All Features
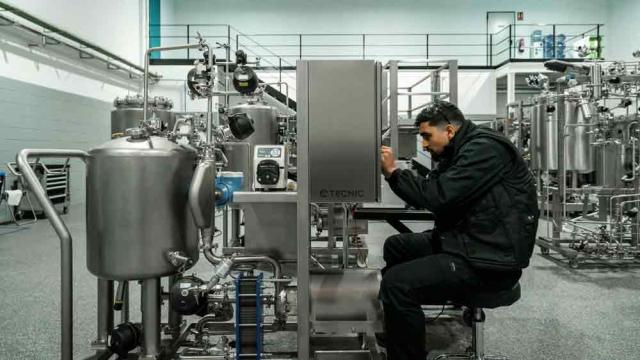
Bryan Christiansen
The cornerstone of efficient industrial and facility management, maintenance, repair, and operations (MRO) cover all activities related to equipment maintenance, procurement, upkeep, and inventory management. This includes spare parts, consumables, lubricants, cleaning supplies, safety equipment,…
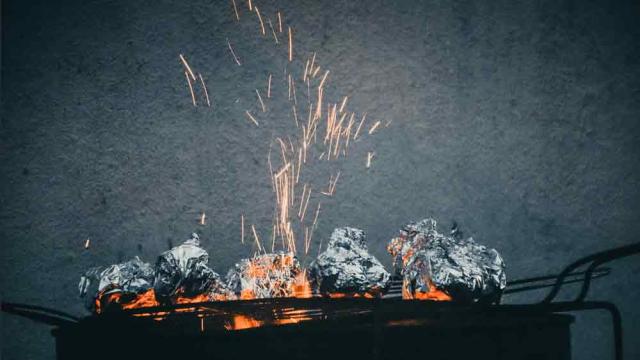
Donald J. Wheeler
For many hundreds of years, “If it ain’t broke, don’t fix it” has summarized the predominant approach to process operation. From the physician’s admonition to do no harm, to the slightly more positive aphorism that the squeaky wheel gets the grease, there is a common theme of differentiating…
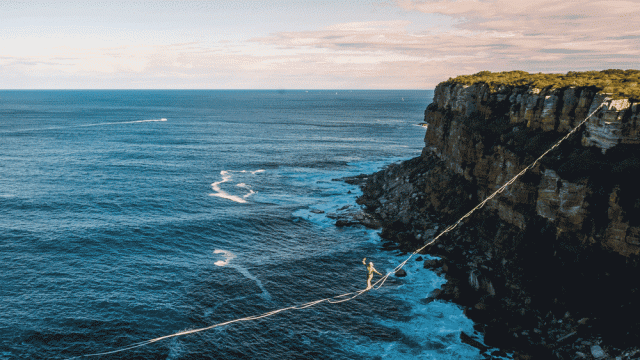
Harish Jose
I am a longtime admirer of George Spencer-Brown’s “Laws of Form.” In this article, I explore how his notion of reentry helps illuminate the paradoxes and blind spots in modern ideologies, especially the rise of xenophobia and extreme nationalism. These rigid ideologies depend on distinctions…
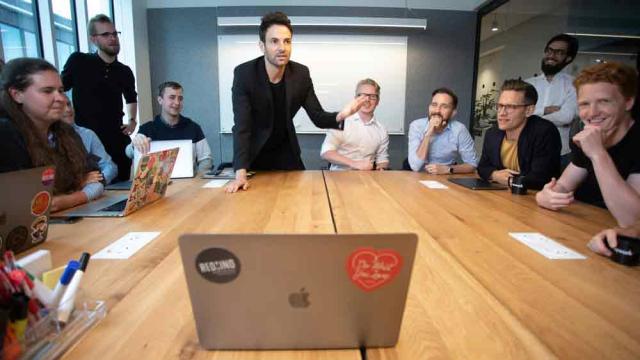
Mike Figliuolo
There’s an old army saying, “No plan survives first contact with the enemy.”
I’m sure some Navy or Marine guy out there will attribute this comment to their branch of service, but to be clear, it came from the Army.
