All Features
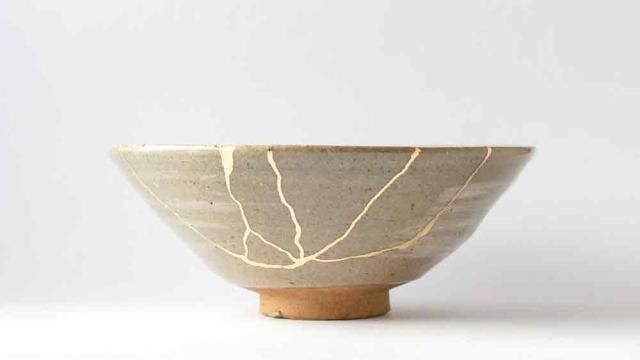
Akhilesh Gulati
In today’s competitive manufacturing landscape, resilience is the new quality. And one of the most powerful lessons in resilience doesn’t come from a factory—it comes from an art form.
In the Japanese tradition of kintsugi, a broken ceramic bowl is not discarded or disguised. It’s repaired—…
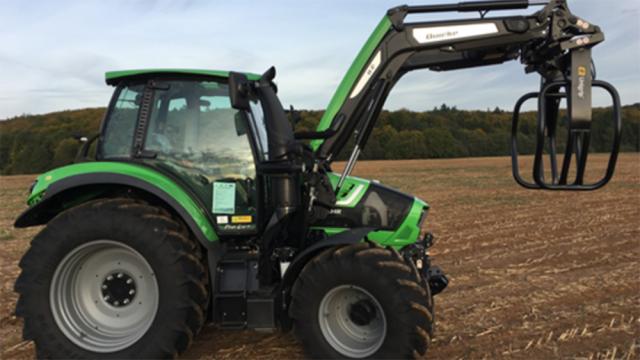
Creaform
Ålö Agricultural Machinery (Ningbo) Co. Ltd., a wholly owned subsidiary of Ålö, is a leading manufacturer of loaders and implements for agricultural tractors.
With production facilities in four countries, and customers in more than 50, Ålö holds approximately 30% of the world market for tractor…
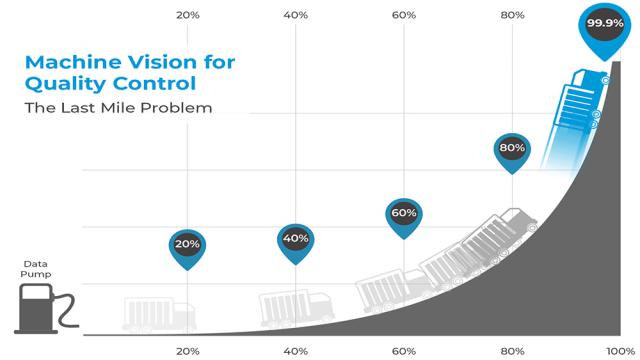
Wilhelm Klein
In 2025, sustainability is no longer optional—it’s a strategic imperative. Manufacturers, responsible for nearly 40% of global material waste, face rising demands to reduce emissions, cut waste, improve product consistency, and enhance efficiency.
Artificial intelligence (AI) is central to this…
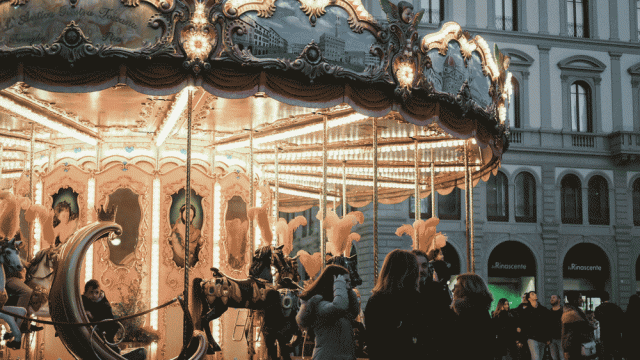
Kate Zabriskie
You know that friend who’s always there when you’re in need? The one who shows up on time, follows through on promises, and genuinely cares about what’s going on in your life? That’s exactly what your business needs to be for your customers.
