All Features
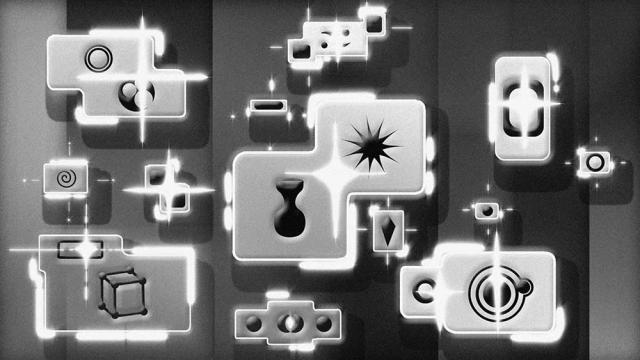
Gleb Tsipursky
In the current professional landscape, idea generation is revered as a hallmark of creativity and innovation. Organizations celebrate those who can generate new and groundbreaking concepts, often overlooking the subtler art of idea curation.
However, the rapid advancement of generative AI is…
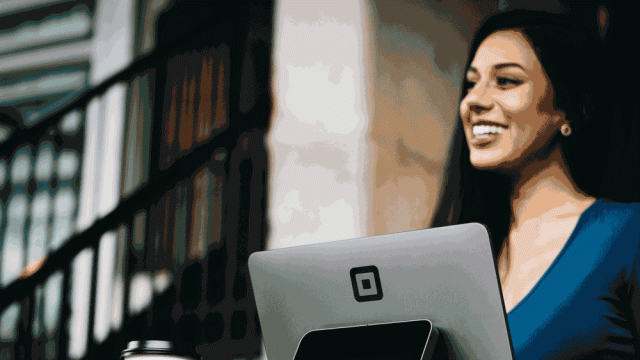
John Tschohl
I ’ve been skiing in Vail, Colorado, one of the best skiing areas in the world, for more than 50 years. George Gillett Jr. acquired the resort in 1985. But when I first met him in 1978 and asked him what he does, he said, “I am in customer service.”
Gillett is out of that business now. And though…
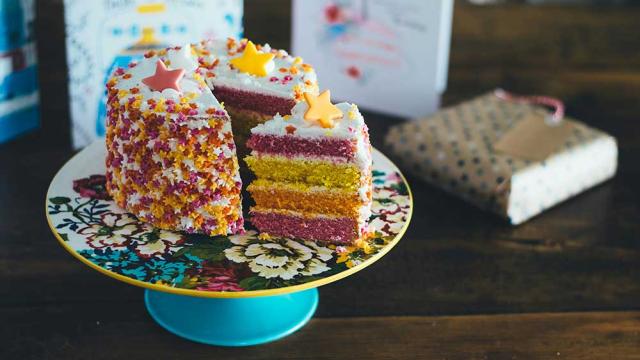
Mike Figliuolo
Things are awesome at work until that dreadful day your boss (with whom you have an awesome relationship) tells you, “Hey, I’ve hired a new person who will be reporting to me, and you’ll now report to that person.” Just like that, you’ve officially been layered. And we all know getting layered is…
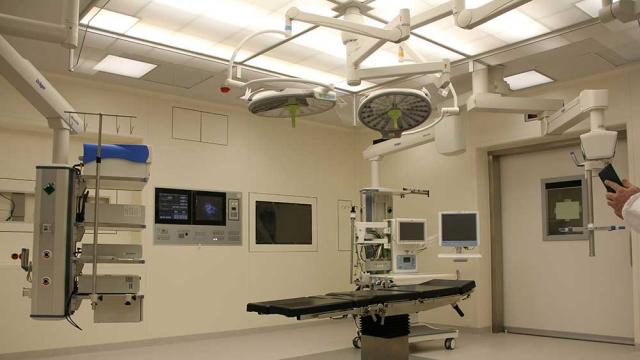
Etienne Nichols
Have you ever wondered what your medtech company looks like from the point of view of a U.S. Food and Drug Administration investigator? Well, this is your chance to find out.
