Quality control workflows are only as effective as the machinery they rely on. Ensuring functionality requires understanding what to test and how to measure these factors. Consequently, choosing appropriate material testing equipment is a crucial—if overlooked—step in the quality assurance process…
All Features
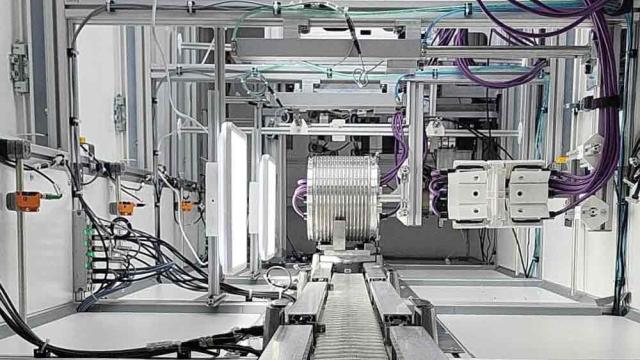
Silke von Gemmingen
In areas such as high-precision metalworking, accuracy is nonnegotiable. This includes the automotive industry and its suppliers, which are in crisis in Germany for several reasons. The industry is under enormous pressure to deliver products of impeccable quality while reducing operating costs (for…
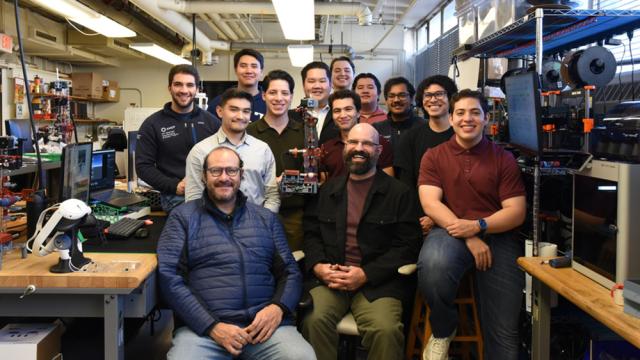
Stefanie Koperniak
For more than a decade through a collaboration managed by MIT.nano, MIT and Tecnológico de Monterrey (Tec), one of the largest universities in Latin America, have worked together to develop innovative academic and research initiatives with a particular focus on nanoscience, nanotechnology, and,…

Creaform
Hawthorne High School of Manufacturing & Engineering in Los Angeles is not your typical high school program. Led by program coordinator Lucas Pacheco, it’s a hub where young minds are immersed in advanced manufacturing and engineering design courses. With a hands-on curriculum covering multi-…
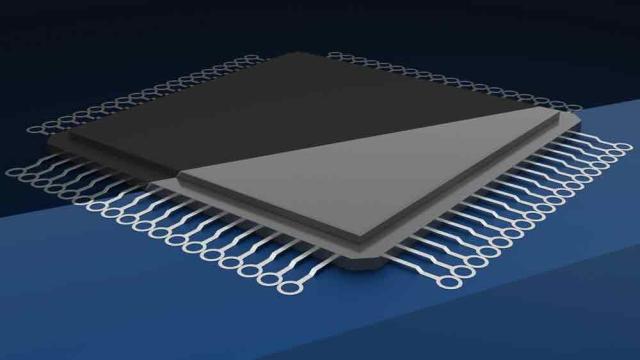
Elisa Duquet
The semiconductor industry is one of the most complex, dynamic, and technologically advanced sectors in the world. It plays an essential role in shaping modern life, serving as the foundation for everything from smartphones and MRI machines to kitchen appliances and space shuttles. In today’s…

Gleb Tsipursky
Generative AI (gen AI) is fundamentally transforming industries, reshaping the way professionals innovate, create, and solve problems. These systems, capable of generating text, images, music, and complex solutions, aren’t just tools—they’re catalysts for a paradigm shift in the professional and…
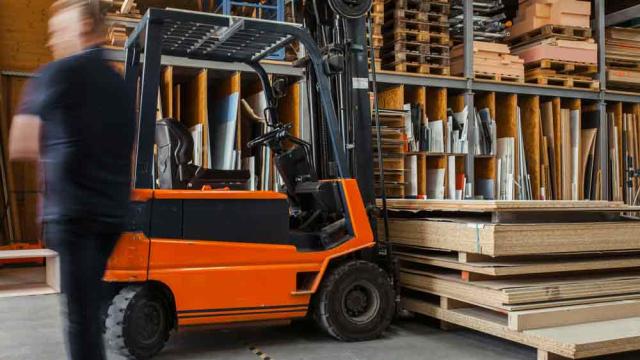
John O'Kelly
Warehouses are the backbone of supply chains, ensuring that goods move efficiently from suppliers to consumers. However, the physical demands of warehouse work—heavy lifting, repetitive motions, and prolonged standing—can take a toll on employees, leading to fatigue, injuries, and long-term strain…
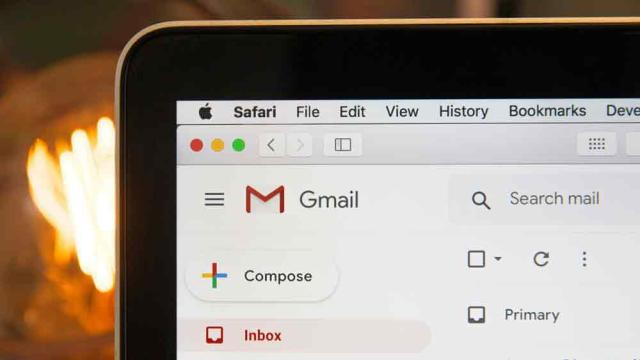
Mike Figliuolo
Email is the bane of our existence. Sure, it’s awesome for funny cat videos, chain letters, and getting awesome blogs like this one (see what I did there?), but it can also cause massive amounts of stress and waste tremendous amounts of time.
