All Features
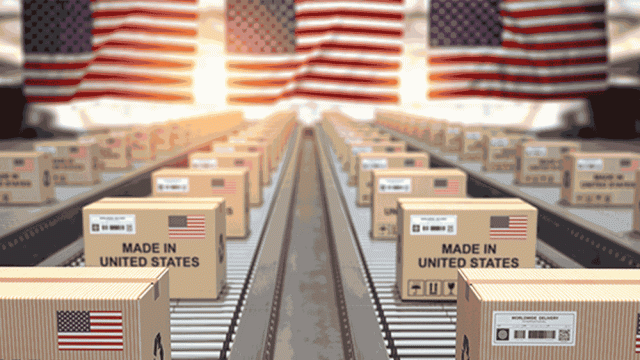
NIST
The U.S. manufacturing industry is evolving at a rapid pace, driven by new technologies, smarter supply chains, and an increasingly dynamic workforce. This year, small manufacturers will face a mix of opportunities and challenges as they navigate these changes. To stay competitive, small and medium…
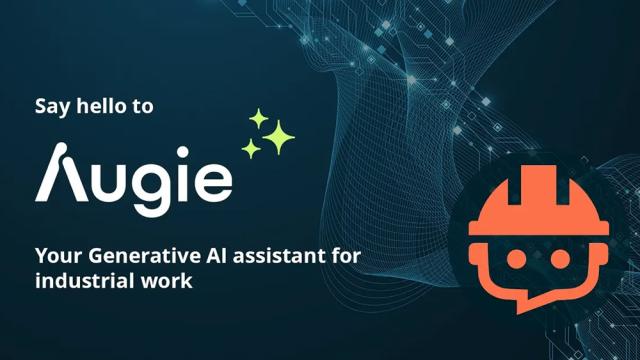
Quality Digest
Augie, Augmentir’s industrial generative AI assistant, is designed to enhance manufacturing operations. Unlike standard AI-powered helpers, Augie relies on real-time operational data, workforce insights, and training records to deliver solutions that integrate smoothly into daily workflows. It…
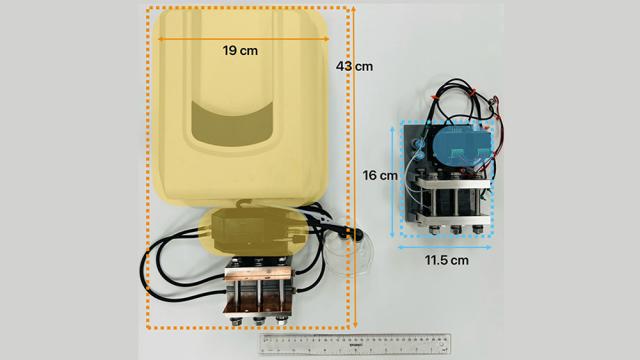
Karyn Hede
Sometimes, to go big you first have to go small. That’s what researchers at the U.S. Department of Energy’s Pacific Northwest National Laboratory have done with their latest innovation in energy storage.
With a goal of speeding up the time to discovery of new grid energy storage technology, the…
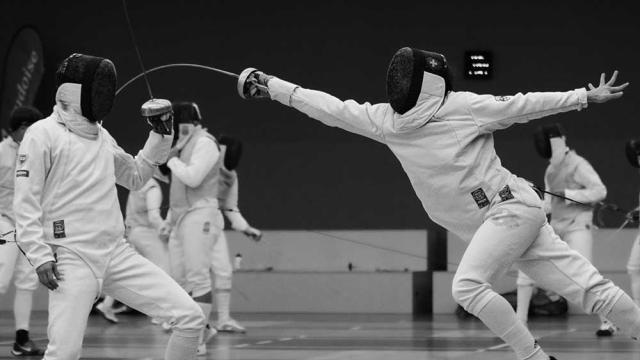
Mike Figliuolo
We all have enemies. Some of us have many. But when we spend our time and energy focused on attacking them and counterattacking their inevitable strikes, we’re the ones losing.
