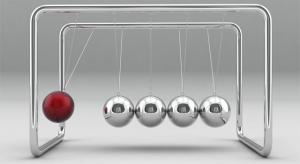
Harish Jose
Today I’m looking at Factory Physics and the Toyota Production System (TPS). My main references for the post are the 1977 paper co-authored by ex-Toyota president Fujio Cho and key ideas from Factory Physics (Waveland Press, 2011).
One of my favorite definitions of lean comes from Wallace J. Hopp…
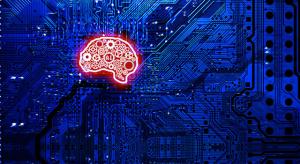
Doug Devereaux
Artificial intelligence (AI) is widely acknowledged as a crucial aspect of what is broadly referred to as Industry 4.0. Although no one knows yet how AI will be incorporated into the next phase of the Industrial Revolution, most agree that it will allow greater connectivity between people, machines…
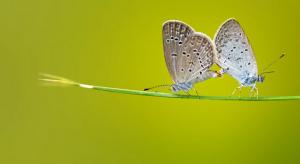
Shobhendu Prabhakar
Historically, conventional wisdom among business managers was that the higher the quality, the higher the cost. This perception still holds true today among a few business managers. Common sense also tells us the same thing, i.e., to create higher quality products or services, organizations will…
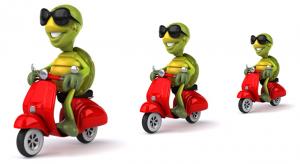
Harish Jose
Today I’m looking at the profound phrase of Canadian philosopher and a media theorist Marshall McLuhan, “The medium is the message.”
McLuhan noted that: “Each medium, independent of the content it mediates, has its own intrinsic effects, which are its unique message.... The message of any medium…
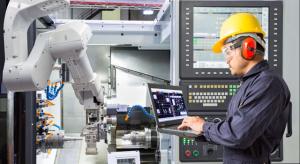
Scott A. Hindle
‘Process Capability: What It Is and How It Helps,” parts one, two, three, and four, discussed Alan’s development in the field of process capability1 He’d learned about the mistakes that can be made and how to avoid them in practice to become better at his job. Alan had since passed on his learning…
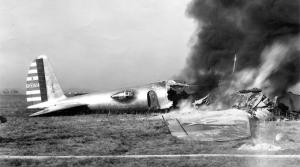
Shobhendu Prabhakar
Why do we waste our time and effort completing checklist after checklist for tasks that we can complete even when half awake? Do we not have better things to do than complete checklists?
Good question! And the answer is simple: If there is a checklist, it exists for a reason, and we need to follow…
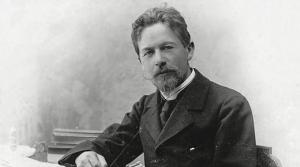
Harish Jose
One of my favorite things to do when I learn new and interesting information is to apply it to a different area to see if I can gain further insight. Here, I am looking at the principle, “Chekhov’s gun,” named after the famous Russian author, Anton Chekhov (1860–1904), and how it relates to gemba…
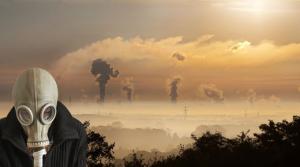
Dirk Dusharme @ Quality Digest
We tied up last year in a neat little bow, talking about how stories define ourselves and our work; waste is waste, no matter your political leanings; and putting numbers from the news in context.
“The Gift of Being Small” This article by Quality Digest’s Taran March wonderfully illustrates how we…
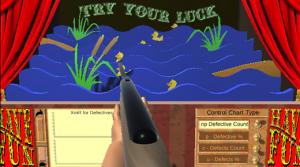
Anthony D. Burns, Michael McLean
The control chart is at the heart of the very definition of quality. It is central to building, maintaining, and predicting quality into the future. However, control charts today, more often than not, are misused and misunderstood. The aim of this article is to show not only how control charts are…
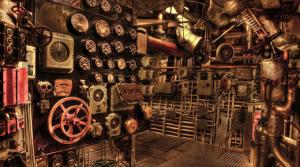
Anthony Chirico
Everybody wants to design and conduct a great experiment! To find enlightenment by the discovery of the big red X and perhaps a few smaller pink x’s along the way. Thoughtful selection of the best experiment factors, the right levels, the most efficient design, the best plan for randomization, and…
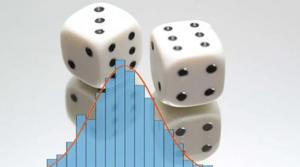
Jody Muelaner
In this article I will show that the conventional method for calculating uncertainty is not always reliable. In fact, it is generally only exact when the measurement can be represented by a simple linear equation and the input uncertainties are all normally distributed. Whenever the measurement is…
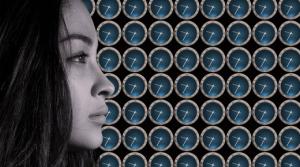
Scott A. Hindle
Walter Shewhart, father of statistical process control and creator of the control chart, put a premium on the time order sequence of data. Since many statistics and graphs are unaffected by this, you might wonder what the fuss is about. Read on to see why.
Figure 1 shows a series of measurements…
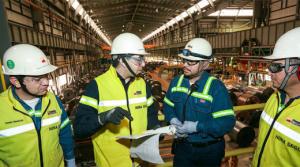
Eric Stoop
The frequently referenced learning pyramid asserts than an average student retains 75 percent of information learned through practice, compared to just 5 percent of what he hears in a lecture. Although experts may dispute the relevance of these figures when applied to modern society, all of us can…
Minitab LLC
Process validation is vital to the success of companies that manufacture pharmaceutical drugs, vaccines, test kits, and a variety of other biological products for people and animals. According to FDA guidelines, process validation is “the collection and evaluation of data, from the process design…
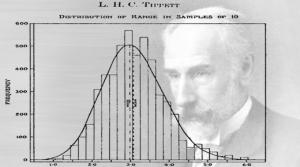
Anthony Chirico
Perhaps the reader recognizes d2 as slang for “designated driver,” but quality professionals will recognize it as a control chart constant used to estimate short-term variation of a process. The basic formula shown below is widely used in control charting for estimating the short-term variation…
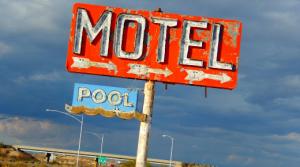
Dirk Dusharme @ Quality Digest
In this episode we look at a history of quality, how you serve your customer in the housing industry, and what makes a good review.
“Young couples ‘trapped in car dependency’”
Building entry-level housing along highways may give couples the chance to buy a home, but at what cost to them and the…
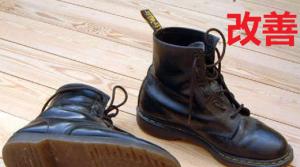
Harish Jose
I am writing today about “bootstrap kaizen.” This is something I have been thinking about for a while. Wikipedia describes bootstrapping as “a self-starting process that is supposed to proceed without external input.” The term was developed from a 19th-century figure of speech—“pull oneself over a…
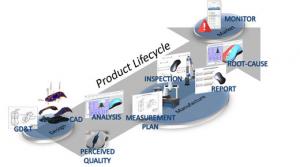
Gary Bell
It is all too common in the industry: A part design is created and sent out for production only to hit repeated snags as questions arise about datums, locators, symbols, and values. Even simple misunderstandings, such as where the geometric dimensioning and tolerancing (GD&T) lines terminate,…
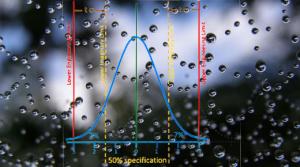
Anthony Chirico
In my first article, the merits and cautions of AS9138 c=0 sampling plans were discussed and a simple formula was provided to determine the required sample size to detect nonconforming units. In the second article, the process control properties of MIL-STD-105 c>0 sampling plans were…
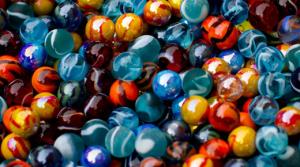
Anthony Chirico
In my previous article, I discussed the merits and cautions of the “acceptance number” equal zero (c=0) sampling plans contained within AS9138. A simple formula was provided to determine appropriate sample size, and it was illustrated that twice the inspection does not provide twice the consumer…
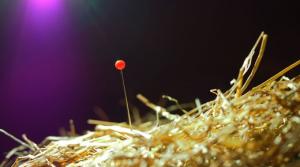
Anthony Chirico
Aerospace standard AS9138—“Quality management systems statistical product acceptance requirements” was issued this year (2018), a few years after its accompanying guidance materials in section 3.7 of the International Aerospace Quality Group’s (IAQG) Supply Chain Management Handbook. The new…
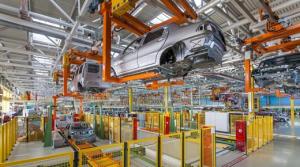
Dirk Dusharme @ Quality Digest
In this all-manufacturing episode, we look at the STEM pipeline into manufacturing, supplier development, how to make sense of manufacturing data and, no, manufacturing is not dead.
“Strengthening the STEM Workforce Pipeline Through Outreach”
NIST does more than just research and come up with…
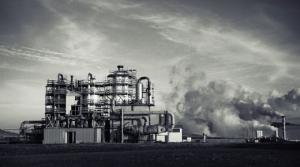
Donald J. Wheeler
Parts One and Two of this series illustrated four problems with using a model-building approach when data snooping. This column will present an alternative approach for data snooping that is of proven utility. This approach is completely empirical and works with all types of data.
The model-…
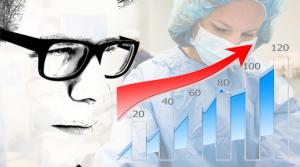
Rip Stauffer
I must admit, right up front, that this is not a totally unbiased review. I first became aware of Davis Balestracci in 1998, when I received the American Society for Quality (ASQ) Statistics Division Special Publication, Data “Sanity”: Statistical Thinking Applied to Everyday Data. At the time, I…
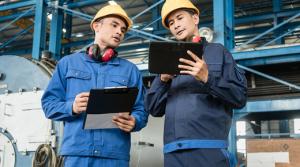
Ryan E. Day
‘In God we trust; all others bring data.” “Follow the data.” “Let the data talk.” Nice clichés, but there’s one problem... data can’t talk. In fact, data don’t say a darn thing. Data are bits of raw information. If you want to reduce product variation, improve your manufacturing processes, and…
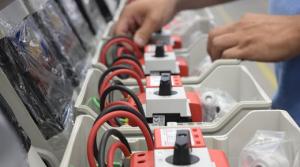
Glenn S. Wolfgang
Flow quality management (Flow QM) is a logistical alternative to handling product in lots for the purpose of assessing and mitigating defects. It features a streamlined, automated acceptance sampling methodology, is built on empirical metrics, and facilitates timely, meaningful performance…
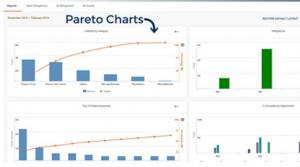
Stephen Salata
It’s an open secret that many automotive and aerospace manufacturers have unacceptably high defects and costs. And where defects are on the rise, quality costs aren’t far behind.
Even one defect could mean recalling an entire batch, a problem that can cost thousands of dollars per minute if it…
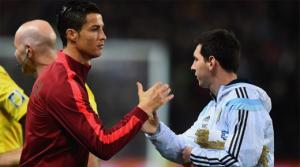
Scott A. Hindle
I recently got hold of the set of data shown in figure 1. What can be done to analyze and make sense of these 65 data values is the theme of this article. Read on to see what is exceptional about these data, not only statistically speaking.
Figure 1: Example data set.
A good start?
While…
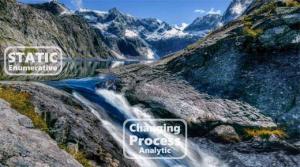
Anthony D. Burns
Quality is related to processes. A process is “a series of actions or steps taken in order to achieve a particular end.” It doesn’t matter whether the process is the handling of invoices, customers in a bank, the manufacture or assembly of parts, insurance claims, the sick passing through a…
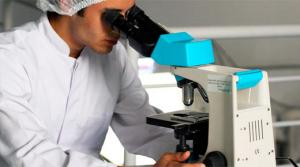
Cheryl Pammer
Confidence intervals show the range of values we can be fairly, well, confident, that our true value lies in, and they are very important to any quality practitioner. I could be 95-percent confident the volume of a can of soup will be 390–410 ml. I could be 99-percent confident that less than 2…
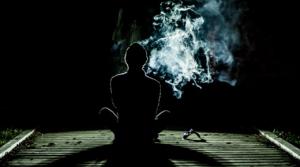
Rip Stauffer
A lot of people in my classes struggle with conditional probability. Don’t feel alone, though. A lot of people get this (and simple probability, for that matter) wrong. If you read Innumeracy by John Allen Paulos (Hill and Wang, 1989), or The Power of Logical Thinking by Marilyn vos Savant (St.…
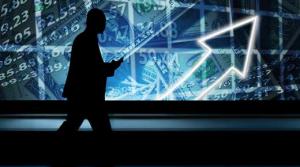
Mike Richman
There are many subjects that we cover regularly here at Quality Digest. Chief among these are standards (ISO 9001 or IATF 16949, for example) methodologies (such as lean, Baldrige, or Six Sigma), and test and measurement systems (like laser trackers or micrometers). One topic, however, is…
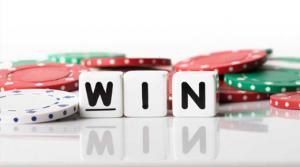
Matthew E. May
Process improvers the world over rally around root cause analysis as if it were the holy grail of all things organizational. But is it?
Understanding the root cause of a problem certainly makes sense in the context of a present day situation carrying the potential for a correct answer or solution…
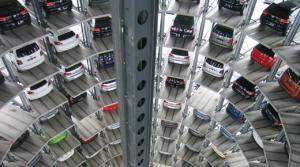
Dirk Dusharme @ Quality Digest
In our May 11, 2018, episode of QDL, we looked at overproducing ideas, bad quotas (aren’t they all), and how anger can help identify core values.
“Questioning Quotas”
When are quotas bad? Most of the time. But here’s a good example.
“How to Find Your Company’s Core Values”
Oddly enough, your…
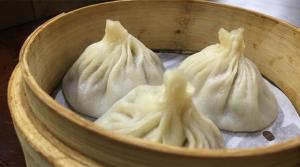
Harish Jose
I have been writing about kaizen a lot recently. It is a simple idea: change for the better. Generally, kaizen stands for small incremental improvements. Here I’m going to look at what is the best kind of kaizen.
The twist in the dumpling
A few posts back, I talked about the order for kaizen,…
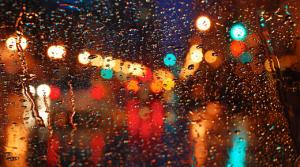
Willie L. Carter
Becoming a process-focused organization requires a sustained effort, and for most industrial and service organizations that is a difficult task. Failure to improve the performance of your processes leads to a failure to improve the organization and results in improperly managing the business.
All…
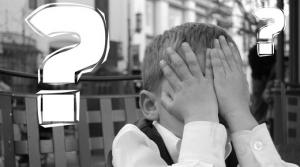
Douglas C. Fair
Here’s a quick rundown of what we covered in part one of our list of top 10 mistakes to avoid when using statistical process control (SPC): training everyone, charting everything, segregating control charts from manufacturing, “pinching” the SPC coordinator, and using SPC because it’s a “good thing…
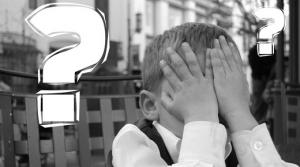
Douglas C. Fair
As you think about your organization’s manufacturing quality efforts—what you’ve overcome and what you hope to accomplish in the future—there is something you need to know.
You: What? Who? Me?
Me: Yes, you. No matter how long you’ve been playing this game (and I know many of you have been playing…
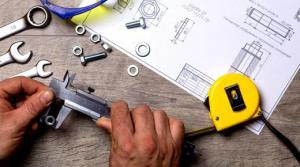
William A. Levinson
Inspection is a mandatory but nonvalue-adding activity, and our objective is to do as little as possible, provided that we continue to fulfill the customer’s requirements. The zero acceptance number (c = 0) sampling plan requires far less inspection than the corresponding ANSI/ASQ Z1.4 (formerly…
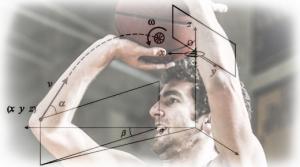
Mike Richman
QDL always strives to bring you a look at the people and stories making the news in the world of quality. We succeeded admirably on the “people” side of things this week and threw in a fun story about the physics of the basketball to boot. Let’s take a closer look:
“Clarity First Book Review and…
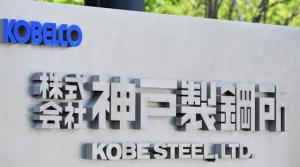
Debashis Sarkar
The cheating at Kobe Steel shook not just Japan but the entire manufacturing world. As Kobe Steel CEO Hiroya Kawasaki revealed, about 500 companies had received its falsely certified products, which affected not only those companies but also its entire supply chain. However, the issue at Kobe was…
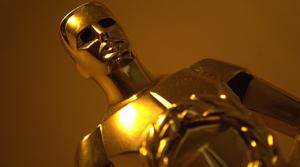
Jason Furness
In a previous article I wrote about the reasons why so many lean manufacturing, Six Sigma, and other improvement programs fail. In this article I’m going to expand on reason No. 1: the Academy Award Syndrome.
Academy Award Syndrome
The Academy Award Syndrome is where a program or project is…
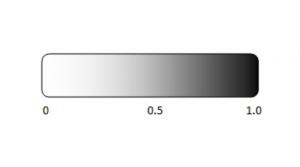
Harish Jose
It’s not easy to find topics to write about, and even if I find good topics, it has to pass my threshold level. As I was meditating on this, I started to think about procrastination and ambiguity. So my column today is about the importance of “fuzzy concepts.” I am using the term in a loose sense…
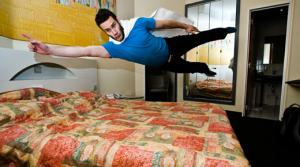
Richard Harpster
Richard Harpster's op-ed is in response to a recent Quality Digest article and webinar discussing the benefits of the draft AIAG-VDA FMEA Handbook. As he points out at the end of this article, the AIAG has provided a means to solicit comments, pro or con, on the handbook. We encourage interested…
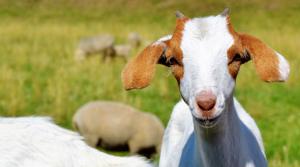
Chip Bell
Variation and defects. They are the bane of all manufacturing companies. They signal an absence of efficiency, a neglect of productivity, and a total disregard for cost effectiveness. Who is seen as the rescuing knight in shining armor? Sir Six Sigma!
Fundamentally, Six Sigma (always capitalized,…
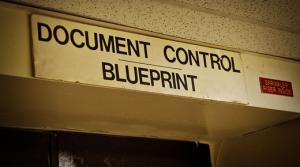
Mike Richman
During the Nov. 3, 2017, episode of QDL, we (figuratively) traveled the globe to bring you quality information. Let’s take a closer look:
“‘Made in Japan’ Falls from Grace Amid Scandals, Systematic Flaws in Manufacturing Industry” Kobe Steel is the latest Japanese manufacturer to admit to…
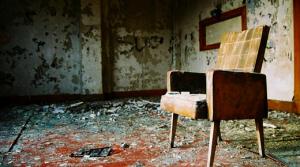
Scott A. Hindle, Donald J. Wheeler
In theory, a production process is always predictable. In practice, however, predictable operation is an achievement that has to be sustained, which is easier said than done. Predictable operation means that the process is doing the best that it can currently do—that it is operating with maximum…
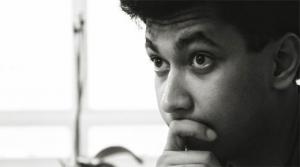
Harish Jose
Today I will look at epistemology at the gemba. Epistemology is the part of philosophy that deals with the theory of knowledge. It tries to answer the questions, “How do we know things, and what are the limits of our knowledge?” I have been learning about epistemology for a while now, and I find…
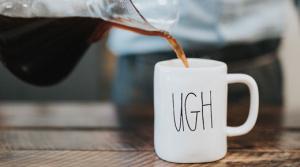
Matthew Barsalou
Quality tools can serve many purposes in problem solving. They may be used to assist in decision making, selecting quality improvement projects, and in performing root cause analysis. They provide useful structure to brainstorming sessions, for communicating information, and for sharing ideas with…
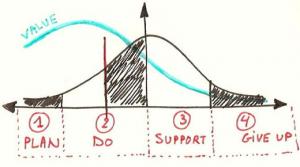
John Flaig
Story update 9/26/2017: The words "distribution of" were inadvertently left out of the last sentence of the second paragraph.
Some practitioners think that if data from a process have a “bell-shaped” histogram, then the system is experiencing only common cause variation (i.e., random variation).…
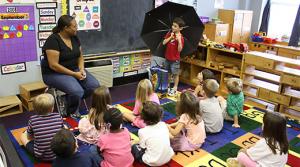
Mike Richman
QDL from Fri., Sept. 15, 2017, demonstrated that everywhere you look, you’ll find the positive effect of better quality. Here’s what we chatted about:
““U.S. Business Sectors Gain or Hold Steady in Public Esteem”
According to a recent Gallup survey, U.S. citizens’ outlook on a number of industries…
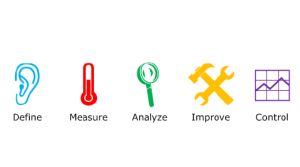
Eston Martz
The Six Sigma quality improvement methodology has lasted for decades because it gets results. Companies in every country around the world, and in every industry, have used this logical, step-by-step method to improve the quality of their processes, products, and services. And they’ve saved…
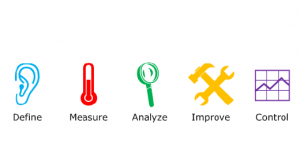
Eston Martz
Six Sigma is a quality improvement method that businesses have used for decades—because it gets results. A Six Sigma project follows a clearly defined series of steps, and companies in every industry in every country around the world have used this method to resolve problems. Along the way, they’…
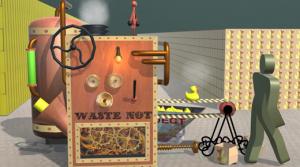
Anthony D. Burns
I had humble, that is, poor, beginnings. I didn’t even know the taste of real ice cream until later in life. One of the first impacts I felt of the luxury that technology brings was the diode my father bought for me to replace the cat’s whisker on my crystal radio. My high school was lovingly…
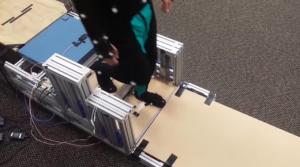
Dirk Dusharme @ Quality Digest
Our August 11, 2017, episode of QDL looked at the role of technology in after-market service, stairs that help you up, Fidget Cubes, and more.
“Climbing Stairs Just Got Easier With Energy-Recycling Steps”
These stairs actually help you go up.
“The Curious Case of the Fidget Cube”
How a product…
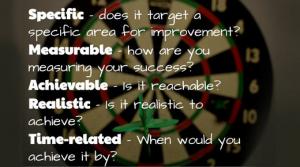
Ken Levine, Satish Nargundkar
Completing the define phase of a lean Six Sigma (LSS) project is a critical part of any project, although it’s often underestimated in practice. The define phase of the define, measure, analyze, improve, control (DMAIC) process typically includes three elements. The first is selecting a specific,…
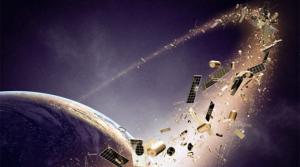
Mike Richman
The June 30, 2017, episode of QDL offered a wrinkle in time, of sorts: not only orbiting debris and medieval medicine, but moments in the here and now such as our interview with Keith Bevan of the Coordinate Metrology Society and the UK’s National Physical Laboratory, and an on-the-go version of…
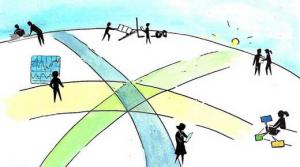
Douglas C. Fair
Plant-floor quality issues tend to focus on a company’s technical resources. When products fall out of spec, alarms sound and all hands are immediately on deck to fix things. Despite large technology investments to monitor and adjust production processes, manufacturers are still bedeviled by…
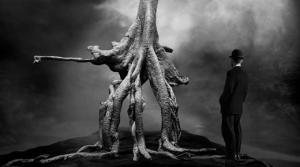
Matthew Barsalou, Robert Perkin
As you drive east on I-70 coming from the Rockies, there is a point where you seem to have stopped descending, but a sign says, “Trucks: Don’t be fooled. Four more miles of steep grades and sharp curves.” The message is that it would be premature to relax at this point, and vigilant driving is…
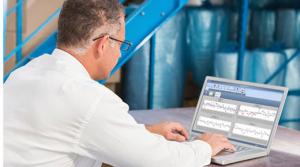
Steve Daum
I have daily conversations with manufacturer plant managers, quality managers, engineers, supervisors, and plant production workers about challenges when using statistical process control (SPC). Of the mistakes I witness in the application of SPC, I’d like to share the five most prevalent; they…
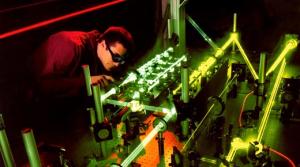
Matthew Barsalou
I
n part one of this two-part series, I described the need for empiricism in root cause analysis (RCA). Now, I’ll explain how to achieve empiricism when performing a RCA by combining the scientific method and graphical explorations of data.
