All Features
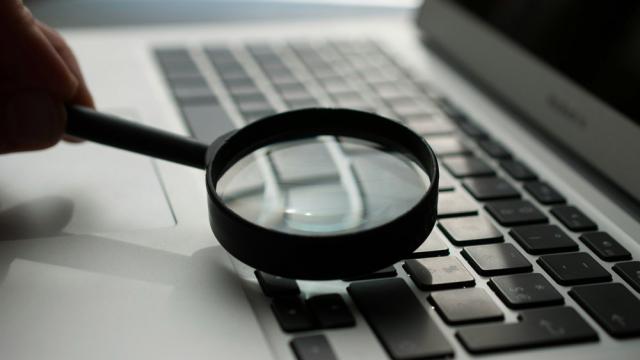
Ayush Soni
Audits and inspections are critical components of industrial safety management. These processes help organizations ensure compliance with legal requirements, identify risks, and improve workplace safety and operational efficiencies. Conducting regular audits and inspections is not just a regulatory…
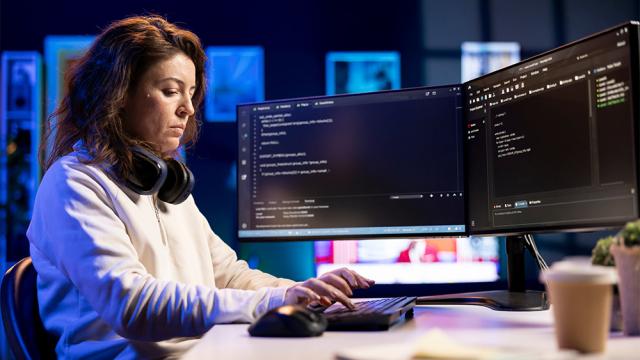
Ilana J. Sprongl
Back in 2023, only 15% of businesses had adopted AI-augmented software testing tools. By 2027, that number is expected to leap to 80%. The reason behind this rapid adoption is clear. The complexity of modern software and products is skyrocketing, and with it, the risks associated with quality…
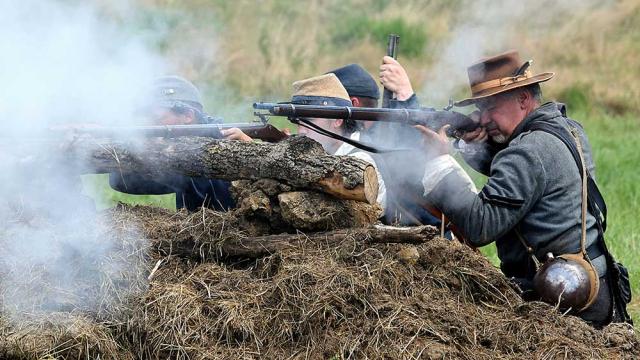
Akhilesh Gulati
In the world of operations and quality management, the pressure to act quickly can feel overwhelming. Senior executives are constantly racing against time to meet customer demands, solve problems, and keep shareholders satisfied. In the rush to address immediate challenges, “Ready, aim, fire!” gets…
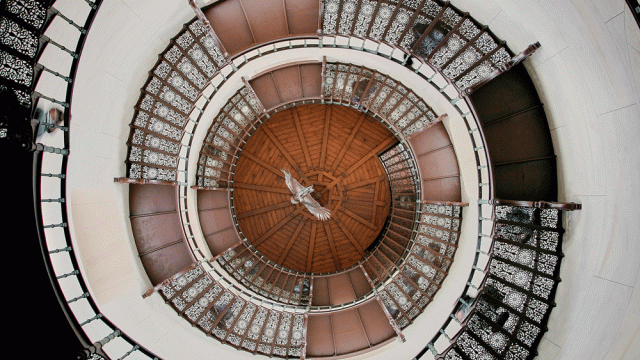
Harish Jose
In this article, I’m exploring complexity through the lens of George Spencer-Brown’s Laws of Form (Cognizer Co., 1994). This philosophical and mathematical treatise explores the foundations of logic and mathematics via a unique symbolic system. Spencer-Brown introduces a primary algebra based on a…