Sure, those splashy marketing campaigns and point-…
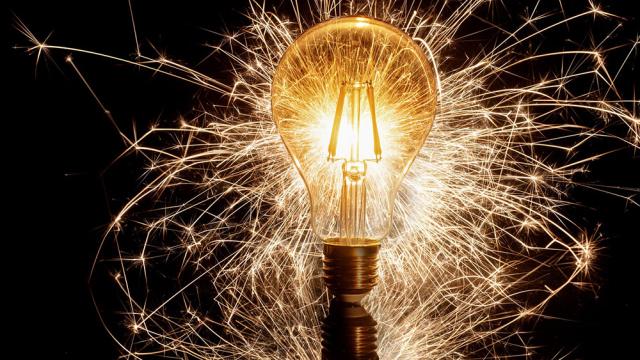
Cornelia C. Walther
Artificial intelligence’s relentless march has sparked excitement and apprehension across the business landscape. Although early narratives often pitted human intellect against the burgeoning capabilities of machines, a more nuanced and powerful reality is emerging: the era of hybrid intelligence.…
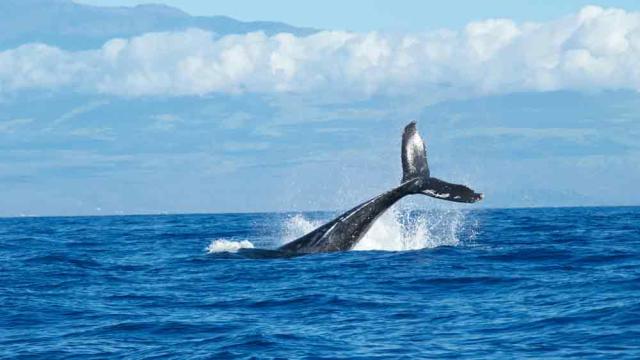
Mike Figliuolo
You can’t get big without thinking big right from the start. As an entrepreneur starting a business, it’s easy to see yourself as “the little guy.” If you do, you’ll forever stay the little guy.
Too many times I’ve seen entrepreneurs name their companies after themselves (e.g., Tom Jones, LLC).…
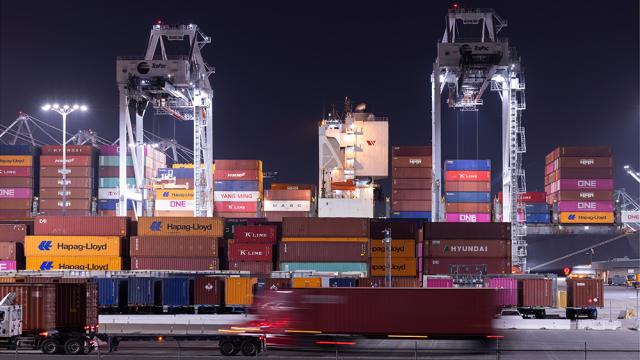
Sunderesh Heragu
According to the U.S. Census Bureau and the U.S. Bureau of Economic Analysis, trade with our three largest partners—Canada, China, and Mexico—accounted for more than $1.32 trillion in imports and $0.82 trillion in exports in calendar year 2024. This represented 40% of the total trade between the…
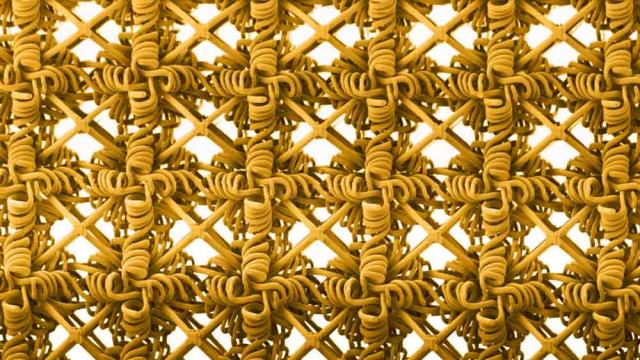
Jennifer Chu
In metamaterials design, the name of the game has long been “stronger is better.”