One of the first things I do when I take on a new…
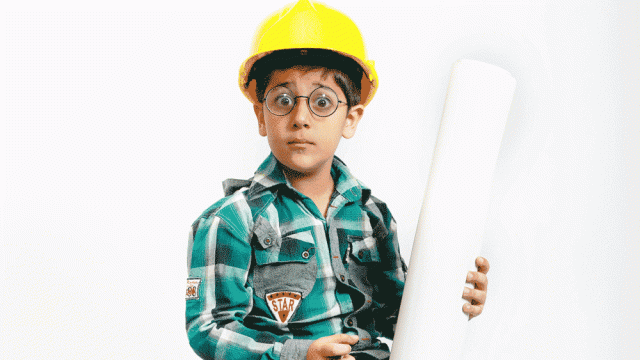
NIST
Every year, employers across the United States open their doors to curious kids, inviting them to experience a day in the life of their parents at work. On April 25, 2025, Take a Child to Work Day and Beyond will give children whose parents work in manufacturing a fun opportunity to explore…
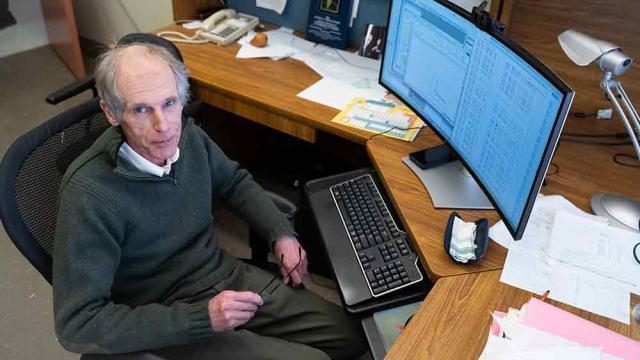
Alexander Kramida
Nearly everything we know about the universe comes from light. Cosmologists learn about the universe by studying light from faraway stars and comparing what it shows us to the light of the same atoms here on Earth. Astronomers use this information to study the expansion of the universe after the…
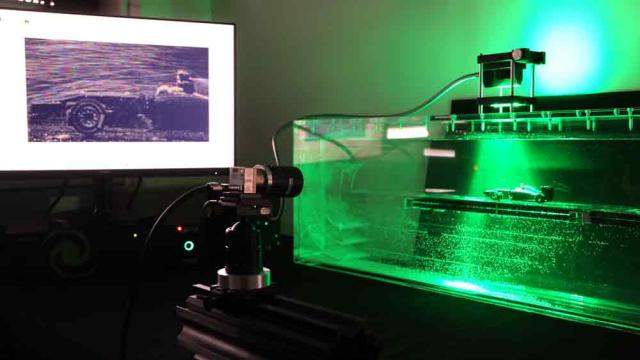
Sabine Terrasi
Today, modern measurement technologies enable high-precision detection of the movement of liquids and gases, providing valuable data for numerous applications. How does air flow around an airplane? How does blood move through our veins? And how can pollutant emissions in combustion processes be…
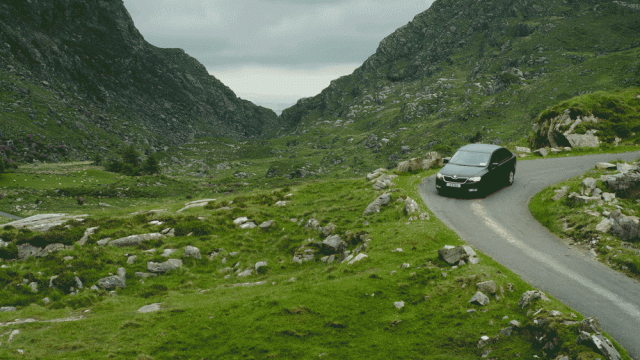
Jones Loflin
I took a deep breath as we left the “car park,” as it’s called in Ireland. The only comforting thought I had was, “I’m glad I paid for the upgrade to an automatic.” Changing gears with my left hand while navigating roundabouts and narrow, rock wall-lined roads was an added stress I didn’t need when…
