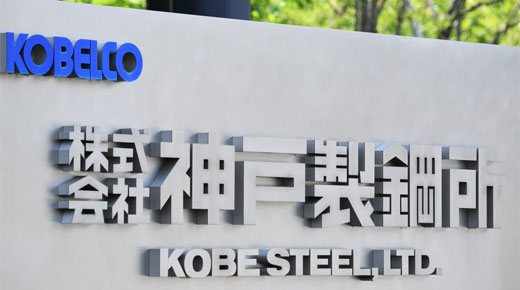
The cheating at Kobe Steel shook not just Japan but the entire manufacturing world. As Kobe Steel CEO Hiroya Kawasaki revealed, about 500 companies had received its falsely certified products, which affected not only those companies but also its entire supply chain. However, the issue at Kobe was only the latest. Sadly, Japan has had many quality eruptions during the past year, including the recent recall by Nissan Motor Co of more than one million vehicles, and the major quality issues with now-bankrupt airbag producer Takata Corp.
ADVERTISEMENT |
As W. Edwards Deming said, more than 85 percent of quality problems are due to management, and that seems to be the case with what happened at Kobe Steel.
Here are few lessons that top management in any company could learn from Kobe Steel’s problems in order to avoid the same.
…
Comments
Good solution, but not to the Kobe problem.
Hi,
Thanks for the article, good thoughts, good internal audit checks for top management brave enough to deal with the findings, but, I fear, not a solution to the Kobe Steel debacle and its kind elsewhere.
You say "A top management diagnosis is a meeting where the CEO and top management come together to discuss all matters that have an effect on the quality of the company’s product or service" and you offer some tools in support, thanks for that.
I don't think the top management at Kobe Steel and the rest of them would be in their current predicaments if any of them were clever enough to understand the point you're making. Why would they wait until their reputations were in tatters and their debtors were kicking in the front door? And who would lead them to carry out your top management diagnosis, isn't that what CEOs are there for in the first place? Isn't such a diagnosis what proper CEOs do every day?
It seems to me that the real problem at Kobe et al was incompetence born of lousy education, inadequate qualifications and a lack of relevant technical experience all backed up by useless recruitment and retention procedures. Hence, if the owners of Kobe Steel and the rest of them were stupid enough to hand over the management of their organisations to idiots they deserved what they got.
The bigger issue for us in our quality world is the failure of the accredited certification system to pick up the quality management system errors and omissions that must have been blatantly obvious at every single audit. What saddens me is the probability that this failure too is probably due to similar "incompetence born of lousy education, inadequate qualifications and a lack of relevant technical experience all backed up by useless recruitment and retention procedures."
Thanks for the audit checks, I do have some clients who will appreciate them.
Kind regards.
Add new comment