The statistician John Tukey believed data should be…

Matthew Barsalou
There are many reasons for performing a root cause analysis (RCA). These reasons include determining the cause of a failure in a product or a process as well for determining the root cause of the current level of performance when a product or process has been selected for improvement.
There are…
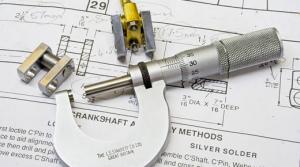
Stefan H. Steiner, R. Jock MacKay
In his February 2017 Quality Digest column, “Don’t We Need Good Measurements?” Donald J. Wheeler recommends that a measurement system contributing up to 80 percent of the overall variation (on the variance scale) is good enough to detect persistent mean shifts when using a process behavior (…
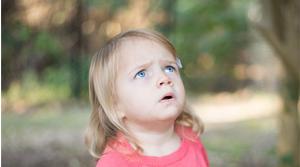
Harish Jose
I have been reading a lot these days about Western philosophy. The most recent book, All Life is Problem Solving (Routledge, 2001), is by Karl Popper, one of the great philosophers of the 20th century. This is a collection of Popper’s writings. One of the great teachings from Popper is the concept…
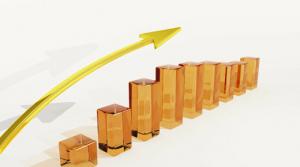
Jason Furness
In a previous column based on our recent book, Manufacturing Money (Amazon Digital, 2015), we explained how to maximize ROI. Here we describe some changes that business owners and managers can make on their way toward becoming a Black Belt in a manufacturing and distribution business.
Before any…
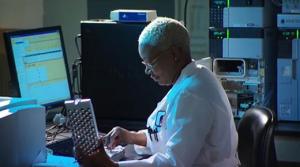
Michael Causey
Former FDA Chairman Robert Califf, M.D., stepped down on Jan. 20, 2017, and it’s not always easy to predict what the Center for Drug Evaluation and Research (CDER), or any FDA agency, will accomplish under a new chairman. Efforts at quality management could be affected by what appears to be an…
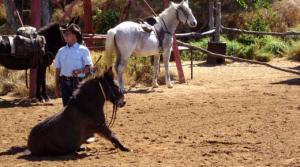
Harish Jose
As our new year unfolds, I wanted to write an article to remind myself of three pieces of advice. They are from Epictetus (55–135 AD), Marcus Aurelius (121–180 AD), and George Pólya (1887–1985). Epictetus and Aurelius are two famous Stoic philosophers of the past, and Pólya is a famous Hungarian…
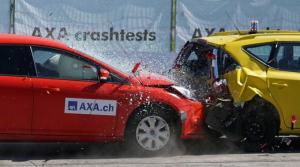
Donald J. Wheeler
What can be done when a test is destructive? How do we characterize measurement error? How can we determine if a test method is adequate for a given product or application? How can we check for bias?
All of the techniques for assessing the quality of a measurement system require us to make…
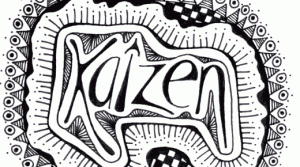
Kyle Pheland, Belinda Jones
Change is inevitable in every organization. Planned or not, forces inside and outside the enterprise can sometimes encumber a workforce and lead to nonvalue-added processes. Growing spurts, major technology implementations, or even small supply-chain organizational projects can present more issues…
Donald J. Wheeler
Who can be against apple pie, motherhood, or good measurements? This is why everyone stands up and salutes when we are told to maintain our measurement systems in good calibration. But what is good calibration? By what method will we achieve it? And how will we know when we have it?
One day I…
Davis Balestracci
Have you ever heard something like: “I’m committed to Dr. Deming’s approach [or Six Sigma or lean or TPS, it doesn’t matter], but executives don’t seem to listen anymore. All they do is keep interrupting my very clear explanations with, ‘Show me some results, then show me what to do.’ I was…
The United State Occupational Safety and Health Administration (OSHA) estimates that $60 billion is lost annually from workplace injuries and illness. Using the administration’s $afety Pays Program calculator, 20 carpal tunnel syndrome injuries will cost a company $1,260,000 in direct and indirect…
Joel Bradbury
Healthcare professionals have a long history of caring for their patients and improving the quality of their services. During the Crimean War (1853–1856), British nurse Florence Nightingale realized that the mortality rate of soldiers was far too high. A visionary statistician as well as a…
Bruce Hamilton
One of Shigeo Shingo’s popular status quo targets was engineers, whom he placed in three categories: table engineers, those who just sit around a table and talk about problems; catalog engineers, those who think the solution to every problem can be found in a catalog; and nyet engineers, those who…
Jason Furness
Editor’s note: This is an excerpt from Manufacturing Money (Amazon Digital Services, 2015) by Jason Furness and Michael McLean. See the article on the Manufacturship blog.
I n martial arts, the level of skill of the practitioner is recognized by the use of different colored belts to be worn with…
Davis Balestracci
Client A came to me for a consultation and told me upfront his manager would allow him to run only 12 experiments. I asked for his objective. When I informed him that it would take more than 300 experiments to test his objective, he replied, “All right, I’ll run 20.”
Sigh. No, he needed either to…
GBMP
Ellis Medicine is a 438-bed community and teaching healthcare system serving New York’s capital region. With four main campuses, five additional service locations, more than 3,300 employees, and more than 700 medical staff, Ellis Medicine offers an extensive array of inpatient and outpatient…
Harish Jose
Kaizen is often translated as “continuous improvement” and identified as one of the core themes in lean. Today I’m pondering the question: Can kaizen ever be bad for an organization?
In order to go deeper on this question, first we have to define kaizen as a focused improvement activity. The…
Ryan E. Day
Sponsored Content
You might say what Henry Ford did for the automobile, GE, Siemens, and Mitsubishi have done for the gas and steam turbine industry. Naturally, the tools and technicians of both sectors have had to evolve right along with the challenges of new technology and the ever-increasing…
Quality Transformation With David Schwinn
We recently had dinner with a wonderful friend and colleague, Michelle Guenther. During our meal, Michelle mentioned a conversation at work when she responded to a question with, “What I believe to be true is....” She said she frequently prefaces her answers to questions with that phrase and that…
Bruce Hamilton
The following is inspired by The Teachings of Don Juan (Washington Square Press, reprint 1985), an anthropological novel from the 1960s written by Carlos Castaneda, chronicling his travels with Don Juan, a Yaqui shaman. To crudely paraphrase, according to Don Juan, the road to knowledge is first…
Bob Emiliani
To this day, lean management has yet to enter the mainstream in business. It remains solidly on the fringe, despite great efforts by many people over many decades.
You almost never hear of lean management in the business press unless the article is written by an insider such as James P. Womack or…
Harish Jose
Uncertainty is all around us. A lean leader’s main purpose is to develop people so they can tackle uncertainty. There are two ways to tackle uncertainty: One is genchi genbutsu (go and see, or seeing for yourself), and the other is to employ the plan-do-check-act (PDCA) cycle, a method for…
Barbara A. Cleary
In a rapidly changing business environment, it’s sometimes hard just to keep up with everyday demands—never mind having time to develop new and better approaches to changing requirements, needs, or markets. Staying ahead of the curve sounds as if it might demand working longer hours, hiring more…
Quality Transformation With David Schwinn
It’s hard these days to miss the passion of people who support Donald Trump or Bernie Sanders, the steadfastness of the Tea Party, the outrage of the Occupy Wall Street group, and the frustration of young people who have so given up on the system that they choose not to vote. Most grievous is the…
Peter J. Sherman
As organizations become successful and grow, uncertainty is generally the enemy. Thriving organizations seek to eliminate variation and increase efficiency. They identify best practices and policies, and design standard operating procedures. Such efforts can make a business wildly efficient at…
Greg Fox
My recent beach vacation began with the kind of unfortunate incident that we all dread: killing a distant relative.
It was about 3 a.m. Me, my two sons, and our dog had been on the road since about 7 p.m. the previous day to get to our beach house on Plum Island, Massachusetts. Google maps said…
Afaq Ahmed, Yves Van Nuland
New technologies have empowered customers to seek out the best products and services at the lowest cost and shortest delivery times. Customers can compare price and delivery information as well as reviews about product quality. Thus, the importance of sustaining outstanding quality in order to…
Harish Jose
There is a concept in lean known as a “monument.” It refers to a large machine, piece of equipment, or something similar that can’t be changed right away, and so you have to plan your processes around it. This generally impedes the flow and frequently becomes a hindrance to lean initiatives. A…
Davis Balestracci
Today I want to concentrate on the foundation of what is most commonly taught as design of experiments (DOE)—factorial designs.
Elsewhere I’ve mentioned three of C.M. Hendrix’s “ways to mess up an experiment.” After 35 years of teaching DOE, I’ve concluded that he pretty much captures the…
Ken Levine
How do you determine the “worst case” scenario for a process? Is it by assuming the worst case for each process task or step? No. The reason is that the probability of every step having its worst case at the same time is practically zero. What we’re looking for is a value that will occur a very…
Harish Jose
In this article I want to look at the concept of equifinality in relation to the plan-do-check-act (PDCA) cycle. In systems theory, equifinality is defined as reaching the same end, no matter what the starting point was. This is applicable only in an open system, one that interacts with its…
Bruce Hamilton
Twice in the last month I’ve heard the phrase “traditional lean” used in public presentations. In neither case did the presenter explain the expression, but one displayed a slide with a Venn diagram showing the overlap between lean and Six Sigma.
I suppose this means that he defined traditional…
Quality Transformation With David Schwinn
The map is not the territory.
—Alfred Korzybski
This column is a tribute primarily to Jamshid Gharajedaghi, a long-time teacher, mentor, colleague, and friend. My wife Carole and I recently visited him while in Philadelphia doing a presentation for the International Society for Performance…
Jim Benson
We are all cursed with “surprises” at work. We come in, sit down, get ready for the day. We select a task to start on, and about halfway through, it explodes on us. The seemingly simple task now has 30 subtasks all lined up, ready to destroy our day.
This is stressful. Since we’re likely already…
Fred Schenkelberg
What if all failures occurred truly randomly? Well, for one thing the math would be easier.
The exponential distribution would be the only time to failure distribution—we wouldn’t need Weibull or other complex multi-parameter models. Knowing the failure rate for an hour would be all we would need…
Bruno Scibilia
In yesterday’s column, I discussed how a DOE was chosen to optimize a chemical-mechanical polishing process in the microelectronics industry. This important process improved the plant’s final manufacturing yields. We selected an experimental design that let us study the effects of six process…
Ken Levine
One poorly understood concept in lean Six Sigma is how much to “stretch” when setting S.M.A.R.T. goals. These letters are defined as S—specific; M—measureable; A—assignable, attainable, or achievable; R—realistic, reasonable, or relevant; and T—time-based or time-bound. Regardless of the different…
Kimberly Watson-Hemphill, Kristine Nissen Bradley
Editor’s note: This is an excerpt from the new book, Innovating Lean Six Sigma, by Kimberly Watson-Hemphill and Kristine Nissen Bradley.
Like every company, healthcare businesses do their work through processes, and any process can be studied and improved using basic lean Six Sigma methods. Figure…
Davis Balestracci
April Fool’s Day (today) and the opening of baseball season (this Sunday) are upon us. To mark the first event, I’ll let my distinguished colleague Donald Wheeler make some eloquent and crucial statistical points that turn out to be, well, laughably simple. (No fooling!) Regarding the baseball…
Matthew Barsalou
The start of a failure investigation may involve brainstorming, but empirical methods will be required to actually identify a problem's cause. Implementing an improvement action without a confirmed root cause risks a reoccurrence of the issue because the true root cause has yet to be addressed.…
Eston Martz
There’s plenty of noisy disagreement about the state of healthcare, but when you look beyond the controversies, a great deal of common ground exists.
Many agree that the way we’ve been doing things is wasteful and inefficient, when healthcare should be delivered as efficiently and effectively as…
John Flaig
Sometimes when authors try to make a technical concept more understandable, it’s simplified but unfortunately, less accurate.
For example, when the developers of Six Sigma wanted to explain control charts and process capability analysis, they needed to include how the signal can be separated from…
Beth Savage
Out-of-control gas prices reported in the news have our attention. Nearly every media outlet, from the small-town daily news to The Wall Street Journal, has a gas price story on a weekly basis: “Gas Prices Are Plunging,” and “How Low Will Gas Prices Go?” It’s news when they rise and news when they…
Davis Balestracci
This article is based on some ideas from my respected colleague Mark Hamel. Despite the lean framework, these ideas apply to any improvement approach—all of which come from the same theory, lean included.
During the past 35 years, quality has evolved from the necessary evil of quality control to…
Mike Micklewright
In October 2014, 17-year-old Laquan McDonald was shot 16 times by a Chicago police officer. In November 2015, footage of the shooting was released and has been viewed all over the world. The footage shows an aggressive attack by a police officer, a supposed person of service to the community, as…
Davis Balestracci
Marketers are relentless in their efforts to seduce you with fancy tools, acronyms, Japanese terminology—and promises—about their versions of formal improvement structures such as Six Sigma, lean, lean Six Sigma, or the Toyota Production System, each with its own unique toolbox.
In my last column…
Quality Transformation With David Schwinn
Wherever you stand, be the Soul of that place. —Rumi
I was blessed last week to spend two glorious days with my wife, Carole, our daughter, Lisa, and Lisa’s consulting partner, Rox. Those two days were a model for how we could be in every one of our workplaces... and the world would be a better…
Quality Transformation With David Schwinn
I teach management and leadership. Recently, the topic in one of my classes was change and stress. I asked my students, who are nearly all employed and range in age from 19 to 55, what caused them the greatest stress in the workplace. Among the various responses were several related to how they…
Steve Daum
In daily conversations, I field questions from plant managers, quality managers, engineers, supervisors, and plant production workers about the challenges of applying statistical process control (SPC) methods. Following are the five most prevalent and costly mistakes I witness in the application…
William A. Levinson
The Shewhart control chart is relatively insensitive to non-normal distributions, and the worst foreseeable consequences of a wrong decision involve searching for an assignable or special cause when none is present. The economic consequences depend on the time wasted, and whether unnecessary…
Quality Transformation With David Schwinn
This month’s column results from my wife, Carole, asking me to “watch this.” This was a short video on her computer showing two young children brilliantly and inspirationally singing, “You Raise Me Up.” I was dumbstruck. Their song immediately took me to many places. I was reminded of the wisdom…
Patrick Runkel
Did you ever wonder why statistical analyses and concepts often have such weird, cryptic names? One conspiracy theory points to the workings of a secret committee called the International Committee for Sadistic Statistical Nomenclature and Numerophobia (ICSSNN), which was formed solely to befuddle…
Bill Kalmar
My wife Mary has an obsession—she always checks the expiration and freshness dates on food products that we purchase. Mary also marks purchase dates on products such as ketchup, mustard, and salad dressings when she places these items in our refrigerator. I think she has an expiration date on me…
George Chemers, Patricia Cronin
Although information is readily available about applying team-building techniques to Six Sigma projects, there’s not much about how learning styles affect the success of Six Sigma teams. Knowing that the “people side” of an otherwise technical and statistical-based methodology is important to a…
Matthew Barsalou
I gave a rather successful talk on communicating design of experiments (DoE) at the recent ENBIS 14 conference in Linz, Austria. Things went mostly well, but it’s also fair to say many attendees had one major criticism: I didn’t explain why one factor at a time testing (OFAT) isn’t ideal. That…
Barry Johnson
The adage “if you aren’t moving forward, you’re falling behind” is true more often than not. Regardless of the type of business, all organizations need to improve to survive. The last words uttered by managers in failing organizations are, “We’ve always done it this way.”
The key to long-term…
Donald J. Wheeler
The best analysis is the simplest analysis that provides the needed insight. Of course this requires enough knowledge to strike a balance between the needed simplicity and unnecessary complexity. In parts one and two of this series we looked at the properties of Weibull and gamma probability…
Dan Somers
As a person working in quality manufacturing, it’s probably in your DNA to look at a quality challenge and choose Six Sigma or something similar as the framework for getting to the answer. It’s also likely that you’re spending a lot of time gathering and analyzing data, applying hypothesis…
Darin Marcuz, Laron Colbert
This article describes a novel approach to calculating the financial aspect of overall equipment effectiveness (OEE), with the result referred to as $EE (as in monetary units). By using $EE, a management team readily can “SEE” their operation in financial terms. Employees are then better able to…
Eston Martz
When we take pictures with a digital camera or smartphone, what the device really does is capture information in the form of binary code. At the most basic level, our precious photos are really just a bunch of 1s and 0s, but if we were to look at them that way, they'd be pretty unexciting.
In its…
Donald J. Wheeler
Story update 9/8/2015: There was an error in the data set for columns "Skew" and "Kurt" in figure 7. The error has been corrected.
Clear thinking and simplicity of analysis require concise, clear, and correct notions about probability models and how to use them. Last month in part one we looked…
Quality Transformation With David Schwinn
I recently had a dream in which Adrian Bass, a colleague and friend for whom I have much admiration, asked me why I still care about quality management after all these years.
You can substitute Six Sigma for quality management because, in my mind, they are both part of a larger belief system that…
Fred Schenkelberg
Just, please, plot the data if you have gathered some time-to-failure data, or you have the breakdown dates for a piece of equipment. Any data really. It could be your review of your car maintenance records and notes and dates of repairs. You may have some data from field returns. You have a group…
Eston Martz
Statisticians say the darnedest things. At least, that’s how it can seem if you’re not well-versed in statistics.
When I began studying statistics, I approached it as a language. I quickly noticed that, compared to other disciplines, statistics has some unique problems with terminology. These are…
Gorur N. Sridhar
Quality and Six Sigma are often considered as links in a chain. For example, when quality is poor, many times the immediate response is, “Let’s improve it using Six Sigma.” But does Six Sigma, or any other program for that matter, really improve quality? Or, are they simply mirrors to let us know…
Joel Smith
Just 100 years ago, very few statistical tools were available and the field was largely unknown. Since then, there has been an explosion in available tools, as well as ever-increasing awareness and use of statistics.
Although most readers of this column are looking to pick up new tools or improve…
John Flaig
I have discussed the economics of project management numerous times in presentations all over the country, and based on the response to my message, I have to conclude that many people just don’t get it.
Let me again sound the wake-up call with a quote from V. S. Liebhold, co-author of the article…
Donald J. Wheeler
Some commonly held ideas about skewed probability models are incorrect. These incorrect ideas are one source of complexity and confusion regarding the analysis of data. By examining the basic properties of skewed distributions this article can help you to greater clarity of thought and may even…
Quality Transformation With David Schwinn
This month’s column was prompted by an especially thoughtful commencement address by Michael Ward, reproduced in the May/June 2015 issue of Imprimis (Hillsdale College). Ward, of course, encouraged the students to strive for success, but interestingly predicted that failure is inevitable and is to…
Eston Martz
If you’ve read the first two parts of this tale, you know it started when I published a post that involved transforming data for capability analysis. When an astute reader asked why Minitab didn‘t seem to transform the data outside of the capability analysis, it revealed an oversight that…
Eston Martz
In my last post, I told you how I had double-checked the analysis in a post that involved running the Johnson transformation on a set of data before doing normal capability analysis on it. A reader asked why the transformation didn’t work on the data when you applied it outside of the capability…
Eston Martz
I don’t like the taste of crow, which is a shame, because I’m about to eat a huge helping of it.
I’m going to tell you how I messed up an analysis. But in the process, I learned some new lessons and was reminded of some older ones I should remember to apply more carefully.
This failure starts in…
Joel Smith
Last month, the ESPN series Outside the Lines reported on baseball pitchers suffering serious injuries from being struck in the head by line drives, and the efforts that Major League Baseball (MLB) is making toward having protective gear developed for pitchers.
You can view the report here if you…
Davis Balestracci
This is a continuation of my last column, which I’ve written to honor my late dad who loved golf. As promised, let’s look at the Masters golf tournament final four-round scores for the 55 players who survived the cut. We’ll analyze and then give it a twist based on the ongoing enumerative vs.…
Matthew E. May
No, this isn’t an opinion piece or in any way a critique. It’s more like a public service announcement for business professionals in the job market, looking for a strategy position with a market leader.
Like most regular users of LinkedIn, I constantly get pushed notices about “jobs I might be…
Quality Transformation With David Schwinn
“If we are to achieve a richer culture, rich in contrasting values, we must recognize the whole gamut of human potentialities, and so weave a less arbitrary social fabric, one in which each diverse human gift will find a fitting place.”
—Margaret Mead
This month’s article comes from the…
Brian Maskell
T here are three ways in which a standard costing system is typically used in a manufacturing company:
1. Performance measurement 2. Decision making 3. Inventory valuation
From an accounting perspective, performance measurement and decision making are part of a company’s management accounting…
Fred Schenkelberg
Control charts provide an ongoing statistical test to determine if a recent reading or set of readings represents convincing evidence that a process has changed from an established stable average. The test also checks sample-to-sample variation to determine if the variation is within the…
Patrick Runkel
I’ve never understood the fascination with selfies.
Maybe it’s because I'm over 50. After surviving the slings and arrows of a half a century on Earth, the minute or two I spend in front of the bathroom mirror each morning is more than enough selfie time for me.
Still, when I heard that Microsoft…
Bruce Hamilton
The last few weeks for me have been all things Shingo, including a presentation at the Shingo Institute’s International Conference three weeks ago in Provo, Utah, followed by four days of Shingo Institute workshops at Vibco in Richmond, RI. Questions at both events about assessing for enterprise…
Patrick Runkel
It’s usually not a good idea to rely solely on a single statistic to draw conclusions about your process. Do that, and you could fall into the clutches of the “duck-rabbit” illusion shown below.
If you fix your eyes solely on the duck, you’ll miss the rabbit—and vice-versa.
If you’re using…
Brian Maskell
It is vitally important for lean people to know nothing when working on improvement. This sounds like a crazy idea, but it is another 100-percent turnaround from traditional management thinking.
To do this, it’s necessary to do three things: • Understand how lean thinkers go about radically…
Rip Stauffer
Recently, in one of the many online discussion groups about quality, Six Sigma, and lean, this question was posed: “Can X-bar R and X-bar S be used interchangeably based on samples size (n) if the subgroup size is greater than one and less than eight?” Answers varied, of course.
In some of these…
Dawn Keller
Generally speaking, I have a problem with authority. I don’t like being told what to do or how to do it. I’m not proud of that.
I recall debating with my high school trigonometry teacher regarding the value of the homework “process”—specifically in those situations where the student in question…
Jens R. Woinowski
As you browse through lean management pages on the Internet, you may have seen reports on companies having little success with lean, or comments about how misunderstanding lean can lead to bad consequences. From time to time I can sense the level of frustration from those comments, and I…
Eston Martz
Last week I attended the American Society for Quality’s World Conference on Quality and Improvement in Nashville, TN. The ASQ conference is a great opportunity to see how quality professionals are tackling problems in every industry, from beverage distribution to banking services.
Given my…
Steve Daum
The ability to make predictions has always been rewarded. Statistician Donald J. Wheeler says that “prediction is the essence of business.” With growing bodies of data and good analytical models, our predictions are getting better.
The statistical models and algorithms behind prediction can be…
Donald J. Wheeler
Parts per million (ppm) is part of the language of Six Sigma. It pervades the sales pitch and is used in all sorts of computations as a measure of quality. Yet what are the rules of arithmetic and statistics that govern the computation and usage of parts per million? To discover the answers read…
Bruno Scibilia
The Cp and Cpk are well-known capability indices commonly used to ensure that a process spread is as small as possible compared to the tolerance interval (Cp), or that it stays well within specifications (Cpk). Yet another type of capability index exists: the Cpm, which is much less known and used…
Quality Transformation With David Schwinn
Let’s begin with yet another example of a lack of understanding of the Perversity Principle, this one from a recent The Times of India report.
“Authorities in India have reportedly arrested some 300 people and expelled 600 students in connection with a massive cheating scandal in the northeastern…
Bob Emiliani
Regular readers of my column, as well as my Twitter and LinkedIn feeds, will know that in recent months I have posted many critiques on various aspects related to the products, promotion, and practice of lean management. Why now? The reason is that 20 years of engagement in lean offers the unique…
Michelle Shemo
As a member of Minitab’s technical support team, I get the opportunity to work with many people using design of experiments (DOE).
People often will call after they’ve already chosen their design, run the experiment, and identified the important factors in their process. But now what? They have…
Bruno Scibilia
Suppose you have designed a brand-new product with many improved features that well help create a much better customer experience. Now you must ensure that it’s manufactured according to the best quality and reliability standards so that it gets the excellent long-term reputation it deserves from…
Patrick Runkel
Right now I’m enjoying my daily dose of morning joe. As the steam rises off the cup, the dark, rich liquid triggers a powerful enzyme cascade that jump-starts my brain and central nervous system, delivering potent glints of perspicacity into the dark crevices of my still-dormant consciousness.…
Quality Transformation With David Schwinn
Last weekend we took all 16 members of our family on a ski trip. It was amazing, and we are incredibly lucky. We haven’t done such a thing in 17 years, when our first grandchild, Claire, was only one month old. Life gets complex and 17 years fly by.
