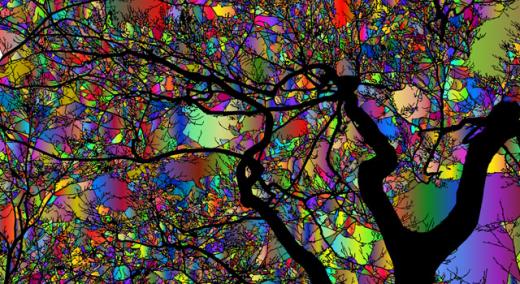
Lean Six Sigma (LSS) professionals have an enormous opportunity to add value to organizations and to our communities during this coronavirus pandemic. We have the objective orientation, methods, and tools to help. Process improvement is currently more important than ever in this “new normal” environment. Furthermore, it is clear that this is not a short-term event; it is a time for structural change. We also do not have the time to ponder the possibilities for too long.
ADVERTISEMENT |
The purpose of this article is to suggest a few thoughts and actions that would be helpful to consider.
The opportunity is huge because there is a clear need for change. Everyone is aware that we need to rethink our processes for the sake of the health crisis, as well as for economic reasons. And it is also obvious that we need analytics to find the proper balance between reward and health and safety. This is also not new to us, as this trade-off has always been with us, especially in manufacturing.
…
Comments
Kaizen or Kaikaku?
Six Sigma has traditionally aligned itself with Kaizen. While I am not sure about LSS, the rapid onset of the virus its transmission, probable mutation, and effects on the economy would infer that Kaikaku might be a better strategy for adjusting to the changing medical and economic conditions.
Kaikaku, which has been incorrectly labeled as 'Breakthrough Kaizen' by some, is a method of change that is more dynamic and rapid, as opposed to the methodical cyclic DMAIC process endorsed by Kaizen. While some traditional LSS types might fear rapid, radical change, we should take heart in knowing that Kaikaku-type change has been used for more that 50 years in Project Management; a method known as 'Waterfall'. Only in the past decade has Project Management begun to endorse Kaizen-type methods, known collectively as 'Agile'.
Rapid response to change during these covid-19 times can make the difference between ' business as usual' and innovation, between abysmal performance and success, between failure and company survival. Kaikaku should certainly be considered when change is planned for implementation during these rapidly developing scenarios. 'Analysis Paralysis', a frequent drawback of Kaizen, must be avoided in any case.
Add new comment