Greenlight Guru invited Vincent Cafiso, a former FDA investigator, to the Global Medical Device Podcast to share his…
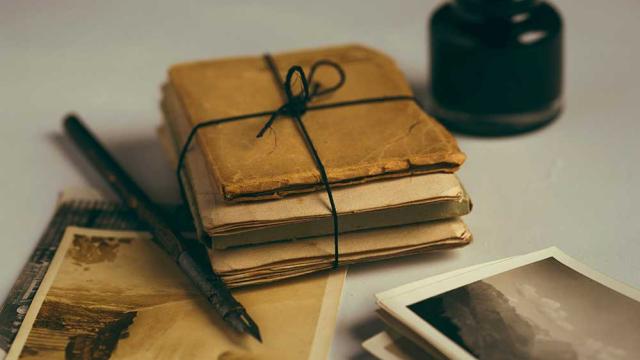
Aimee Levitt
It’s a cliche that the most innovative ideas come in a flash of inspiration: Archimedes in his bathtub, Newton and the apple.
But anyone whose job depends on coming up with new ideas knows that’s not entirely true, mostly because there’s no such thing as a totally novel or original idea. New ideas…
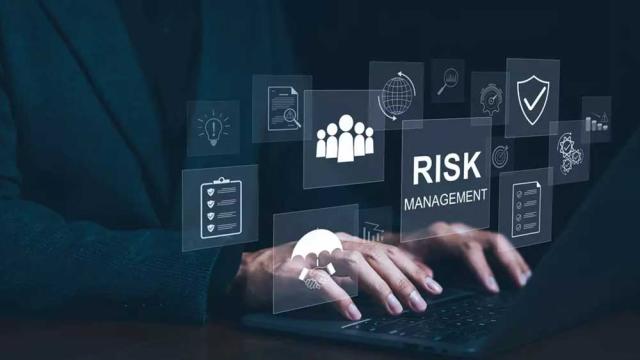
Stephanie Ojeda
Quality risk management (QRM) has become a crucial tool for ensuring regulatory compliance worldwide. It plays a central role in ISO management system standards and regulations, as well as the EU Medical Device Regulation (MDR/IVDR), FDA 21 CFR 820, and ICH Q10 in the pharmaceutical and biotech…
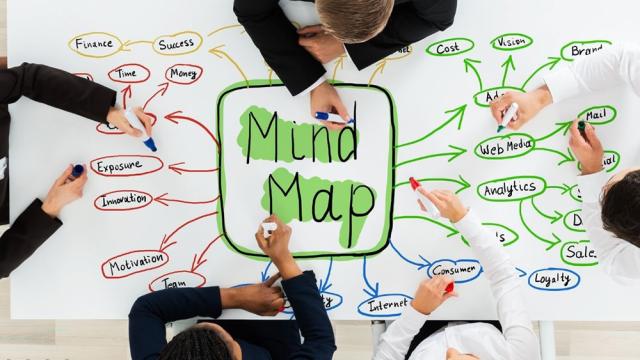
Susan Robertson
Despite the energy and effort you and your team pour into trying to innovate, it often feels like there’s no real progress. When new challenges and opportunities arise, you aspire to chart a bold new course. Perhaps your company has created brainstorming spaces, hired external creative talent, or…
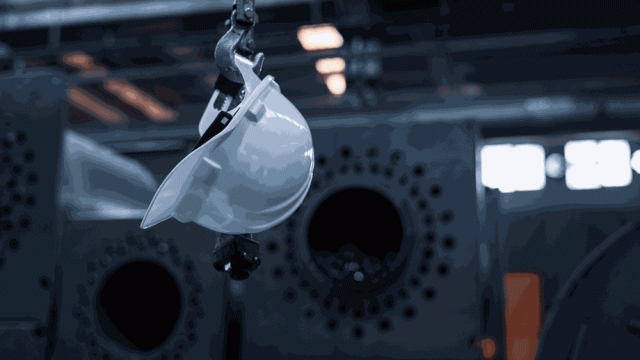
Nick Haase
After spending years working alongside frontline manufacturing teams, I’ve come to see one thing clearly: Preventing incidents isn’t just a legal requirement. It’s the heartbeat of a healthy operation. With workplace safety making headlines daily—often with tragic details—it’s time to highlight how…