That experience reminded me of work my wife,…
Davis Balestracci
In my last column, I discussed how even a well-designed study with a statistically significant result doesn’t necessarily mean viability in the real world. Post-study, one must study the manifestations of variation on the result in any environment in which the result is applied—and each…
Joel Smith
I typically attend a few lean Six Sigma conferences each year, and at each there’s at least one session about compensating belts. There are any number of ideas for how to do so, but they commonly include systems that provide a percentage of savings as a portion of pay, or provide a bonus for…
Quality Transformation With David Schwinn
‘From laughing tots in Haitian preschools to inner-city gang members to top executives in global corporations, people everywhere are gathering in circles. These circles are generating trusting relationships among people with long histories of antagonism; promoting healing among people suffering…
Davis Balestracci
I have evolved to using fewer, simpler tools in my consulting and have never been more effective, as I commented upon in my last column. It made me ponder the relevance of much of what I learned in my master’s statistics program. Thinking of the most basic concepts, I decided to look up what the…
The purpose of this article is to point out a problem when using percentages for subgroups over time, or for members in a larger group, where the size of the denominator varies and probabilities are being estimated. Also to introduce a solution: adjusted p-chart scores (APC), a new way to score or…
Patrick Runkel
If you’re not a statistician, looking through statistical output can sometimes make you feel a like you’ve wandered into Alice in Wonderland. Suddenly, you find yourself in a fantastical world where strange and mysterious phantasms appear out of nowhere. For example, consider the T and P in your t…
Donald J. Wheeler
Whenever the original data pile up against a barrier or a boundary value, the histogram tends to be skewed and non-normal in shape. Last month in part one we found that this doesn’t appreciably affect the performance of process behavior charts for location. This month we look at how skewed data…
Thomas R. Cutler
This is the last in a series about how lean manufacturing has affected the people and the companywide culture at Hytrol Conveyors, a designer and manufacturer of advanced conveyor systems. As described in part 1 and part 2, dozens of interviews were conducted with a wide range of employees at the…
Barbara A. Cleary
When my mother looked at the prices of new hats, studied their features, and then went home and tried to remodel her old hat with feathers or lace to look like those fancier models, I saw the value of doing things yourself—for my mother, an attitude perhaps shaped by her own parents and their…
Dawn Keller
I really can’t make this stuff up.
I wrote a post a couple of years ago titled: “How to Talk to Your Kids About... Quality Improvement,” in which I lamented about Community Hero Day in my daughter’s first-grade class and the need to explain to her why I wasn’t at the “community-hero level” of…
Davis Balestracci
I've been presenting at the Institute for Healthcare Improvement (IHI) annual forum for 21 consecutive years. Maybe the biggest surprise from these two decades has been the awesome power of simply "plotting the dots," i.e., plotting important organizational data in their naturally occurring time…
Mark Rosenthal
The title of this article is a search term that recently hit The Lean Thinker site. It’s an interesting question—and interesting that it gets asked.
“Kaizen” is now an English word—it’s in the OED—and defined as such: “Noun. A Japanese business philosophy of continuous improvement of working…
Matthew Barsalou
There are many tools available for investigating quality problems. One useful and easy-to-use set of statistical tools is John W. Tukey’s exploratory data analysis (EDA), which quality engineers can use for generating hypotheses. Tukey’s EDA provides many different methods for looking at data, and…
Mike Micklewright
Should an organization’s design engineers step foot on the production floor, or would this be too much of a distraction from what they get paid to do—cranking out new designs? For most progressive and forward-looking organizations, this is a no-brainer. Of course product engineers would be, and…
Joel Smith
On a recent vacation, I was unsuccessfully trying to reunite with my family outside a busy shopping mall and starting to get a little stressed. I was on a crowded sidewalk, in a busy city known for crime, and it was raining. I thought there was no way things could get more aggravating when…
Thomas R. Cutler
In November 2014, Quality Digest Daily published the first in a series about companywide lean cultures and how a lean journey affects people and companies. Jonesboro, Arkansas-based Hytrol Conveyors, a designer and manufacturer of advanced conveyor systems, allowed an in-depth examination of why…
Donald J. Wheeler
Whenever the original data pile up against a barrier or a boundary value, the histogram tends to be skewed and non-normal in shape. In 1967 Irving W. Burr computed the appropriate bias correction factors for non-normal probability models. These bias correction factors allow us to evaluate the…
Tripp Babbitt
In my last column I wrote about the seven perspectives that pollute customers and culture. These perspectives rule the design of our organizations. They are inherent to our work cultures and thinking. They put us on autopilot as we toil in our everyday work. The first step to change that is to…
Quality Transformation With David Schwinn
My wife, Carole, and I recently participated in the 16th Annual ILA (International Leadership Association) Global Conference. The theme was conscious leadership. At the conference, Meg Wheatley was given a Lifetime Achievement Award. That puts her in the company of Peter Drucker, Warren Bennis,…
Meredith Griffith
During the last year or so I've heard a lot of people asking, "How can I calculate B10 life in Minitab?" Despite my being a statistician and an industrial engineer (mind you, one who's never actually been in the field) and having taken a reliability engineering course, I'd never heard of B10 life…
Mike Micklewright
Editor’s note: This article discusses topics covered at greater length in episodes 19–23 of a new streaming video training series, Creating and Sustaining Lean Improvements—Integrating Principles, Culture, and Tools by the author and 360 Performance Circle, a sister company to Quality Digest.…
Bruce Hamilton
There was a time when it was unfashionable for managers to associate with front-line employees. Alluding to an old adage, I used to joke that you could not even lead the horse (i.e., the manager) to water, let alone make him drink. Division of labor at that time was a great divide. In my early…
Donald J. Wheeler
There is no virtue in obedience when we do not have a choice. But when we have a choice it helps to understand both the law and the reason behind the law. This column is about bad choices that are being made on a daily basis by the users of statistical software. These bad choices violate the laws…
Walter Garvin
The foundation of lean manufacturing is kaizen, or continuous improvement. Although this principle usually targets manufacturing processes, it can also extend to the people who plan and implement lean projects—individuals that grow professionally and personally as a result of new skills and…
Danei Edelen
With multiple projects vying for your budgetary dollars, every purchase is scrutinized. With regards to statistical process control (SPC) software, companies view it primarily as a production efficiency tool, but they should expect more from their SPC software solution.
When evaluating SPC…
Bob Emiliani
Have the leading figures in the lean community walked the “Respect for People” talk? Not in my view.
Most of these leaders have only recently begun to understand and embrace the “Respect for People” principle. Although there are many dimensions to the “Respect for People” principle within lean,…
Bruno Scibilia
Using statistical techniques to optimize manufacturing processes is quite common now, but using the same approach on social topics is still an innovative approach. For example, if our objective is to improve student academic performances, should we increase teachers’ wages, or would it be better…
Donald J. Wheeler
Much of modern statistics is concerned with creating models which contain parameters that need to be estimated. In many cases these estimates can be severely affected by unusual or extreme values in the data. For this reason students are often taught to polish up the data by removing the outliers…
Mike Micklewright
You and your spouse go out to dinner to your favorite restaurant, on a “date” no less, to celebrate a big anniversary. You have been looking forward to this evening all week, and after a long, hard day at work, you’re famished and excited to eat your favorite meal. As you order dinner, the waiter…
Davis Balestracci
My last article demonstrated a common incorrect technique—based in “traditional” statistics—for comparing performances based on percentage rates. This article will use the same data to show what should be done instead.
To quickly review the scenario: In an effort to reduce unnecessary expensive…
Steve Moore
Up until a few years ago, I wasn’t a big fan of run charts. Why not just go ahead and construct a process behavior chart and move on? Well, sometimes a run chart is more appropriate for certain data structures.
For example, some data are “chunky”—see Donald Wheeler’s treatment of chunky data in…
Patrick Runkel
The word “kurtosis” sounds like a painful, festering disease of the gums. But the term actually describes the shape of a data distribution.
Frequently, you’ll see kurtosis defined as how sharply “peaked” the data are. The three main types of kurtosis are shown below.
Lepto means “thin” or “…
Quality Transformation With David Schwinn
Shortly after the death of the brilliant comedian and actor Robin Williams, his daughter Zelda quit Twitter and Instagram following online harassment over his death. How sad. We seem to somehow like to see the dark side of the world.
Even my three tennis buddies seem unable to keep from trash…
Jim Frost
In a previous article, I showed why there is no R-squared for nonlinear regression. Anyone who uses nonlinear regression will also notice that there are no P values for the predictor variables. What’s going on?
Just like there are good reasons not to calculate R-squared for nonlinear regression,…
Davis Balestracci
My last column, “Dealing With Count Data and Variation,” showed how a matrix presentation of stratified count data could be quite effective as a common-cause strategy. I’ll use this column to review some key concepts of count data as well as to demonstrate the first of two common statistical…
Akhilesh Gulati
An important concept within TRIZ is that someone, somewhere, has already solved your current problem. In other words, they have “been there, done that.” Or course, the problem has to be clearly stated, in a generic sense, to enable the recognition of existing valid solutions.
TRIZ is not alone in…
Bob Emiliani
The lean community continues to face a problem that hurts efforts to advance progressive lean management: It is the great difficulty in clearly separating and effectively communicating the difference between real lean and fake lean, i.e., lean management done right vs. lean management done wrong…
Arun Hariharan
On a recent visit to Japan, I had an opportunity to visit Toyota’s headquarters. During a meeting with some of its top executives, I asked one of them what role the senior leadership played in Toyota’s much-admired quality philosophy. The reply I received was, like many things about Toyota and…
Joel Smith
Learning to ride a bike is a rite of passage for any kid, so much so that we even use the expression “taking the training wheels off” for all kinds of situations. We say it to mean that we are going to let someone perform an activity on his own after removing some safeguard, even though we know he…
Quality Transformation With David Schwinn
Last evening my wife, Carole, and I attended a celebratory dinner for the family of one of my former students. Luca, my student, originally from Italy, brought his wife, Olivia, and his young daughter, Kendra.
Olivia, originally from Uganda, is a family physician working primarily with…
Patrick Runkel
If you teach statistics or quality statistics, you’re probably already familiar with the cuckoo egg data set.
The common cuckoo has decided that raising baby chicks is a stressful, thankless job. It has better things to do than fill the screeching, gaping maws of cuckoo chicks, day in and day out…
Gary Phillips
For decades now, the measurement systems analysis (MSA) approach has been the predominant method for evaluating measurement systems capability. Although this method is widely considered to be an acceptable and comprehensive approach throughout most of the world, a growing number of specialized…
Donald J. Wheeler
One of the common tools of quality assurance is acceptance sampling. Acceptance sampling uses the observed properties of a sample drawn from a lot or batch to make a decision about whether to accept or reject that lot or batch. While the textbooks are full of complex descriptions of various…
Joel Smith
In part 1, part 2, and part 3, we shared our blind wine-tasting experiment, the survey results, and the experimental results, respectively. To wrap things up, we’re going to see if the survey results tied to the experimental results in any meaningful way.
First, we look at whether self-identified…
Joel Smith
In part 1 of “Blind Wine,” we introduced our blind wine-tasting experimental setup, which included some survey questions asked ahead of time of each participant. In part 2 we looked at the results of that survey. Here we’ll examine how well the survey results align with the experimental results.…
Joel Smith
In part 1, we introduced our blind wine-tasting experimental setup, which included some survey questions asked ahead of time of each participant.
The four questions asked were: 1. On a scale of one to 10, how would you rate your knowledge of wine? 2. How much would you typically spend on a bottle…
Davis Balestracci
I was teaching a class and asked participants to create a control chart of an indicator that was important to them. A lab supervisor presented me with a chart on the number of procedures her department performed and told me that it wasn’t very useful.
She wanted to use the chart for staffing…
Joel Smith
Already relaxed on his first day in Napa, Brutus and his wife, Suzy, decide to visit their favorite winery just before lunch to taste its new Cabernet Sauvignon. The owner recognizes them as they walk in the door and seats them on the patio overlooking the vineyard. Two glasses appear, and as the…
Quality Transformation With David Schwinn
I recently noticed that Starbucks initiated a College Achievement Plan. Starbucks’ partners (employees) who pursue a college degree at Arizona State University (ASU) will receive some combination of tuition reimbursement, scholarships, and other financial aid from the company to help them graduate…
Carly Barry
The Six Sigma students at Rose-Hulman Institute of Technology are at it again! A few months back, we blogged about the Six Sigma project they did to reduce food waste at the on-campus dining center.
This time, the students—led by Dr. Diane Evans, Six Sigma black belt and associate professor of…
MIT Management Executive Education
Lean production, high -performance work systems, virtual communications, and collaboration applications are all examples of the latest tools, technology, and processes executives are encouraged to implement to improve productivity and efficiency. But why are there more useful tools and processes…
Abdallah Samaha
Lin Engineering is a California-based manufacturer of hybrid step motors that was founded in 1987 as a consulting company specializing in step-motor applications. Today, Lin Engineering is the largest manufacturer of 0.9-degree step motors in the motion control industry. As the quality and custom-…
Davis Balestracci
Author's note: To my non-U.S. readers, I apologize for using the sport of baseball to make my points today—and during the World Cup, no less! It’s a perfect context, however, and I hope you will be able to understand the main points.
In my last column, I talked about the different types of control…
Peter J. Sherman
Who says business luncheons are a waste of time? Recently, I enjoyed one of the most productive business luncheons of my career. In February, I was dining with two senior-level professionals at an IT staffing firm. After the usual chitchat about the recent snowstorms and traffic snarls, we started…
Donald J. Wheeler
One of the common tools of quality assurance is acceptance sampling. Acceptance sampling uses the observed properties of a sample drawn from a lot or batch to make a decision about whether to accept or reject that lot or batch. Textbooks are full of complex descriptions of various acceptance…
Patrick Runkel
You know what really gets on my nerves? A lot of things.
That slow, slinky way that cats walk by. Grrrr.
The rude, abrupt arrival of delivery persons in their obnoxiously loud trucks. (Why do they always pull up just as I'm settling down for a nap?) Grrrr.
Total strangers who reach…
Jay Arthur—The KnowWare Man
When looking at any existing process, people often have a hard time visualizing the enormous amount of delay, waste, and nonvalue-added work involved. That’s where a time value map comes in; it makes the invisible waste visible. A time value map shows value-added and nonvalue-added activities and…
Eston Martz
Remember The Little Engine That Could, the children’s story about self-confidence in the face of huge challenges? In it, a train engine keeps telling itself, “I think I can” while carrying a very heavy load up a big mountain. Next thing you know, the little engine has done it, but until that…
Donald J. Wheeler
One thing burned into the brains of those who survive a statistics class is that you have to specify an alpha-level before you do anything statistical. And when it comes to statistical inference, they are correct. But just what does the alpha-level represent? What does it mean in practice? Read on…
Quality Transformation With David Schwinn
This month’s column is about a recent trip to New York and what I learned along the way. About a month ago, we attended the National Band and Orchestra festival at Carnegie Hall. The high school orchestra our granddaughter, Claire, plays in was invited to participate, and we were not about to miss…
Davis Balestracci
My recent columns have emphasized the need for critical thinking to understand the process that produces any data. By just plotting data in their naturally occurring time order, many important questions arise about the data’s “pedigree” (a term coined by my respected colleagues Roger Hoerl and Ron…
Donald J. Wheeler
Who could ever be against having good measurements? Good measurements are like apple pie and motherhood. Since we all want good measurements, it sounds reasonable when people are told to check out the quality of their measurement system before doing an experiment or putting their data on a process…
Davis Balestracci
In my last column, I considered two of the most common questions faced by a statistical educator and the deeper questions that need to be addressed. I encouraged people to consider their everyday reality for the necessary context. Predictably, some become frustrated by my lack of concise answers…
Carly Barry
A few years ago I wrote about the difficulties that can ensue when you’re trying to get started on a lean Six Sigma or quality improvement initiative. What can be especially difficult is having many potential projects and you aren’t sure which one will give the most bang for your buck.
When it…
Mark R. Hamel
What do bus schedules have to do with a lean management system? Quite a bit, even though, obviously, the notion of a bus schedule is more metaphor (or is that analogy?) than reality.
Effective lean management systems are largely constituted by “mechanics” and lean leadership behaviors. The…
Taran March @ Quality Digest
Football is one of life’s mysteries for me. Despite a lifetime of passing television screens where blockish humanoids coalesce and separate against a green background, I can’t get past my shallow impression of huddle and muddle.
However, this has given me at least a rudimentary understanding of…
Bruce Hamilton
For many years I worked for a manufacturer of pressure and temperature switches, a small company with a very big product selection. In our product catalog there were roughly three dozen distinct product families with hundreds of standard products, each available with thousands of optional…
Joel Smith
A couple of years ago, I wrote a blog post titled "What I Learned From Treating Childbirth as Failure" that conveniently ended up getting published the day before my daughter was born. You should read it first, but to summarize, it demonstrates how we can predict the odds of an event happening…
Dan Nelson
When we think of plan-do-check-act (PDCA), W. Edwards Deming might spring to mind… and Walter Shewhart, maybe Kaoru Ishikawa as well. But the thinking that results from PDCA today can most always be traced to Shewhart’s 1939 book, Statistical Method From the Viewpoint of Quality Control; these…
Kevin Meyer
I’ll preface this article by saying that yes, I’m from crazy California. I eat granola with fruits and nuts in the morning, am vegetarian (well, pescatarian), dislike wearing shoes, and practice yoga. At least I don’t have dreadlocks—yet. So there—now you’re warned.
I’m currently winging my way…
Mike Micklewright
Years ago, there was a memorable TV commercial of a toaster waffle that had this very memorable tag line: “Leggo my Eggo.” Today, this product still exists, as does the tag line, but the tag line is much more obscure than it once was.
Today, CEOs and top executives everywhere are quaking in their…
Bruce Hamilton
An old TV series I watched recently reminded me of an experience I’ve had many times in my work. In this I Love Lucy episode, Lucy is ordered by Ricky to create a schedule to make her “more efficient.” A schedule board, posted in their home, is a “best practice,” but without the best intent. The…
Alan Nicol
When we learn the ways of lean methodology, we’re taught that there are two types of waste: pure waste, which needs to be eliminated; and necessary waste, which does nothing to improve our performance or profits but must be produced anyway.
I’ve decided that there’s a third type of waste, called…
Patrick Runkel
My previous article examined how an equivalence test can shift the burden of proof when you perform a hypothesis test of the means. This allows you to more rigorously test whether the process mean is equivalent to a target or to another mean.
Here’s another key difference: To perform the analysis…
Ryan E. Day
And so the debate rages on about whether the wildly popular Flappy Bird app is actually a tool for teaching lean or teaching theory of constraints. Really? No, not really. But at least I’m not the only one thinking about it.
Actually, it was Jens Woinowski’s article “What You Can Learn about Lean…
Patrick Runkel
With more options come more decisions. With equivalence testing added to Minitab 17, you now have more statistical tools to test a sample mean against target value or another sample mean.
Equivalence testing is extensively used in the biomedical field. Pharmaceutical manufacturers often need to…
Dan Nelson
Why is internal auditing important to your quality management system (QMS)? To ensure that processes conform to ISO 9001 requirements, or to ensure that the company conforms to management’s own defined plans? Although audits can be done for both reasons, the second choice is more important.…
Davis Balestracci
To summarize my last three articles, most improvement approaches come out of the same theory and are based on the assumption that everything is a process.
The universal process flowchart in Figure 1 sums it up beautifully. The boxes at the top are how executives think the process works. The…
Lean Math With Mark Hamel
Available time for changeovers per period (Ta∆), also called available time for (internal) setups, represents the time per a given period (e.g., day, shift, week) during which a machine, equipment, or resource can be changed over (i.e., from one product to another, prepared for a different medical…
Carly Barry
Ugh, your process is producing some parts that don’t meet your customer’s specifications. Fortunately, after a little hard work, you find a way to improve the process.
However, you want to perform the appropriate statistical analysis to back up your findings and make it easier to explain the…
David Muil
Management systems are sometimes misunderstood as nothing more than a heavy administrative burden providing limited business benefit. In fact, many organizations with management systems in place haven’t effectively defined the processes they actually employ at all. Perhaps it’s because they think…
Donald J. Wheeler
Why bother to plot your data? A simple shortcut is available that will allow you to do your analysis without the data getting in the way. How do you accomplish this breakthrough? Read on.
This marvelous advance in analysis is known as the “data-free graph.” As usual we begin with a collection of…
Mike Micklewright
Editor’s note: This article discusses topics covered at greater length in episodes 19–23 of a new streaming video training series, Creating and Sustaining Lean Improvements—Integrating Principles, Culture, and Tools by the author and 360 Performance Circle, a sister company to Quality Digest.…
Matthew J. Savage
Lori, a software customer, phoned to ask if Cpk is the best statistic to use in a process that slits metal to exacting widths. As a PQ Systems technical support analyst, I too wondered what index would be best suited for her application, a highly specialized one. Perhaps Cpk, Ppk, Cpm, or some…
Bruno Scibilia
My main objective is to encourage greater use of statistical techniques in the service sector and present new ways to implement them.
In a previous blog, I presented an approach you can use to identify process steps that may be improved in the service sector (quartile analysis). here I’ll show…
Matthew Barsalou
While reading a list of 5S activities, I thought, “Am I mistaken?” The activities on the list didn’t match what I thought they should be. I dug a little deeper and discovered there has been a lot of variation in the translation from Japanese to English for the methodology called 5S, which is often…
Lean Math With Mark Hamel
Triangle kanban, one of three types of signal kanban, is unique in that there is only a single kanban per part number or stock-keeping unit. Accordingly, kanban-sizing math has nothing to do with determining the number of kanban; that’s obviously fixed.
Instead, the math is focused on determining…
Davis Balestracci
My last column, “Can We Please Stop the Guru Wars?” made the case that the various improvement approaches are all pretty much the same. To recap, there are seven sources of problems with a process. The first three sources help frame the situation.
They are: Source No. 1. Inadequate knowledge of…
Bruce Hamilton
Across a large swath of the United States, the winter has been especially cold, snowy, and dreary this year. So here’s a post with a link to a cheery video at the end, just to pick my spirits up—and maybe yours, too.
The English language can be confounding. For example, the word “turkey” is slang…
Jim Benson
How do you know when to clean up your kanban’s Done column? When it’s full.
When we showed our board to people in classes and on consulting engagements, the Done column showed that we were really, really productive. It was huge. It went on forever. Hundreds of completed tasks.
So, how do we clean…
Donald J. Wheeler
Students typically encounter many obstacles while learning statistics. In 44 years of teaching I have discovered some distinctions that help students overcome these obstacles. This article will remove some sources of confusion concerning the relationship between statistical process control (SPC)…
Quality Transformation With David Schwinn
I was reminded recently of the passing of Thomas Berry, one of the most eminent cultural historians of our time. His work and insight have been touchstones for me for the last 30 years.
For me, the story starts in 1993 when my wife, Carole, and I were invited to help the folks in the North Simcoe…
Jay Arthur—The KnowWare Man
Let’s face it: Everyone isn’t cut out to be a belted Six Sigma guru, but everyone should know how to use key tools in the right order to solve the problems facing businesses. And they can’t wait months or years to get results; the marketplace moves too quickly.
During the early 1990s, I attended…
Mark R. Hamel
Larry Loucka, a close friend and colleague, recently pointed me to a Feb. 16, 2014, article in The Wall Street Journal (WSJ). Now, before you roll your eyes and give me the WSJ-isn’t known-for-getting-the-lean-thing-right look, hear me out. What the journal published is really, really good stuff—…
Bob Emiliani
Let’s get rid of value stream maps. I can hear it now: “Why would you say such a thing? Value stream maps are great. We can’t see waste without them.”
Precisely.
Value stream maps have developed an outsized importance in relation to other types of basic information that one gathers when trying to…
Mike Micklewright
Editor’s note: Mike Micklewright will be a guest on Quality Digest Live, on Feb. 28, 2014, at 11 a.m. Pacific/2 p.m. Eastern. Micklewright will also present a webinar, “Sustaining Lean Improvements While Adding Spark to Your QMS,” on March 6, 2014, at 11 a.m. Pacific/2 p.m. Eastern.
Many years ago…
John Flaig
Engineers have used safety margins for centuries to protect their companies and customers from the consequences of product degradation and failure. Sometimes the safety margins are fairly obvious (e.g., maximum-load limits posted in elevators), and other times they’re not.
Design margins are…
Mark Rosenthal
Over the years, I’ve observed a number of efforts at various companies to implement A3 problem solving, an approach based on the plan-do-check-act (PDCA) cycle that summarizes the problem and solution on a folded form, usually 11 in. × 17 in. I worked for some of those companies; I’ve observed…
Alan Nicol
In part one, we looked at the importance of understanding findings in order to make better decisions. To do this we and our decision-making leaders must become adept at data investigation and analysis so we can ask critical questions.
In part two I want to emphasize another truth that will prevent…
Eston Martz
In part one, I shared a case study of how a small bicycle-chain manufacturing company in India used Six Sigma’s DMAIC approach to reverse declining productivity. After completing the define, measure, and analysis phases, the team had identified the important factors in the bushing creation process…
Mike Figliuolo
PowerPoint is the devil’s instrument, and when you use it, you risk becoming a musician in his demonic orchestra. All of us are required to give presentations in some form or fashion at various points in our careers. If you’d like to succeed in those efforts, there are three things you should never…
Eston Martz
Using data analysis and statistics to improve business quality has a long history. But it often seems like most of that history involves huge operations. After all, Six Sigma originated with Motorola, and was embraced by thousands of other businesses after it was adopted by a little-known outfit…
Akhilesh Gulati
Editor’s note: This article continues the series exploring structured innovation using the TRIZ methodology, a problem solving, analysis, and forecasting tool derived from studying patterns of invention found in global patent data.
Belinda started the My Executive Council (MEC) meeting on an upbeat…
Davis Balestracci
The various improvement approaches are, in essence, all pretty much the same. Any competent practitioner would neither want to be called a “guru” nor have any problems dealing with another competent practitioner of another improvement philosophy.