Actually, the original of this paraphrased quote is widely attributed to Prussian…
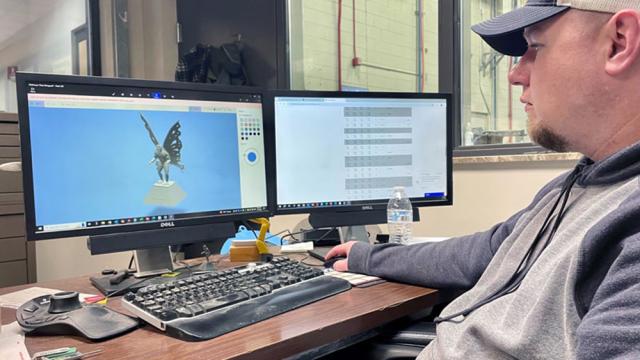
Creaform
The Marshall Advanced Manufacturing Center (MAMC) is a leading-edge resource facility dedicated to driving innovation and advancing manufacturing technologies.
Operating from West Virginia facilities in Huntington, South Charleston, and Point Pleasant, the MAMC is at the heart of groundbreaking…
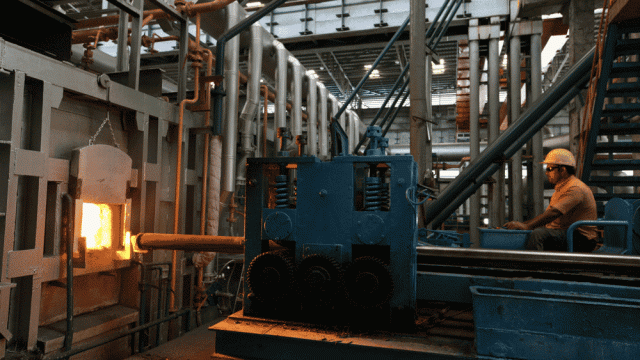
Nick Haase
When I talk with maintenance leaders, I hear urgency. Pressure is mounting. They’re being asked to cut costs, attract skilled workers, and embrace AI—and fast. Yes, pressure turns coal into diamonds. But constant pressure can wear down even the best teams. So for our 2025 State of Industrial…
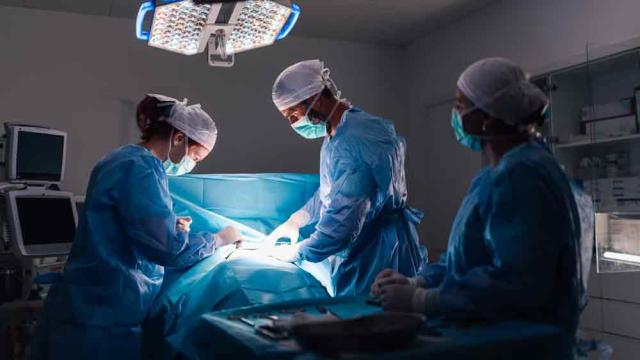
Bruce Hamilton
Last year, after many years of physical therapy, cortisone shots, and experimental treatments to prop up my failing knees, I decided to go bionic and get full knee replacements. Holding out hope for more than a decade that emerging cell-therapy technology would offer breakthrough cartilage…
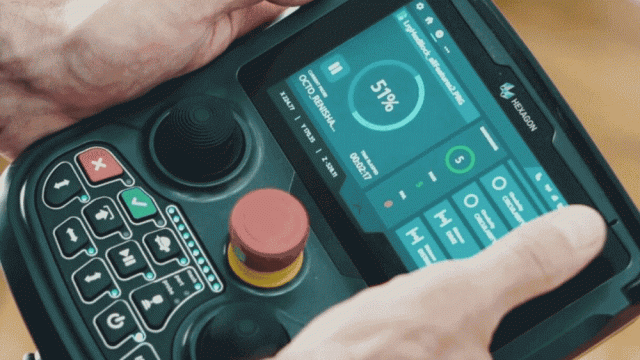
Justin Sirotin
In the early 2000s, at my former company, my team was tasked with creating educational products for a major national educational toy brand. We developed an impressive line of learning tools—forensic kits, microscopes, telescopes—designed to engage curious young minds. After securing coveted shelf…
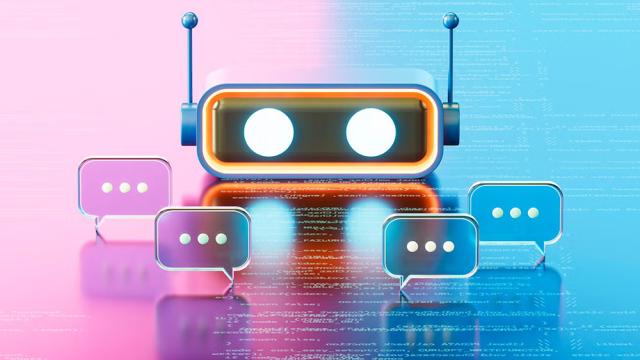
Angie Basiouny
Chatbots are everywhere. A fast-growing communication channel for brands, AI-powered chatbots are being deployed by companies to handle everything from booking travel to refunding purchases to helping shoppers choose the right outfit.