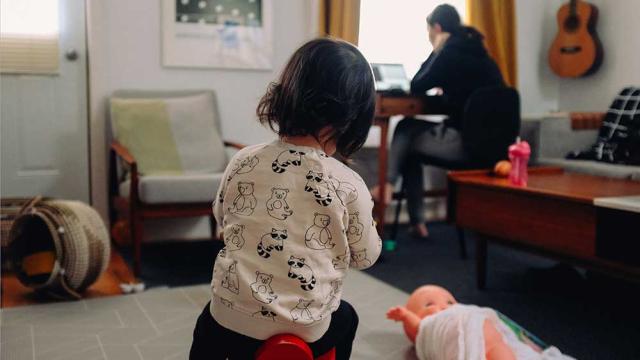
Gleb Tsipursky
In the rapidly evolving business landscape, the momentum toward policies mandating a return to the office (RTO) is gaining traction. However, this shift risks overlooking critical segments of the workforce, particularly older employees, individuals with disabilities, and women, whose participation…
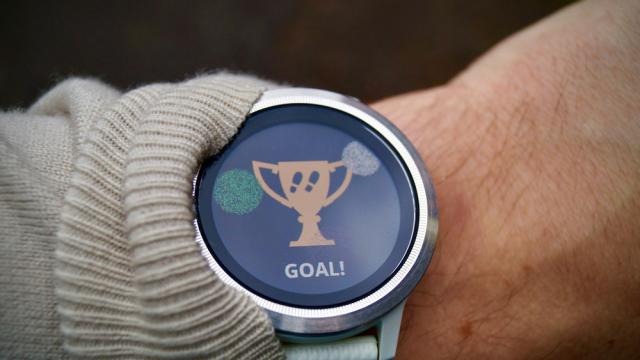
Laurie Locascio
So much has changed since I walked onto the Gaithersburg, Maryland, campus of the National Institute of Standards and Technology (NIST) almost three years ago to begin my term as its director and U.S. Commerce Undersecretary for Standards and Technology.
We were all still feeling the impacts of…
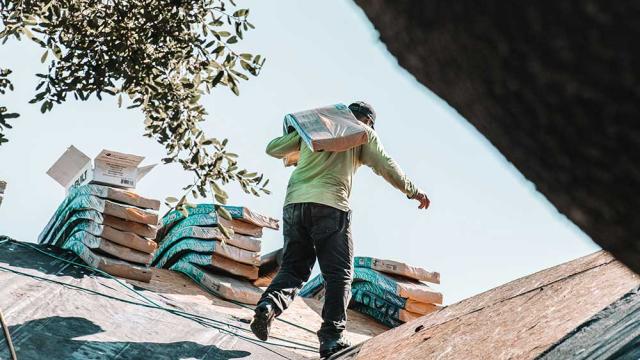
William A. Levinson
Recent labor relations controversies and ongoing arguments about the minimum wage have raised questions as to how a supply chain should share the utility it produces.
If we ask the wrong question, however, we’ll get the wrong answer. “What is a fair share?” asks how a supply chain should divide a…
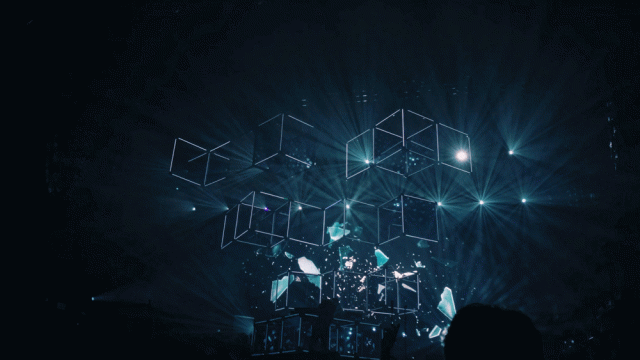
Malcolm Chisholm
Data are the fuel of the Information Age, and all organizations acknowledge the value of well-managed corporate data assets. The problems start when we begin to ask just exactly how the data assets are to be well managed.