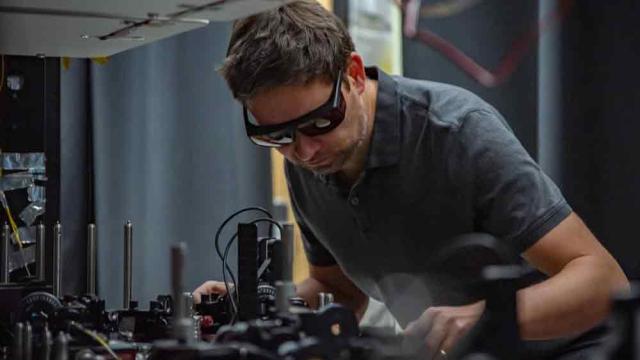
Krister Shalm
One lecture in an undergraduate quantum physics class changed my life forever.
It was 2001, and the professor introduced the idea that physicists could use quantum particles to build a new kind of superpowerful computer. I was so captivated by the idea that quantum physics could lead to…
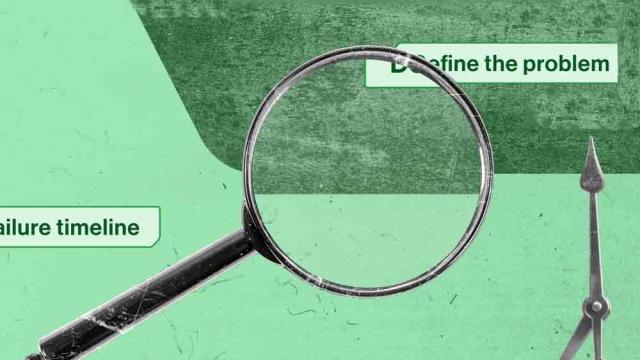
Bryan Christiansen
Failure analysis helps uncover the root cause of equipment issues so you can fix problems and prevent them from happening again. This guide outlines a clear, six-step process to conduct effective failure analysis and write a report that adds long-term value.
Failure analysis techniques vary widely…
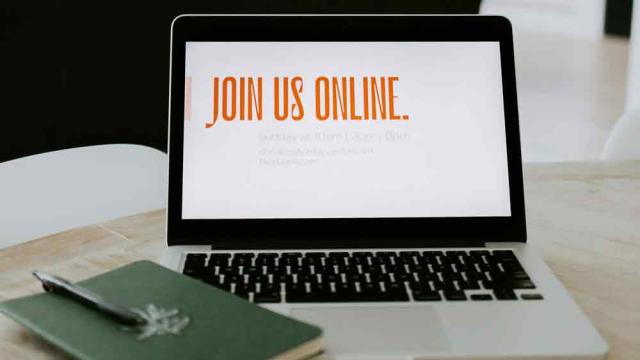
Quality Digest, Donald J. Wheeler
Dr. Donald J. Wheeler has been one of Quality Digest’s most highly read authors for decades. His teaching on the use of control charts in industrial settings has long been considered the gold standard. He has conducted more than 1,100 seminars in 17 countries on six continents, and his books have…
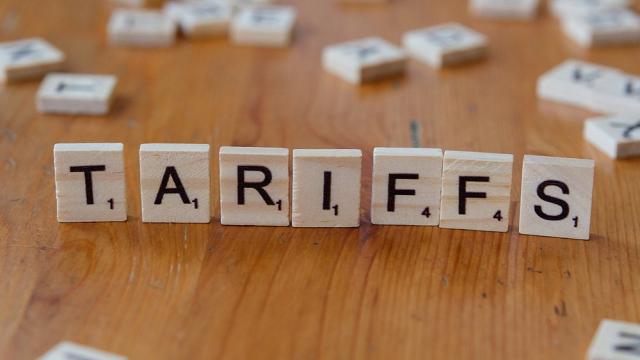
Kelley Jacobsen
As global trade uncertainty intensifies, health systems should take steps to minimize the effect of this volatility on their medical equipment inventory. The evolving policies of the United States and its trading partners could strain global supply chains and make acquiring or maintaining medical…