In my opinion, any approach should also involve the…
Donald J. Wheeler
Last month in “The Analysis of Experimental Data,” I presented a method for analyzing experimental data that was built on the use of the range statistic as a measure of dispersion. In this day of computers and software, why should we even consider using ranges in our analysis of experimental data…
Carly Barry
I had the opportunity to speak with a great group of students from the New Jersey Governor’s School of Engineering and Technology—a summer program for high-achieving high school students. Students in the program complete a set of challenging courses while working in small groups on real-world…
Tom Kadala
With 90 percent of the world’s data created during the last two years, what can we expect our data vaults to hold two or even 20 years from now? Today we measure our lives in peta-bytes, but by 2020 estimates show a 2,300-percent increase in the bits and bytes that will define our lives.
How then…
Tripp Babbitt
W. Edwards Deming is often given as the source for the following quote: “Managing a business on historical data is like driving a car while looking in the rearview mirror.” Deming actually borrowed the quote from Myron Tribus. The idea is that management should be looking ahead and not behind.…
Davis Balestracci
For all the talk about the power of control charts, I can empathize when audiences taking mandated courses on quality tools are left puzzled. When I look at training materials or books, their tendency is to bog down heavily in the mechanics of construction without offering a clue about…
Jim Frost
Ihave written a number of blog posts about regression analysis, and I think it would be helpful to collect them in this post to create a regression tutorial. I’ll supplement my own posts with some from my colleagues.
This tutorial covers many aspects of regression analysis, including choosing the…
Carly Barry
In my first post in this series, I mentioned that Minitab reached out to our customers who are practitioners of quality improvement to better understand how they complete projects, what tools they use, and the challenges they come across in achieving quality initiatives. One area they said they…
Arun Hariharan
I know the CEO of a group of large companies who is a big believer in small, continuous improvements—primarily through ideas from employees on how to improve their own work or processes. This group also has Six Sigma experts, some of whom privately believed that small improvements weren’t worth…
A few days ago we received an email from a friend at a machine shop. He had just finished a process capability analysis for a critical feature (a runout on a cylindrical part) and was shocked by the output. The spreadsheet software he used showed him a process capability (Cpk) of 0.39 (see figure…
Quality Transformation With David Schwinn
I just finished participating in a delightful design charrette. I’m sharing this with you because design can be a very powerful tool in the Six Sigma arsenal, and this little charrette both reminded me of and taught me a few important lessons about the design process.
Lansing Community College,…
Quality Transformation With David Schwinn
Story update 12/06/2013: Wow did we mess up. When this story originally published we, the editors, introduced an error into the story regarding the Alaskan oil spill (which the author hadn't mentioned in his original) and didn't realize it. When readers pointed out the error we compounded the…
Cody Steele
Capability statistics are wonderful things. They tell you how well your process is meeting the specifications that you have. But there are so many capability statistics that it’s worth taking some time to understand how they’re useful together.
Two capability statistics that are hard to keep…
Carly Barry
In part one and part two of this series, I've outlined some reasons why a lean Six Sigma project might have been deemed a failure. We’ve gathered many of these reasons from surveying and talking with our customers. I'd like to present a few more reasons and then share some advice from Minitab…
Kyle Toppazzini
In the lean Six Sigma framework, we normally define what is called the critical-to-quality (CTQ) characteristics. A CTQ characteristic is any feature or product that is important to the customer. However, in the FUSE framework, which stands for formulate, understand, synthesize, and execute, we…
Carly Barry
In part one, I discussed how to avoid a lean Six Sigma project failure, specifically if the reason behind the failure is that the project solution never gets implemented. Now let’s discuss a few other project roadblocks that prevent teams from completing projects and some suggestions for…
Bruce Hamilton
Many managers ask me, “How can I accelerate my company’s lean transformation?” My answer is twofold: First get the direction right, and then get everyone rowing in that direction.
One of my columns on this topic from about three years ago (worth reading for context if you don’t remember it),…
Patrick Runkel
Defects can cause a lot of pain to your customer. They can also cause a lot of pain inside your body.
The picture below shows my broken right clavicle. Ouch! You might think of it as the defective output from my bicycling process, which needs improvement.
Sitting around all summer cinched up in…
Paul Naysmith
Arecent call with an old colleague from Europe got me wondering about a question that few are conscious of: Who is the customer of your quality document? Oh boy, did we have an interesting discussion about quality systems.
My friend was developing and reinvigorating his employer’s quality system,…
Kyle Toppazzini
Before my first book, Maximizing Lean Six Sigma (West Bow Press, 2013), was published, I’d begun work on a second book, which details a new approach to lean Six Sigma called FUSE—for formulate, understand, synthesize, and execute. It’s an approach that enables organizations to maximize enterprise…
Lean Math With Mark Hamel
The time observation form, also known as a process study form, is a basic and often-used tool for lean practitioners. Note that here we are talking about applying the continuous time-observation method and not the work-sampling method.
The form, in combination with a stopwatch, serves multiple…
Rick Haynes
Measurement system analysis of uncertainty is one topic in lean Six Sigma training that is too often ignored or under-taught. I believe that it is under-taught because most instructors have never used or understood it. Therefore, this column will dive deep into what it is and why you should learn…
Kyle Toppazzini
How many of you have been through a lean Six Sigma (LSS) project or business transformation and there was no internal conflict between employees or among managers? My guess is very few. In any LSS project, company transformation, or change initiative there are going to be instances of love and war…
Tripp Babbitt
S
ometimes it’s necessary for a person to offer up views that seem to be an affront. Because these views often challenge the status quo, people’s reactions can be mixed. Some will consider the person a heretic for expressing them, and others will wonder why anyone would say such a thing. The…
Lean Math With Mark Hamel
Work content (Wc) represents total operator cycle time or, if multiple operators are involved, the sum of operator cycle times to perform a specific process(es) or subprocess(es). The scope of human work, including both value-added and nonvalue-added activities, may encompass a complete value…
Mona K. Draper
Maersk Line is the largest container shipping company in the world. At any given time, its 500 vessels transport approximately 3 percent of the world's gross national product (GNP). In 2007, I walked into Maersk as a lean Six Sigma consultant looking for business and walked out with a job.
I saw…
Carly Barry
To promote ethical and moral responsibility in shaping its graduates, the Rose-Hulman Institute of Technology created a sustainability initiative to reduce its own environmental footprint.
As part of that team’s efforts, Six Sigma students at Rose-Hulman conducted a project to reduce food waste…
Arun Hariharan
During the past dozen years, companies I have worked with have, between them, completed more than 1,000 lean Six Sigma (LSS) projects. Based on this experience, I’ve found that improvement projects can be broadly categorized into three types: quality-improvement, revenue-enhancing, and cost-saving…
Michael Ray Fincher
For me, a quality professional with 20 years experience in manufacturing—producing everything from garbage bags to luxury ski boats—my transition to the service industry was a shocking experience to say the least. It was not without challenges, I must confess.
When I was asked to join the…
Bruno Scibilia
All processes are affected by various sources of variations over time. Products that are designed based on optimal settings will, in reality, tend to drift away from their ideal settings during the manufacturing process.
Environmental fluctuations and process variability often cause major quality…
Bull Wranglers
There are more than 1,100 textbooks referring to “short-term process capability,” as distinct from “long term.” Surely 1,100 textbooks can’t be wrong? Let’s apply the first Bull Wrangler test. Does short- and long-term process capability make common sense?
What is capability?
According to ISO…
Akhilesh Gulati
Editor’s note: This article continues the series exploring structured innovation using the TRIZ methodology, a problem-solving, analysis, and forecasting tool derived from studying patterns of invention found in global patent data.
Belinda started the My Executive Council (MEC) meeting with the…
Kyle Toppazzini
One of the recurring sentiments I hear from business executives is that lean Six Sigma (LSS) simply takes too long to implement. Without senior management buy-in, implementing it is not only difficult, it’s also nearly impossible. What if there were an easier way that resulted in faster…
Quality Digest
On March 28, 2013, the world lost a person whom many consider to be a major contributor to the world of industrial statistics: George E. P. Box. Relatively unknown outside the world of statistics, Box was certainly very well known by those who have studied or practiced industrial statistics.
His…
John Flaig
What’s wrong with root cause analysis? Let’s begin with the name, which is singular. It implies that there is only one root cause, when in reality most problems are usually caused by a complex combination of several factors, some of which are more significant than others.
To appreciate this point…
James Brewton
During the past 20 years, lean Six Sigma (LSS) has proven itself as an effective strategy for business success in virtually every industry sector. The methodology has helped organizations realize their processes are the engines that drive operational excellence and customer value. Recently,…
Cody Steele
Statistician to the Stars William Briggs deserves credit for his correct prediction of the Best Picture Oscar the day before the ceremonies this year. Although Briggs would never encourage anyone to misuse his model this way, I feel my statistics heartstrings strummed by the desire to remind…
Keith McDavit
Last weekend I decided to change the oil and tune up my classic car, a 1972 Datsun 1200. (My wife has other names for it.) It sports a “four on the floor” and a simple four-cylinder engine that doesn’t even need fancy smog controls. Since I hadn’t tinkered with this car in a long while, I was…
John Flaig
There are many different process control methods and procedures available to the quality practitioner. A popular but problematic visual technique employs the traffic light analogy.
As discussed in the article, “Stoplight Charts With SPC Inside,” by Steven Prevette (Quality Progress, 2004), the…
Kyle Toppazzini
One of the most challenging issues I hear from people within the lean Six Sigma community is how to ensure that a lean Six Sigma project is sustainable. If your lean Six Sigma project is highly dependent on top leadership support to keep it going, there’s a risk of losing the focus and support when…
Eric Heckman
It’s your first day at the Jedi Temple, working as a lightsaber manufacturer. Your first task on the job is to run a capability analysis on the length of lightsabers being produced. Your main concern is to see if the lightsabers fit within the required length specifications set forth by the Jedi…
Kyle Toppazzini
Allow me to introduce you to FUSE, a value-based lean Six Sigma model that enables organizations to maximize enterprise performance with the least friction. FUSE embodies three core Chinese concepts of trust (shin), relationships (gunaxi), and knowledge (zhi), or more specifically, reflective…
Quality Transformation With David Schwinn
Ron Behrens, an old friend and colleague, recently replied to my invitation to share examples of the intelligent use of statistics, such as that used in our Six Sigma projects. I asked for stories, some data, and some statistical analyses. With his response, he noted that I had probably already…
Kyle Toppazzini
In lean Six Sigma, the concept of voice of the customer (VOC) is paramount. VOC takes into account the customer’s wants and needs. But I believe this concept falls short in taking into account the wants, needs, and concerns of all aspects of an enterprise. We may not get the support we need to be…
Kyle Toppazzini
The three value concepts of my new lean Six Sigma model are based on the Chinese terms shin, gunaxi, and zhi. The third term, zhi, means to know or understand. Confucius believed that for most people, learning was ongoing. One of the philosophies of Confucianism is that everything a person learns…
Matthew Barsalou
Six Sigma was originally created by Bob Gavin at Motorola during the 1980s; however, it could be argued that a comparable methodology was in use as early as the 1850s. Florence Nightingale is known for founding the field of nursing, but few people outside of the field of mathematics appreciate her…
Bruce Hamilton
Last week I visited with JVS, a terrific Boston-area organization whose mission is “to empower individuals from diverse communities to find employment and build careers, and to partner with employers to hire, develop, and retain productive workforces.”
I was reminded of my first experience with…
Joel Smith
It’s no secret that in the world of statistics, the individuals chart and X-bar chart are pretty much the popular kids in school. But have you ever met their cousin EWMA? He’s all about exponentially weighted moving averages (EWMA). That’s him in the middle of the class, wearing the clothes that…
Jon Miller
At the heart of the Toyota Way are two pillars, continuous improvement and respect for people. These are supported by five values: challenge, improvement (kaizen), seeing for yourself (genchi genbutsu), respect, and teamwork. The word “challenge” means either a tangible thing, such as competition…
Matthew E. May
In our world of excess everything, savvy innovators realize that less is actually best. They know that delivering a memorable and meaningful experience hinges on user engagement, which is best achieved through a subtractive approach. Anything excessive, confusing, or wasteful is intelligently and…
Mark R. Hamel
Isee the same cycle in so many places. What cycle? A five-step process for ensuring that ideas fail.
Step 1: Altruistic leaders encourage suggestions and ask associates for their continuous improvement ideas in an attempt to foment some daily kaizen. Step 2: Associates (not all of them), somewhat…
Anthony Burns’ opinion piece, “Six Sigma Psychology” published in the Oct. 25, 2012, edition of Quality Digest Daily, piqued my interest. I read it in anticipation of discovering a candy house waiting at the end of a long dark path, along with suggestions about how to avoid the oven. Perhaps I’d…
Quality Transformation With David Schwinn
It may seem dangerous to ask questions, especially in an environment that is hostile to change. The heart of improvement often lies in listening to many viewpoints in order to involve people affected by the outcome. In an environment of trust, it’s okay to disagree with the boss. W. Edwards Deming…
Forrest Breyfogle—New Paradigms
A report of how a process performs is not only a function of process characteristics and sampling chance differences. It can also depend on sampling approach. For example, one person could describe a process as out of control, which would lead to activities that address process perturbations as…
Kyle Toppazzini
I have seen organizational lean or lean Six Sigma job requirements stating that any level of certification from almost any institution is acceptable, at least according to the recruiter. But guess what? Taking a four-hour online course on lean, lean Six Sigma, or any other quality management…
Rip Stauffer
Editor’s note: In response to Kyle Toppazzini’s article, “Lean Without Six Sigma May Be a Failing Proposition,” published in the Sept. 27, 2012, issue of Quality Digest Daily, Rip Stauffer left the following observant comment.
I started my career in quality when the consulting world hadn’t yet…
Jay Arthur—The KnowWare Man
I went into my local Barnes & Noble looking for a book and decided to check if they carried my book, Lean Six Sigma Demystified. There were four rows of business books on management, leadership, sales, and so on. The “quality” section, consisting of about 15 titles, was on the bottom shelf of…
Kyle Toppazzini
In a Harvard Business Review article Tom Davenport writes, “I hope that when companies start getting excited again about process improvement, they resist one method for doing so. A hybrid, combined approach is really the only approach that makes any sense. In religion many people worship only one…
Davis Balestracci
Editor’s note: This is the third of a three-part series on effective, focused data analysis. Part one discussed helping management deal with common cause; the first common cause strategy—stratification—was discussed in part two.
In my last column, I introduced some aspects of common cause…
Paul Naysmith
I’m back, writing about another Toyota dilemma of mine. In part one, interestingly titled “My Toyota Dilemma,” I wrote how I, as an avid fan and supporter of the Toyota Production System (TPS) have never owned a Toyota. I ended that column vowing I would use Toyota’s greatest gift—the 5 Whys—to…
Kyle Toppazzini
Another transformation initiative has been announced in your organization and you think to yourself, “How much change are we expected to undertake?” In a lean Six Sigma engagement, it is imperative to take into consideration the number of ongoing and past change initiatives. This article explains…
Carly Barry
I recently had the chance to talk to Brett Warland, global director of process improvement at PolyOne Corp. The word “global” is often present in the titles of many organizations’ process improvement programs and employee job titles that deal with quality. This can convey not only an international…
Kyle Toppazzini
A s you may be aware, causality is critical in strategy execution. Without causality, it is nearly impossible to measure the impact of various strategic initiatives of a company’s overall goals; therefore, it would be difficult to tell if you were headed in the right direction, a situation similar…
Kyle Toppazzini
Whenever I write about continuous improvement and lean Six Sigma, without fail I get a comment about Toyota and its quality issues. So I decided to investigate this matter further, present the facts, and let the data be the voice of reason. I do expect the proverbial “Yabut and Costello” comments—i…
Kyle Toppazzini
I can’t tell you how many times I’ve heard, “We don’t have the data for this. I guess we’ll need to make an educated guess.” In the lean Six Sigma engagements I work on, my response to this is, “Let’s create the data.” Without fail, I get the deer-in-the-headlights stare for a couple of seconds…
Quality Transformation With David Schwinn
One of the most important events I remember experiencing years ago as part of my MBA was an introductory conversation I had with J. B. Black, Jr., a dean at Wright State University. One of the things I learned from Black was that a most important part of my forthcoming job as a manager was to “make…
Mark Graban
When I was a guest on Quality Digest Live, co-host Dirk Dusharme asked me about hesitations that some health care professionals might have about the lean concept of “standardized work.” As you can see in the show’s archived recording, I talked about how the increased standardization of core…
Donald J. Wheeler
In a class last month I was asked to explain a number that occurs in some measurement system evaluations and which is known as the precision to tolerance ratio (P/T ratio). As I will show in this column, it turns out to be related to the capability ratio.
We will need some notation in what follows…
Bruce Hamilton
When I was in production, we used the term “waves” to describe the ebb and flow of work to the factory. Some days there would be very little, and others a big heaping pile. When the waves came, we worked overtime, bumped queues, and sometimes used less experienced workers to fill in gaps. So-called…
Dawn Keller
I love product development and quality engineering. There are days when I can’t believe that I actually get paid to do this. Between you and me, I’d do this work for a lot less money. In fact, even on the days that I hate the particular circumstances of my job, I still love my job. If that makes…
Davis Balestracci
I am in the midst of teaching an online MBA course in statistical thinking. This is actually my second go-round, and I've heavily revised my inherited materials, which were well-meaning but had some obvious gaps.
ADVERTISEMENT
I insisted on using Brian Joiner’s Fourth Generation Management…
Kevin Rudy
If you like baseball pitching statistics, then you’ve loved the month of June. On the first of the month, Johan Santana pitched the first no-hitter in Mets history. Then a week later, the Seattle Mariners used six different pitchers to do the same thing, which tied the Major League Baseball record…
Dawn Keller
I remember a time in my career when I mistakenly thought I knew statistics—really knew statistics. It was before I met Yanling Zuo, Michelle Paret, Eduardo Santiago, and a whole host of other statistical experts. I was a quality engineer, and I’d been applying statistics for years. I assumed that…
Jay Arthur—The KnowWare Man
Although Quality Digest often has in-depth articles about the nuances of control charts, I’ve found that many beginners are at a loss to figure out how to organize their data, especially in service industries such as health care, hotels, and food. They complain that the examples are all…
Steve Wise
Selecting the right control chart starts by knowing something about what you want the chart to say about the process—what questions do you want the chart to answer? Another way to look at this is to ask yourself, “Why am I collecting data on this part?” The answers to these questions will provide…
Bruce Hamilton
I think there are no new airplane stories left for those of us who take to the not-always-friendly skies, but having been on one of those super delay specials recently and coincidentally not caring especially about being hours late (I had booked a full day of buffer as a hedge against possible…
Mark R. Hamel
Recently, fellow-blogger David Kasprzak, introduced me to the Results-Only Work Environment (ROWE) strategy. ROWE, created at Best Buy’s Minneapolis headquarters, espouses a philosophy under which employees can work where they want, when they want, and how they want—as long as the work gets done.…
Jim Frost
If you combine tough economic times with a presidential election year, you get a heightened interest in how the economy is changing. Is it growing faster or slowing down? Unsurprisingly, there are many contradictory predictions about what will happen over the longer term. You’ll find countless TV…
Jim Frost
This is part two in a three-part series where we assess what information we can obtain from the various estimates of quarterly GDP growth using statistical analysis and a control chart. Read part one here, and part three here.
An I-MR chart comprises two plots, the individuals (I) chart on the top…
Stewart Anderson
What is the economic rationale for pursuing lean production? Much of the lean literature is concerned with the nuts and bolts of lean, and the economics of lean are somewhat less publicized. This article attempts to redress that imbalance, albeit in a very condensed way.
Firms employ capital and…
Patrick Runkel
Meet Betty and Bart Bickerson, husband-and-wife quality analysts who work at different companies. Betty and Bart argue about everything. They argue whether grey is a color. They argue whether tomato is a fruit. They argue whether the chicken came before the egg, and whether the egg tastes better…
Tom Pyzdek
One of the cornerstones of quality and lean Six Sigma is data: “We insist on it.” “Don’t tell us what you think the situation is; let the data do the talking.” “In God we trust—all others bring data.” You get the idea.
An unfortunate side effect of this emphasis is the proliferation of useless…
Carly Barry
I found that training to run a marathon is a lot like completing a quality improvement project. I ran my first full marathon in November 2011, and as I was completing my training, I came across this quote about quality improvement from V. Daniel Hunt, quality management improvement author and CEO…
Donald J. Wheeler
I
n my February 1996 Quality Digest column I discussed an article out of USA Today. Since that article provides a great example of how we need to filter out the noise whenever we attempt to interpret data, I have updated it for my column today. “Teen Use Turns Upward” read the headline for a graph…
MIT News
The information age is also the age of information overload. Companies, governments, researchers, and private citizens are accumulating digital data at an unprecedented rate, and amid all those quintillions of bytes could be the answers to questions of vital human interest: What environmental…
James Brewton
Lean Six Sigma has proven itself as an effective strategy for business success in both private and public sectors. The methodology has helped enterprise leaders recognize business processes as engines that drive performance excellence and help to deliver value. Lean Six Sigma offers a…
Eston Martz
It’s all too easy to make mistakes involving statistics. Statistical software can remove a lot of the difficulty surrounding statistical calculation, reducing the risk of mathematical errors, but correctly interpreting the results of an analysis can be even more challenging.
A few years ago,…
ASQ
(ASQ: Milwaukee, WI) -- The results of ASQ’s 25th annual Salary Survey show strong average salaries for quality professionals in 2011 and fewer lay-offs as companies continue to see the value of quality and its positive impact on an organization.
The survey results also show that experience…
Donald J. Wheeler
Many times measurements are made using measurement increments which are too large for the job. Fortunately this problem is easily detected by ordinary, production-line process behavior charts. No special studies are necessary; no standard parts or batches are needed. You simply need to…
FARO
In production plants across the globe, lean manufacturing techniques are being used to meet increasing demands placed on manufacturers. Originally developed as a methodology to make production processes highly efficient, lean techniques have been adopted by more than 72 percent of machine shops…
The teaching of lean concepts is typically tuned to continuous processes: Day in, day out, value flows continuously from suppliers until the final product reaches the customer. The concepts of lead time (the time it takes individual “flow-units” to travel through a process), Takt time (the…
Mark R. Hamel
During the first winter storm this year in the Northeast, I found myself, along with hundreds of thousands of folks in the area, without power for the better part of a week. It was a long wait before the lights came on… and the heat.
Heck, they had to send the National Guard to my town, and…
Bruce Hamilton
A short time after I moved into operations as the vice president of manufacturing, our assembly department made an early and, dare I say, imperfect attempt to realign the factory floor for ease-of-material delivery and pick up. I would not describe this as improved flow because we were still…
Jay Arthur—The KnowWare Man
At a recent health-care conference I had a conversation with Mary, a Six Sigma Black Belt for a 700-bed hospital. She told me that the hospital had only a few copies of Minitab software, which was shared by several people. She was always being asked to close out of the program so that someone…
Donald J. Wheeler
From the perspective of data analysis, rare events are problematic. Until we have an event,
there is nothing to count, and as a result many of our time periods will end up with zero counts.
Since zero counts contain no real information, we need to consider alternatives to counting the rare…
Jay Arthur—The KnowWare Man
For the last decade, people have come by my booth at the American Society for Quality (ASQ) World Conference on Quality and Improvement and asked: “Isn’t there a better way to implement Six Sigma that doesn’t cost so much or take so long?” Of course there is, but conventional wisdom inhibits…
Jay Arthur—The KnowWare Man
Ask almost anyone what is the No. 1 requirement for Six Sigma success, and he will say: top leadership commitment. It’s easy to look at Six Sigma successes like General Electric (GE) under Jack Welch and use them as evidence of the power of leadership commitment. The belief is so often repeated…
Mark R. Hamel
Some lies you can see a mile away: “The check is in the mail.” “Your table will be ready in a few minutes.” “I didn’t say that.” “This won’t hurt a bit.” Add to this rather long list some lies of the lean variety. I’ve heard more than my fair share.
Often, I just shake off the falsehoods and…
Steve Moore
The quote “Baseball been berry, berry good to me” comes from one of my favorite Saturday Night Live skits from the late 1970s. Garrett Morris played Chico Escuela, a retired Hispanic baseball player who knew very little English. His pat answer for most questions—“Baseball been berry, berry good…
Bruce Hamilton
I was listening to Alan Robinson present recently at the Lean Systems Summit about the power of “small ideas.” Alan wondered aloud why so many organizations continue to pursue the few million-dollar ideas while small ideas account for more than 75 percent of the innovation outcome.
I reflected…
Mark R. Hamel
Regular tiered meetings are a staple of any company’s lean management system. The quick stand-up meetings represent part of the daily accountability process which, when combined with leader standard work and visual controls, provide the foundation for sustaining gains, rigorously practicing…
Davis Balestracci
Any article about control charts leads to inevitable (and torturous) discussions of special cause tests—all nine of them. No wonder confused people continue to use things like trend lines. But I’m getting ahead of myself.