In response, many organizations have put data governance departments in…
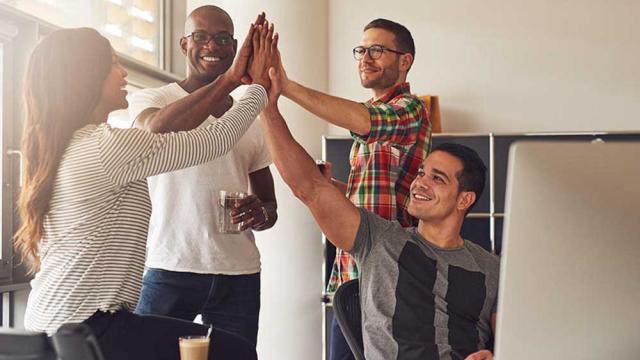
Harry Hertz
A recent Inc.com blog post by Jessica Stillman discusses Malcolm Gladwell’s new book, Revenge of the Tipping Point (Little, Brown and Co., 2024). The theme in both works is that you can’t create a high-performing team simply by bringing together individual high performers. They need to gel as a…
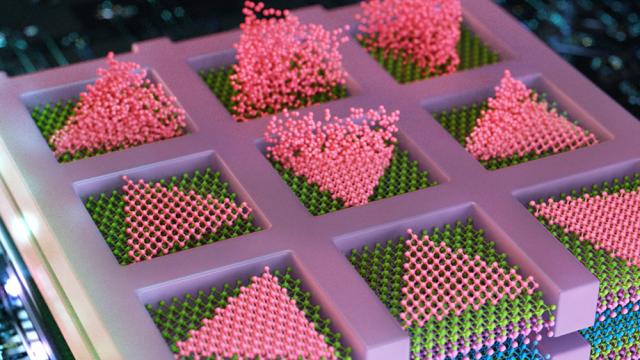
Jennifer Chu
The electronics industry is approaching a limit to the number of transistors that can be packed onto the surface of a computer chip. So chip manufacturers are looking to build up, rather than out.
Instead of squeezing ever-smaller transistors onto a single surface, the industry is aiming to stack…
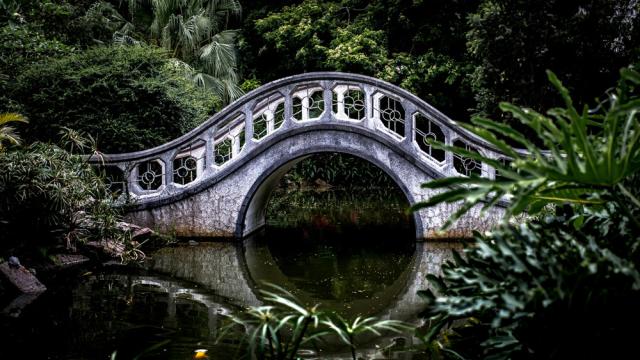
Nick Haase
In the evolving landscape of industrial digital transformation, the unified namespace (UNS) has emerged as a transformative approach to enterprise data management. At its core, UNS provides a single source of truth that eliminates barriers between disparate systems and data sources, enabling any…
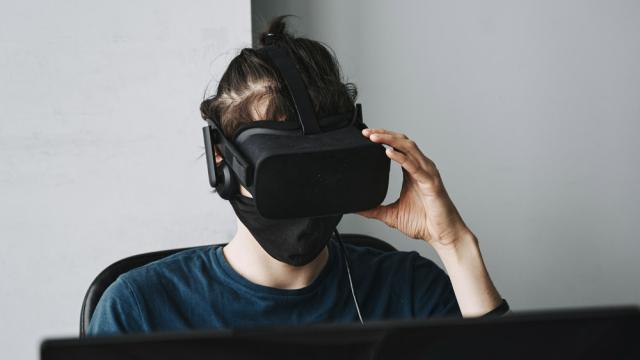
Peter Zemsky, Ricky Wong
Gemini, O1, Grok, Claude, Llama, Yi, and Mistral: The number of large language models (LLMs) seems to have grown exponentially since OpenAI’s ChatGPT burst into the public consciousness in late 2022. It’s estimated that $154 billion was spent on AI by businesses in 2023, while the most recent …
Quality Digest
(Deloitte: London) -- Deloitte’s annual “Tech Trends” report details six AI-fueled trends shaping business operations, growth, and transformation.