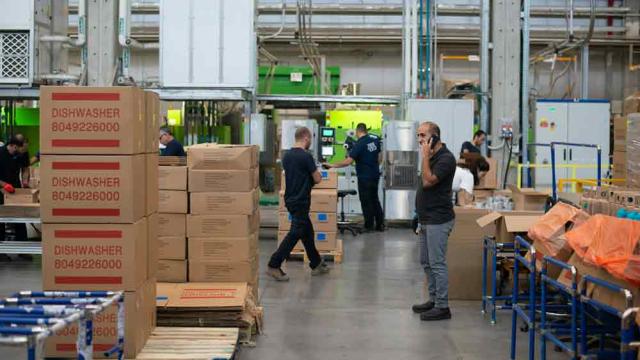
Akhilesh Gulati
As director of quality at a manufacturing plant, James faced the reality of shift every day. As the plant embraced new technologies and adapted to changing global dynamics, he knew that quality management could no longer be reactive. The question was whether he could turn these shifts into…
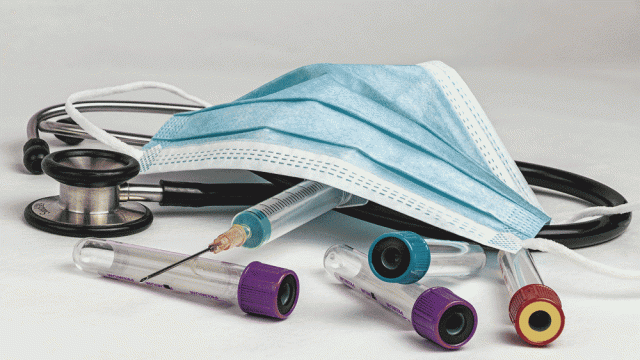
Etienne Nichols
What’s your favorite regulatory pitfall? I know that’s a strange question, but if you’ve spent much time in the medical device industry, there are likely a few that come to mind. People reach out to me all the time asking how to break into the medical device industry—and I love those conversations…
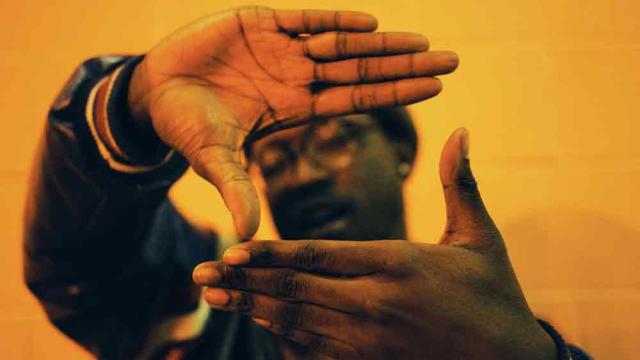
Gleb Tsipursky
Once hailed as both an ethical mandate and a strategic necessity after the upheaval of 2020, diversity, equity, and inclusion (DEI) initiatives now face intense scrutiny and pushback. Major corporations—ranging from Walmart to Google—are quietly retreating from these programs amid escalating…
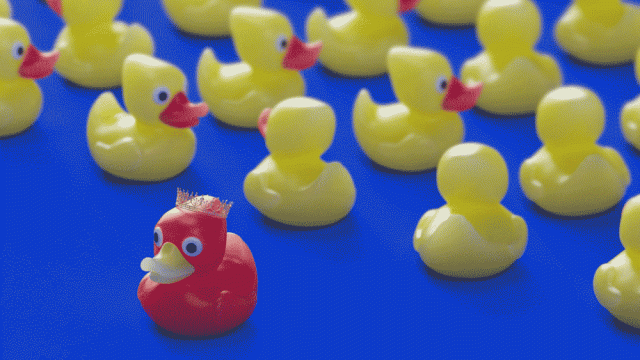
Stephanie Ojeda
The pharmaceutical industry and the medical device industry have unique ways of defining terms like deviation and nonconformance. Often, this leads to confusion about how events should be classified and managed.