ADVERTISEMENT
First of all,…
Steven Ouellette
Let's face it—many industrial researchers, including Six Sigma Black Belts, do a terrible job of planning the research they need to do to perform their jobs efficiently. See that guy over there? Yeah, he is the one I am talking about, so you should read this article so you can help the poor…
John Flaig
A run chart is a graphical display of data over time. Run charts are used to visually analyze processes according to time or sequential order. They are useful in assessing process stability, discovering patterns in data, and facilitating process diagnosis and appropriate improvement actions.…
Mark R. Hamel
First, the introduction. This post was earnestly written by my friend, Jeff Fuchs. He’s the director of the Maryland World Class Consortia, a lean nonprofit assistance organization in the mid-Atlantic. He’s also president of Neovista Consulting, which works with large and small organizations on…
Donald J. Wheeler
With the use of statistical software, many individuals are being exposed to more than just measures of location and dispersion. In addition to the average and standard deviation, they often find some funny numbers labeled as skewness and kurtosis. Since these numbers appear automatically, it is…
Minitab LLC
C
otton. Given that it’s the most widely used fiber in clothing, you’re probably wearing some right now. We love cotton’s comfortable properties and soft feel. But as everyone who’s ironed a cotton shirt or pants knows, these same properties can make cotton-based fabric particularly prone to…
Bruce Hamilton
Significant digits, the number of digits to the right of a decimal point that are warranted by the accuracy of the means of measurement, are a critical part of scientific investigation. In developing products and services, the concept is essential. For example, how many products have failed to “…
Productivity Press
Of the 100 companies named to Fortune magazine’s list of the world’s largest companies in 1956, only 29 of them remain on that list today. Many lost their way because they failed to recognize the changes taking place, or were too big to react quickly enough to shifting market conditions.…
John Flaig
Story update 7/08/2011: We corrected an error in Figure 2, and in the section preceded by "Expressed symbolically for a stable process...".
Two topics that have generated significant interest and frequent comments are, “Is normality required for control charts?” and “You need to estimate the tail…
Steven Ouellette
Although we may use the define, measure, analyze, improve, control (DMAIC) mnemonic to help guide us through our problem solving, that doesn’t really give us a lot of specific direction (as I bemoan in my Top 10 Stupid Six Sigma Tricks No. 4). Good experimental design technique is critical to being…
It seemed like a good idea at the time to Jon Shupenus, U.S. Army Forces Command’s process improvement specialist and lean Six Sigma Black Belt. Shupenus was attending a Department of Defense performance management seminar in 2010 when Kirk Nicholas, director of the Army’s continuous process…
Stewart Anderson
Not all customers are equally profitable. Different customers have different needs, and hence different costs to serve. The overall profitability of a business is a function of the profitability of individual customers and customer groups.
Many businesses measure customer satisfaction but they…
Paul Naysmith
I greatly believe in training. I have been fortunate to work in businesses that also believed in having trained and qualified professionals in their organization. I have personally and professionally benefited from that philosophy, and I have gained new knowledge as a result.
Since graduating from…
Stewart Anderson
Often a firm is confronted with the key question of whether the quality of its products and services should be improved. For many readers, the question may even seem illogical: How could it not be beneficial for a firm to improve the quality of its products and services?
On closer analysis, however…
Donald J. Wheeler
Whenever we present capability indexes the almost inevitable follow-up question is, “What is the fraction nonconforming?” What this question usually means is, “Tell me what these capability indexes mean in terms that I can understand.” These questions have resulted in multiple approaches to…
Mike Richman
Last month I wrote an article entitled “Being Comfortable in a World of Never-Ending Change.” Editor in Chief Dirk Dusharme and I also covered this story on the April 29th edition of Quality Digest Live (QDL). QDL, by the way, is our live video show wrap-up of the week’s top industry news and…
Tom Pyzdek
Lean, Six Sigma, and quality provide a set of tools and a framework for achieving excellence in any process. Quality professionals are able to help organizations determine if customer requirements are properly defined and if the organization is meeting those requirements. Lean practitioners have a…
Mark R. Hamel
Among other things, an effective lean management system drives process adherence and process performance. The daily accountability portion of the system includes brief tiered meetings with the stakeholders.
At the tier I level, the core meeting participants are pretty much the natural work team…
Ryan E. Day
For those of us frustrated by the prevalence of mediocrity and apathy in the management theater, there may yet be hope. The Avery Point Group’s annual employment study found a sharp increase in demand for lean and Six Sigma skills this year. That would seem to indicate companies and businesses…
William A. Levinson
The cause-and-effect diagram is one of the seven basic quality improvement tools, and this article will illustrate its synergy with the affinity diagram. The article will then discuss how modern computer technology can enhance both techniques to create keyword-searchable quality records that…
John Flaig
In the article, “Four Control Chart Myths from Foolish Experts,” by Davis Balestracci (Quality Digest Daily, March 30, 2011) the following comments were made regarding what Balestracci considers statistical process control (SPC) myths:
“Myth No. 4: Three standard deviation limits are too…
Quality Transformation With David Schwinn
As we continue our sabbatical journey, more opportunities for the improvement of management practices continue to appear. This month, the overriding theme that I have observed is the lack of front-line performance that seems to be a result of the system. I have been reminded of the many times we as…
Angelo Lyall
It seems the most popular way to improve a process these days is by applying the glorious "Lean Toolkit." Many companies focus on learning and implementing process improvement practices introduced by Toyota without realizing the same success that Toyota achieved. How can it be that so many firms…
Mark R. Hamel
Every once in awhile people will ask me to (discretely) evaluate a kaizen event team’s effectiveness. I don’t necessarily relish doing that when it is intended for the purpose of team comparisons, but it’s not an unfair request from senior leaders.
Someday, I should probably try to pull the…
Donald J. Wheeler
One-hundred-percent inspection is commonly used to avoid shipping nonconforming product. Each of the items produced is measured and judged to be either conforming or nonconforming. The conforming items get shipped, and the nonconforming items get set aside for use as factory-authorized replacement…
Jim Benson
There are two ways to slide easily through life: to believe everything or to doubt everything. Both ways save us from thinking. —Alfred Korzybski
Over the last several years, I’ve studied a lot of processes and watched communities grow around them. I’ve been a member of many of these communities.…
Mike Richman
Welcome to Quality Digest Daily 2.0! This new format represents a significant re-imaging of our flagship brand (the industry’s only daily newsletter), which we first launched nearly two years ago. I hope you notice that we’ve added more video content to the newsletter as well as greater editorial…
Minitab LLC
Ford Motor Co. is one of the largest automakers in the United States, producing millions of automobiles each year at 70 plants worldwide. According to J. D. Power and Associates Initial Quality Survey, Ford has received more top rankings than any other automaker since 2007. It’s no surprise that…
William A. Levinson
The first part of this article illustrated the kinds of problems that can happen when data from non-normal processes are plotted on traditional control charts, and when traditional process capability assessments are applied to these data. This second part will show what to do about these problems…
Davis Balestracci
My March 30, 2011 article ended with wisdom from Yogi Berra as a warning to the quality profession. Some prickly reactions to it got me thinking about the last 30 years or so of quality improvement.
ADVERTISEMENT
The 1980 NBC television show, “If Japan Can, Why Can’t We?” introduced the…
Bruce Hamilton
Gary was a talented, creative welder with an idea that made perfect sense to him but was not supported by conventional measures. Gary was determined to implement his idea and pressed for a closer evaluation by his supervisor when the idea was not immediately accepted. This was Gary’s idea:
A…
John Schultz
Problem solving is much more than arriving at an elegant solution. It is a twofold progression that includes problem resolution and solution implementation. Six Sigma and process improvement methods are examples of this sequenced approach to developing and deploying a remedial action that improves…
Taran March @ Quality Digest
Story update 4/13/2011: We corrected a misquote regarding who first said, “As goes GM, so goes the nation.”Every day, it seems, business as usual gets a bit more unusual. I’ve been haunting the news portals and blogs, curious to see how experts are viewing potential supply shortages following the…
Mark Graban
I was in Los Angeles on Tuesday, and I had a little extra time on my way to the Burbank airport, which meant a rare treat—lunch at the famed In-N-Out Burger. I don’t mean to be that guy who tweets what he eats, but my lunch is pictured at right.
The main picture I wanted to share is a simple…
Joseph A. DeFeo
How many times have you heard, “Lean is in and Six Sigma is out” from a colleague? The funny thing about this is that I used to hear the same thing 23 years ago. Only then it was, “Lean is in, and quality improvement teams are out.” Little has changed since then. Everyone is looking for a simple…
Mark R. Hamel
Understanding a process’ cycle time is extremely important, especially in the context of takt time. In a mixed-model environment, cycle time can be a bit less straightforward. That’s where weighted averages may make sense.
Weighted-average cycle time, also known as “average weighted cycle time…
Danita Johnson Hughes Ph.D.
Read this. It won’t be a waste of time.
Time gets lost. People kill time. Time flies. It gets wasted. Time weighs heavy on our hands. We spend time. Time passes. It drags on or it hurries by. Those behind bars are said to be doing time. Sometimes, we have no time left; we’re out of time.…
Donald J. Wheeler
Measurement error is generally considered to be a bad thing, and yet there is very little written about how measurement error affects the way we use our measurements.
This column will consider these effects for four different uses of data. But first we need to describe how to characterize…
Donald J. Wheeler
Measurement error is generally considered to be a bad thing, and yet there is very little written about how measurement error affects the way we use our measurements.
This column will consider these effects for four different uses of data. But first we need to describe how to characterize…
Davis Balestracci
There are four statements regarding control charts that are myths and in my experience, just refuse to die. The next time you're sitting in a seminar and someone tries to teach you how to transform data to make them normally distributed, or at any point during the seminar says, “Normal distribution…
Tom Pyzdek
Story update 3/29/2011: We corrected an error in the next to last sentence. "p < 0.05" was changed to "p > 0.05."
One of the exercises I assign to students in my training involves creating two histograms from normally distributed random numbers. The results often look similar to those shown…
Tom Pyzdek
Story update 3/29/2011: We corrected an error in the next to last sentence. "p < 0.05" was changed to "p > 0.05."
One of the exercises I assign to students in my training involves creating two histograms from normally distributed random numbers. The results often look similar to those shown…
Stewart Anderson
An excellent article by Donald Wheeler on the economic cost of quality, “What Is the Zone of Economic Production?” gave me pause to consider the strategic implications of reducing the costs associated with poor quality. As Wheeler pointed out in his article, there is an economic zone of production…
Stewart Anderson
An excellent article by Donald Wheeler on the economic cost of quality, “What Is the Zone of Economic Production?” gave me pause to consider the strategic implications of reducing the costs associated with poor quality. As Wheeler pointed out in his article, there is an economic zone of production…
Steve Moore
During the late 1990s, Marilyn vos Savant, holder of the Guinness Book of Records’ highest recorded IQ of 228, received an avalanche of hostile responses, many from Ph.D.s in math and statistics, when she correctly solved the controversial “Monty Hall Problem.” This concerns whether a contestant on…
Steve Moore
During the late 1990s, Marilyn vos Savant, holder of the Guinness Book of Records’ highest recorded IQ of 228, received an avalanche of hostile responses, many from Ph.D.s in math and statistics, when she correctly solved the controversial “Monty Hall Problem.” This concerns whether a contestant on…
Davis Balestracci
When teaching the I-chart, I’m barely done describing the technique (never mind teaching it) when, as if on cue, someone will ask, “When and how often should I recalculate my limits?” I’m at the point where this triggers an internal “fingernails on the blackboard” reaction. So, I smile and once…
William A. Levinson
Last May I wrote in “Airline Companies Are Driving Customers Away” that the U.S. Military Academy allows cadets only four responses to questions as to whether a specific duty or responsibility was carried out: “Yes, sir,” “No, sir,” “I don’t understand, sir,” and “No excuse, sir.” Col. Larry…
Joseph A. DeFeo
Designing for customer needs always leads to higher quality products and services, as well as innovative outcomes, because an effective design process uncovers hidden customer needs. Adapting the most effective models of continuous innovation can create the habit of innovation. Continuous…
Angelo Lyall
The business world seems fascinated with the story of how Toyota “invented” lean manufacturing. In actuality, Toyota did not aim to create this heavily marketed tool kit that we call lean manufacturing; the company simply did things “The Toyota Way” as they put it. Unleashing the innovative…
Miriam Boudreaux
There’s no more vicious cycle than problems that constantly reoccur because there’s no time to stop and solve them correctly. Although we all would like this cycle to stop, managers can’t afford to let employees waste time with too much researching, and employees don’t always have the time…
Steven Ouellette
“Come and listen to a story ‘bout a man named Ned / a poor Texas Sharpshooter barely kept his family fed. Then one day he was shootin’ at his barn / and he came up with a plan to spin a silly yarn. ‘Specifications,’ he said, ‘making of… the easy way.’ ” What do a Texas sharpshooter and…
Mark R. Hamel
A recent George F. Will column referenced the sign re-created to the right. Although I don’t necessarily believe that the signage encompasses the complete definition of discipline, it certainly provides food for thought.
A lot of folks think of discipline, especially in the context…
Kimber Evans
Kaizen. Across many industries in many countries, this term is thrown around as a “standard practice.” Continuous improvement—the ultimate goal of business everywhere, right? Find ways to get things done quicker, cheaper, more efficiently… and then implement those goals into an everyday routine.…
Jon Miller
There is an expression in Japanese, “Dust accumulates to form a mountain.” (Chiri mo tsumoreba yama to naru.) While this may not be geologically correct, it carries a deep truth that lean practitioners will recognize through experience. Taken positively, this is the essential spirit of kaizen…
I have long admired and respected Toyota. I have been to its factories, published and written books and articles about its revolutionary production system, known many of its brilliant people, and taught its methods to thousands of students. Like many of Toyota's admirers, I was shocked and saddened…
Steven Ouellette
With the announcement of another Toyota recall, it seems that everyone and their dog have an opinion about Toyota, and some of them might even be drawing the right conclusions. While everyone is allowed to have opinions (not the dogs—on quality matters I don't trust entities that consider cat poo a…
PQ Systems
In the world of continuous improvement, it might seem that one does not want to look back. After all, as systems improve, old data is no longer useful, and keeping it around—like keeping old love letters—may someday get you into trouble.
Knowing when to recalculate control limits is important, as…
Pierre Huot
If a manufacturer were to ask its clients how they evaluated goods or services, the three most common metrics would be goods at a fair price, on-time delivery, and quality. Ask which could be most valuable and in all likelihood the most significant response would be quality. When included in the…
Bill Hathaway
While eating my lunch at the park last fall, I looked down at the wooden deck below me, and noticed that an ant had picked up a large crumb from my sandwich. The crumb was heavy, and the ant labored to move it. Unfortunately, the gap between the deck planks was too wide for the ant to cross…
Donald J. Wheeler
Last month’s column looked at how to fix some of the Problems with Gauge R&R Studies. This month I will show you how to learn more from your gauge repeatability and reproducibility (R&R) data with less effort. Rather than getting lost in a series of computations, the "evaluating the…
Mark R. Hamel
My teenage education was (maybe) enhanced by substantial doses of Monty Python. Occasionally, I discover a lean metaphor somewhere within their body of work. One of my absolute favorite scenes is from the movie, Monty Python and the Holy Grail. The three-minute scene goes by two names: “The…
I was a 30-year-old quality project manager on a continuous metal processing line. We coated metal for a broad range of consumer and industrial products. Just like many metal-processing facilities, particularly back then, we used a bunch of processes involving chemistry of varying evilness for a…
Christopher Sirola
Many years ago, I was flipping through stations on the radio and came across a talk show. I don’t remember the topic of discussion, but something the host said stuck with me.
“Scientists,” the host blustered (and I paraphrase), “are 95-percent confident of these results! Wow!”
The sound you’re now…
William A. Levinson
Six Sigma has been credited with six- or even seven-figure returns in single projects, but it has not kept the manufacturing jobs of its principal exponents—Motorola, General Electric, and Maytag—in the United States. Henry Ford, on the other hand, proved that lean manufacturing can make almost any…
Barbara A. Cleary
A young man in PQ Systems' hometown survived a dramatic auto accident last summer in which police-captured video footage of his spectacular, airborne vehicle was broadcast throughout the nation. That was just the beginning of his problems, for during his hospitalization, his medical records were…
Steven Ouellette
After my last column citing some really bizarre flaws in how our brains perceive reality, I thought I might cover some flaws in logic that are applicable in the world of quality. So, basically, even if our brains are working correctly, we can still send our Black Belts off on false trails trying…
The emergence of cargo cults on some Pacific Islands after World War II is an amusing and oft-repeated story.
The relatively simple lifestyles of these islanders were interrupted by Japanese aircraft dropping large supplies of clothing, medicine, canned food, and tents to support the Japanese…
Bill Waddell
I got one of those mass e-mails the other day, the ones with inspirational stories promising good luck and eternal salvation, provided you forward it to 10 people immediately. I chose to delete it and take my chances with the Almighty, betting that He was not really a party to an agreement linking…
Bruce Hamilton
A colleague, friend, and lean leader in health care related a story awhile back that I think is worth sharing. Joanne Marqusee, COO at Hallmark Healthcare System, was standing in line at a grocery store checkout. While she waited, Joanne recalls, she noticed that the cashier had added an unusual…
Minitab LLC
(Minitab: State College, PA) -- Swiss-based Metalor Technologies, a global leader in precious metals and advanced materials, is a supplier to electronics companies and manufacturers of medical and electrical equipment.
Metalor’s skill in creating reliable technology has earned the company a…
Donald J. Wheeler
Measurement error is ubiquitous. As a result, over the past 250 years, different areas of science and engineering have come up with many different ways to deal with the problem. One approach to the problem of measurement error was developed during the 1960s within General Motors. Throughout the…
Bruce Hamilton
A couple years ago, I was consulting in a large rolling mill to help reduce late deliveries to its customers. After walking the floor for the first time with an enthusiastic 20-something engineer (let’s call him Mark), I asked for help with observation at a particular point in the factory where…
A new year always brings new hope, new plans, and new perspectives. While looking ahead is the most direct route to progress, looking back is essential to understanding the present. After all, the past creates the consequences that will shape the future.
With this in mind, the editors of…
Akhilesh Gulati
A friend recently returned from a visit to China; his company had been acquired by a Chinese organization and he had gone there as part of the mutual due diligence. Not only did he come back impressed by their lower manufacturing costs but also with their technological advancements. While we in…
Donald J. Wheeler
In my July column, “Where Do Manufacturing Specifications Come From?” we found that the intraclass correlation coefficient is the natural measure of relative utility. This measure is theoretically sound and easy to explain. This column will look at how to use the intraclass correlation to…
Minitab LLC
ResMed is a global manufacturer of medical devices. The company’s products help people with sleep-disordered breathing (SDB) and other respiratory disorders. Characterized by the interruption of normal breathing patterns during sleep, an estimated 18 million people in the United States suffer from…
Barbara A. Cleary
Signs in factories or on the back of long-range trucking rigs sometimes proclaim “X days since our last accident” or “No on-the-job injuries since 1964.” Extending the stretch between such accidents may be motivated by this announcement alone, but there are better ways to diminish or prevent…
Davis Balestracci
You know what the third-quarter review meeting means: a packet will be handed out with bar graphs and, no doubt, trend lines on each of about a zillion “key performance indicators” that show:
• This month vs. last month vs. 12 months ago (maybe year-to-date as well)
• The three months’…
Minitab LLC
B
efore Michael Mercer established his consulting company, he accumulated more than 30 years of quality improvement experience at 3M. That experience led him to develop a deep trust in the power of Minitab Statistical Software. He began using one of the earliest mainframe computer versions to…
Steven Ouellette
I know we have been talking about statistics a lot in my last few articles, but recent reader comments have prompted me to think more about why doing statistics properly matters. Come with me, dear reader, on a journey to find out why you should embrace, and not run screaming from, your inner…
Minitab LLC
Gold'n Plump Poultry provides chicken products to stores, delicatessens, and restaurants in 40 states. Commitment to process excellence has helped the company thrive even in tough times, and Minitab Statistical Software has provided the powerful tools they needed to analyze quality data. But the…
Mike Richman
A recent article appearing in the Quality Digest Daily e-newsletter (“Why Lean? Why Now?” by Dean Bliss http://www.qualitydigest.com/inside/health-care-news/why-lean-why-now.html) discusses the value of lean in a health care setting. In his editorial, Bliss writes about the manufacturing origins…
Donald J. Wheeler
Last year I discussed the problems of transforming data prior to analysis (see my August 2009 column, “Do You Have Leptokurtophobia?,” my September 2009 column, “Transforming the Data Can Be Fatal to Your Analysis,” and my October 2009 column,“Avoiding Statistical Jabberwocky.”) There I…
Jon Miller
People can make plenty of mistakes when launching a lean enterprise transformation. Interestingly, many of these mistakes are similar if not identical to those made by entrepreneurs when starting a business. Perhaps these mistakes are generic enough to be widely applicable and not specific to lean…
Taran March @ Quality Digest
Sometimes it’s interesting to watch trends develop from the relatively safe perch of business media. A press release from Aveta Business Institute last week drew my attention because it wasn’t doing what 99.9 percent of all press releases do: selling something. Instead of announcing a new product,…
Aly Fields
As my quest for knowledge and understanding of the real world continues, I decided to meet with an old professor of mine. I can remember almost every professor I ever had boasting about mentoring former students, so I figured my professor would be delighted to help me out. I am smart, hardworking…
Steven Ouellette
Throughout the last couple of articles, I have explained and illustrated that understanding the random sampling distribution (RSD) of a statistic is key to understanding the entire basis of inferential statistics. Which is just a fancy way of saying “avoiding career-terminating decisions.” This…
Aly Fields
Editor’s note: Several weeks ago, a young woman by the name of Aly Fields contacted us wanting to learn more about “quality” in general and Six Sigma in particular. A recent college graduate, Aly had taken it upon herself to earn a Six Sigma Yellow Belt. Why? Read her own words below. What…
Mark R. Hamel
I recently experienced the pain associated with coaching a team with poor chemistry. It happened within a kaizen event team, so the pain was finite, being that a kaizen event is a rapid improvement of a limited process area. It was, however, an opportunity to learn a few team-formulation lessons,…
Donald J. Wheeler
In my August column, “How to Turn Capability Indexes Into Dollars,” and my September column, “The Gaps Between Performance and Potential,” I showed how to convert capability indexes into the effective cost of production and use (ECP&U), and how to use these costs to quantify the payback for…
Tripp Babbitt
Systems thinking requires a massive change in the way organizations design and manage work. Old thinking must be flushed out so that new and better thinking can replace it. The outdated functional design of organizations according to the type of work performed needs an overhaul. Frederick Taylor,…
Davis Balestracci
I attended a talk in 2006 given by a world leader in quality that contained a bar graph summary ranking 21 U.S. counties from best to worst (see figure 1). The counties were ranked from 1 to 21 for 10 different indicators, and these ranks were summed to get a total score for each county (e.g.,…
Mark Graban
Lean thinkers see the waste in health care when they are at the hospital gemba. I think this is true whether you are a lean person who is new to health care or if you’re a long-time hospital person who has learned lean. Experts (doctors) ranging from John Toussaint to Patricia Gabow to Don Berwick…
Jon Miller
I am in Japan helping to lead one of our lean manufacturing benchmarking trips. What I took away from the debriefing from yesterday’s lean benchmarking visit was a series of lessons on how to sustain a lean culture after 10 years. The company we visited had made a few defining choices, played its…
CEED
Students of CEED—an Australia-based program that links university engineering students with industry and government companies to complete specific on-site projects as part of their studies—are contributing significantly to the success of manufacturing projects, including those focused on making…
Davis Balestracci
During my recent travels, I have noticed an increasing tendency toward formalizing organizational quality improvement (QI) efforts into a separate silo. Even more disturbing is an increasing (and excruciating) formality. Expressions such as “saving dark-green dollars” are creeping into…
Jon Miller
Leaders lead. Or do they? There is not always a cause-and-effect relationship between leadership actions and follower behavior. Not all leaders succeed at pulling people along in the same direction. If a leader needs to drive people in a direction, keeping the fringes from straying too far from…
Steven Ouellette
Last month I wrote about how the random sampling distribution (RSD) of various sample statistics are the basis for pretty much everything in statistics. If you understand RSDs, you understand a lot about why we do what we do in hypothesis testing, inferential statistics, and estimation of…
Donald J. Wheeler
In my August column, “How to Turn Capability Indexes Into Dollars,” I defined the effective cost of production and use and showed how it can be obtained directly from the capability and performance indexes. In this column, I will show how these indexes can be used to estimate the benefits to be…
Jon Miller
Whether I am speaking about lean to an audience of one or 100, if the conversation goes on long enough the question inevitably arises: “What’s next for lean?” I always manage an answer, typically tying it to the theme of the discussion, speech, or intended teaching but never quite giving the same…
Mike Micklewright
“To effect the economies, to bring in the power, to cut out the waste, and thus to fully realize the wage motive, we must have big business – which does not, however, necessarily mean centralized business. We are decentralizing.”
--Henry Ford “Today and Tomorrow”, 1926
Is your…
Gwendolyn Galsworth
As every company knows, workplace information—production schedules, customer requirements, engineering specifications, operational methods, tooling and fixtures, material procurement, work-in-process, and the thousand other details on which the daily life of the enterprise depends—can change…
Barbara A. Cleary
A spate of cartoons and commentary throughout the summer has lampooned BP, Halliburton, Transocean, and Cameron International for their apparent inability to plan timely control measures that might have constrained the destruction after the blowout on the Deepwater Horizon oil rig in the Gulf of…
Alberto B. Ayulo
Every journey has a beginning, and mine began during a U.S. Air Force commander’s first week on the job. He called a staff meeting and told everyone that things had to change for the organization to succeed, and “lean” was the solution. Everyone in the room looked dazed and confused, wondering…
John David Kendrick
Complexity can be thought of as the level of difficulty in solving mathematically presented problems. Six Sigma practitioners and operations research professionals are often asked to predict the complexity of a hardware or software product by predicting (in man-hours or full-time equivalents) the…
Gwendolyn Galsworth
Editor's note: In this second in a series of articles on workplace visuality, Gwendolyn Galsworth, Ph.D., author of Work That Makes Sense (Visual Lean Enterprise Press, 2010) and Visual Workplace/Visual Thinking (Visual-Lean Enterprise Press, 2005), and recognized visual expert, shows us how…
Steve Martin
I like the plan-do-check-act (PDCA) cycle for three reasons: It’s simple, it provides a pathway for teaching, and it works.
