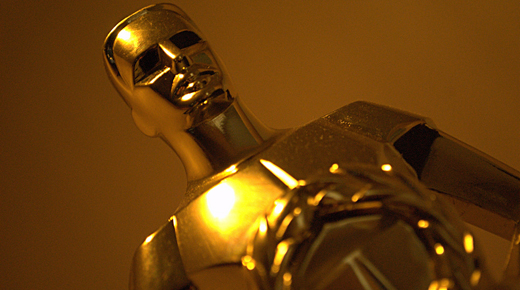
In a previous article I wrote about the reasons why so many lean manufacturing, Six Sigma, and other improvement programs fail. In this article I’m going to expand on reason No. 1: the Academy Award Syndrome.
ADVERTISEMENT |
Academy Award Syndrome
The Academy Award Syndrome is where a program or project is launched to much fanfare, ceremony, and expense, but six months later all that remains is a bunch of faded posters on the wall, boxes of expensive and unused workbooks, and an even more cynical and jaded bunch of employees than we had before.
In our society we are generally becoming more cynical. We are certainly overwhelmed with the launches of new initiatives from our politicians, from companies that are trying to sell us new products, and the daily media cycle that supports these launches.
Within a company our new project or initiative that we are all enthusiastic about is probably not the first that has ever occurred. If previous initiatives have been launched and then abandoned, our employees can be very cynical, and this can cripple our program.
…
Comments
Broken link
Great article. It is a pity that the link to the previous article is not valid.
Link removed
Add new comment