When done right, they can drive sales and provide positive…
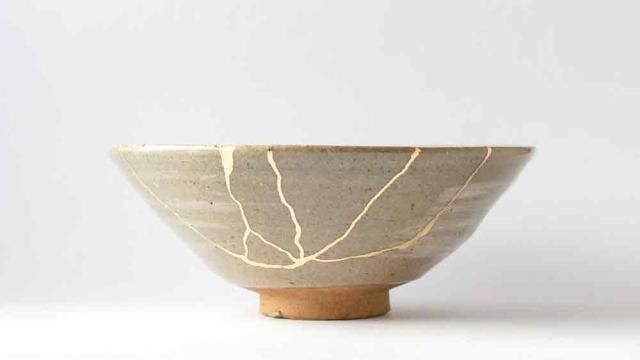
Akhilesh Gulati
In today’s competitive manufacturing landscape, resilience is the new quality. And one of the most powerful lessons in resilience doesn’t come from a factory—it comes from an art form.
In the Japanese tradition of kintsugi, a broken ceramic bowl is not discarded or disguised. It’s repaired—…
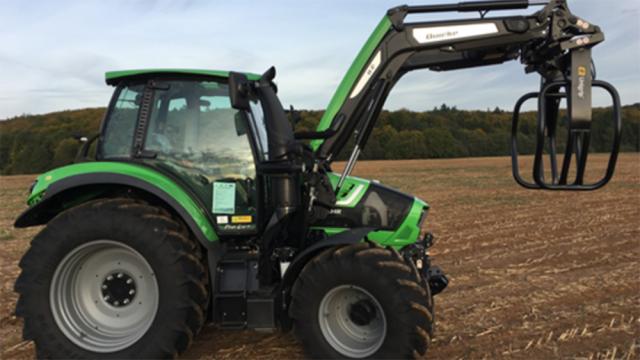
Creaform
Ålö Agricultural Machinery (Ningbo) Co. Ltd., a wholly owned subsidiary of Ålö, is a leading manufacturer of loaders and implements for agricultural tractors.
With production facilities in four countries, and customers in more than 50, Ålö holds approximately 30% of the world market for tractor…
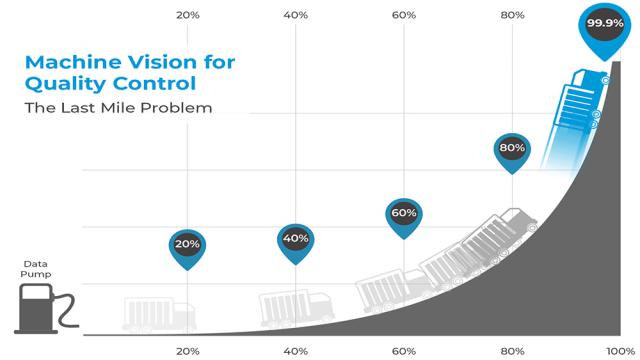
Wilhelm Klein
In 2025, sustainability is no longer optional—it’s a strategic imperative. Manufacturers, responsible for nearly 40% of global material waste, face rising demands to reduce emissions, cut waste, improve product consistency, and enhance efficiency.
Artificial intelligence (AI) is central to this…
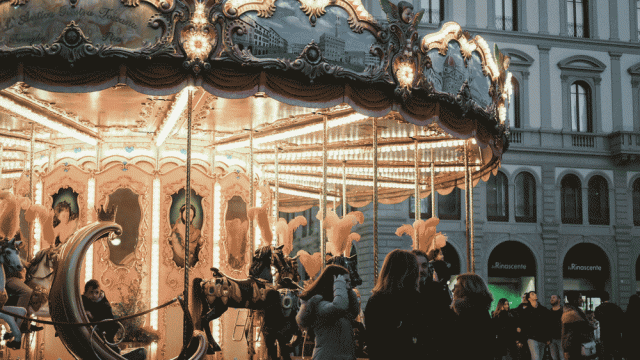
Kate Zabriskie
You know that friend who’s always there when you’re in need? The one who shows up on time, follows through on promises, and genuinely cares about what’s going on in your life? That’s exactly what your business needs to be for your customers.
