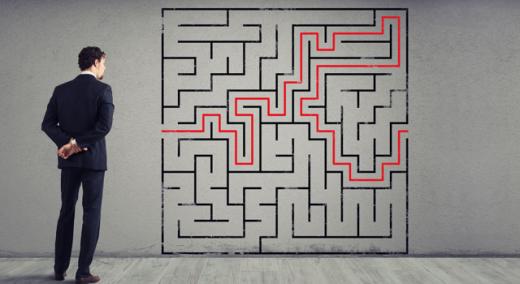
Someone recently asked me why quality failures and safety incidents continue to occur despite organizations communicating their quality and safety visions to the workforce, developing and implementing quality and safety management systems, and campaigning day in and day out about quality and safety.
ADVERTISEMENT |
This is an important question, and the broad answer is that even the best systems rely on people to design them and to carry them out. Let’s call them the scriptwriters or authors, and the actors who follow those scripts. Let’s take a look at what I think are five key issues.
…
Comments
Not Bad Actors
There is only one reason that quality and safety problems still happen...Because They Can.
Deming and Juran both attributed <15% of probems to the workers and >85% to the system.
Procedures should be written such that they are the best, fastest and cheapest shortcut to do the task.
Most workers want to do a good job and few will go out of their way to do it wrong.
When writing SOPs and developing processes we should remember the 3 rules of error proofing...
1 - Make it easier to do right than wrong.
2 - Make it obvious when it is wrong.
3 - Make it easy to correct if it's wrong.
A classic example is MS Word
1 - Auto-correct will fix most minor mispelled words as you type
2 - Unrecognized spellings and bad grammar are underlined
3 - Just backspace and retype to correct the error.
This should prevent all errors except those where the worker must rush and omit a step entirely. (Like not proof-reading your document before printing.)
But again, this is a system issue as well.
Quality & Safety Failures
I agree with the previous comment and would like to add one thing - if a process or task is "boring" to the point that workers are likely to become inattentive this is also a serious system failure. The process should either be automated or eliminated because it is clearly a threat to the system in its present form. One cannot simply mandate increased attentiveness to a process that by its very nature is repetetive, uninspiring, routine or all three together.
Add new comment