In getting us to attack, our enemy has taken us away from productive pursuits. They’ve hung a dark cloud over our days.…
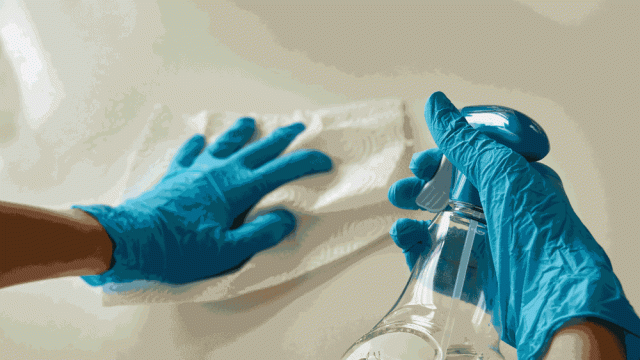
Saurabh Joshi Shripad
Established pharmaceutical facilities play a pivotal role in public health by ensuring the safety and efficacy of the medications they produce. This critical responsibility demands strict adherence to the Code of Federal Regulations, including 21 CFR 211.67—“Equipment cleaning and maintenance,”1,2…
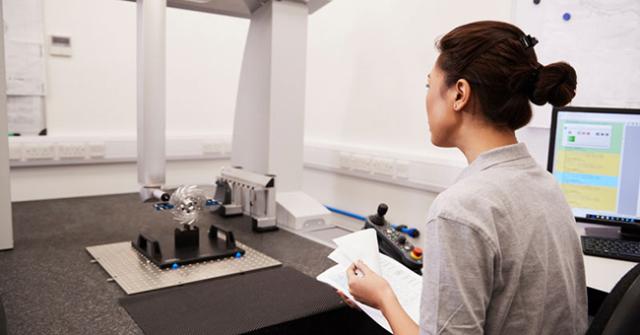
Creaform
Quality control (QC) teams need reliable results they can trust to make informed decisions and address manufacturing challenges. This is why they rely on the coordinate measuring machines (CMMs). However, a CMM’s speed is often a limitation, making the idea that routine quality control can be…
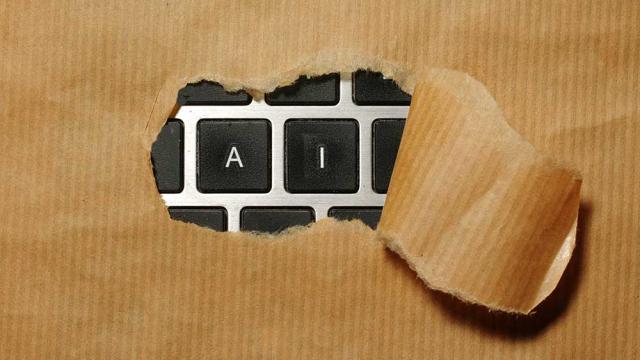
Gleb Tsipursky
The transformative potential of generative AI in learning and development (L&D) is a topic of growing interest among business leaders. And if you think your workers aren’t using gen AI, you might be seriously off-base.
According to a global study of 14,000 workers by Salesforce in late 2023,…
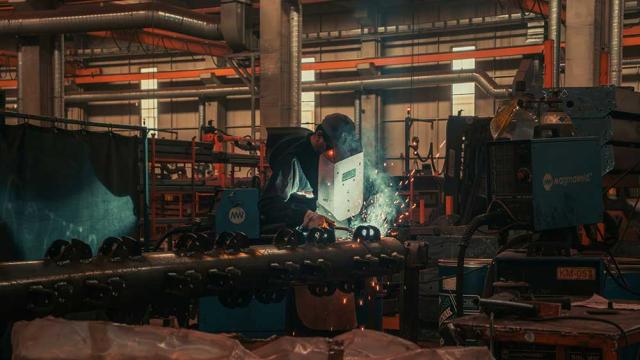
Nathan Ginty
In recent years, reshoring—the process of bringing manufacturing back to the U.S.—has gained momentum. Companies are reevaluating their offshore supply chains, driven by rising costs, geopolitical risks, and supply chain disruptions. For smaller manufacturers, this shift also presents a unique…
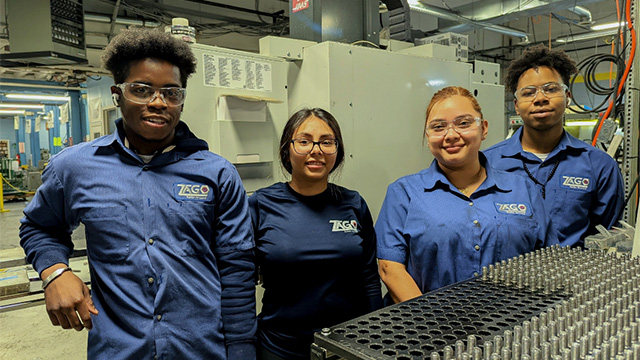
Roy VanGemert Jr.