Sure, those splashy marketing campaigns and point-…
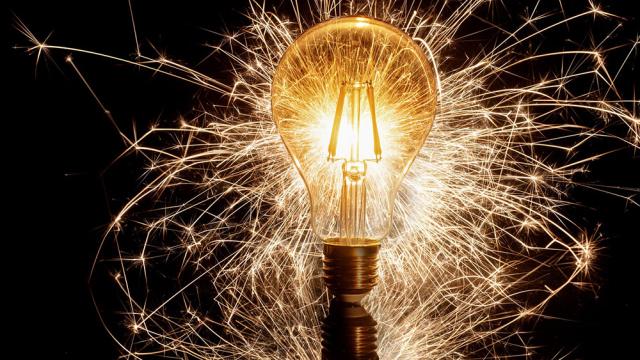
Cornelia C. Walther
Artificial intelligence’s relentless march has sparked excitement and apprehension across the business landscape. Although early narratives often pitted human intellect against the burgeoning capabilities of machines, a more nuanced and powerful reality is emerging: the era of hybrid intelligence.…
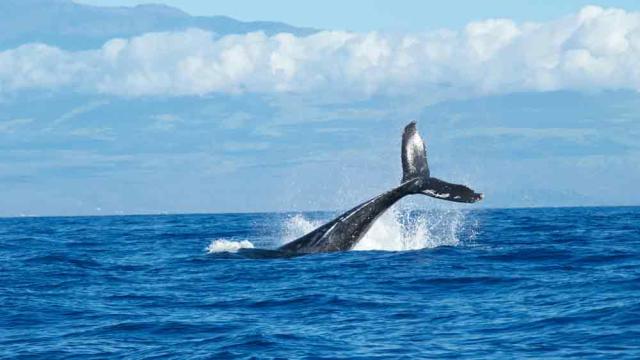
Mike Figliuolo
You can’t get big without thinking big right from the start. As an entrepreneur starting a business, it’s easy to see yourself as “the little guy.” If you do, you’ll forever stay the little guy.
Too many times I’ve seen entrepreneurs name their companies after themselves (e.g., Tom Jones, LLC).…
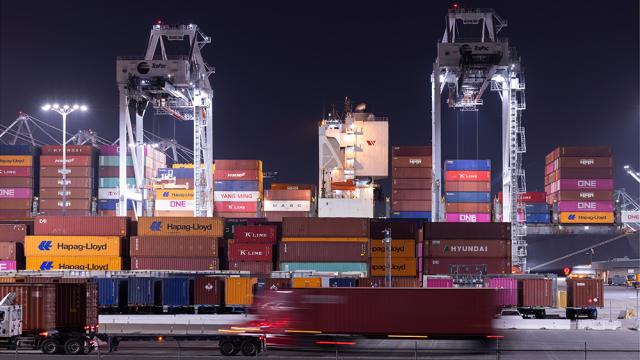
Sunderesh Heragu
According to the U.S. Census Bureau and the U.S. Bureau of Economic Analysis, trade with our three largest partners—Canada, China, and Mexico—accounted for more than $1.32 trillion in imports and $0.82 trillion in exports in calendar year 2024. This represented 40% of the total trade between the…
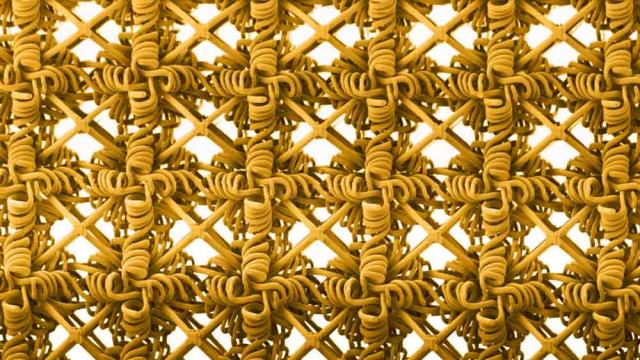
Jennifer Chu
In metamaterials design, the name of the game has long been “stronger is better.”