I love teaching. For me, seeing the light bulb over a lean student’s head illuminate for the first time is highly rewarding. During the early years of my lean journey,…
Mark Graban
I have as many bad customer-service experiences as the next guy, with health care and other businesses. As I’ve said before, unless there’s a broader lesson involved, I try not to be a “hack” blogger who just uses his platform to complain about the last bad thing to happen. However, I think the…
Mark R. Hamel
My dog, Bailey, has a sensei—a dog-obedience trainer. Actually, my wife and I have a sensei to teach us how to train our dog. In fact, my wife and I have used the same dog-obedience trainer for the last three dogs, all German shepherds. No one would mistake us for Mr. and Mrs. Dog Whisperer.…
Stewart Anderson
The recession has been an extremely disruptive event for many organizations. Many bear relentless pressure to identify new market needs, create appropriate products and services, become more effective and efficient, and develop and modify systems and processes to meet and deliver those goals. In…
Tripp Babbitt
While reading an issue of Quality Digest Daily, I came across an article by Kenneth Levine and Peter Sherman titled, “Ten Simple Principles for Treating Employees as Assets.” I thought it followed the usual themes about engaging employees and driving out fear until I ran across the following jewel…
Steve Moore
An article titled “Sharp Drop in Firefighter Fatalities in 2009” appeared in a safety trade journal recently. For the first time in three years, it said, on-the-job firefighter fatalities dropped below 100. The article went on to say that the 82 firefighter deaths in 2009 were substantially below…
Steven Ouellette
Story update 10/05/2010: Corrections were made to captions for Figures 6, 7, 8, 9.
As I was teaching class the other day, I told the students I was going to reveal to them the one secret they needed to learn to understand every statistical test they would ever use. The secret was the one thing…
Donald J. Wheeler
Capability indexes allow us to characterize the relationship between the process potential and the specifications. Performance indexes characterize the past performance relative to the specifications. Yet, in practice, we seek to make sense of these index numbers by converting them into other…
Mike Micklewright
In part one of this series I described what dyslexia is and how I linked “dyslexia” with “lean.” In part two, I suggested an approach to training in the work place called “universal design for learning” (UDL), which takes into account those who learn differently from others. In this part, I will …
Chet Marchwinski
One of my favorite value-stream walks is with the senior managers of several organizations who share and jointly manage a value-creating process that stretches all the way from raw materials to the end customer. I’ve been taking walks of this sort for more than 20 years and I usually see the same…
Angelo Lyall
When so many managers and businesses have access to virtually the same tools and information, it seems peculiar that two similar businesses can operate so differently, one being a success story while the other fails. To induce needed changes rather than superficial ones, managers must first accept…
Tom Pyzdek
In this four-part series, we take an in-depth look at how to design an effective work environment. Part one discusses the elements of continuous-flow work cells. Part two considers how to enhance the efficiency of such work cells. Part three explores the 5S methodology. In this, the last part of…
Donald J. Wheeler
Evidently Steven Ouellette did not like my June column, “Is the Part in Spec?” The adjectives he used were “complicated,” “unhelpful,” “backward,” “confusing,” “unnecessary,” “crazy,” and “disastrous.” (Ouellette’s response, “Know the Process Before Altering Its Specifications,” can be read here…
Tom Pyzdek
In this four-part series, we take an in-depth look at how to design an effective work environment. Part one discusses the elements of continuous-flow work cells. Part two considers how to enhance the efficiency of such work cells. Part three explores the 5S methodology. In part four of the series…
ANDREA LAHOUZE
John Berger is no stranger to the benefits of training within industry (TWI). In 1995, when Berger was working for global manufacturing giant Emerson, he was challenged to move an entire product line of electro-mechanical sensors from Minnesota to Singapore.
At Emerson’s Minnesota plant,…
Tom Pyzdek
In this four-part series, we take an in-depth look at how to design an effective work environment. Part one discusses the elements of continuous-flow work cells. Part two considers how to enhance the efficiency of such work cells. Part three explores the 5S methodology. In part four of the series…
Tom Pyzdek
In this four-part series, we take an in-depth look at how to design an effective work environment. Part one discusses the elements of continuous-flow work cells. Part two considers how to enhance the efficiency of such work cells. Part three explores the 5S methodology. In part four of the series…
Willie L. Carter
Higher customer expectations, cost-cutting pressures, thinner margins, and shorter lead times are some of the daily challenges that organizations face. A management system built around lean processes enables companies to achieve operational excellence, while providing flexibility in the way…
Jon Miller
When we say that a task is Herculean, it means it is extremely difficult. Heracles was a Greek hero (Hercules in the Roman version) who got into some trouble for killing a member of his family in a fit of madness and was assigned a series of challenging tasks as penance. Sometimes we face…
Value stream or other lean analysis helps identify the main obstacles to flow in a process. Improvement projects using lean tools in a transactional environment (i.e., office) are often confronted with the following problem: Lean teams lack a methodology to consistently problem-solve how to…
Steven Ouellette
So I thought I was done with measurement system analysis after my last column, but I just finished reading Don Wheeler’s June 1 column, “Is the Part in Spec?” and the first thing I thought was, “Well, that was… complicated and ultimately unhelpful in answering the article’s title question.” I like…
Bruce Ballinger
A recent article published in Quality Digest Daily pointed out that to foster a problem-solving culture, managers must serve as mentors and cultural leaders—building the systems and atmosphere that support and encourage team members at all levels to problem solve effectively.
That is…
Dirk Dusharme @ Quality Digest
For more than 20 years, Toyota’s methods, known as “lean,” have made headlines. And that’s how long engineer, researcher, and author Mike Rother has been involved with the subject. Like many others, Rother began with Toyota’s production tools. And like many others, he found that these are…
Jon Miller
In a recent e-mail, a reader of my blog asked me, “How can we enhance top management commitment and involvement for implementing total productive maintenance (TPM)?”
This is a great general question to ask during any effort to establish excellence, maintain excellence, or transform excellence…
National Association for Healthcare Quality
The Toyota Production System and U.S. health care improvement share a long history. What lessons can health care leaders learn from Toyota’s recent production troubles? A few experts recently discussed this on WIHI, an audio program sponsored by the Institute for Healthcare Improvement (IHI). Here…
Donald J. Wheeler
During the past 20 years it has become fashionable to condemn measurement processes that are less than perfect. Yet the reality is that we must always use imperfect data. Given this fact of life, how can we ever know if a measured item is or is not within the specifications? Put another way, how…
Stewart Anderson
I am often struck by a remark of W. Edwards Deming that the aim of a system must include plans for the future. As Deming wrote in The New Economics, “A system must have an aim. Without an aim, there is no system. The aim of the system must be clear to everyone in the system. The aim must include…
(Academy Leadership Publishing: King of Prussia, PA) -- When news headlines trumpet story after story about fiscal mismanagement, unchecked greed, massive bankruptcies, and rampant downsizing, it’s hard to believe there’s any good news about the business world. Indeed, it’s almost impossible not…
R. Eric Reidenbach Ph.D.
Successful quality initiatives are based on understanding the true nature of “quality.” It resides in the minds of those who judge it and use it to make their purchase decisions—in other words, the market. Divorced from the market, quality or value has no real meaning. Uninformed definitions of…
Davis Balestracci
Customer satisfaction data resulting in various quality indexes abound. The airline industry is particularly watched. The April 10 Quality Digest Daily had an article with the title "Study: Airline Performance Improves" and the subtitle "Better on-time performance, baggage handling, and customer…
Pete Abilla
Some time ago, while consulting for a huge call center, I took a group of customer service agents for a little gemba walk and a quick activity to demonstrate a few lean fundamentals. What was scheduled for a 60-minute exercise turned out to be an experience that awakened the agents, several of whom…
Steven Ouellette
We have recently covered a lot of ground on the topic of measurement system analysis (MSA). We talked about the basics of MSA, the potential study, the short-term study, and the long-term study. At this point you should have a pretty firm foundation in the importance and methods of good MSA…
Donald J. Wheeler
Having an effective model for the nature of data will inevitably identify two different paths to process improvement. One path seeks to operate a process up to its full potential while the other path seeks to operate to meet requirements. This article explains how these two paths differ and how…
Donald J. Wheeler
Having an effective model for the nature of data will inevitably identify two different paths to process improvement. One path seeks to operate a process up to its full potential while the other path seeks to operate to meet requirements. This article explains how these two paths differ and how…
Jon Miller
After every major natural disaster that disrupts global supply chains, there are voices that cry out “A-ha! I told you just-in-time inventory doesn’t work!” Recently the Icelandic volcano turned European skies airplane-free for a few days and news programs reported shortages of critical raw…
R. Eric Reidenbach Ph.D.
I just read an article that appeared on Quality Digest Daily, “The Quality Crisis in America,” by David C. Crosby. The gist of the article is that the nation is in the midst of a quality crisis that has been with us for a very long time. The problem, according to Crosby, “is that the ‘big boss’—…
Jeff Liker
The most stunning accomplishment of Toyota during the last 50 years is its turnaround from making “junk” to virtually redefining quality in the auto industry. Toyota was influenced to the core by W. Edwards Deming and quality is evident everywhere in the company. The objective of the Toyota…
Mark Kiemele Ph.D.
I
t is no secret that lean Six Sigma (LSS) and design for Six Sigma (DFSS) have arguably been the most effective initiatives for improving bottom line results and revenue growth since the advent of Frederick Taylor and management science. Billions of dollars in bottom-line impact have been…
Chet Marchwinski
I’ve now been continuously thinking about lean for 30 years, since the fall of 1979 when my bosses at the Massachusetts Institute of Technology (MIT) asked me to explore how a few Japanese companies had developed a striking advantage in designing and making motor vehicles. Recently, I’ve found…
Jon Miller
These days, there must be people at Toyota waking up in a cold sweat from dreams in which they are being scolded by Taiichi Ohno, furious at the massive vehicle recalls caused ostensibly by the pursuit of scale and volume production at the expense of quality. At least I sincerely hope this is the…
Donald J. Wheeler
Courses in statistics generally emphasize the problem of inference. In my December column, “The Four Questions of Data Analysis,” I defined this problem in the following manner:
Given a single unknown universe, and a sample drawn from that universe, how can we describe the properties of that…
Anantha Kollengode
T
he check sheet is a simple and effective tool useful in lean Six Sigma projects. It is sometimes referred to as a concentration diagram or location plot. It is a handy tool for qualitative and quantitative data gathering and analysis. Check sheets help to systematically collect and organize…
Rip Stauffer
It’s better to measure things when we can; that’s been well-established in the quality literature over the years. The use of go/no-go gauges will always provide much less information for improvement than measuring the pieces themselves. However, we don’t always have the luxury of using continuous…
Arizona MEP
Vantage Mobility International (VMI) is well on its way to achieving its goal: to become the No. 1 provider of personal mobility transportation solutions by the end of 2010.
“We’re transforming our business from soup to nuts,” says Doug Eaton, president and CEO of VMI. “Our company is growing…
Steven Ouellette
A
hh, measurement system analysis—the basis for all our jobs because, as Lord Kelvin said, “… When you cannot measure it, when you cannot express it in numbers, your knowledge is of a meager and unsatisfactory kind.” How interesting it is then, that we who thrive on data so frequently don't…
Lean Six Sigma methodologies have been around since Henry Ford’s creation of the assembly line in the early 1900s. Yet, companies that turn to lean Six Sigma often find themselves defending against the stigma that it stifles creativity, turns people into robots, or is just another way to get more…
Greg Hutchins
Toyota is in the news daily for its safety-related recalls. It’s sad… no, tragic. How could a company’s quality reputation be diluted so quickly? The pundits are saying that it will take many years to regain its lost quality reputation.
For Toyota, its reputation was its most important asset—…
Jon Miller
I received pair of questions about lean logistics over the past few weeks that prompted this article. The questions were “What is the milk run method?” and “What is the role of the water spider?”
The milk run
The milk run is an example of time-fixed, quantity-variable replenishment of…
Eric Clower
In July of 2008, I stepped out of an engineering leadership role and into an operational role. The transition was exciting and overwhelming. While I had been in and around manufacturing for a little more than a decade, I had never operated as a part of supply chain or production management. The…
Tim McMahon
A management system is the framework of processes and procedures used to ensure that an organization can fulfill all tasks required to achieve its objectives. A lean management system consists of the discipline, daily practices, and tools that you need to establish and maintain a persistent,…
Steve Moore
The following words of an anonymous poet as he (or she) immortalized the lessons from Deming’s funnel experiment.
“Tamper, tamper is the game, try to make all the same. Squeak and tweak it every day, off we go to the Milky Way.”
—Anonymous
I offer a corollary that may help…
R. Eric Reidenbach Ph.D.
“Our corporate mission is to deliver the ‘Best Value in Energy and Related Services,’” according to a large Midwestern electric and gas utility company. This is a mission statement, which after a minor modification (just change the industry), could be posted on any boardroom wall and inserted into…
Georgia Institute of Technology
The cross-functional team at Piedmont Newnan was made up of employees that deal with the process daily. For this process improvement project, they focused on case carts, which are used for pulling together all supplies needed for surgical procedures.
Pam Murphy, a…
H. James Harrington
With the onset of Six Sigma methodology, many organizations have spent large sums of money to make all of their products and processes as close to six sigma as they can. I agree that the higher the level of sigma value, the better the quality of the output is if it’s not screened. But is that the…
Donald J. Wheeler
In the 1940s the War Production Board trained approximately 50,000 individuals in how to use process behavior charts (also known as control charts). At that time the computations were done by hand, and the emphasis was on making things as easy as possible for those doing these computations. As a…
James Wells
How many times has this happened to you? You’re leading a Six Sigma project on a transactional process of some kind, something not directly tied to manufacturing or measurement of product quality. You get to the measure phase of your Six Sigma project and struggle to figure out how to satisfy the…
Knowledge at Wharton
Toyota’s legendary lean processes didn’t come out of nowhere. They were forged by the fire of urgency in post-World War II Japan when resources were scarce. Toyota innovated—and continued to innovate. Today, the Toyota Production System is the most respected manufacturing and inventory control…
R. Eric Reidenbach Ph.D.
One of my clients, a wireless business-to-business (B2B) telecom company, was experiencing a significant problem in their call center. They were absolutely inundated with calls—most of them problems. They were spending a significant amount of money trying to manage the call center—adding new call…
Knowledge at Wharton
In 2008, the University of North Carolina (UNC) Health Care System faced a challenge: Length of stay per patient at this major nonprofit health system and academic medical center was longer than it needed to be. If administrators could figure out how to cut the length of stay by an average of just…
Steven Ouellette
In the past couple of articles, we have been having fun together testing whether a measurement device is usable for the crazy purpose of determining if we are actually making product in or out of specification. Last month, we performed a measurement systems analysis (MSA) “potential study” using a…
Barbara A. Cleary
What is known as “point mentality” is a knee-jerk response to what appears to be a problem. We may learn this when we take our child’s temperature and find that it’s high; we are inclined to do something right away—give ibuprofen, orange juice, and bed rest—rather than waiting to see if this is a…
Jon Miller
Editor's note: At the time this interview was published by Gemba Research LLC, Toyota hadn't announced a fix to the sticky accelerator issue that caused the company to recall approximately 2.3 million select vehicles. On Feb. 1, the company announced that its engineers have developed a solution…
Donald J. Wheeler
In my column of Jan. 7, “The Right and Wrong Ways of Computing Limits,” I looked at the problems in computing limits for average charts. This column will consider the right and wrong ways of computing limits for charts for individual values. As before, a data set will be given that you can use to…
Tom Pyzdek
While we work to improve quality and efficiency, our leaders manage our organizations into oblivion. Literally. Something is terribly wrong. Leaders of major corporations in virtually all industries do things that cause them to, either accidentally or deliberately, destroy billions of dollars in…
Steve Moore
The purpose of this article is to give you an appreciation of the Quincunx as an educational tool for teaching some of the theory behind the tools and concepts of so-called modern quality management. The Quincunx is often seen in the possession of organizations practicing in-house education of…
The Un-Comfort Zone With Robert Wilson
In the early 1970s I was a young teenager who was completely caught up in the Zeitgeist. I admired the long-haired rebels and radicals who were engaged in protesting the establishment and developing the counter-culture. I didn’t really know what any of that meant, but to me it was all about…
Steven Ouellette
If you can’t trust your measurement system, you can’t do anything with the data it generates. Last month, in “ Letting You In On a Little Secret,” we talked about the purpose of measurement system analysis (MSA) and I gave you a neat spreadsheet that will do MSA for you, as well as some data (…
H. James Harrington
In the first column of this three-part series, I reviewed an interview that was conducted in 1988 with F. James McDonald, president of General Motors. In this interview he explained what GM was doing to improve quality and customer satisfaction. Typical activities that GM was involved in during…
Donald J. Wheeler
Today virtually everyone uses software to create process behavior charts, yet the available software is notoriously unreliable in terms of the way the limits are computed. This column will explain and illustrate the difference between the correct and some of the incorrect ways of computing three-…
H. James Harrington
The world is changing so fast today that it is almost impossible to keep up with the latest trends in your own profession. If you are not spending at least two hours per day updating yourself in your chosen profession, you probably are behind the current state of the art. It has been estimated that…
Mike Micklewright
Can you imagine producing products with a tremendous amount of variation? I’m sure many of you know this all too well. I mean, here you’re trying to produce the same products, trying to ensure consistency, and many of the products you produce have different shades of color, many function…
Steven Wachs
The purpose of using control charts is to regularly monitor a process so that significant process changes may be detected. These process changes may be a shift in the process average (X-bar) or a change in the amount of variation in the process. The variation observed when the process is operating…
Knowledge at Wharton
The financial services sector has been a laggard in adopting lean tools and practices, perhaps because of their manufacturing origins. But those attitudes are slowly changing. As more banks discover the benefits of lean operations—such as lower costs, fewer errors, faster cycle times and far…
Gain sharing and lean Six Sigma are highly complementary systems that are mutually reinforcing. While both efforts are excellent by themselves in improving productivity, quality, and a variety of other measures, they are much more powerful together. Both systems are based on the principles of…
Aditya Bhalla
The Six Sigma journey of many organizations has morphed into “lean Six Sigma” during the past couple of years.
While the fusion of two methodologies has yielded benefits, it has also spawned a number of urban legends on the context and relevance of combining the two methodologies.
What…
Tim Leary
Story update 11/23/2010: A paragraph was added to the end of this case study to reflect the current state of the company's quality initiatives.
Acme Technology Services (not their real name) is a privately-held provider of technology-enabled business solutions. Acme’s retail software division…
Jay Arthur—The KnowWare Man
After a meal at a local Chinese restaurant, my fortune cookie said, “If you keep too busy learning the tricks of the trade, you may never learn the trade.” When I think about how this applies to Six Sigma, it seems obvious that far too much Six Sigma training is dedicated to the tricks of the…
Davis Balestracci
The economy has become a convenient excuse on which to pin the blame for everything—especially job losses. Well, in the case of quality positions, yes… and no.
A sobering thought: Will the Pareto principle (the 80/20 rule) inevitably apply to the quality profession? I think so. It’s time to “…
Jon Miller
For a group of people who claim to practice management by fact, questioning the as-given condition, we in the lean community have a troubling habit of citing and accepting made-up lean enterprise statistics. In fact, I would say that at least 50 percent of statistics cited about lean have been…
WILLIAM SCHERKENBACH
I’ve spent most of the past two years living in China where I have learned much on how enterprise is managed over there. Many people have said that this century belongs to Asia. That may be, but they have a lot to learn and change before that happens. They cannot depend on cheap rote labor to…
Donald J. Wheeler
The four questions of data analysis are the questions of description, probability, inference, and homogeneity. Any data analyst needs to know how to organize and use these four questions to be able to obtain meaningful and correct results.
The description question
Given a collection of…
Knowledge at Wharton
“Lean” has come to mean an integrated, end-to-end process viewpoint that combines the concepts of waste elimination, just-in-time inventory management, built-in quality, and worker involvement supported by a cultural focus on problem solving. Can such practical principles be applied to innovation…
Steven Ouellette
You know how sometimes you think everyone knows a secret that they haven’t let you in on? Well, I had the opposite happen to me the other day. I assumed everyone knew the purpose for measurement system analysis (MSA), a.k.a. gauge repeatability and reproducibility; but I found out that a number of…
Minitab LLC
Kaj Ahlmann (right), owner of the Six Sigma Ranch, Vineyards, and Winery, and vineyard manager, David Weiss, create great wines by applying old-world techniques and the rigor of proven quality improvement.
Some people take it easy when they retire. But Kaj…
Malcolm Chisholm
I have just finished rereading Walter A. Shewhart's 1939 book Statistical Method from the Viewpoint of Quality Control (Dover Publications, 1986). Mine is the 1986 edition, which has a foreword by W. Edwards Deming. Shewhart, a Bell Labs man, pioneered quality control and was a major inspiration…
Scott Alamanach
Sometimes when studying something that has become too familiar to us, we can gain valuable new insights by looking at it from a radically different perspective. Much has been written, for example, about how important customer service is for business—so much, in fact, that it becomes easy to lose…
Stewart Anderson
Last week I had occasion to view once again, in the company of a client, the excellent little video, “Toast Kaizen,” produced by the Greater Boston Manufacturing Partnership (GBMP)1, and narrated by Bruce Hamilton. In that video, Hamilton takes a simple everyday process, that of making toast, and…
John David Kendrick
A common error of many Six Sigma and operations research professionals is not properly selecting the correct subgroup sampling technique when constructing a statistical process control (SPC) chart. Incorrect subgroup sampling technique selection has become worse in the modern computing age,…
Mike Richman
Here at Quality Digest, we get a lot of mail: Some of it’s critical, some of it’s praiseworthy, some of it’s cantankerous, and some of it’s challenging. All of it is insightful. And then, every once in awhile, something comes along that simply... well...
The following was sent to us from a…
Tripp Babbitt
I have identified myself as a “reformed” lean Six Sigma Master Black Belt. Some will see this as an affront to lean and Six Sigma. I want to assure you that there are many things to like about lean and Six Sigma. The issue at hand is that a better solution is available that can help organizations…
Forrest Breyfogle—New Paradigms
Lean, lean Six Sigma, total quality management (TQM), and other techniques have helped companies improve processes through the execution of projects. However, much of these efforts have resulted in siloed process improvements that don't benefit the enterprise as a whole.
To illustrate this…
Jon Miller
I was flipping through some Japanese books on sayings and speeches given by Taiichi Ohno looking for inspiration for a new article when I found the following passage:
“Within the Toyota Production System, a lack of ability to do kaizen becomes a critical flaw. Does this mean that if you do…
Tom Gaskell
If you are buying two or three complex assemblies per month from a contract manufacturer, it would be reasonable to check every one carefully; there’s a lot that could go wrong. However, if you are buying 100,000 simple subassemblies per month it makes no sense for you to 100-percent check them…
Jon Miller
I became aware of a truth about lean problem solving and kaizen yesterday while reading an article about 10 internet rules and laws, “Internet rules and laws: the top 10, from Godwin to Poe,” published on the Daily Telegraph’s web site (www.telegraph.co.uk).
4. Skitt’s Law…
Donald J. Wheeler
I
n the past there was only one criterion required to be a good supplier: you had to ship very few nonconforming items. If your proportion of nonconforming items took a turn for the worse then you would be “in trouble,” and you would stay in trouble until your fraction nonconforming dropped…
Forrest Breyfogle—New Paradigms
S
ix Sigma and lean provide tools for process improvement. Most of today’s business improvement programs can trace their roots back to a lean or a Six Sigma heritage. In general, these process improvement methodologies are considered advances from total quality management (TQM) and other methods…
Forrest Breyfogle—New Paradigms
The financials of an enterprise are a result of the integration and interaction of its processes, not of individual procedures in isolation. Using a whole-system perspective, one realizes that the output of a system is a function of its weakest link or constraint. If you're not careful, you can be…
Jay Arthur—The KnowWare Man
At the 2009 National Association for Healthcare Quality conference, I gave a speech on lean Six Sigma simplified. At the end of the session, one of the attendees asked, "If Six Sigma is so easy, why isn’t everyone doing it?" My answer: Because we’ve made it too complicated, expensive, and hard…
Stewart Anderson
Story update 10/22/2009: We added a reference to Toyota Kata in the first paragraph.
The tools and techniques of what is commonly called “lean manufacturing” have their origin in the Toyota Production System (TPS). While the lean movement deserves much credit for popularizing these tools and…
Steven Ouellette
I'm not saying that the following apply to you... really. But, you might be a Black Belt if...
You test your co-workers for normality – and find some of them to be non-normal and a little skewed…
…and you know you can handle non-normal co-workers if you can just transform them
You recall…
In 2005, according to a BBC News report at the time, operating rooms all over the United Kingdom were thrown into chaos and operations canceled due to broken, missing, or dirty surgical instruments. The Royal College of Surgeons called for a national audit of decontamination units, following a…
Bill Kalmar
Regular readers of my column know that I abhor surveys that don’t provide some type of incentive or discount on a future purchase for completing the survey. I realize that I may have discussed this subject ad nauseam, but have you noticed that every store, restaurant, gas station, doctor’s office…
Jay Arthur—The KnowWare Man
I
n his inauguration speech, President Obama called for improving health care quality and reducing costs. In 2008, U.S. health care costs exceeded $2.4 trillion and are expected to climb to $3.1 trillion by 2012, according to the National Coalition on Health Care.
Of these costs, 25 percent…
A
n emergency response organization differs substantially from our usual public health organization for day-to-day business. However, as the spring 2009 H1N1 (also referred to as swine flu) outbreak highlighted, usual public health processes are fundamental for effectively responding to a…
Donald J. Wheeler
This is the final column in the debate between Donald Wheeler and Forrest Breyfogle on whether or not to transform data prior to analysis. Because the debate started with Wheeler's article "Do You Have Leptokurtophobia?" we are letting him have the last word on the topic.