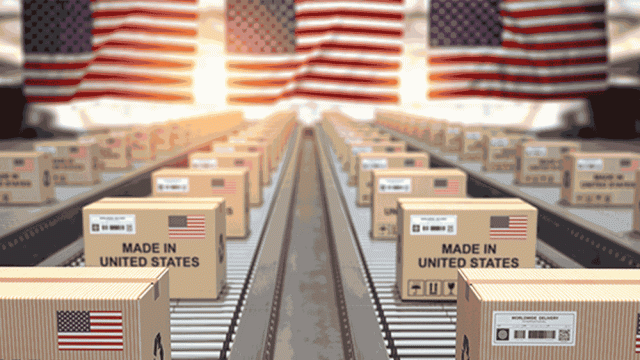
NIST
The U.S. manufacturing industry is evolving at a rapid pace, driven by new technologies, smarter supply chains, and an increasingly dynamic workforce. This year, small manufacturers will face a mix of opportunities and challenges as they navigate these changes. To stay competitive, small and medium…
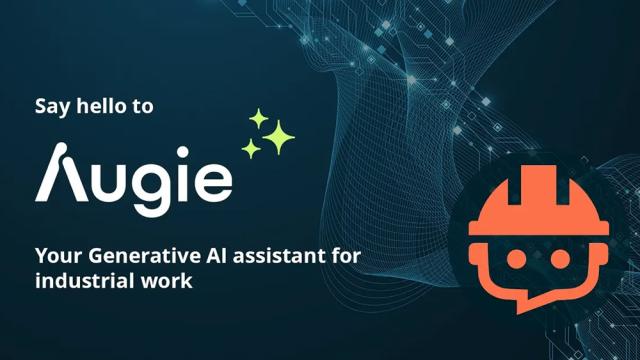
Quality Digest
Augie, Augmentir’s industrial generative AI assistant, is designed to enhance manufacturing operations. Unlike standard AI-powered helpers, Augie relies on real-time operational data, workforce insights, and training records to deliver solutions that integrate smoothly into daily workflows. It…
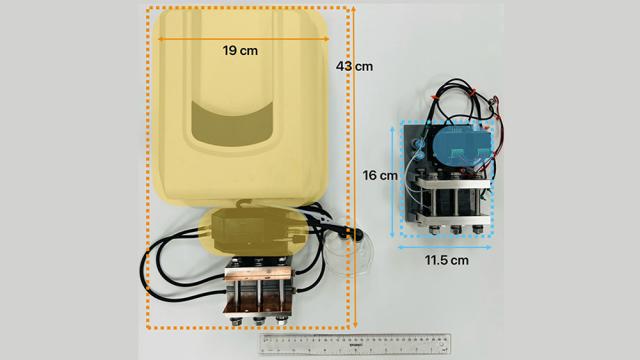
Karyn Hede
Sometimes, to go big you first have to go small. That’s what researchers at the U.S. Department of Energy’s Pacific Northwest National Laboratory have done with their latest innovation in energy storage.
With a goal of speeding up the time to discovery of new grid energy storage technology, the…
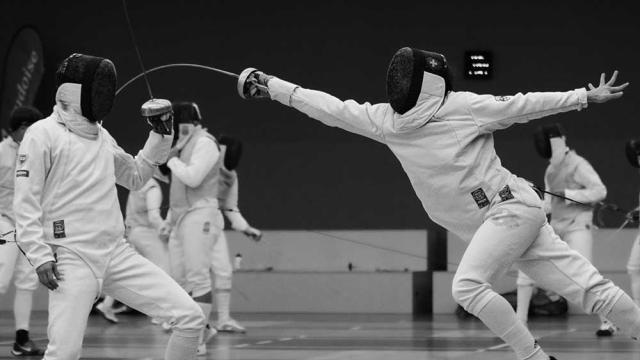
Mike Figliuolo
We all have enemies. Some of us have many. But when we spend our time and energy focused on attacking them and counterattacking their inevitable strikes, we’re the ones losing.
