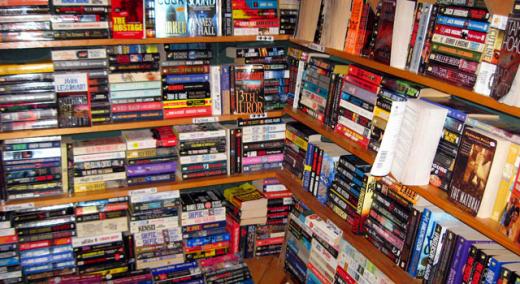
As usual with Quality Digest’s diverse audience, this year’s top stories covered a wide range of topics applicable to quality professionals. From hardware to software, from standards to risk management, from China trade to FDA regulations. It’s always fun to see what readers gravitate to, and this year was no different.
ADVERTISEMENT |
Below are five articles that garnered a lot of interest from our readers. As you can see, the topics are quite diverse.
![]() |
Improve Risk Management and Quality Across the Value Chain by Increasing Visibility
by Kelly Kuchinski
…
Add new comment