The articles following…
Raissa Carey
To Chris Collins, lean and Six Sigma, just like government and business management, go hand in hand.
In Erie County, where he fiercely advocates that a lean government can and will save taxpayers millions of dollars, Chris Collins became the first county executive in the nation to implement lean…
While I have been saying this for decades, and while K’ung Fu-tzu implied it millennia ago when he called for a balance of knowledge and action, it takes a while to sink in. W. Edwards Deming showed how simply taking a pencil with paper and plotting the data makes action possible. Experts in data…
Forrest Breyfogle—New Paradigms
A previous article of mine in this newsletter, “NOT Transforming the Data Can Be Fatal to Your Analysis,” addressed the need for appropriate transformations and a predictive performance measurement system.
The statistical business performance charting (SBPC) methodology that was described in…
James O. Pearson
We have all had to plan a trip to the airport. Sometimes it goes well and sometimes not so well. One of the problems we have is dealing with the variation in the trip time to the airport. Since I travel to the airport a lot and like analyzing data, I keep track of my travel time to the airport.…
Steven Ouellette
If you have been following my articles over the last few months, you have seen that even though statistical process control (SPC) charts are very powerful tools for examining a process, it turns out that there are a lot of ways to mess up SPC. This month, I am going to finish up with a few more…
John Stiller
Story update 9/23/09: Reference to 9.5.2.f was changed to 8.5.2.f in second paragraph.
As more suppliers are required by their regulators and customers to achieve ISO 9001 certification, and because certification symbolizes a point of competitive differentiation in a tight economy, emphasis on…
Stewart Anderson
Is the theory of constraints compatible with lean thinking and can the two approaches be used together? This article looks at some of the similarities and differences between the two approaches and suggests how they might be coupled to advantage.
The book, Lean Lexicon: A Graphical Glossary for…
Forrest Breyfogle—New Paradigms
Not surprisingly, there was controversy over Forrest Breyfogle's article, "Non-normal Data: To Transform or Not to Transform," written in response to Donald Wheeler’s article "Do You Have Leptokurtophobia?" Wheeler continued the debate with "Transforming the Data Can Be Fatal to Your Analysis."…
The Un-Comfort Zone With Robert Wilson
“Writing is not a job; it’s a hobby!” thundered my father when I told him my plans for college. “You need to get a profession: Medicine, law, engineering, or accounting.”
I cheerlessly acquiesced and enrolled in a pre-med program, but at the end of my first year, after struggling through…
Donald J. Wheeler
Following my article on Leptokurtophobics (Do You Have Leptokurtophobia?) it was almost inevitable that we should hear from one. We were fortunate to have someone as articulate as Forrest Breyfogle III to write the response. However, rather than offering a critique of the points raised in my…
Lonnie Wilson
Five things to lean my company? In two days? That's pretty quick. Why so quickly?
I can think of two reasons. First, people expect things to be done better and faster each day; and it appears we’re getting decent at doing just that. Lean has made huge strides toward contributing to that “…
Bill Kalmar
The band “Chicago” sang those words about "time" decades ago. The second line “Does anybody really care?” seems to sum up what is still in vogue today, especially in the workplace. Just as with vacations where workers are reluctant to leave for fear that someone will discover that their job is…
Michelle Paret, Eston Martz
Story update 8/27/2009: An error was spotted and corrected by author in paragraph starting with "The population mean for a six-sided die..."
Mark Twain famously quipped that there were three ways to avoid telling the truth: lies, damned lies, and statistics. The joke works because statistics…
Minitab LLC
Story update 8/27/2009: An error was spotted and corrected by author in paragraph starting with "The population mean for a six-sided die..."
Mark Twain famously quipped that there were three ways to avoid telling the truth: lies, damned lies, and statistics. The joke works because statistics…
Forrest Breyfogle—New Paradigms
Story update 8/24/2009: The original graphics for this story were missing key data due to errors in converting them. We have fixed the problem.
I
n “Do You Have Leptokurtophobia?” Don Wheeler stated, “‘But the software suggests transforming the data!’ Such advice is simply another piece of…
Steven Ouellette
Over the past couple of articles, we have explored how an incomplete understanding of how SPC limits are calculated can lead to constructing control charts that look strange. But using some of the things I mentioned, hopefully you can see that these “strange” control charts actually reveal quite…
David Boghossian
As the founder of PowerSteering and a practitioner in strategic management and continuous improvement for more than 25 years, I have seen my share of management fads come and go, and even been in the room when some of them were created.
There were quality circles and total quality management…
Li Zongming
Design of experiments (DOE) is a crucial tool in Six Sigma quality management and its application is widespread in Japan; nevertheless, many manufacturing companies in other countries have not formally adopted it because of its complex concepts and costs. As a matter of fact, the essence of the…
Raissa Carey
I
f you’ve been to Starbucks lately, you probably noticed the fast-paced employees working their java magic as they take orders from customers in line, not at the register, so that baristas can start the order, and sometimes finish it, before the customer even pays for it.
Yes, I’m all for…
Donald J. Wheeler
The symptoms of leptokurtophobia are (1) routinely asking if your data are normally distributed and (2) transforming your data to make them appear to be less leptokurtic and more “mound shaped.” If you have exhibited either of these symptoms then you need to read this article.
The origins of…
H. James Harrington
World War III has begun. This time it’s not a war of battleships, bullets and bombs—this is an economic war. The weapons are televisions, steel, cars, and clothes. This is a war where we have no allies. Every nation is out to capture more of its share of the U.S. and world’s market. We are being…
R. Eric Reidenbach Ph.D.
Pick up any article or book, attend any conference on Six Sigma, or talk with any Black Belt or Master Black Belt and you will hear the Six Sigma gospel about the importance of the voice of the customer. For example, in their book Six Sigma: The Breakthrough Management Strategy Revolutionizing the…
Tom Pyzdek
Today I received a sales call from a person interested in becoming a certified Six Sigma Black Belt. He had what I call a "can't do" personality. This is the diametric opposite of the "can do" person. This type of individual looks for reasons why a particular thing can't be done. How about a…
Tracy Willis
Do you hear Six Sigma professionals express frustration that the organization does not support their efforts?
Are there department heads in your life who have complained that their Six Sigma professionals are not delivering the needed results? And that each project is too time-consuming?…
Tom Pyzdek
In a recent post on the Evolving Excellence blog, Bill Waddell tackles one of my pet peeves: activity-based costing, or ABC. Few things do more harm to lean Six Sigma than this method of accounting. In fact, it is my opinion that the accounting systems used by U.S. businesses are responsible for a…
Stewart Anderson
Just the other week, I had the privilege of visiting with three or four companies that were doing lean process improvement. In every visit, each company invited me into their “war room” where they took great pride in showing me their process and value-stream maps and the other trappings of their…
Steven Ouellette
Have you ever met people who “do” statistical process control (SPC) only to get some screwy-looking control chart, and then text: OMG I H8 SPC! (If you don’t understand that, ask your nine-year-old child or grandchild.)
Last month we saw how it is not a failure of SPC, but rather an EBKAC (…
Barry Johnson
When someone mentions design for Six Sigma (DFSS), the initial thought usually turns to developing new, innovative products. While DFSS has its roots in product development, individual components of the toolset can be applied in a variety of ways.
Recently, the use of DFSS has exploded in…
Peter J. Sherman
It is widely known among quality and process improvement practitioners that the lack of a clearly defined scope or charter is perhaps the leading cause for projects not getting started or completed on time and within budget. What are other causes? From my experience, the No. 2 cause for restarting…
Davis Balestracci
Click here to read part 1 of this series.
Analytic statistical methods are in very strong contrast with what is normally taught in most statistics textbooks, which describe the problem as one of “accepting” or “rejecting” hypotheses. In the real world of quality improvement, we must look for…
James Odom
In “The Power of Observation—Part 1,” we learned that a good portion of problem solving should be devoted to a thorough understanding of what’s going on before any corrective action steps are taken.
In many cases, too much time is spent on proposing various solutions before the problem has been…
Donald J. Wheeler
Some authors recommend that you have to wait until you have the range chart “in control” before you can compute the limits for the average chart or the X chart. Why this is not true will be the subject of this column.
To illustrate the issues we will once again use the NB10 data. The 100 values are…
H. James Harrington
I often get assignments at organizations where I am required to take aside a group of people, either within the building facility or off campus, to focus on issues or problems. Typically these groups spend a considerable amount of time to summarize and present a well-defined problem. The next step…
Niagara Transformer is a supplier of transformers that meet the most demanding applications. It has a tradition of supplying transformers for unique applications with unusual specifications and requirements. As an industry leader, Niagara Transformer has successfully completed several quality…
Davis Balestracci
This is an expanded version of an article that Balestracci wrote for Quality Digest in December 2007.
--Editor
I discovered a wonderful unpublished paper by David and Sarah Kerridge several years ago (Click here to get a pdf). Its influence on my thinking has been nothing short of profound. As…
David C. Crosby
The most important element in producing a quality product or service is the attitude of the people doing the work—not only the worker—but the attitude of all levels of management. Employee attitude about the product, about the work, about the boss, and about the company will pretty well determine…
Minitab LLC
A $1 billion annual budget may sound ample, but a few years ago, the costs of services ranging from law enforcement to cleaning county buildings had squeezed the government of Erie County, New York, to its limit. Residents faced a painful choice: raise taxes or slash services. But Chris Collins,…
The emergence of green technology and increased environmental awareness has prompted a paradigm shift in the way companies think about the design of their products. Because robust designs mean creating products to meet customer and societal needs, it is important that all enterprises rethink these…
Steven Ouellette
One of the most useful diagnostic tools for understanding what is going on in a process is the statistical process control chart (SPC). This is also a frequently misunderstood tool, and these misunderstandings lead to misdirected effort during a Six Sigma process, resulting in lost time and money…
Dale Hershfield
Twitter is the latest new thing. Want to follow John McCain or Al Gore throughout their day? Easy. Just sign up to receive their tweets. While their tweets may provide insights, or just entertainment (Ashton Kutcher and 50 Cent also tweet), does Twitter have value for business management?
The…
Craig Cochran
When I first got into quality, I really hated verifying the effectiveness of actions taken to correct a problem. After all, I was young and inexperienced. All of the people whose actions I was verifying were older, wiser, and more experienced than I was. Who was I to say that their actions were…
Barbara A. Cleary
Specific techniques for data collection, fundamental to accurate analysis, are sometimes overlooked in the need to see outcomes or trends in data. The lowly check sheet represents a critical tool in effective data collection if it is used correctly.
Because check sheets are such simple tools,…
Steve Daum
With several generations of statistical process control (SPC) technology under our belts, it may be time to rethink how we apply SPC in the 21st century. Basic techniques have been practiced since the 1930s. Some companies will soon be able to say, “we’ve been practicing SPC for 100 years.”…
James Odom
Charles Kettering, the famous inventor, once said: “A problem well stated is a problem half solved.” This implies that a good portion of problem solving should be devoted to a thorough understanding of what’s going on before any corrective action steps are taken.
In many cases, too much time is…
Scott Alamanach
Don’t miss the author’s follow-up to this article, “Going Low Profile in Afghanistan.”
--Editor
Profitable manufacturing requires efficiency, and this principle guides most (if not all) of our quality management systems (QMS). We’ve learned there’s little gain in correcting a production error…
Akhilesh Gulati
Recently a strategy consultant was overheard saying she writes romantic novels. Look into many organizations and, although said in jest, it has more than a modicum of truth to it.
Don’t get me wrong. The high-level strategic plans are important and necessary. But, the devil is in the details,…
Gretchen Hancock
These days blogs and newspapers seem to make a daily reference to climate change, resource scarcity and security, the environment and the economy. It's overwhelming … and with the legions of experts in each of these fields, hard to see where one organization, let alone an individual, can make a…
John Bruman
Editors note: The author submitted this just days before he lost his job. What is ironic about this "rant," as Bruman puts it, is that it was written seven years ago. Do we never learn?
Recent months have brought disturbing news about the U.S. economy, the stock market, and business leadership…
Chet Kagel
Command Medical Products of Ormond Beach, Florida, is a medical-device manufacturer that designs, manufactures, assembles, and packages disposable medical devices such as intravenous tubing, blood bags, IV bags, and catheters. Command Medical initiated its journey into lean manufacturing to…
Donald J. Wheeler
Last month we showed the X chart in figure 1. The four lowest values and the three highest values were seen to be “outliers” when we looked at the histogram. When we fitted a bell-shaped curve to the histogram, the outliers corrupted the model and resulted in a poor fit. Yet we used all the data…
Here’s a story that proves once again that exciting quality applications can occur anywhere in the world.
BHP Billiton operates the EKATI Diamond Mine in Canada’s Northwest Territories, approximately 200 miles northeast of Yellowknife—just below the Arctic Circle. Arctic winter gear designed…
Chet Marchwinski
The current recession is the fifth in my working career. And it is beginning to feel like the worst. I can't imagine that any manager or improvement team member in any industry in any country isn't feeling a bit queasy at this point, as the world economy keeps recessing toward an unknown bottom.…
Steven Ouellette
A colleague of mine made an interesting point about how we teach and learn experimental design techniques, and I thought I'd explore the subject further. He observed that the order that we teach statistics is almost exactly opposite of how one would actually use them. So this month I will describe…
Steven Ouellette
One of the most frequent questions I get from Black Belts and Green Belts I train is about the characteristics of a good Six Sigma project, particularly a first project. Define, measure, analyze, improve, control (DMAIC) is a procedure that is useful for certain types of projects and terrible for…
Akhilesh Gulati
Those best adapted to particular conditions will succeed in the long run. This idea was invented by Herbert Spencer in Principles of Biology (University Press of the Pacific, 2002) to describe Charles Darwin's theory of natural selection of living species.
By the early 1900s, this insight was…
Criteria changes and lean Six Sigma
In these difficult economic times, organizations are looking at all possible means to operate profitably. As demand for products and services drops and customers expect the lowest possible price, organizations are feeling urgent pressure to cut costs as a…
Steven Ouellette
Many people go through a point in their lives where they question the beliefs they hold most dear. Then there are those who question the entire basis for statistical process control (SPC) once they have learned the statistical basis for them. I can’t help you with the former, but I have something…
Steven Ouellette
As you read this you will, no doubt, have already made (and perhaps broken) your New Year’s resolutions. I’d like to propose one that we, as business leaders, have a special responsibility to follow and whose failure we hear about in the news almost every day.
Of course, I’m talking about…
Bipin Roy
During a recession, the concept of lean should make absolute sense to an information technology (IT) manager who wants to pursue every channel to increase efficiency and productivity.
We have seen a procession of quality standards adopted by software services organizations in the last two…
David C. Crosby
There are several issues about the Six Sigma approach to quality that bother me. First, Six Sigma is a performance standard that hardly anyone can understand. Secondly, it’s an engineering approach to quality management. It’s more of a defect-management program than it is defect-prevention.…
Barry Johnson
The cost of doing business is rising dramatically. Included in this is the cost to recruit and hire talent to join your team. It’s estimated that the total cost of one hire can exceed $30,000 when relocation and set-up expenses are included. That cost is minimal compared to the lost opportunity…
Steven Ouellette
What purpose, if any, does Six Sigma serve in economic downturns? Full disclosure: I teach and consult in Six Sigma and related areas, and you’re reading this article because you’re interested in Six Sigma, so we may not be the most objective people to assess this, but in this article, I will do…
Tej Mariyappa
Organizations embarking on the journey to process excellence have much to gain if appropriate actions are taken in the early stages of deployment. A key principle of Six Sigma is that defects identified and fixed upstream will result in significant leverage and benefits downstream. Similarly, the…
Peter J. Sherman
Today’s hyper-competitive business environment is creating a need for even more new products, new services, and new processes. Design for Six Sigma (DFSS) offers a generalized and effective approach for designing new products and services from the ground up. One of the more popular DFSS…
Steven Ouellette
By the time you read this, the amazingly long U.S. presidential election will be over. All U.S. citizens will be wandering around aimlessly bumping into objects, pressing their hands to the sides of their heads as the indignation poisons slowly leave their bodies, leaving them with a hangover-like…
Akhilesh Gulati
A physics exam question asked students to describe how they would use a barometer to measure the height of a skyscraper. One student who failed the test contested that his answer was correct. He was given a second chance to defend his position, verbally, to the professor. When the student didn’t…
Steven Ouellette
Every once in a while, people ask about acceptance sampling plans and I get all riled up. We all know (especially in this political season) that humans are addicted to their indignation high, so here’s your fix for today.
Back when defective products and services were considered inevitable, the…
Mike Micklewright
Question: What is the proper way of wearing a Black Belt once you’ve earned it?
Answer:
as in ….
I’m a changed man. I’m an American Society for Quality (ASQ)-certified Six Sigma Black Belt. To obtain the ASQ Black Belt, I had to pass a test and then show proof to someone within…
Akhilesh Gulati
"We have had a series of power outages even though we have central and local uninterrupted power supply (UPS) systems. This disruption causes a loss of service to our customers. While we don’t necessarily lose data, it’s an irritant, and also results in loss of productivity. Perhaps we could…
Steven Ouellette
In the Six Sigma world, we give a lot of lip service to the importance of the customer; we even have an official name for it—voice of the customer, or VOC. The problem is that many businesses don’t really have a good system for giving the customer what they ask for, much less one for listening to…
Lori Loethen
When organizations decide to deploy a Six Sigma initiative, there are several foundation stones required for a successful venture. One of those building blocks is leadership. From executive-level support to assigning champions and choosing the right projects, leadership is critical for Six Sigma…
Steven Ouellette
I read an article in Wired magazine the other day that got me to thinking about the relationship between statistics, engineering knowledge, and theory. The article claimed that with the era of massive data storage and analytical capabilities, the scientific concept of the “theory” was becoming…
Niraj Goyal
Abbreviations
t
Thickness of stack of product
T
Batch average of t sampled in the hour
Ta
Average if batch averages T…
I was working with a client to create their business’s critical performance measures the other day, and one of the managers said, “We should set the target higher than we want it—you know, aim high to hit low.” This set off one of my rants, and I thought I would share it with you.
When I worked as…
We examined the practices and major problems that can easily occur in the use of balanced scorecards in the June 3 issue of InsideSixSigma. Now let’s look at why attention to causal event analyses can improve the future performance of any process. Often, this traditional method fails to make metric…
Forrest Breyfogle—New Paradigms
We examined the practices and major problems that can easily occur in the use of balanced scorecards in the June 3 issue of InsideSixSigma. Now let’s look at why attention to causal event analyses can improve the future performance of any process. Often, this traditional method fails to make metric…
Steven Ouellette
I
was working with a client to create their business’s critical performance measures the other day, and one of the managers said, “We should set the target higher than we want it—you know, aim high to hit low.” This set off one of my rants, and I thought I would share it with you.
When I…
Over the years, scorecards have progressed through many changes, good and bad. Although scorecards often evolve into a meet-the-numbers game, regardless of the consequences to an enterprise as a whole, restructuring can produce dramatic improvements for any organization. This results in counter-…
Steven Ouellette
I thought this month we would get away from the stats of the last few columns. Hey, quiet down! How can anybody read over all that cheering?
There’s something missing from most Six Sigma implementations—a gap that, if left unattended, leads to wasted time and money, as well as the failure of the…
Thomas R. Cutler
Manufacturing firms intent on capturing and distilling rich streams of data will find them. Companies will often look at a capability maturity model (CMM) in rows and columns—a format common across many industries and many applications—in Excel. Most data dumped from a database end up in a grid,…
Thomas R. Cutler
Manufacturing firms intent on capturing and distilling rich streams of data will find them. Companies will often look at a capability maturity model (CMM) in rows and columns—a format common across many industries and many applications—in Excel. Most data dumped from a database end up in a grid,…
Steven Ouellette
If you have been following my articles for the last few months, you know that we’re almost done with an experimental analysis and that today we will be doing the final step—making our company money. If you haven’t been following my articles, then you should probably be flogged with a soggy…
Peter J. Sherman
Few process improvement topics generate more questions or may be least understood than design of experiments (DOE). This is regrettable as DOE is probably one of the most important activities—after the charter definition—that a manager/Black Belt will be performing during the Six Sigma process.This…
Alan P. Brache
Six Sigma promoters and innovation advocates have emerged as opposing camps in the battle for tool supremacy in the organization improvement wars. As Business Week said in “Six Sigma: So Yesterday?” and “At 3M, A Struggle Between Efficiency and Creativity,” which described how GE, Home…
Steven Ouellette
For the last couple of columns, we have been analyzing a simple experiment where we look for the best choice for a new gear material. We have used analysis of variance (ANOVA) to detect a difference in the mean wear for the four different materials. In the last column, we performed a post-hoc…
Anthony D. Burns
In Part 1 of this article I discussed Six Sigma failures and the fundamental flaws in the term Six Sigma, as seen in figure 1 below, which highlights the flaws in the hundreds of Six Sigma web sites displaying the nonsense of out-of-control processes that are the result of the claimed “unavoidable…
Steven Ouellette
Last month, I described a simple problem to determine which gear material resulted in longer wear. We reviewed the extremely powerful technique called Analysis of Variance (ANOVA) and found a statistically significant and important effect on the average wear due to gear material. I also…
Anthony D. Burns
Six Sigma captured the imagination of CEOs around the world. There have been many claims of its successes yet these have at least partially been attributed to the Hawthorne Effect, which implies that if enough money is thrown into any methodology, at least some short-term results can reasonably be…
Steven Ouellette
By the time you are reading this, you will have made your New Year’s resolutions, and I will have already broken mine. But I have an idea for a resolution that you might be interested in keeping, and one that could make your New Year happy and profitable. It is something that most Black Belts I…
Allen Huffman
With all the emphasis today on quality, and studies showing that quality is very important to the leaders of American business, why are so many organizations struggling to achieve and sustain quality systems? The answer is that managers have been inundated for 20 years with a parade of quality…
Forrest Breyfogle—New Paradigms
Editor’s note:This short story is part of a three-volume series—Integrated Enterprise Excellence: Going Beyond Lean Six Sigma and the Balanced Scorecard, by Forrest Breyfogle. Within the context of this fictional story the author discusses the attributes of an integrated training program that he…
Steven Ouellette
As I’m writing this, our first big snowfall of the year is piling up outside and it is –10°C (15°F). This brings to mind the many times my grandfather told me of how he walked to school in winter uphill (both ways) with no shoes. So I wondered, will I be able to spin the same yarn for my girls and…
Praveen Gupta
Imagine you decide to learn a new language and never make a mistake while learning it. No typos, no misspellings, no grammatical errors, everything turns out perfect. The first reaction is, “How can this happen?” Perfection isn’t believable. Similarly, if everything one tries doesn’t work, usually…
Steven Ouellette
Harvest time—vegetables fresh from the local farmer’s market going right into a homemade soup, eaten with fresh bread. Yum! This month, I’d like to talk about a recipe for a Greek alphabet soup, which you had better know about if you plan on doing an experiment. This may be the first recipe that…
Praveen Gupta
Between 1987 and 1992, the most successful implementation of Six Sigma didn’t require Black Belts or Green Belts. Instead, Six Sigma initiates received training in problem solving, team work, basic quality tools, and statistical tools. However, sense of urgency, dramatic improvement, and teamwork…
Steven Ouellette
I seem to be thinking about the measurement phase a lot recently. I suppose it’s because I’ve seen some teams working hard on problems that turned out to be nothing more than problems with measurement. Let me give you an example.Once upon a time, I was responsible for a product that was frequently…
Praveen Gupta
Six Sigma is being implemented at more and more corporations. After a significant investment in training, corporations initiate projects. Six Sigma Champions have told me that some companies have several thousand projects in the pipeline. Managing that many projects is a major task. How many…
Steven Ouellette
There is something that will get you into trouble if you don’t know about it, and which in my experience very few Black Belts or even Master Black Belts know about. It’s only in the mind of the person doing the research, and no software program will know about it. This mysterious property is “…
Steven Ouellette
There is something that will get you into trouble if you don’t know about it, and which in my experience very few Black Belts or even Master Black Belts know about. It’s only in the mind of the person doing the research, and no software program will know about it. This mysterious property is “…
V. Viswanathan
For quite some time a major question has been cropping up in my mind: Is Six Sigma’s application in software development as effective as it is in the manufacturing industry?The answer is “No.” The savings and benefits that occur in the software industry due to Six Sigma and other process-…
Praveen Gupta
As I teach Six Sigma in my classes, I try to create projects for myself, and often it’s the same project over and over. This time, my project was to use Six Sigma to reduce my extra weight.In 1986 one of my clients distributed a “heart for life” goodie bag on Christmas. In the bag was a measuring…
Steven Ouellette
I spent my June and July articles beating up on the “sigma” index commonly associated with Six Sigma (and continue to do so over in my discussion board.) Let me sum up by saying that, while not wrong, “sigma” isn’t an efficient metric for accomplishing what we are trying to do in today’s business…
Praveen Gupta
Six Sigma was Bill Smith’s vision for excellence in everything. Prior to Six Sigma, companies were implementing total quality management, statistical process control, pre-control, cost of poor quality, and other techniques with minimal effect. Quality became a promise of “motherhood and apple pie…
Steven Ouellette
Last month I talked about the “sigma” index and how it can be used. So what could be bad about the “sigma” index?Never forget that metrics drive behavior and that people are very, very good at finding a way to succeed when given a goal. It just may not be the thing you wanted them to do. If “sigma…
Praveen Gupta
I’m surprised how quickly we blame a methodology for a business’s lack of performance. We’re always looking for some silver bullet to cure all ills. In contrast, Six Sigma integrates many methodologies to achieve sustained profitable results. When Motorola practiced Six Sigma under the leadership…
Steven Ouellette
Now that we have talked about defining Six Sigma and 10 stupid Six Sigma tricks, I’ll move on to the measure phase and discuss some things that work and don’t work in measuring the effect of Six Sigma. The new metric that Six Sigma brought to us was the sigma index, so let’s start…
Steve Wise
The manager of a local grocery store is having dinner with his statistician friend. The store manager tells his friend about a certain cashier who is stealing from the company.