This article explains the difference between a deviation and a nonconformance, and why…
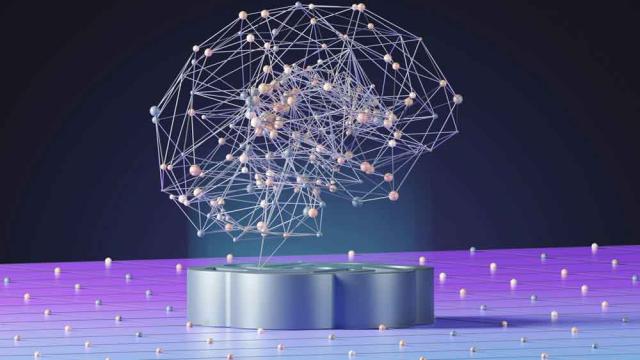
Quality Digest
If you’re a corporate employer, you must know the importance of training and its effects on your firm’s growth. Teaching employees with the help of corporate training is an essential step that every firm should follow to reach its goals. Additionally, incorporating OSHA training ensures workplace…
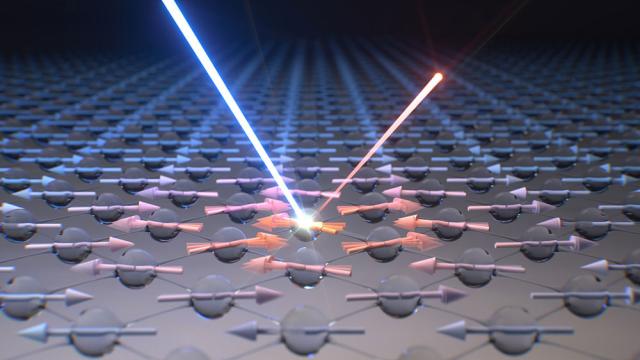
Brookhaven National Laboratory
Researchers use a technique called resonant inelastic X-ray scattering, or RIXS, to study the electronic behavior of quantum materials. The image above illustrates an ultrabright X-ray striking a quantum material’s electrons (gray circles) and scattering off the sample. In this example, the X-ray’s…
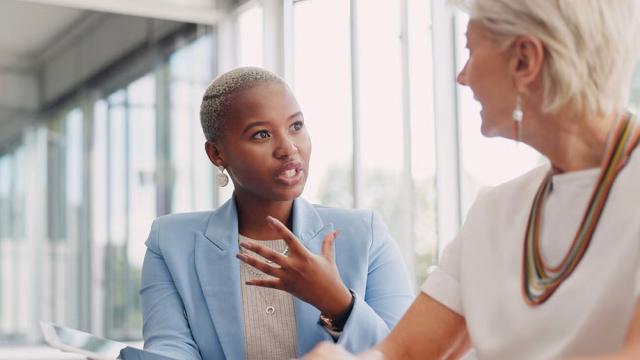
Seb Murray
What happens when workers get a say in evaluating their managers? At one Chinese carmaker, the results speak for themselves: happier teams, better leadership, and a noticeable boost in productivity—without a single downside. Those are key findings of a recent study by Wharton associate professor of…
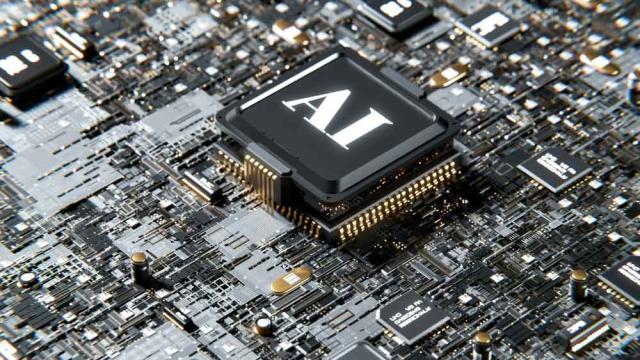
Akli Adjaoute
Keeping quality high in today’s fast-moving production world is a big challenge. Traditional quality checks have worked well, but they can be slow, require a lot of work, and are prone to mistakes.
AI could change this by making quality control faster, more accurate, and easier to scale. It could…
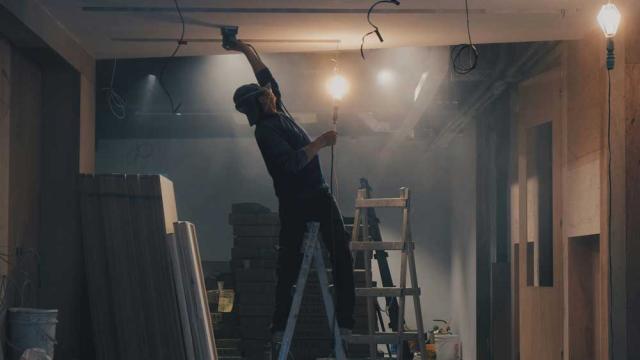
ISO
How do health and safety incidents affect your business? If a worker is injured or becomes ill, what kind of disruption does it cause? Is your productivity affected? What’s the effect on other workers in terms of workload or psychological health and well-being?
People are the foundation of every…