In getting us to attack, our enemy has taken us away from productive pursuits. They’ve hung a dark cloud over our days.…
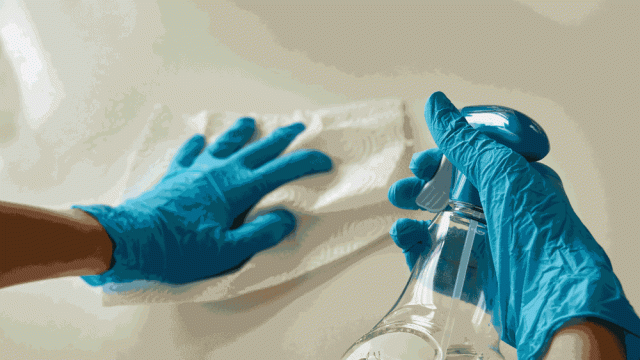
Saurabh Joshi Shripad
Established pharmaceutical facilities play a pivotal role in public health by ensuring the safety and efficacy of the medications they produce. This critical responsibility demands strict adherence to the Code of Federal Regulations, including 21 CFR 211.67—“Equipment cleaning and maintenance,”1,2…
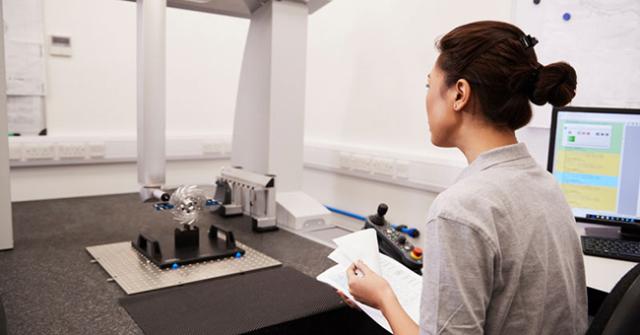
Creaform
Quality control (QC) teams need reliable results they can trust to make informed decisions and address manufacturing challenges. This is why they rely on the coordinate measuring machines (CMMs). However, a CMM’s speed is often a limitation, making the idea that routine quality control can be…
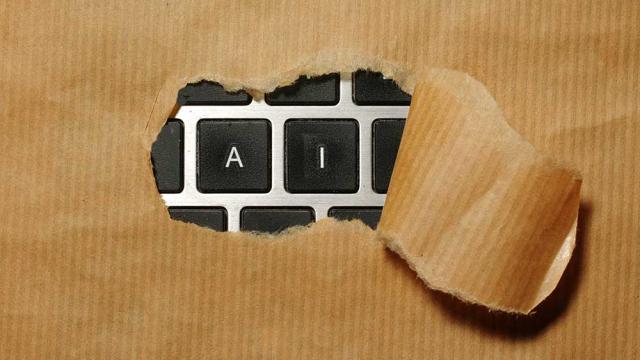
Gleb Tsipursky
The transformative potential of generative AI in learning and development (L&D) is a topic of growing interest among business leaders. And if you think your workers aren’t using gen AI, you might be seriously off-base.
According to a global study of 14,000 workers by Salesforce in late 2023,…
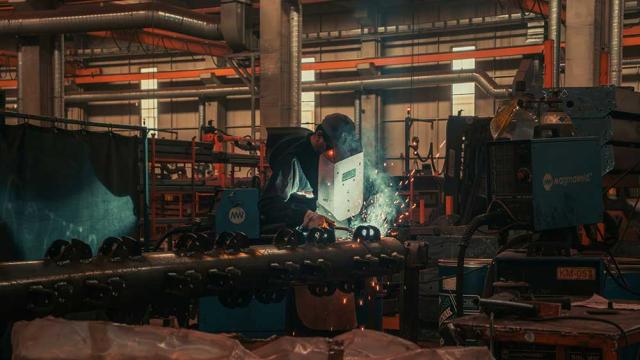
Nathan Ginty
In recent years, reshoring—the process of bringing manufacturing back to the U.S.—has gained momentum. Companies are reevaluating their offshore supply chains, driven by rising costs, geopolitical risks, and supply chain disruptions. For smaller manufacturers, this shift also presents a unique…
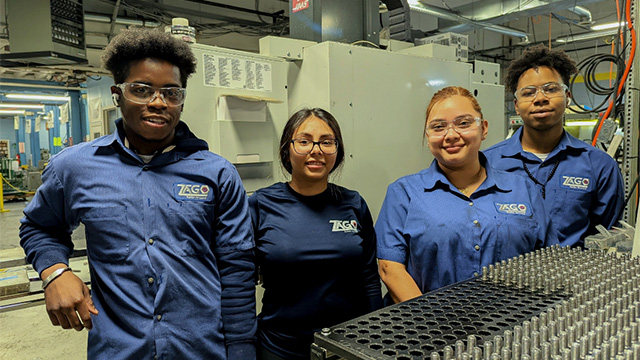
Roy VanGemert Jr.
