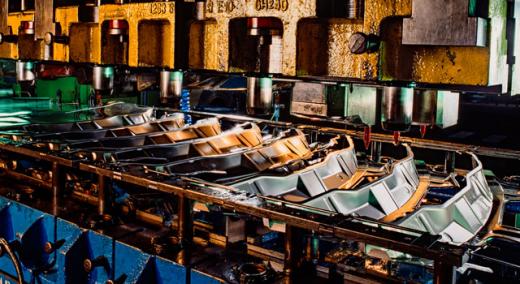
On Dec. 7, 2021, Ford Motor Co. updated its IATF 16949—“Customer specific requirements” (CSR), which require the use of reverse FMEAs (RFMEA) on new equipment (“tooling”). The first sentence of the reverse FMEA requirement reads: “Organizations are required to have a process in place that ensures all new launches complete an RFMEA event once the equipment is installed and running.”
ADVERTISEMENT |
As one might expect, multiple webinars are offered by RFMEA training providers, as well as two-day RFMEA classes ranging in price from $795 to $995. My guess is that it won’t be long before RFMEA software is available for purchase.
Having spent six years as a Ford plant and equipment design engineer, and an additional 32 years afterward helping companies manage new tooling risk, I see significant problems with the RFMEA processes being proposed by RFMEA training providers. Ford’s objective in requiring companies to use the RFMEA is to ensure that their suppliers effectively manage tooling risk.
…
Comments
RFMEA
From my point of view is another tool that Is required but will not create added value because of already known handling of PFMEA or DFMEA in solitude without active participation of teams.Should be the best practice to train people on the shop floor and give them the opportunity to touch the process with their own hands during the brainstorming otherwise this will remain only a nice package to show in audit place but without substance within.Seen all the recalls we can't say if there wasn't FMEA study realy performed or if there is a questioni of lack of knowledge and applying.Usually this tool is handled by one person and often other perché people even know what Is contained inside and what does RPN means.
Don't Lose Faith in FMEAs
Massimo,
Don't lose faith in properly implemented FMEAs. When I first used the Process FMEA as Plant Manager in 1987 for Ford we reduced our reject and rework by 40% after only nine months of implementation for an average weekly cost savings of $144,000. You are correct in your assessment that the majority of DFMEAs and PFMEAs are not done by the correct people. We constructed our PFMEAs by involving both the hourly and salary people who we believed the experts in the maintenance and operation of the equipment for the process step we were trying to improve. I had the advantage of having over 700 people to pick from. We then circulated the first drafts of the PFMEA to other workers on the line. Most did not comment on them but everyone was offered the opportunity to contribute. It took a while (nine months for 300 different process steps) to implement our PFMEAs and the Process Control plans they drove, but it was well worth it as evidenced by the money we saved. The good news is that with the current software tools we now use, it would have taken about 600-700 total hours to create the PFMEAs and Control plans.
The fact that you talk about RPNs tells me you may also be using a dated FMEA methodology. I have not used RPN to determine what to work on in a FMEA since 1987 when I was first taught to do so as a member of Ford managment and quickly realized it does not work. It was not until 2008 that the 4th Edition AIAG FMEA manual stated not to use RPN. Unfortunately, RPN has been replaced by AP in latest AIAG/VDA and SAE J1739 FMEA manuals. It is very easy to show that AP is just RPN with slightly different clothes. It is equally flawed and does not work.
The purpose of the "Ten Things You Need to Know About Reverse FMEAs" article is to show people they do not need a "Reverse FMEA" process if you already have an effective new tooling QMS process because you are already doing everything the RFMEA experts are telling you a Reverse FMEA process includes. Based on the RFMEA webinars I have reviewed, the biggest problem is that the RFMEA experts don't understand the existing risk managaement tools and how to use them to effectively to manage tooling risk. I remember my first year as a Plant and Equipment Design Engineer with Ford. I asked the senior design engineer why we waited until the equipment was installed on our floor to make it do what we wanted it to do. We were constantly modifying new equipment after installation. He had no answer. As you can see from the latest "Reverse FMEA" craze, change is difficult.
As you say, we do not need a new tool. We need to use the ones we already have correctly.
I appreciate your commment. Feel free to email me with any questions you may have about any type of FMEA (Machinery, Design, Process, Reverse, etc.) at richard.harpster@harpcosystems.com
Rich
Add new comment