Metamaterials are synthetic materials with microscopic structures that give the overall material exceptional properties. A huge focus has been in designing metamaterials that are stronger and stiffer than their…
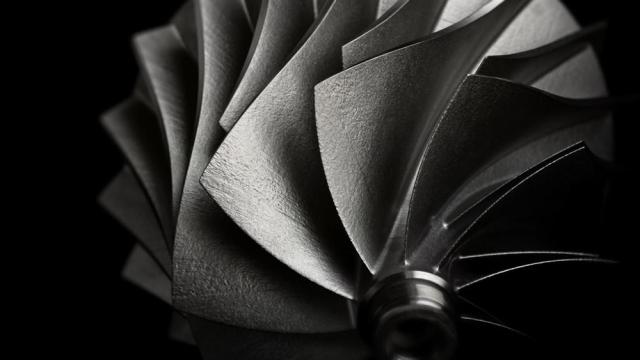
Oak Ridge National Laboratory
When Jonaaron Jones started his master’s degree at the University of Tennessee-Knoxville (UT), his mentor invited him to visit the Manufacturing Demonstration Facility, or MDF, at Oak Ridge National Laboratory (ORNL). “I saw a metal 3D-printed part for the first time,” says Jones. “I knew I was…
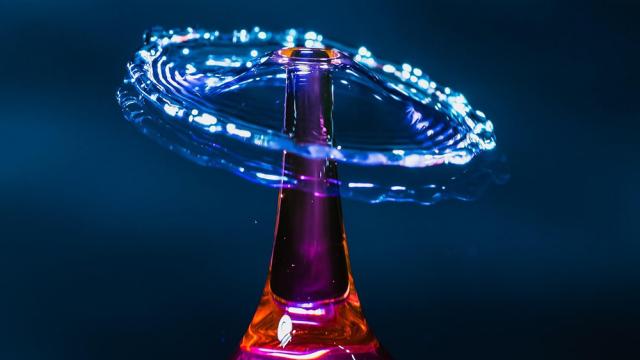
Georgia Institute of Technology
What’s the hottest thing in electronics and high-performance computing? In a word, it’s “cool.”
To be more precise, it’s a liquid cooling system developed at Georgia Tech for electronics and aimed at solving a long-standing problem: overheating.
Developed by Daniel Lorenzini, a 2019 Tech graduate…
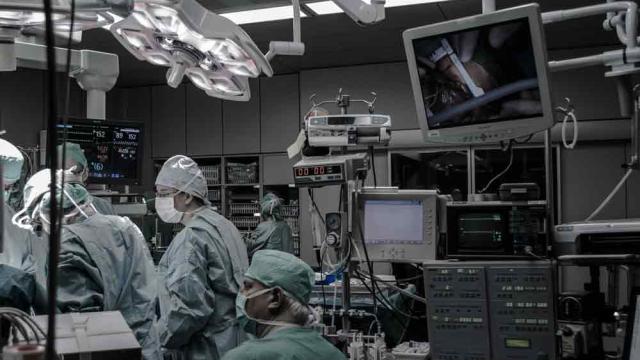
Matt McFarlane
One of the key findings in Greenlight Guru’s 2025 Medical Device Industry Report was that economic uncertainty is playing a large role in the decisions medical device companies make this year.
The report surveyed more than 500 medical device professionals across quality, regulatory, product…
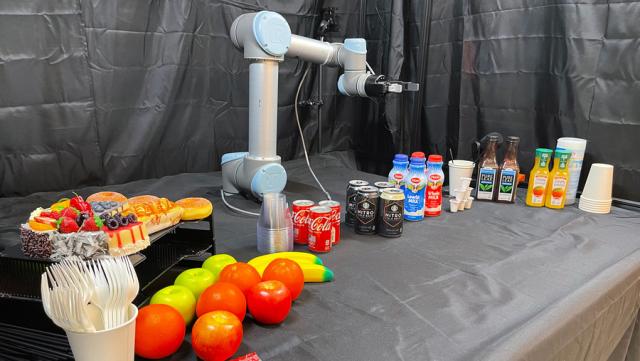
Jennifer Chu
For a robot, the real world is a lot to take in. Making sense of every data point in a scene can take a huge amount of computational effort and time. Using that information to then decide how to best help a human is an even thornier exercise.