Key takeaways
AI is everywhere. From the server room to the boardroom, artificial intelligence is becoming foundational to enterprise IT, and an…
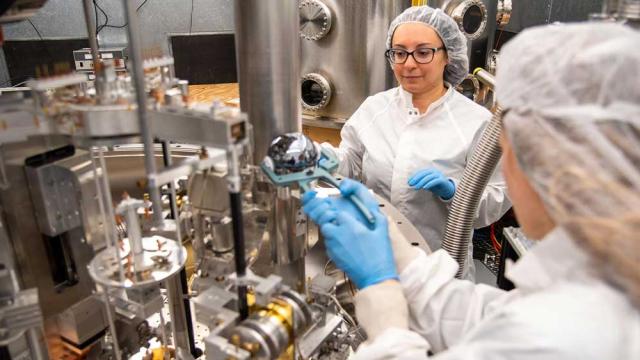
Ben P. Stein
NIST is unique as the national measurement science institute. We are the U.S. agency responsible for maintaining measurement standards, from the second to the kilogram.
We help ensure that these units of measure are consistent across our watches and our grocery scales. But this isn’t as…
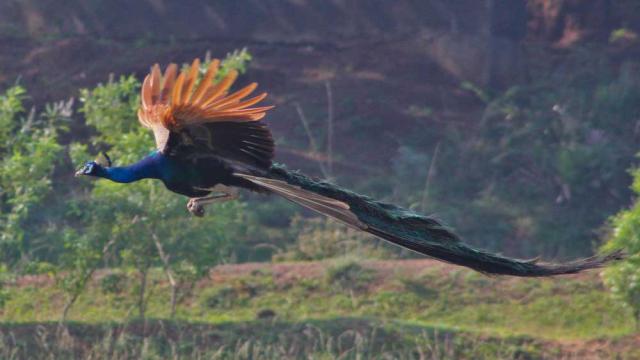
Donald J. Wheeler
When Sir Ronald Fisher created the analysis of variance (ANOVA) in the 1920s, he extended the two-sample t-test to allow the comparison of k sample averages. During the same time period, Dr. Walter Shewhart was creating the process behavior chart. So it should be no surprise that both techniques…
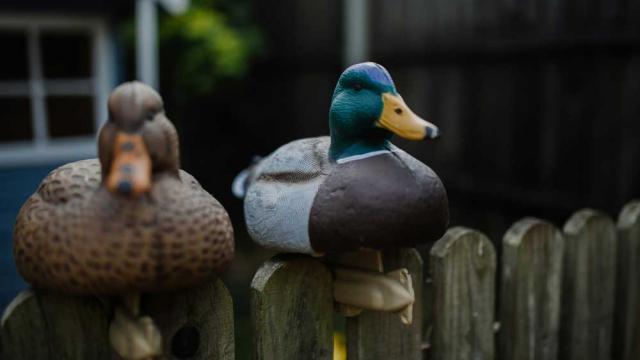
Mike Figliuolo
Every day there’s a new pile of “experts” cropping up on every subject imaginable. The key to differentiating genuine experts from frauds is to ask the right questions.
