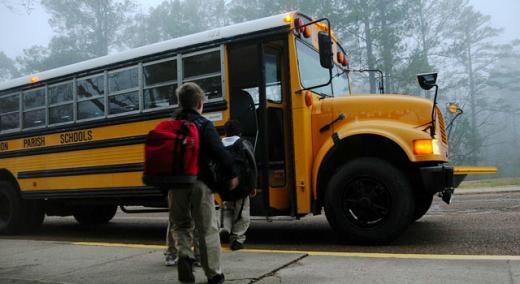
Whatever the process or type of data collected, all data display variation. This is also true in software development. Any measure or parameter of interest to our business will vary from time period to time period, e.g., number of incidents per week or month, time taken in resolving incidents, number of tickets encountered in a production support environment per month, and defect density in code.
ADVERTISEMENT |
Understanding variation is about being able to describe the behavior of processes or systems over time. This variation can be stable, predictable, and routine, or unstable, unpredictable, and exceptional. Being able to distinguish between stable or common-cause variation, and unstable or special-cause variation, helps us to decide the type of action needed to improve the process. The control chart, developed by Walter Shewhart, is the tool that enables us to do so.
…
Comments
Common Cause Reduction in Software
Control charts can help monitor software system performance.
You can also use control charts, Pareto charts and root cause analysis to eliminate bugs that are the common cause of errors. And you don't need much data to do it.
Here's how: https://www.qimacros.com/pdf/dirty30.pdf
Other mistakes
First, good work on this...we don't get enough examples from other industries of the types of measures that could be monitored with process behavior charts. You might consider a follow-on article describing some of those measures you discussed in your first paragraph or so. I would like to be able to add those to a list I keep so when someone tells me "...yeah, sounds good, but you couldn't do that in MY industry..." I can show them examples. Sometimes it helps.
There are other errors you can make while investigating variation, even if you're using process behavior charts. Subgrouping unlike things is one--fortunately, if you understand what the charts are saying, the voice of the process will tell you about this, too, by hugging the centerline. Lack of good operational definitions will hurt you, too. One of the worst errors I ever made was allowing a company to just send me the data each month so I could put it on a chart for them...I think I will put together an article on this one; Dirk might find it useful.
Re RIP STAUFFER
Thanks RIP STAUFFER. Yes i beleive this kind of work has not been done much before. Will try and consider a follow up article as well.
My Contact
For any queries please reach me at rohitmathur100@gmail.com
Feedback
Everyone, will love to hear any feedback on rohitmathur100@gmail.com
Add new comment