Now, MIT roboticists have a way to cut through the data…
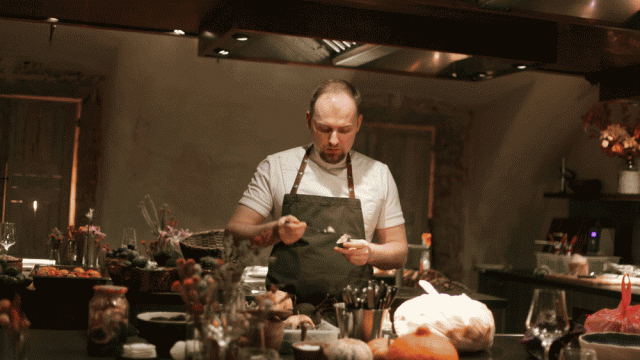
Jones Loflin
In a professional kitchen, no chef prepares a steak, a cake, and a casserole simultaneously with all the ingredients scattered across the counter. There’s a method: one recipe at a time, with only the ingredients needed for that specific dish.
The same principle applies to how we work, especially…
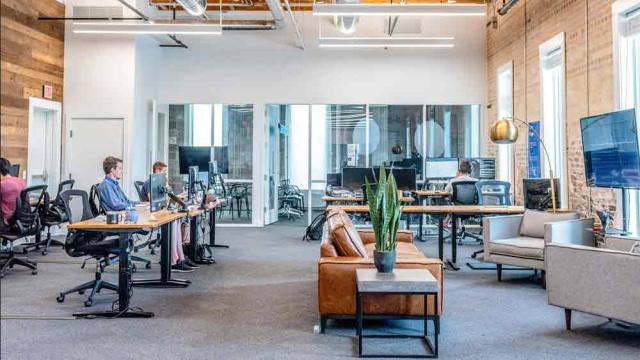
Bruce Hamilton
A few months ago I visited a potential customer, a high-tech startup, which like many Boston-area tech companies is developing astounding products that would have been considered science fiction only 10 years ago. The parking lot was half full at 8 a.m., but the entrance was locked to visitors, and…
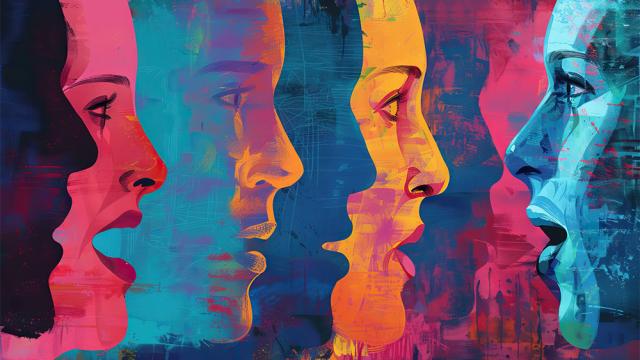
Chris Chuang
As a technology leader, I must admit that making the right investment in new innovations has its challenges. It’s easy to get caught up in the grandiose potential solutions offer, become overwhelmed by the setup, and struggle with employee adoption.
For the last decade, I’ve worked with human-…
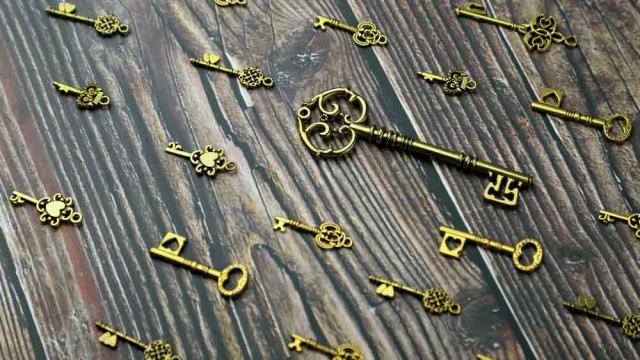
Stephanie Ojeda
Every day, quality leaders face a variety of production and process issues. Although some problems are easy to fix, others require deeper investigation, such as using a 5 Whys analysis or fishbone diagram. But then there are the stubborn, recurring issues that can lead to quality issues, increased…
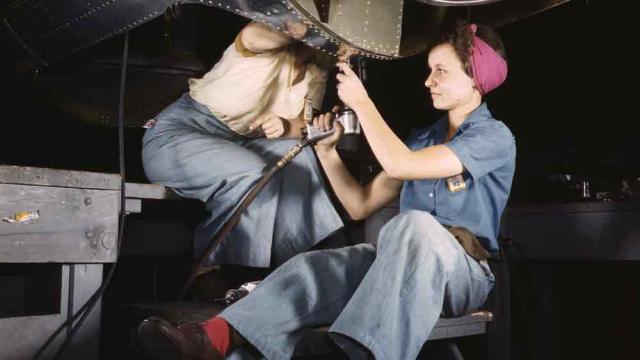
William A. Levinson
