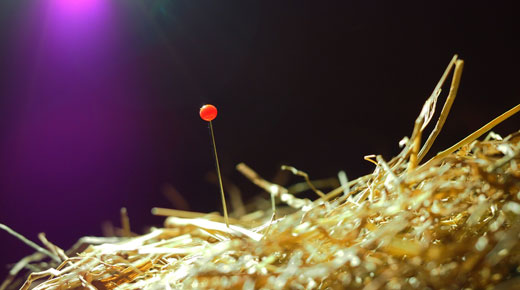
Aerospace standard AS9138—“Quality management systems statistical product acceptance requirements” was issued this year (2018), a few years after its accompanying guidance materials in section 3.7 of the International Aerospace Quality Group’s (IAQG) Supply Chain Management Handbook. The new aerospace standard supersedes the aerospace recommended practice of ARP9013 and, related to MIL-STD-105 (ANSI/ASQ Z1.4), claims to shift focus from the producer’s risk to the consumer’s risk with sampling plans having an acceptance number of zero (c=0).
ADVERTISEMENT |
Somewhere along this evolutionary path, the sampling procedures of MIL-STD-105 have fallen out of favor, even though the consumer risks of MIL-STD-105 at their designed lot tolerance percent defective (LTPD) point are superior to most plans found within AS9138.
…
Comments
acceptance sampling
It is very hard to break the tradition of c=0 sampling plans. As you so smartly show, sample size can get to be rather exaggerated. I recently published a paper on consumer and producer risks where both parties can suffer from alfa and beta, but in different proportions. I would really appreciate your comments.
https://link.springer.com/article/10.1007/s40092-017-0231-9
acceptance sampling
Hello Robert - I am in receipt of your paper and I will be happy to comment through your email account once I have an opportunity to fully appreciate your research. - Thank You
Add new comment