The manager is frustrated because he thinks he knows who the thief is, but can’t fire the miscreant because the employee…
Praveen Gupta
It’s easier to start a Six Sigma project than to close it successfully. Green Belts and Black Belts are expected to be working on projects constantly, so they work on projects to meet the existing expectations. Some of these projects are unlikely to yield significant improvement due to lack of…
Steven Ouellette
Repent of your wicked ways O fellow Six Sigma Heretics, or surely you shall be smitten (smoted? smited? smartied?) and turned into a pillar of out-of-spec material! The End (of the Top Ten Stupid Six Sigma Tricks countdown, anyway) is here! What could possibly be the No. 1 reason that Six…
There’s a certain manufacturer makes carbon-based friction material in the form of a disk. A press and die are used in the final manufacturing operation to cure the carbon material into a functioning friction pad. Peak temperature uniformity is a critical characteristic during the cure…
Praveen Gupta
I first read about training in listening skills about 25 years ago. I didn’t really understand the difference between hearing and listening. I thought people had hearing problems. Now I get it.Everybody talks I see people talking loudly on cellular phones at airports, in shopping malls…
There’s a certain manufacturer that makes carbon-based friction material in the form of a disk. A press and die are used in the final manufacturing operation to cure the carbon material into a functioning friction pad. Peak temperature uniformity is a critical characteristic during the…
Steven Ouellette
The end is near! Well, at least the end of the Top Ten Stupid Six Sigma Tricks (SSST) countdown. The Heretic soldiers on until his appointment with the stake. This month, we arrive at Stupid Six Sigma Trick #2: Neglecting Daily Management. In this SSST, companies get so starry-eyed over the fancy…
Some folks like to use control charts to analyze gauge study results. When using a control chart in this manner, one can assume that the chart should represent a series of gauge studies conducted over a period of time. In this example, let’s say that each morning a gauge is verified by…
Steve Wise
Some folks like to use control charts to analyze gauge study results. When using a control chart in this manner, one can assume that the chart should represent a series of gauge studies conducted over a period of time. In this example, let’s say that each morning a gauge is verified by recording…
Praveen Gupta
Most of us spend our time being busy. We expect a lot, compare our belongings with those of others and feel miserable about the miss-outs. We complain about the way life treats us. While thinking about my New Year’s resolution for 2007, I looked for an opportunity for self-improvement.I…
Steven Ouellette
I had a lot of feedback from interested readers in regards to Stupid Six Sigma Tricks #5, which I jokingly called “Pop Stars Without Clothing,” and which was about the frequent misuse of statistics in the Six Sigma world. Taking heart from this response to what might have been viewed as dusty old…
For the last Brain Teaser, in an interesting spin, sample size was defined as a time window. A is the correct response. The underlying data type falls into the category of defect counts (complaints) within a constant area of opportunity (one hour). These data, of course, follow the…
Praveen Gupta
Businesses have lately been focusing on profit and process improvement. However, profit improvement at any cost to make the upcoming quarter look bright has a price. It appears that most improvement effort leads with efficiency measured by head-count reduction. Improvement shouldn’t be measured by…
A certain company has a complaint department that answers calls for three unique products. Because of failure rates inherent to each product type, some products have a higher expected complaint rate than others. Calls are tallied each hour and categorized by product type…
Steven Ouellette
We are more than halfway through the countdown of our exploration of the kooky, and expensive, mistakes people make in implementing Six Sigma, and I want to talk about something that’s so fundamental people rarely see it—Stupid Six Sigma Trick #4: Overusing DMAIC.
DMAIC stands for define the…
Since “Sick Sigma” was published in April 2006, the public has become much more aware of Six Sigma’s failings. There is little risk today of being burnt at the stake for pointing out Six Sigma’s many faults. Last fall, even Dilbert discredited Six Sigma, pointing out that Six Sigma…
Praveen Gupta
A few years ago, lean thinking came to light. It sounded similar to what I had learned about the “pull” system. I wondered why we renamed cycle time reduction, or just in time (JIT), “lean.” Cycle time reduction was easy to understand and related to responsiveness to customer demands and waste…
An introduction to Six Sigma for direct marketing Six Sigma methods, used correctly and thoroughly for continuous improvement of direct marketing sales, can produce remarkable results:1. At a university work-force education program, total registrations doubled in three years through…
Steven Ouellette
Today marks a milestone in our countdown of the Top Ten Stupid Six Sigma Tricks. A subjective and unimportant milestone to be sure, but a milestone nonetheless—we have now reached the halfway point. Forget the New Year, this is cause for celebration.
To commemorate this trivial event, let us turn…
Praveen Gupta
Six Sigma was officially launched January 1, 1987, at Motorola, and it took more than nine months to make Six Sigma real. Twenty years later, Six Sigma has grown from a good baby methodology into a mature system that affects thousands of corporations and millions of people and that saves billions…
Steven Ouellette
In this installment of my arbitrary and capricious list of the Top Ten Stupid Six Sigma Tricks (SSST), let’s talk about an error that is perhaps less frequently made now than it has been, but is still common. I call this error SSST No.6, constraining your improvement activities to…
Praveen Gupta
Most quality management systems don’t produce the desired results because of the way companies use it to affect their bottom line.
A QMS is often considered to be a burden, and there’s apathy in all levels of the organization toward quality. ISO 9001 systems, for example, are considered to be paper…
Steven Ouellette
The Stupid Six Sigma Tricks countdown continues this month with an increasingly common error: “Inadequate Infrastructure.” By infrastructure, I mean those systems and processes that need to be in place in order to support the objectives of Six Sigma. Regardless of how you define Six…
Praveen Gupta
Globalization has led to worldwide economic growth, shared resources and shared business functions. Some countries dominate manufacturing, others software or the service industry. The quality of manufacturing operations has been improving for decades, but the quality of service appears to be…
Thomas R. Cutler
In a repetitive manufacturing environment, Six Sigma’s quantification is much easier than in the engineer-to-order (ETO) manufacturing environment, where no two products are identical.
Six Sigma is a program that affects the entire company. What have been missing for ETO manufacturers are the…
Steven Ouellette
So far, we’ve discussed Stupid Six Sigma Tricks #10: Conflating systems, methods and tools and #9: Confusing breakthrough with continuous improvement. This month, I’ll spend some time on a more subtle, and no less costly mistake that, in its extreme form, we’ll call Stupid Six Sigma Trick #8:…
Praveen Gupta
Lean and Six Sigma have been implemented for many years and organizations have benefited from both methodologies. With Six Sigma, corporations have reaped benefits in the billions of dollars. With lean, organizations have reported up to 90-percent reductions in space utilization and cycle-times.…
In the last InsideSixSigma issue, we published a brain teaser by Steve Wise, who proposed a scenario and asked you to pick a chart that best described the situation in a manufacturing operation. Here, Wise gives the correct response and comments on the wrong ones. Correct response The…
Steven Ouellette
This month let’s examine another common mistake that some people (not my loyal, intelligent, heretical and, let’s face it, downright attractive readers) make when they use Six Sigma. I expect to seriously annoy some practitioners when I say that Six Sigma isn’t a method of continuous…
Steve Wise
In a certain operation, a part is subject to a high-temperature curing cycle. The ideal curing scan is illustrated in the chart below. The oven chamber begins at room temperature, ramps up to a conditioning temperature of about 80 degrees, dwells for four minutes, ramps up again to the curing…
Praveen Gupta
Editor’s note: This is an attempt to use DMAIC methodology to resolve conflicts, in concert with the approach presented in an article titled “Feds may unleash Six Sigma on terrorism” by Del Jones in USA Today, October 30, 2002. By no means does either the author or Quality Digest consider the…
Steven Ouellette
As I said in my premier Heretic column, “Dogma and Definition,” I’m interested in examining our assumptions and premises about Six Sigma so we can discard the dross and refine the potential benefits in implementing it.To that end, I have decided to co-opt an omnipresent element of pop…
Tony Coray
One of the latest trends in the ongoing evolution of Six Sigma is its rising popularity among college students and its appearance in universities’ curricula. These courses are exposing students to the power of data-driven quality improvement and, in many cases, giving them firsthand…
Praveen Gupta
Considering the leadership at Motorola and General Electric provided by stalwarts such as Bob Galvin and Jack Welch, respectively, I believe that two leaders with totally different styles can get similar results using the same tools. When I worked at Motorola in Bob Galvin’s time, there was a rule…
Quality Transformation With David Schwinn
Once upon a time, in a real, live U.S. corporation, top management decided that Six Sigma was a good idea. They trained up many Black Belts to lead projects to produce documented savings as defined by the existing accounting system. To encourage people to be successful, the Black Belts—…
Praveen Gupta
At a recent committee meeting of a professional association, the speaker talked about print media and the Internet. Print media are struggling because the Internet can more easily disseminate information. The Internet is changing the world, and print media are those most directly affected by this…
Steven Ouellette
I
n Dirk Dusharme’s First Word in the April 2006 issue of Quality Digest, he sneaks into the back of the “Church of the Six Sigma” and cannily reports the goings on. In this column, I will burst in through the doors dressed in motley and try to pry the scales off of your eyes, chanting, “DMAIC…
Praveen Gupta
Six Sigma has gained a reputation as a data-driven statistical methodology for process improvement. If the statistical methodology by itself were responsible for Six Sigma’s success, then there would be nothing new in Six Sigma. Methodologies based on data-driven statistics have been known for many…
All too often FMEA (Failure Modes and Effects Analysis), DFMEA (Design, Failure Modes, and Effects Analysis) or FMECA (Failure Mode, Effects, and Criticality Analysis) ends up costing a company hundreds or thousands of dollars to prepare and returns nothing by way of payback, increased…
Praveen Gupta
I talk to a lot of people and most of them are stressed at work and carrying it over to their homes. The question then becomes, “What drives performance—fear or fun?”If someone asks employees what it’s like to work at Google, the most likely answer is that it’s exciting to work in a fun,…
Anthony D. Burns
In 1633, opposition to the common viewpoint could mean death. This was the case with Galileo when he proposed that the Earth revolved around the sun. He was tried for heresy. Of course things are different today. People who question dogma are no longer burnt at the stake. Instead, they’re branded…
David C. Crosby
Zero defects is an idea that was discovered in the early 1960s. It was articulated by Phil Crosby and first implemented at the Martin company in Orlando, Florida. Zero defects enjoyed widespread popularity until the mid 1970s, and almost every major company and their suppliers had a zero-defects…
Praveen Gupta
I’ve been reading about the 1.5 sigma shift for some time. Several different interpretations have been published and people are losing sleep over this matter. Some have even driven a stake into the ground to fervidly defend their position. My intent in writing this column is to simplify…
Praveen Gupta
Many people believe that they can buy Six Sigma certification and get some marketing advantage. By documenting a few more procedures, they can achieve Six Sigma recognition. For some, Six Sigma is a fact-based methodology made of fancy statistical tools that solve all business problems.…
Gregory Roth II
I, for one, am tired of the quality flavor of the month. It isn’t quite that bad but it seems like it at times. Have you been through statistical quality control, TQM, total quality speed, re-engineering, zero defects, quality circles, SPC, Motorola Six Sigma, AlliedSignal Six Sigma, GE…
Praveen Gupta
Corporations have been implementing improvement programs as far back as I can remember, at least since my first job at Motorola in 1981. I’ve noticed that more and more organizations—whether it’s Motorola, Ford Motor Co., General Motors Corp., Delphi or smaller, privately-held companies—measure…
Steven Ouellette
“The great aim of education is not knowledge but action.” Herbert Spencer (1820 – 1903) What’s distance learning? Six Sigma Black Belt training has long been the realm of the elite. It used to be so expensive and required so much time that only companies with the cash and resources to…
Praveen Gupta
A major misunderstanding regarding Six Sigma is its fabricated definition, (e.g. “Six Sigma is a fact-based decision-making methodology…”). I’ve seen people willing to attack anyone utilizing common sense to make decisions without facts. One of the reasons for taking such a strong position…
Praveen Gupta
A major misunderstanding regarding Six Sigma is its fabricated definition, (e.g. “Six Sigma is a fact-based decision-making methodology…”). I’ve seen people willing to attack anyone utilizing common sense to make decisions without facts. One of the reasons for taking such a strong position…
Praveen Gupta
During the last couple of years, I’ve interacted with several United Auto Workers (UAW) associates. Irrespective of what the former Big Three do, they’re all trying to do a good job.I’ve had the chance to teach some classes to UAW members. It always amazes me how people make money in the auto…
The purpose of process data analysis is to answer the question, "May the observed data fluctuations reasonably be attributed to common-cause variation?" The principal use of the Shewhart control chart is to guide efforts for process improvement by assisting in the discovery of peculiarities in the…
Ken Levine
Engaging your workforce is a major obstacle in a lean Six Sigma implementation. Only a limited number of employees will initially participate in Six Sigma improvement projects. It can also take one to two years before all employees participate in a lean kaizen event. It’s best to encourage…
Praveen Gupta
Our minds continually perform root cause analysis, which is a way of answering our questions about our surroundings and quenching our curiosity. We establish cause-and-effect relationships between what we see and what we do, or what we get and what we do, or what we want to get and what we need to…
Praveen Gupta
Teamwork has always been considered a critical component of completing complex projects that require significant improvement. The process of teamwork has been well-documented, but teamwork is still often elusive. Why?
When teams succeed, it’s often for the following reasons:
Strong leadership
Well…
Daniel S. Munson
The Empire State Building in New York City, with its 103 stories, 73 elevators, 2,500,000 feet of electrical cable and 6,500 windows, was built in 405 days. The framework rose at a rate of four-and-a-half stories per week. That’s nearly a floor a day. Most impressive was that the project came in…
Praveen Gupta
Most Six Sigma initiatives are project-oriented. And although implementing Six Sigma methodology on a project can lead to some improvement, a company can’t achieve full benefit of implementing Six Sigma. To maximize Six Sigma benefits, a corporation must commit to the methodology in its entirety.…
Praveen Gupta
The price of Six Sigma consulting, training and certification has been coming down and, interestingly, so is the amount or the rate of improvement being reported. We no longer hear success stories like Motorola or GE in larger number commensurate with the growth of Six Sigma, as evidenced by the…
Marilyn Fischbach
Deployment is one of the most critical elements of a successful Six Sigma program. Top-down support, champion training, wide publicity and Six Sigma awareness training for all employees are common components. In addition, employees selected to be Black or Green Belts must be trained and projects…
Tom Pyzdek
Some years back I, along with Drs. Doug Montgomery, Bryan Dodson, John Ramberg and others in the quality community, became concerned that there was no standardized criteria for becoming a Six Sigma Black Belt—or any other Six Sigma belt for that matter. The leading quality organization at that time…
Thomas R. Cutler
Kanban, in its most simplifying role, is a visual signal (or cue) that something needs to be replenished. More specifically, lean manufacturers today use kanban to drive a process to make, move or buy the appropriate parts. Thus, kanban has become one of the fundamental building blocks of a pull (…
Praveen Gupta
Companies are facing challenges in sustaining the energy and resources to continually benefit from Six Sigma. Black Belts face challenges in continuing to work on projects as these are becoming increasingly difficult to identify. Experts are talking about the ”Death of Six Sigma.“ Company…
Praveen Gupta
I had to catch a 6:10 a.m. flight the other day. The day before, I’d returned from work, done the normal stuff, prepared for the flight and finally had gone to bed so I could get up early the next morning. I got up around 3:00 a.m., got ready and went to the airport. As expected, traffic on road…
“Jim, how do we know that your project made any improvement?” asked the Six Sigma champion. The Black Belt candidate looked confused. “Um, the sponsor said he was happy with the outcome,” he offered. The members of the certification board looked skeptically at one another: “But the only metrics…
Tom Pryor
My twin grandsons celebrated their first birthday on July 1, 2001. And while the majority of people reading this article don’t know Alex and Austen, there is another set of twins celebrating their fifteenth birthday this year whose names are familiar. Born in 1986, they are Six Sigma and Activity…
Failure mode and effect analysis, or FMEA, is an attempt to delineate all possible failures, their effects on the system, the likelihood of occurrence and the probability that the failure will go undetected. FMEA provides an excellent basis for classification of characteristics such as identifying…
Scott Paton’s "The Chinese are Coming! The Chinese are Coming!" (Quality Digest, February 2005) describes how China’s Chery Automobile Co. plans to undercut American automakers’ prices by up to 30 percent. The article professes that neither tariffs nor layoffs are the solution to the hemorrhage of…
Praveen Gupta
Companies often have numerous Six Sigma projects in the pipeline, and Six Sigma belts are busy working on projects. However, statistical thinking suggests that not all projects will be equally successful. In fact, the amount of improvement could vary significantly from one project to another. In an…
Praveen Gupta
The Six Sigma initiative starts with an executive’s idea of achieving excellence and superior results. Whether the initiation is based on hearsay or the strategic move, it starts with communication among the executives—or employees. Likewise, throughout the implementation of Six Sigma, constant…
As quality professionals, we frequently report such facts as proportions (percentages), process capability indices, averages and standard deviations as if we know what we’re talking about. But what’s our actual level of confidence? All of our observations and our understanding are based upon data…
”Cause and effect, Chain of events, All of this chaos makes perfect sense” —Joe Diffe Third Rock From the Sun In my recent article, "How to Lead with Six Sigma: What are you solving for?" I discussed the need for leaders to clearly identify just what they’re…
“When, therefore, a man absorbed in the effect which is seen has not yet learned to discern those which are not seen, he gives way to fatal habits, not only by inclination, but by calculation.”
—Frederic Bastiat”That Which is Seen, and That Which is Not Seen,” 1850
“In the South Seas there is a…
Praveen Gupta
If you’re considering opportunities for business improvement, dynamic growth and profitability, “plan,” “do,” “check” and “act” (PDCA) is a leading option. Walter A. Shewhart developed the PDCA cycle in the 1920s and W. Edwards Deming made it famous in the 1980s, even though he modified the PDCA…
Tom Pyzdek
The headlines screamed, “Local Hospital Leads the State in C-Sections!” The gist of the story was that this hospital had more cesarean section births than any other hospital in the state. Indeed, it had led the entire Southwestern region for five years running. It’s well-established that C-…
Praveen Gupta
In layman’s language, Six Sigma means great and fast improvement, which leads to virtual perfection. Another indicator of a successful application of the Six Sigma methodology is the degree of breakthrough. Sometimes, when customers demand zero defects at any cost, suppliers are forced to add an…
Mark Crossley
When we discuss or mention Six Sigma, we almost always hear about getting defect rates down to 3.4 ppm. Consider a light bulb. How would you like to have a defect rate of 3.4 ppm only to find out that the bulb lasted just 20 hours before it burned out? This isn’t good, even though the Cpk was 1.50…
Tim Burke
For years, customers and auditors have been preaching to suppliers the need for the FMEA (failure mode and effects analysis) to be a “living” document. There are probably several interpretations of what it means to have a living FMEA, but one thing is for sure—the FMEA must be updated whenever real…
William A. Levinson
“Then the Husaria broke into a wild g allop and the heavy mass of men and horses cascaded over the Turkish ranks, bowling over the first, slicing through the second… The Grand Vizir leapt onto a horse and made his own escape moments before the winged riders thundered up to the tent and the banner…
Praveen Gupta
After launching a corporatewide Six Sigma initiative, leadership must consider how to get Six Sigma institutionalized in the supply chain. After implementing Six Sigma at an organization, its managers must think about continuing the improvement rate through implementing Six Sigma in its supply…
Sarah Fister Gale
In a lean environment, training is the last part of the production process to be transformed by the new approach to efficiency. While smaller work groups are streamlining steps and multitasking to eliminate waste and improve output, individuals continue to be linked to single skills or production…
Praveen Gupta
Six Sigma was first practiced in product development and manufacturing environments to improve customer satisfaction. There, significant improvements were achieved and sizable savings realized. After successfully implementing Six Sigma in manufacturing, Motorola applied Six Sigma in support…
Praveen Gupta
In simple terms, Six Sigma means quick improvement in a short period of time. Incremental improvement will save a lot of time and money for a company. Breakthrough improvement, therefore, is synonymous with Six Sigma. Breaking rules through innovation is a way to achieve breakthrough improvement.…
Paul Mullenhour
Six Sigma is a powerful tool for effecting change within an organization. Since its development in the late 1980s, it’s helped companies dramatically improve business processes, increase customer satisfaction to new levels and save hundreds of millions of dollars. To say it has the ability to…
Praveen Gupta
Six Sigma is implemented to affect the bottom line. In a corporation, Six Sigma starts in operations then moves into design and finally supporting areas. Finance and accounting (F/A) functions are involved to monitor the financials, however, they aren’t involved in practicing Six Sigma. At Motorola…
The maintenance problem Too many times, in lean manufacturing and other lean environments, 10- to 40-year-old equipment is re-deployed, moved and organized into lean cells without adequate concern or attention to maintenance reliability. In a lean cell, unscheduled equipment downtime usually costs…
Praveen Gupta
Six Sigma has been well applied in manufacturing through improving processes that use the DMAIC methodology. Some larger corporations have integrated Six Sigma so well into the corporate culture that it can be considered the DNA of the company. However, even in such companies, the human resources…
Chuck Doyle
Many organizations need answers to some key questions about lean and quality management: Is there a difference between quality and value? Should we have two teams, one for continuous improvement and one for lean? What roles would each have? What are the differences? The source for this…
Jeffrey S. Goss
Six Sigma, the statistical approach focused on increasing profitability by improving efficiency, has been part of the engineering world since the 1980s. Now, new innovative online and on-campus programs at Arizona State University are shaking up the way people all over the globe are…
Mike Micklewright
I’m a huge proponent of both Six Sigma and lean manufacturing. I’ve been teaching the tools used in Six Sigma for more than 15 years, and I make a portion of my living from consulting and training in these areas.
However, Six Sigma and lean manufacturing are business improvement processes that…
Praveen Gupta
Launching a Six Sigma initiative starts with a lot of enthusiasm from the “champion” who’s found courage and conviction to persuade management to commit to it. With enough resources, interest, excitement and the help of some consultants, the Six Sigma initiative gets off the ground. After initial…
Derrell S. James
Six Sigma. Lean. What do these initiatives have to do with the supply chain? The short answer is everything. The origins of these approaches are based, in Six Sigma’s case, on continuous improvements in quality and variation control, and in lean’s case, on production velocity and…
Praveen Gupta
Six Sigma is an expensive initiative with a huge potential for return on investment. However, there are risks associated with it. False starts, lack of commitment or lack of planning may lead to unsatisfactory results. Considering the complexity of the Six Sigma process, one must minimize the risks…
Arthur G. Davis
Falling revenues and changing customer requirements have forced many companies to look for ways to reduce the workload on current staff while developing long-term solutions. When companies are forced to downsize, the increased workload on remaining employees frequently results in stress…
Using Six Sigma initiatives to focus on improving the performance of business and manufacturing processes isn’t a new concept. But a growing number of manufacturers seeking to stay competitive and improve profitability are, instead, turning to Six Sigma to provide stronger value to…
Dave Wojczynski
The first article in this series, "What the Doctor Didn’t Order But Should Have," established a case for business improvement in the outpatient health care sector. More important, it provided real-life examples of how a Six Sigma framework can help outpatient facilities overcome…
Greg Brue
From its inception, Six Sigma was considered revolutionary. The six original pioneers who implemented the methodology at Allied Signal--the only true Senior Master Black Belts--vowed that the system would unearth inefficiencies in business operations that lead to outrageous levels of…
Dave Wojczynski
The following article, the first of a two-part series, outlines the growing need for Six Sigma initiatives in the outpatient health care market. In part one, we’ll compare a series of health care-specific businesses with parallel enterprises from other industries in order to categorize…
(Publisher’s Note: This article, is reprinted with permission from THE INFORMED OUTLOOK, in which it first appeared in Nov. 2003.)
Following the ISO 9001:2000 transition, the future of quality management continues to align with that of business management. The challenge in both cases is for…
Ronald Ames
As a methodology, Six Sigma has been around since the 1980s. Yet it took a couple of U.S. industry giants, Allied Signal and GE, to draw the world’s attention to the benefits the program offers businesses. Even so, many companies fail to integrate Six Sigma into their corporate cultures due to a…
Kamal Hassan
Would you spend millions of dollars for a return of more than a billion? Sure you would, but that’s just a fantasy, right? It wasn’t just a pipedream for GE’s CEO Jack Welch, who expected to reap a hefty return for every dollar his company spent on Six Sigma. Needless to say, he did. In 1997, GE…
Rick Beaver
Would you spend millions of dollars for a return of more than a billion? Sure you would, but that’s just a fantasy, right? It wasn’t just a pipedream for GE’s CEO Jack Welch, who expected to reap a hefty return for every dollar his company spent on Six Sigma. Needless to say, he did. In 1997, GE…
Howard Cooper
To succeed in our increasingly competitive global economy, many companies have implemented lean manufacturing, a step beyond just-in-time production systems. Other companies claim they’re "lean" but hedge on the concept. They maintain work-in-progress inventories because they fear the consequences…
John Nycz
Jack Welch had a unique vision of an organization that made data-based decisions. At times his tactics for bringing this about were described as “violent,” “abrupt” and “painful,” but his methods worked. GE’s transformation is still a modern model of how to make quantum shifts in the way a huge…