The Chinese character for crisis means “danger” and “opportunity,” and tariffs have created a supply chain crisis throughout the United States. Paul Roberts of the Seattle Times reports that fewer ships are arriving in Seattle: “Fewer ships coming into the U.S. means companies can’t get components…
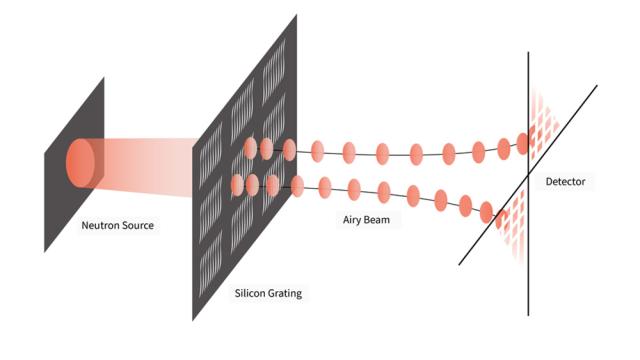
NIST
In a physics first, a team including scientists from the National Institute of Standards and Technology (NIST) has created a way to make beams of neutrons travel in curves. These Airy beams (named for English scientist George Airy), which the team created using a custom-built device, could enhance…
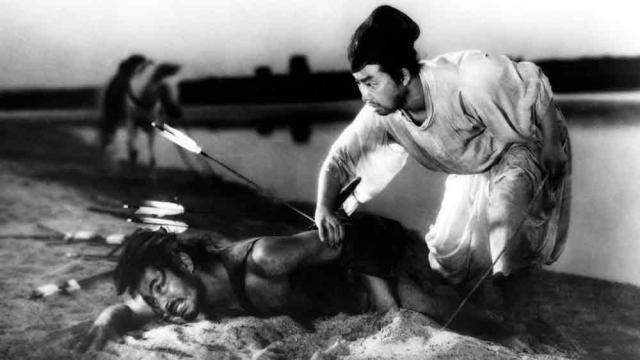
Akhilesh Gulati
When we step into a complex organization—whether in manufacturing, healthcare, or finance—we often find ourselves navigating a sea of competing truths. Everyone seems certain they see the problem clearly. Yet somehow, solving it feels harder than it should.
Why?
Often, it’s not the facts that…
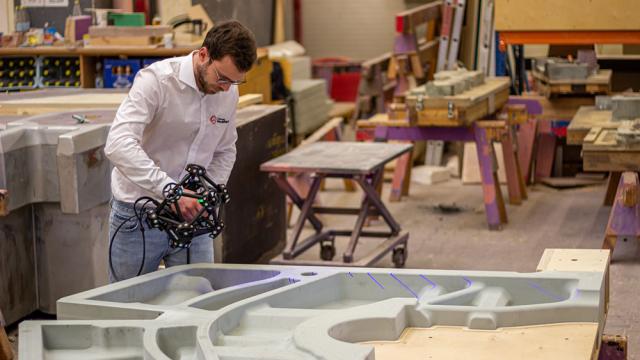
Creaform
In the casting industry, efficiency is key to producing high-quality parts while minimizing rework. Comprehensive data play a vital role in optimizing each manufacturing step. Traditionally, foundries have relied on conventional inspection techniques to ensure dimensional measurement. But the…
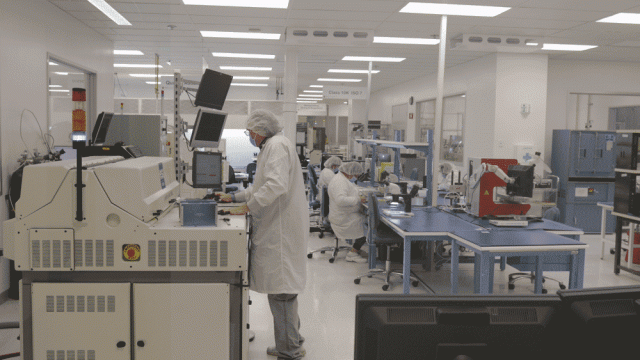
Annette Aquino
To meet the precise requirements associated with semiconductor manufacturing, integrated circuit (IC) packaging and assembly providers must navigate complex quality certification processes, such as those for the well-known ISO 9001 and ISO 13485 standards. Another important certification for…
