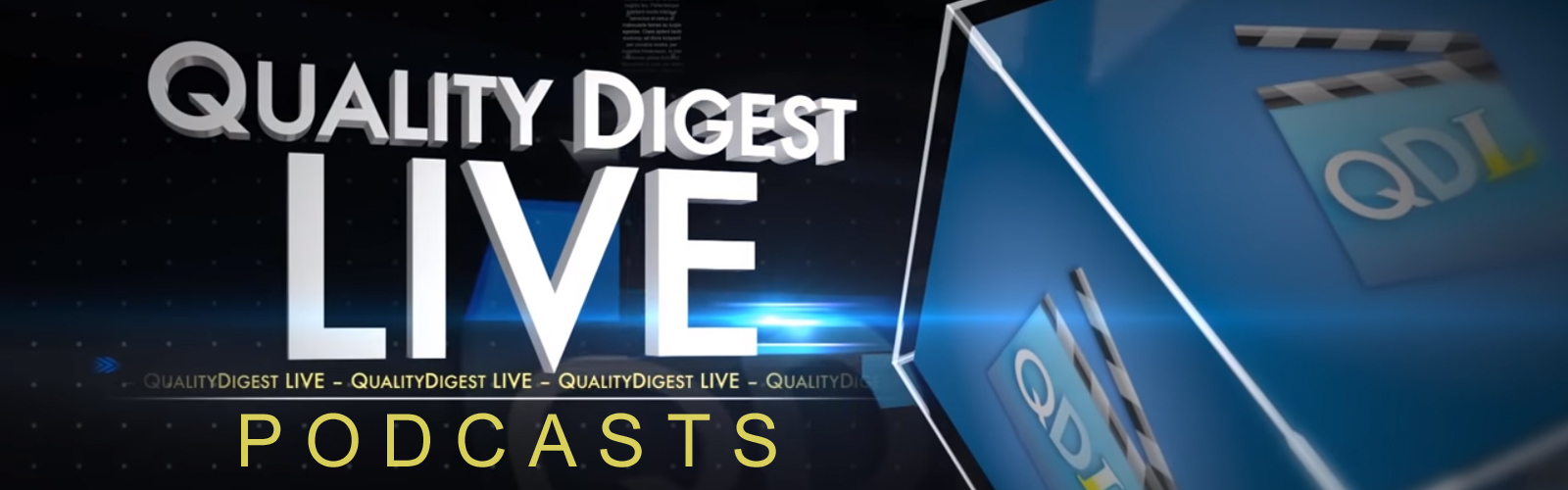
Current business conversation often focuses on data and big data. Data are the raw information from which statistics are created and provide an interpretation and summary of data. Statistics make it possible to analyze real-world business problems and measure key performance indicators that enable us to set quantifiable goals. Control charts and capability analysis are key tools in these endeavors.
Control charts
Developed in the 1920s by Walter A. Shewhart, control charts are used to monitor industrial or business processes over time. Control charts are invaluable for determining if a process is in a state of control. But what does that mean?
“We’re really just talking about a process or system that’s stable and predictable,” explains Matt Savage vice president of product development for PQ Systems. “If it’s in a state of statistical control, it just means that the processes are expected in the future to do what [they have] been doing in the past. Control charts help us understand, statistically, whether a process is in fact stable or whether you’ve got some anomalies, or special causes, or out-of-control points. A control chart is just a simple run chart if you will, with a little bit of math or statistics that help give you clues when the process may have changed, or if in fact it did change, it’s going to give you some clues about that.”
…
Add new comment