What if you could meet your new employees a few years before their start date? Imagine a future where skilled workers are readily available in your local market, eager to contribute and connected to your company’s mission.
By investing in a sustainable local talent pipeline, manufacturers improve…
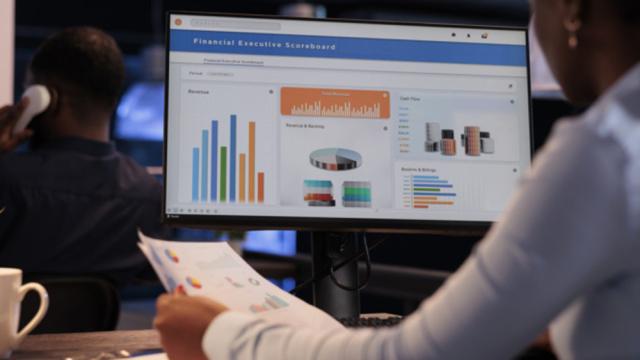
Hannah Fischer-Lauder
In an age where data are among the most valuable assets for any business, the ability to retrieve, process, and utilize information efficiently is critical for success. Yet traditional data-retrieval methods often struggle with the demands of today’s dynamic business environments. Enter retrieval-…
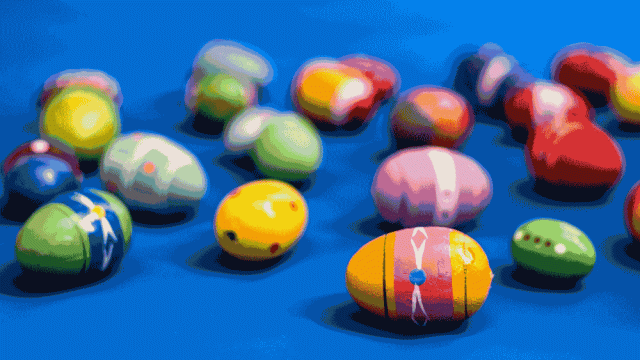
Susan Robertson
Every year, Amy B., a buyer for a large retail chain store, hosts an Easter egg decorating team-building party where she and a bunch of her suppliers spend an entire afternoon coloring and bedazzling boiled eggs. None of them bring kids—they do this for the sheer pleasure of out of the office…
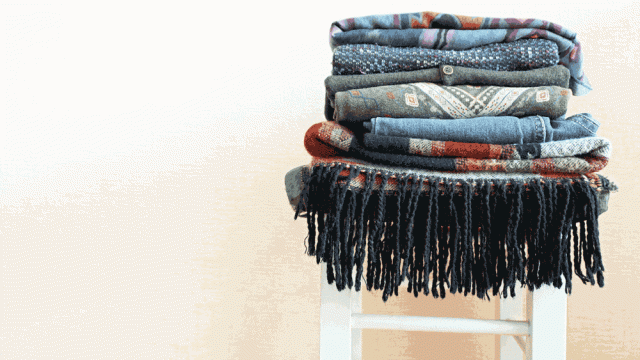
George Schuetz
Machinists working strictly in metalworking shops don’t have many occasions to gage the thickness of soft materials. But many of our readers work in supporting roles, helping to build or maintain the machines that produce textiles, plastic films, paper, and other products that are compressible.…
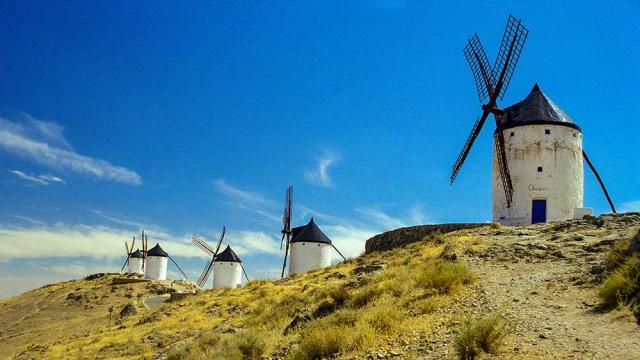
Donald J. Wheeler
The Man of La Mancha never got to the unreachable goal—and if you’re being judged by overall equipment effectiveness (OEE), then your manager may also be dreaming an impossible dream. This column will look at problems associated with the use of OEE values.