Warning: This post is a bit of a rant (but it does have a story and some practical advice). How many new experts are there today…
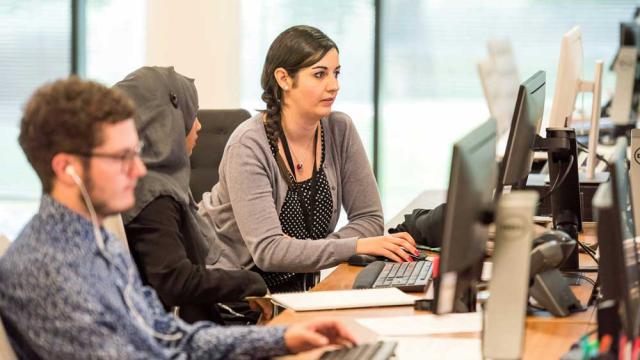
Gleb Tsipursky
In today’s rapidly changing business environment, a subtle yet profound shift is taking place in office dynamics, particularly as we welcome back teams that have been dispersed by the necessity of remote work.
Managers find themselves at the helm of this transformation, charged with the critical…

Angie Basiouny
Hospital patients rate their pain on a scale of 1–10. Teachers grade on a curve. Sports fans spend hours debating stats on their favorite teams. Even the most ardent language lover can’t deny the power of numbers to convey information, especially when choices need to be made.
A new study from…
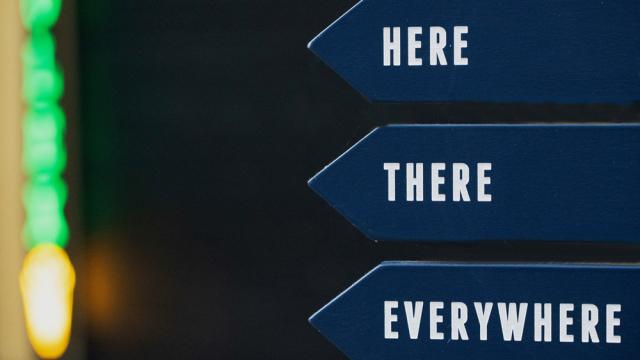
Prashant Kondle
Unplanned equipment downtime costs manufacturers an estimated $50 billion annually, according to a study by Deloitte. It is estimated that unplanned downtime costs more than $100,000 per hour. Traditional maintenance approaches—whether reactive or scheduled—are not sufficient to address these…
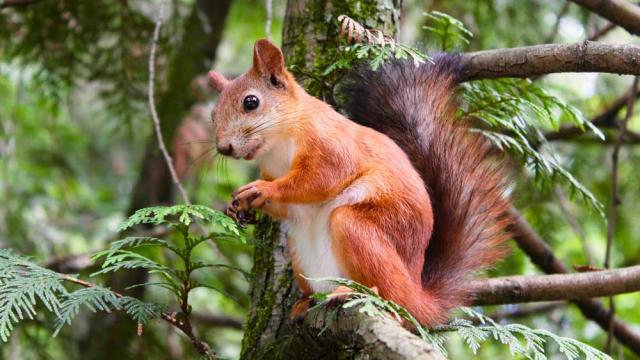
Mike Figliuolo
When it comes to networking, are you a squirrel or a grasshopper? From what I can tell, there are loads of grasshoppers out there but very few squirrels.
You folks know that fable about the squirrel and the grasshopper, right?
The squirrel works his butt off all summer fortifying his little tree…
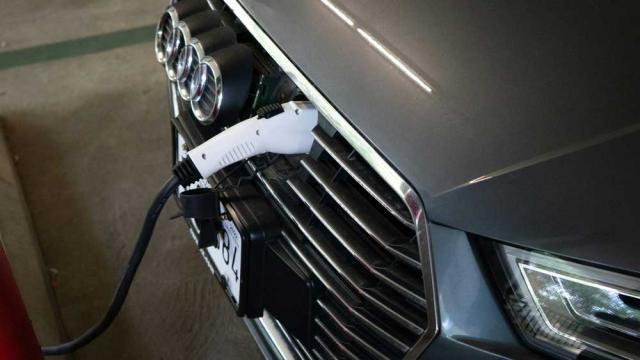
AMETEK
From electric vehicles (EVs) to renewable energy storage to consumer electronics, lithium-ion batteries are powering the world around us. Over the next decade, the market for these batteries is expected to grow more than five times from what it is today.
