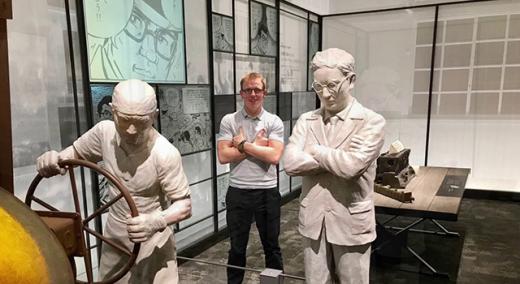
In today’s column, I’m looking at the Ohno Circle in light of German philosopher Martin Heidegger’s ideas. I’ll try to stay away from the neologisms used by Heidegger and will only scratch the surface of his deep insights.
ADVERTISEMENT |
One of the best explanations of the Ohno Circle comes from one of Taiichi Ohno’s students, Teruyuki Minoura, the past president and CEO of Toyota Motor Manufacturing North America. He had firsthand experience of it. Minoura noted: “Mr. Ohno often would draw a circle on the floor in the middle of a bottleneck area, and he would make us stand in that circle all day long and watch the process. He wanted us to watch and ask “Why?” over and over.
“You may have heard about the five ‘whys’ in TPS. Mr. Ohno felt that if we stood in that circle, watching and asking why, better ideas would come to us. He realized that new thoughts and new technologies don’t come out of the blue—they come from a true understanding of the process.
…
Comments
Walking is Waste
Sometimes exercise is waste.
Nurses in a nursing unit can walk 10,000 steps during a shift looking for supplies. While they are walking, they are not with patients. Virginia Mason identified the seven supplies nurses need. Now, instead of spending only 30% of their time with patients, nurses spend 90% leading to better care, outcomes and satisfaction.
Most of the time, walking is waste.
Ohno Circle
Hi Harish,
From almost the get-go. I've had a major problem with the actual pragmatic nature (as opposed to the philosophical nature) of Ohno's Circle. First and foremost, no indication is ever provided as to what the optimal placement of an observation circle (i.e., vantage point) ought to be relative to a process of interest. Second, most end-to-end processes are spread out and, as a result, would be impossible to fully observe and understand from a single vantage point, no matter how judiciously it may have been selected. Third, making anyone, regardless of the underlying intent, spend an entire day in a single spot observing a process (or some subset of the overall process) seems - IMO - to run contrary to the fundamental principle of having and demonstrating respect for the human being.
In light of these perceived issues/whete short-comings, what I consider to be a more appropriate, value-adding approach is to actually walk around the entire end-to-end process with the intent of understanding it as an integrated system whose constituent elements are both interacting and interdependent. Then, IN THAT CONTEXT, try to figure out both WHERE and WHY inefficiencies exist. And I would allow - within prescribed safety limits - an observer to move about at will - including interactioning with the worker(s) until they are satisfied with their understanding and findings. Then, I would under take a debriefing with the observer(s) and focus on WHY they came to the understanding and conclusions they did.
Bottom line: The approach to learning and building understanding and knowledge as prescribed by Ohno - via his standing circle method - is too static, limited in perspective, not open to investgative initiative, and totally reliant upon one's pre-existing and often limited knowledge base. In these multiple regards I tend to view the Ohno Circle approach as being outdated and fundamentally flawed.
Add new comment