What if you could meet your new employees a few years before their start date? Imagine a future where skilled workers are readily available in your local market, eager to contribute and connected to your company’s mission.
By investing in a sustainable local talent pipeline, manufacturers improve…
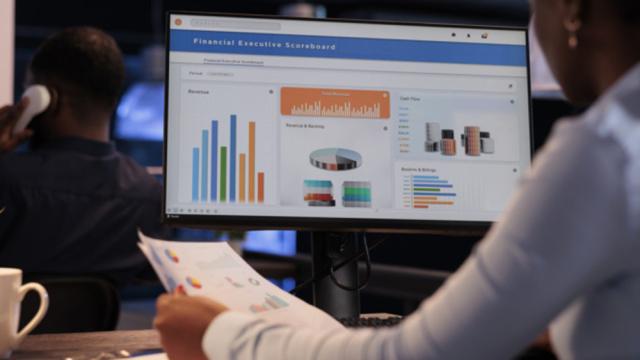
Hannah Fischer-Lauder
In an age where data are among the most valuable assets for any business, the ability to retrieve, process, and utilize information efficiently is critical for success. Yet traditional data-retrieval methods often struggle with the demands of today’s dynamic business environments. Enter retrieval-…
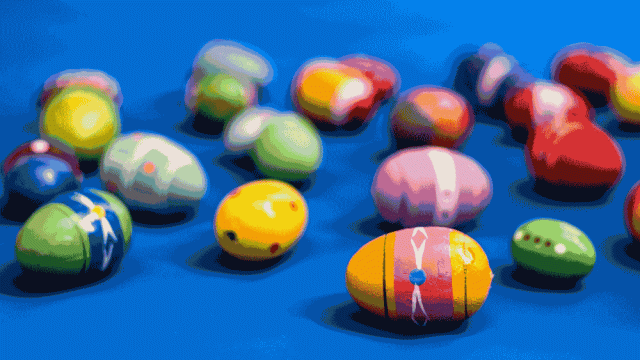
Susan Robertson
Every year, Amy B., a buyer for a large retail chain store, hosts an Easter egg decorating team-building party where she and a bunch of her suppliers spend an entire afternoon coloring and bedazzling boiled eggs. None of them bring kids—they do this for the sheer pleasure of out of the office…
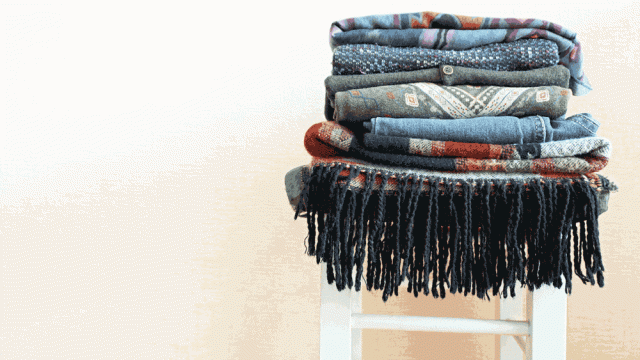
George Schuetz
Machinists working strictly in metalworking shops don’t have many occasions to gage the thickness of soft materials. But many of our readers work in supporting roles, helping to build or maintain the machines that produce textiles, plastic films, paper, and other products that are compressible.…
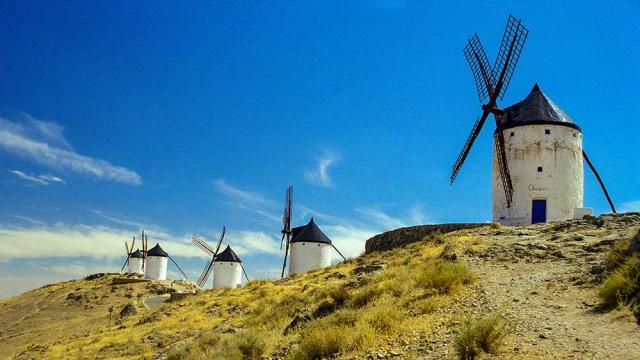
Donald J. Wheeler
The Man of La Mancha never got to the unreachable goal—and if you’re being judged by overall equipment effectiveness (OEE), then your manager may also be dreaming an impossible dream. This column will look at problems associated with the use of OEE values.
