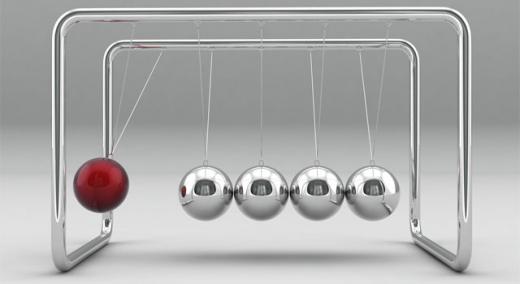
Today I’m looking at Factory Physics and the Toyota Production System (TPS). My main references for the post are the 1977 paper co-authored by ex-Toyota president Fujio Cho and key ideas from Factory Physics (Waveland Press, 2011).
ADVERTISEMENT |
One of my favorite definitions of lean comes from Wallace J. Hopp and Mark L. Spearman, who wrote Factory Physics. They defined lean as follows: “Lean is fundamentally about minimizing the cost of buffering variability.... Production of goods or services is lean if it is accomplished with minimal buffering costs.”
…
Add new comment