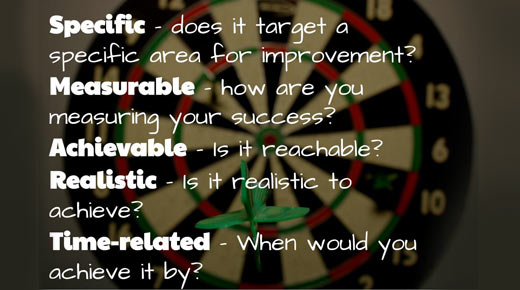
Be SMART about your goal setting
Credit: Aaron Davis
Completing the define phase of a lean Six Sigma (LSS) project is a critical part of any project, although it’s often underestimated in practice. The define phase of the define, measure, analyze, improve, control (DMAIC) process typically includes three elements. The first is selecting a specific, measurable, achievable, relevant, and time-bound (SMART) project objective. Second is creating a charter, and third is selecting a process to be improved. However, a lot more needs to be done before moving to the measure phase.
ADVERTISEMENT |
When Motorola created Six Sigma, it was originally set up as a four-step process, namely “MAIC.” The define step was added when it was found that having a clear, agreed-upon understanding of the project was critical to success. In this article, we discuss 10 key elements project leaders must keep in mind in completing the define phase. These ideas can also serve as a rubric for evaluating project presentations.
…
Comments
Lean Six Sigma Methodologies...
I completely agree with the methods and approach of this article. In my experience I have preferred using the Plan Do Check Act (PDCA) model of project planning due to the use and application of Lean tools in environments that do not require as much data analysis in order to effectively manage the improvement opportunity. From an RTG Solutions Group prospective we strive to include and engage every associate at every level of the organization; this is imperative to the success of the organizational initiative. It also provides the mechanism that can be used to organically develop a Change Management model that ultimately leads to overall Organizational Development of people and processes.
Lean
The aspect of providing time and resource for the project to finish properly is important. Most of the time people are busy with their work and giving time is a constraint.
Add new comment