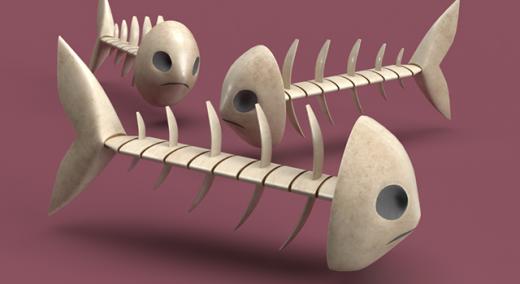
Almost seven years ago, Quality Digest presented a short article by Matthew Barsalou titled “A Worksheet for Ishikawa Diagrams.” At the time, I commented concerning enhancements that provide greater granularity. Indicating that he would probably have little time to devote to such a project, Barsalou graciously invited me to expand upon his work. As one of the few positive outcomes of the recent storms that have raged across the United States, I’ve finally completed that task. In thanks to Barsalou—and with tribute to his mentor—I refer to this effort as the “Enhanced Perkin Tracker.”
…
Comments
Wrong Attachment?
I think you attached the wrong file.
You might be right
ENHANCED PERKIN TRACKER
I've not seen this before. It looks like a cross between a Ishakawa Diagram and a FMEA. This will help in priortizing how your project would move forward. I'll certainly try to use this on my next project. Thanks.
Problem with risk priority numbers
Alan, thanks for your contribution. It is clear there is a need for such prioritization in at least some cases, but I am afraid that your proposed solution suffers from the same fundamental mathematical issue that many (most?) FMEA tools, or House of Quality tools suffer from. Namely that you use ordinal scales (for 4 different quantities), and then you multiply them together. It may seem OK at first glance (similar things are done for FMEA's or Houses of Quality), but unfortunately no arithmetic operation can be performed on ordinal variables. This is simply because they do not preserve scale: a rating of 5 is absolutely NOT 25% more than a rating of 4, and a rating of 2 is not twice (as likely, as costly, as ...) as a rating of 1. 1 does not mean 1, it just means lowest. Multiplying lowest by "next lowest" has no meaning.
You may want to read the article published by Donald Wheeler in Quality Digest: "Problems with Risk Priority Numbers" https://www.qualitydigest.com/inside/quality-insider-article/problems-r…, where he describes this practice (of performing arithmetic on ordinal values as "utter and complete nonsense" (his words, not mine).
Now, if you could derive ratio scales for your 4 criteria, the issue would go away (likelihood, in percent, of the item under consideration being the true cause, cost in $ of the experiment, duration in days of the experiment, odds of success in percent of the experiment), you then could, and should multiply these; but multiplying the percentages, the cost, the duration. This would give you an expected cost-duration.
Thanks
Risk Priority Numbers
While I understand your logic, I prefer to think of the system as dividing each grouping into "n-tiles". When performing this exercise, we are guessing... arriving at a concensus that the probability lies within a range. If merited, simply increasing the ordinal range narrows the range of probailities for each bucket.
I would also make the arguement that expressing the ranking as a decimal may imply, to the casual user, an unwaranted degree of certitude. If you were to limit yourself to one decimal place, how does 0.1, 0.2, 0.3,.... differ from 1,2,3,...? And, for a guess, can one differentiate between .10, .11, and .12?
In whatever manner one might choose to use this system, ordinals or decimals may be utilized, or with a simple revision, decimal values entered directly. Whatever values one chooses to use, in the end, we arrive at a ranking to aid in rational planning.
Thanks for the input
Ishikawa Diagrams
Dr Ishikawa had 3 types of Cause-and-Effect Analysis. It is unfortunate, that most say "Fishbone" for Type A and B when in his books he never described that type as such. These are useful for Event Problem indeed. However, as all work happens through processes, Ishikawa's Process Classification or as Don Dewar (RIP) described and simplified it to the Process Cause and Effect, is more appropriate to process-based problems.
Using a so-called Fishbone on a Process Problem is not as he advised and is sub-optimal in cause analysis. He pointed out that if there were too many causes and expanded 5-Why analysis (see AIAG FMEA for Flow Process Chart or Maynard Industrial Engineering HB and editions) on the highest ranked causes for respective arms or "bones", then the situation is too complex (Event). For processes, it is too unstable (Process). Reference to Standardized Work or Procedures in Processes of the Management System is the foundation.
As others have mentioned, if there are too many causes, these also direct one to the PFMEA as they should have been identified. Too much Problem Solving and one knows the PFMEA is wrong. This Perkins Table could be useful, but Dr Wheeler as the Comment described, provides reasons not so.
For weighting or ranking causes, in doing such Ishikawa Diagrams on real projects across diverse industries, the simple tasks of good brainstorming and data collection is required. Post brainstorming, and where needed to clarify the cause if needed with ‘known’ and current 'evidence' for the causes so voted, then some 5-Why Analysis on the highest ranked cause/s followed by a basic data collection plan on the highest ranked causes, works fine and helps team member segregate the causes from symptoms, or what they thought were causes, were not. Useful discussion and article.
Perkin Tracker
Hi Alan, I like what you did. It is an improvement over the original version.
I have been working on an update since 2019 as part of a PhD thesis and your worksheet is close to my new one. However, I took a different approach and I’m using a matrix for prioritization. My professors require publication in a journal, so it will still be a while before my update is available.
Add new comment