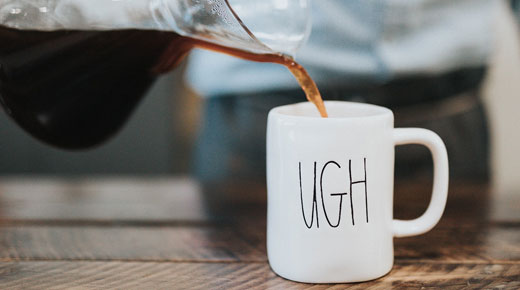
Quality tools can serve many purposes in problem solving. They may be used to assist in decision making, selecting quality improvement projects, and in performing root cause analysis. They provide useful structure to brainstorming sessions, for communicating information, and for sharing ideas with a team. They also help with identifying the optimal option when more than one potential solution is available. Quality tools can also provide assistance in managing a problem-solving or quality improvement project.
ADVERTISEMENT |
Seven classic quality tools
The Classic Seven Quality tools were compiled by Kaoru Ishikawa in his book, Guide to Quality Control (Asian Productivity Organization, 1991). Also known as “The Seven Tools” and “The Seven Quality Tools,” these basic tools should be understood by every quality professional. The Classic Seven Tools were first presented as tools for production employees to use in analyzing their own problems; they are both simple enough for everybody to use, yet powerful enough to tackle complex problems.
…
Comments
Back to Basics
Great to see Mark getting back to basics and avoiding the material that is irrelevant to process improvement, not to mention avoiding the ridiculous dpmo. As Dr Deming put it:"The student should avoid passages in books that treat confidence intervals and tests of significance, as such calculations have no application in analytic problems in science and industry." (W. Edwards Deming, Out of the Crisis, page 639.)"Analysis of variance, t- test, confidence intervals, and other statistical techniques taught in the books, however interesting, are inappropriate because they bury the information contained in the order of production." (W. Edwards Deming, Out of the Crisis, page 132.)
Out of the Crisis, Page 639
Interesting quote from page 639. What edition of, "Out of the Crisis" are you using? Both my copies (two different editions) are just under 500 pages each.
Add new comment