OEE is a value often used in lean…
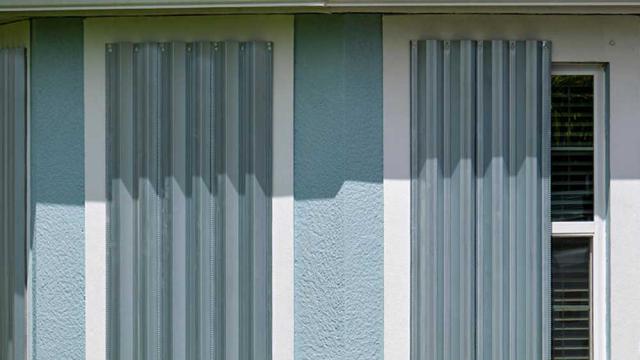
Harry Hertz
My story begins with Hurricane Milton, one of two tragic hurricanes to hit the west coast of Florida last year. Milton went right over Sarasota, where I live part of the year. It was a devastating storm; tree and plant debris still remain on the sides of many roads. Big root balls are still upended…
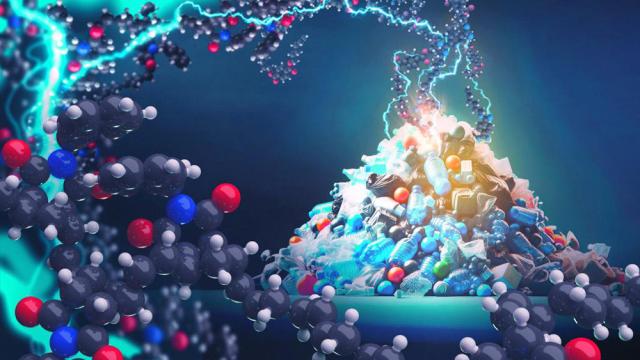
Oak Ridge National Laboratory
By editing the polymers of discarded plastics, chemists at the U.S. Department of Energy’s Oak Ridge National Laboratory (ORNL) have found a way to generate new macromolecules with more valuable properties than those of the starting material. Upcycling may help remedy the roughly 450 million tons…
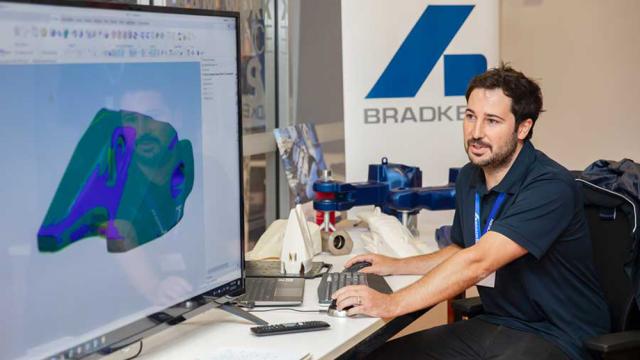
Creaform
Maintaining high-quality standards is critical in the heavy equipment industry. Customers rely on manufacturers to deliver products that perform reliably in harsh and demanding operating conditions. The stakes are high. Deviation from quality and overlooked detail can lead to expensive warranty…
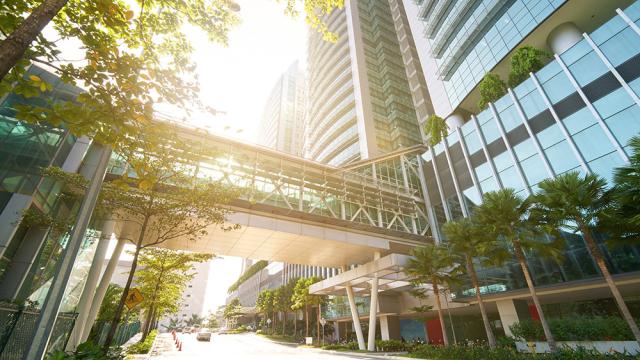
Ben Eidlisz
A safe work environment will foster productivity, reduce hazards, and enhance overall work morale. Keeping your team and assets safe requires implementing the right policies, medical necessities, vigilant oversight, ongoing assessments, and proper training.
