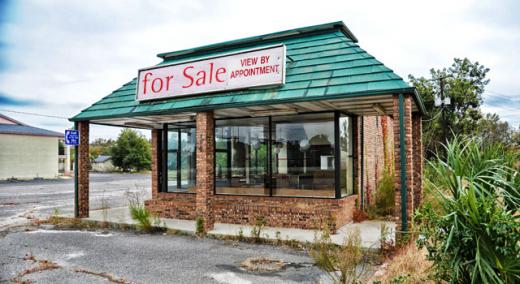
Just as baby boomers on the manufacturing plant floor are getting ready to retire, so are the owners. More than 5,000 small manufacturing operations (with annual revenues between $2 and $20 million) will either close their doors or find new owners during the next five years.
ADVERTISEMENT |
Some of these owners are motivated to keep the business running for their seasoned and experienced employees. Others really want to “cash-out” after decades of hard work. What few of these founders/owners consider is what they can do during the next year to help their businesses be seen as attractive and worthwhile to prospective buyers.
|
…
Add new comment