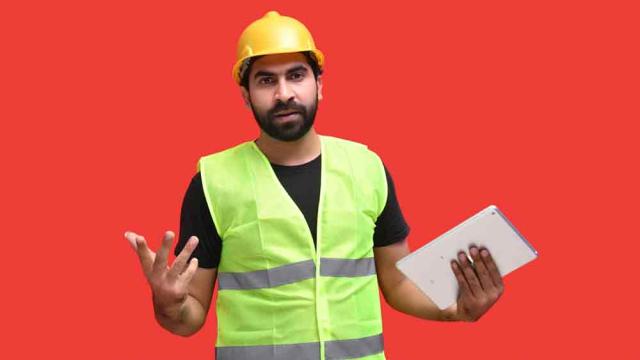
ISO
Occupational health and safety (OHS) is often brushed aside as a checkbox exercise—something assigned to compliance officers or forgotten in day-to-day operations. But this mindset comes at a cost. Every year, millions of people suffer injuries, illnesses, or worse, simply because their workplace…
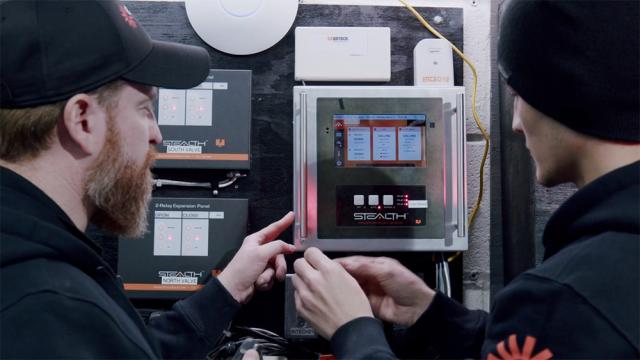
Simon Soloff
Boiler systems are a critical element of many manufacturing plants because they serve as a reliable source of heat and steam to power various processes. In today’s production environment, energy efficiency has become a crucial factor for manufacturing facilities aiming to reduce operational costs.…
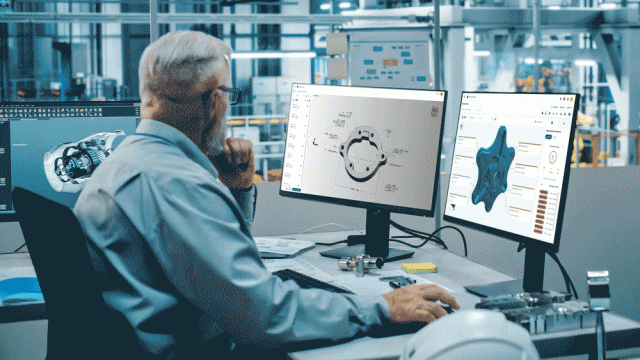
Stephen Graham, Quality Digest
Uploading something “to the cloud” has become common enough that most people are acutely aware of the storage advantages of cloud services—whether in their personal or professional lives—as well as how they might benefit administrators in any business. What might surprise people is the additional…
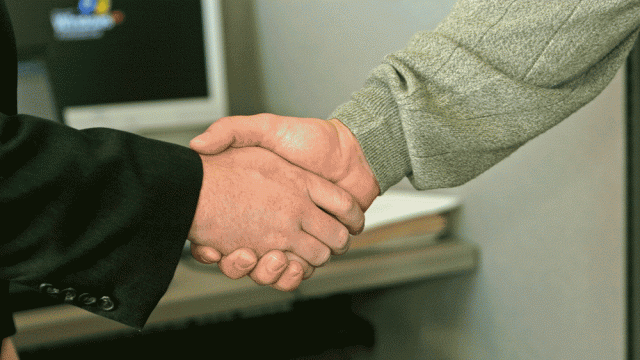
Quality Digest, David Mihal
What happens when a powerhouse company like Hexagon joins forces with an elite innovator like Geomagic Software? Well, here’s a hint: There’s magic right there in the name. Now that talk of acquisition has became reality, Quality Digest is here with more details on what to expect as the two…