As the COO of DUSAW, making smart locks…
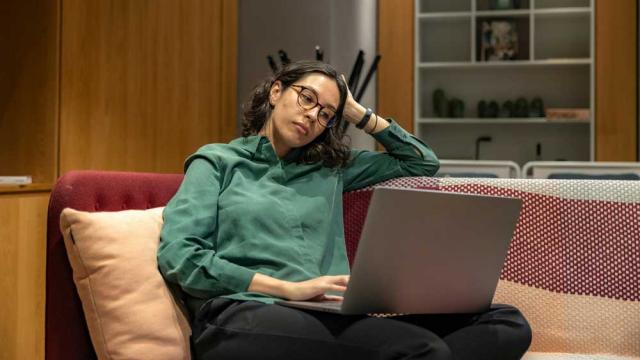
Gleb Tsipursky
New research provides a compelling analysis of the repercussions of return-to-office (RTO) policies on employee turnover, hiring, and the overall talent pool within major corporations. Using data from more than 3 million LinkedIn profiles, Mark Ma, at the University of Pittsburgh, along with other…
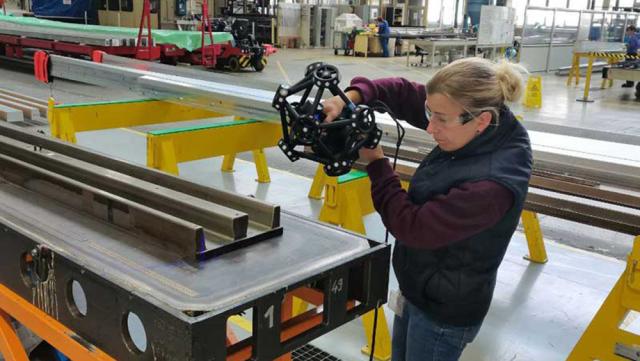
Creaform
GKN Aerospace Deutschland is a global tier-one supplier of airframe and engine structures, landing gear, electrical interconnection systems, transparencies, and aftermarket services.
The company has more than 38 manufacturing locations in 12 countries and 17,000 employees worldwide. It…
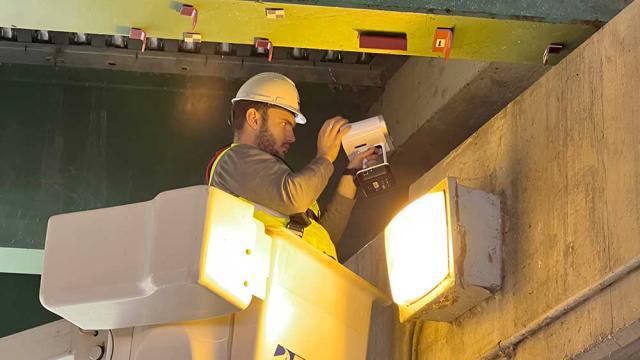
Sergey Sukhovey
The collapse of Baltimore’s Francis Scott Key Bridge in March 2024 was the consequence of a long-standing problem: the fragility of aging infrastructure. As reconstruction gets underway on an estimated four-year timeline, the disaster reflects the urgent need for better bridge inspection nationwide…
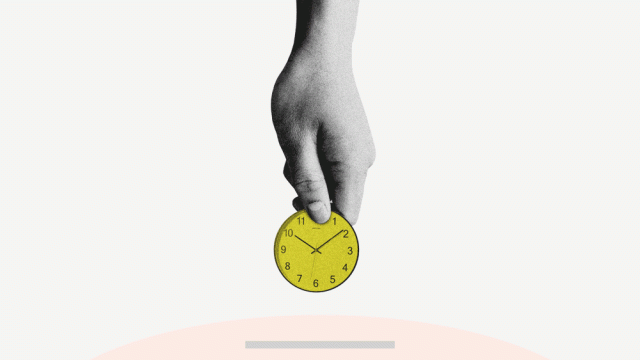
Nick Haase
PharmaNZ is a family-owned nutraceutical company that manufactures health supplements for the world’s leading brands. The company produces more than 250 tonnes of powder-blend products, 10 million tablets, and 70 million hard-shell capsules annually for clients worldwide. The company, founded by…