OEE is a value often used in lean…
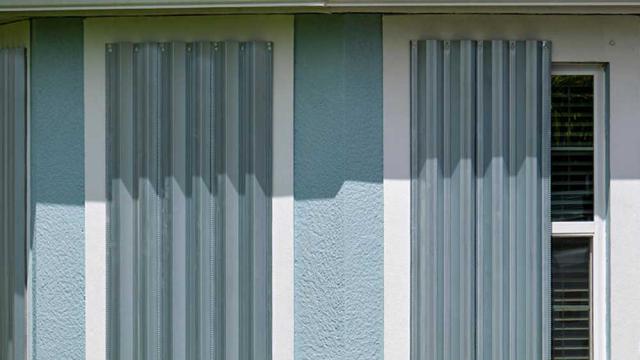
Harry Hertz
My story begins with Hurricane Milton, one of two tragic hurricanes to hit the west coast of Florida last year. Milton went right over Sarasota, where I live part of the year. It was a devastating storm; tree and plant debris still remain on the sides of many roads. Big root balls are still upended…
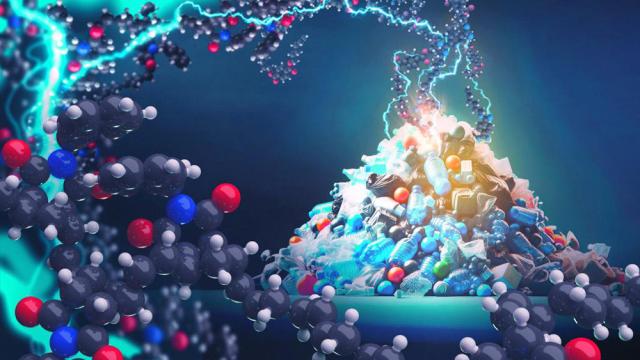
Oak Ridge National Laboratory
By editing the polymers of discarded plastics, chemists at the U.S. Department of Energy’s Oak Ridge National Laboratory (ORNL) have found a way to generate new macromolecules with more valuable properties than those of the starting material. Upcycling may help remedy the roughly 450 million tons…
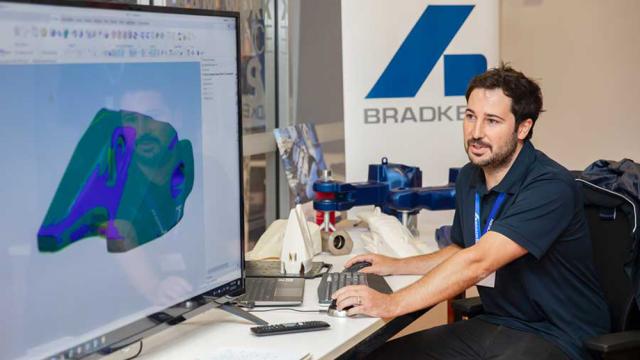
Creaform
Maintaining high-quality standards is critical in the heavy equipment industry. Customers rely on manufacturers to deliver products that perform reliably in harsh and demanding operating conditions. The stakes are high. Deviation from quality and overlooked detail can lead to expensive warranty…
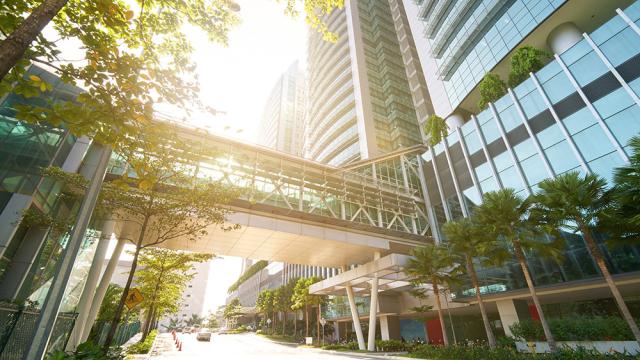
Ben Eidlisz
A safe work environment will foster productivity, reduce hazards, and enhance overall work morale. Keeping your team and assets safe requires implementing the right policies, medical necessities, vigilant oversight, ongoing assessments, and proper training.
As the COO of DUSAW, making smart locks…