Rugged field testing meets real-time…
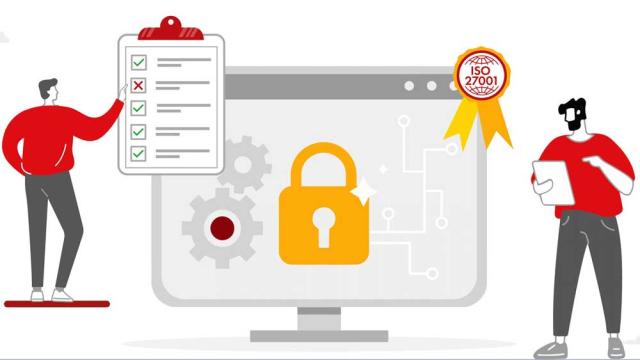
4C Consulting
ISO 27001 is a globally recognized standard for establishing, implementing, maintaining, and improving an information security management system (ISMS). Successfully implementing ISO 27001 can provide tremendous benefits, such as ensuring data security, building trust with customers, and meeting…
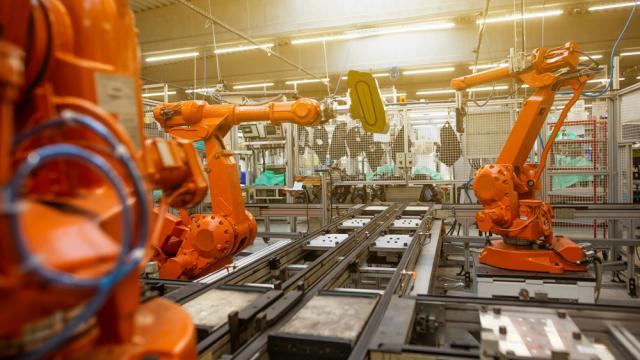
Herman Tang
In manufacturing, especially in assembly systems, every operation plays a role in shaping the quality of the final product. The influence of these operations can carry through each stage, ultimately affecting the quality of the finished products delivered to customers. Understanding how these…
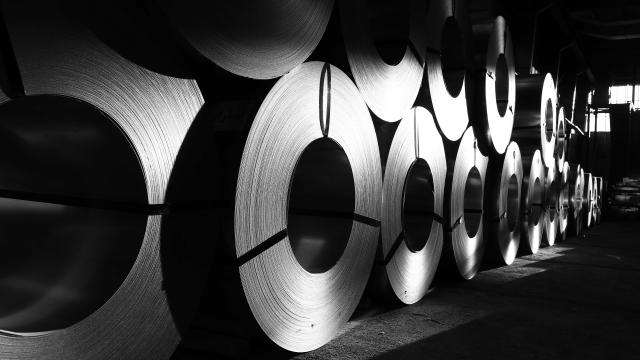
Silas Fulsom
In today’s highly competitive global markets, lean manufacturing is no longer something that’s nice to have—it’s a way of life. You can either reduce costs, simplify operations, and improve productivity on a continual basis—or you can lose business to competitors that do.
Lean manufacturing starts…
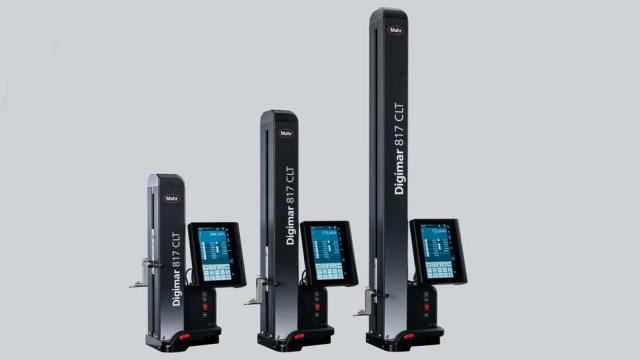
George Schuetz
The need for long-range height measurements has been around since the principles of layout work became a fundamental requirement in machine shops.
The first step in the manufacturing process is to lay out a piece by transferring a design or pattern to a workpiece. This is performed in almost all…