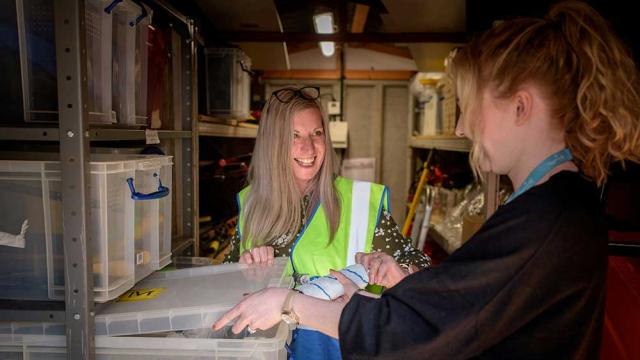
Adam Grabowski
Cash is king for manufacturers, from the owner down to the machine operators. If you visit any manufacturer, you’ll see that most have a keen eye on how everything is being used. Machines are generally only running if they are making parts; employees are typically only working if orders are coming…
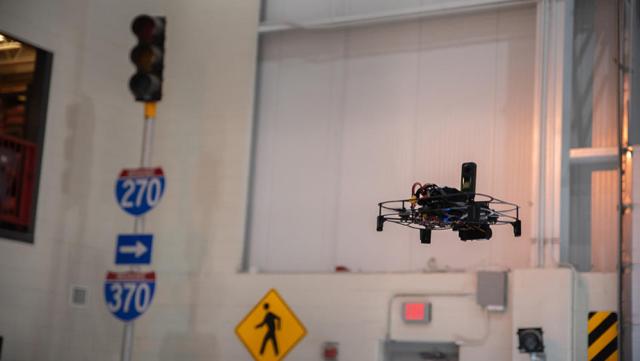
Megan King
When first responders need to rescue people from an earthquake-ravaged home, they need real-time information. If law enforcement officers are looking for a shooter in a crowded building, they must learn everything they can about the scene.
Emergency responders need to know where people are and…
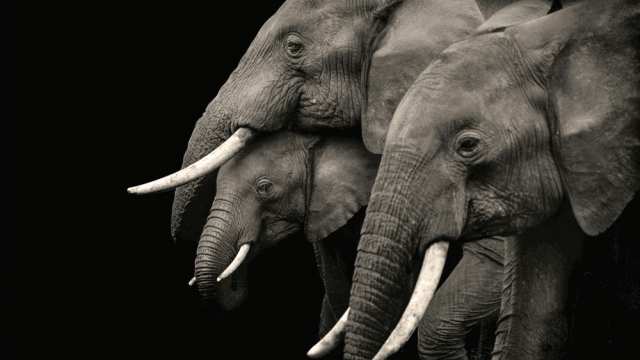
Jones Loflin
I had just finished a keynote presentation and was at the book table set up by the client. Participants were invited to pick up one or more of my books, and the company would pay for them.
One excited audience member quickly made their way to the table and was perusing their possible choices. They…
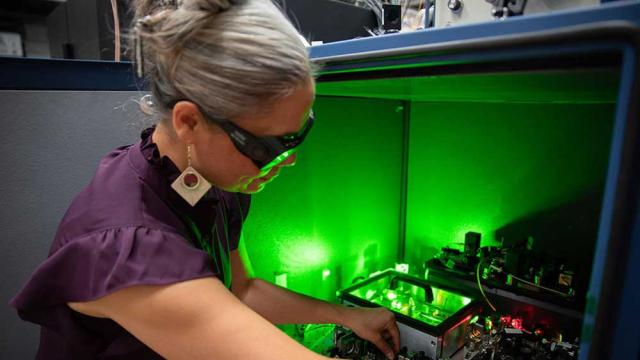
Tara Fortier
If you’ve heard or read about quantum mechanics, you may have seen it described as “weird.” Even the great Albert Einstein—one of the founders of quantum mechanics—called certain aspects of the theory “spooky.”
With its wave-like particles and particle-like waves, quantum mechanics certainly…