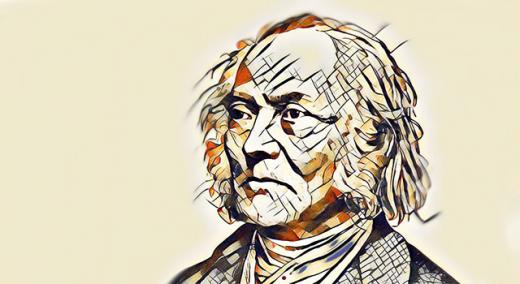
In today’s column, I’m looking at Weber’s Law. It’s named after Ernst Heinrich Weber (born June 24, 1795, died Jan. 26, 1878), a German physician who was one of the pioneers of experimental psychology. I highly recommend the Numberphile YouTube video that explains this in detail.
ADVERTISEMENT |
A simple explanation of Weber’s Law is that we notice things more at a lower intensity than at a higher intensity. For example, the light from your phone in a dark room may appear very bright to you. At the same time, the light from your phone in a bright room may seem insignificant. This type of perception is logarithmic in nature. This means that a change from 1 to 2 feels about the same as a change from 2 to 4, or 4 to 8. The perception of change for an increment of one unit depends on whether you are experiencing it at a low intensity or a high intensity. At low intensity, a slight change feels stronger.
…
Add new comment