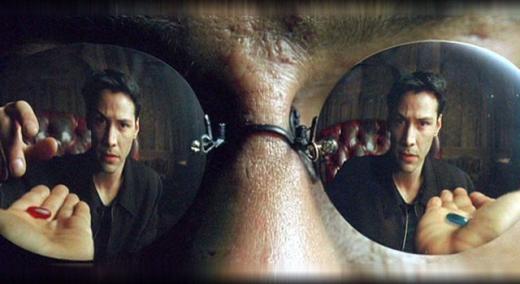
I must confess up front that the title of this column is misleading. Similar to the Spoon Boy in the movie, The Matrix, I will say, “There is no lean problem or a Six Sigma problem. All these problems are our mental constructs of a perceived phenomenon.”
ADVERTISEMENT |
A problem statement is a model of the actual phenomenon that we believe is the problem. The problem statement is never the problem! It is a representation of the problem. We form the problem statement based on our vantage point, our mental models, and biases. Such a constructed problem statement is thus incomplete and sometimes incorrect. We don’t always ask for the problem statement to be reframed from the stakeholder’s viewpoint.
A problem statement is an abstraction based on our understanding. Its usefulness lies in the abstraction. A good abstraction ignores and omits unwanted details, while a poor abstraction retains them, or worse, omits valid details. Our own cognitive background hinders our ability to frame the true nature of the problem.
…
Add new comment