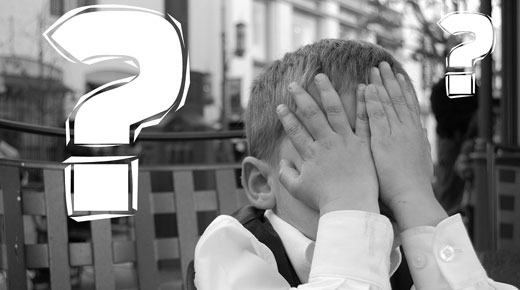
Here’s a quick rundown of what we covered in part one of our list of top 10 mistakes to avoid when using statistical process control (SPC): training everyone, charting everything, segregating control charts from manufacturing, “pinching” the SPC coordinator, and using SPC because it’s a “good thing to do.” Let’s continue with our list.
ADVERTISEMENT |
You: Wait, I thought you were done. There are more? OK, let’s do this thing.
Me: Yeah, there are more. Five more, actually. We’re getting to the really meaty stuff. Stay with me. But remember (disclaimer time again), please do take the right steps that all the experts in all the books discuss, and don’t commit the mistakes I’ll be listing here.
So, let’s continue on with our list. Here are mistakes numbers five through one.
…
Comments
another big mistake
Charting outputs of the process rather than inputs. Doing so just creates "inspection with control charts" as opposed to SPC.
Add new comment