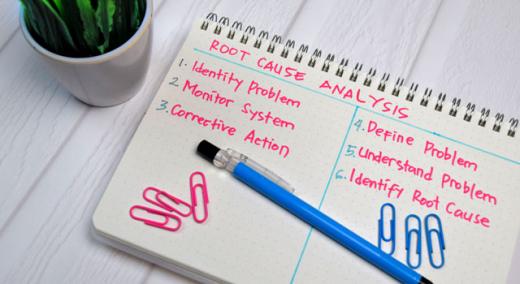
Within every organization, problems or incidents arise that can affect the quality of your operations. Take for example, food recalls due to improper food labeling that not only could cause sickness in humans, but also result in a hit to a company’s reputation. Or, automotive product recalls due to defective parts.
ADVERTISEMENT |
Today, given supply-chain disruptions that require broader sourcing of materials, along with a shortage of skilled workers, the chances of problems rising are increasing exponentially.
Whether causing a minor blip in productivity or tragic results, any problem should be evaluated to minimize the chances that it could occur again. And, while we read about manufacturing issues almost daily, we don’t always learn what the root cause of the problem was and how it was corrected.
…
Add new comment