Metamaterials are synthetic materials with microscopic structures that give the overall material exceptional properties. A huge focus has been in designing metamaterials that are stronger and stiffer than their…
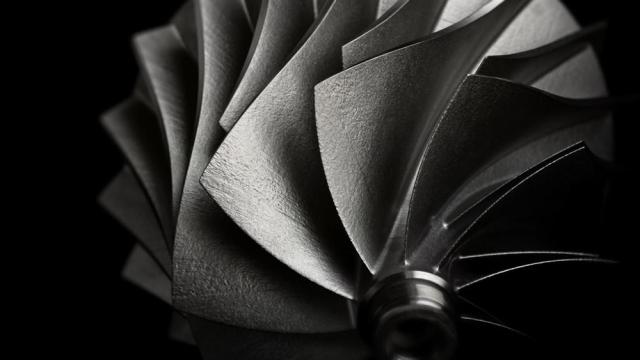
Oak Ridge National Laboratory
When Jonaaron Jones started his master’s degree at the University of Tennessee-Knoxville (UT), his mentor invited him to visit the Manufacturing Demonstration Facility, or MDF, at Oak Ridge National Laboratory (ORNL). “I saw a metal 3D-printed part for the first time,” says Jones. “I knew I was…
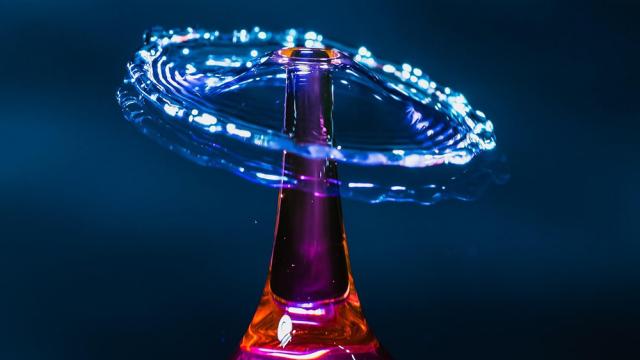
Georgia Institute of Technology
What’s the hottest thing in electronics and high-performance computing? In a word, it’s “cool.”
To be more precise, it’s a liquid cooling system developed at Georgia Tech for electronics and aimed at solving a long-standing problem: overheating.
Developed by Daniel Lorenzini, a 2019 Tech graduate…
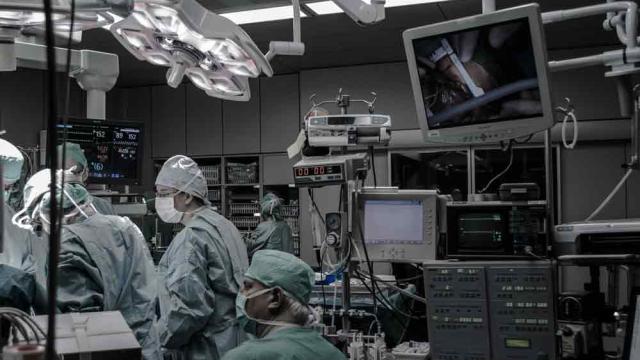
Matt McFarlane
One of the key findings in Greenlight Guru’s 2025 Medical Device Industry Report was that economic uncertainty is playing a large role in the decisions medical device companies make this year.
The report surveyed more than 500 medical device professionals across quality, regulatory, product…
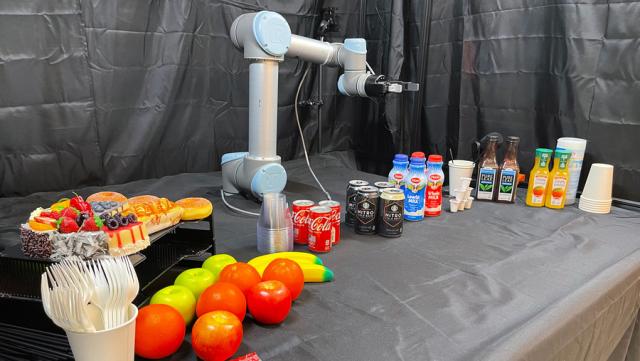
Jennifer Chu
For a robot, the real world is a lot to take in. Making sense of every data point in a scene can take a huge amount of computational effort and time. Using that information to then decide how to best help a human is an even thornier exercise.
Now, MIT roboticists have a way to cut through the data…
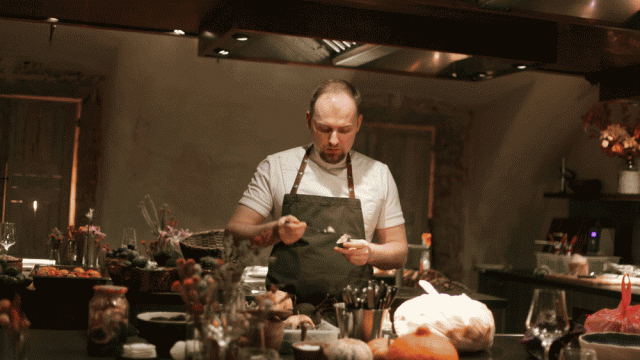
Jones Loflin
In a professional kitchen, no chef prepares a steak, a cake, and a casserole simultaneously with all the ingredients scattered across the counter. There’s a method: one recipe at a time, with only the ingredients needed for that specific dish.
The same principle applies to how we work, especially…
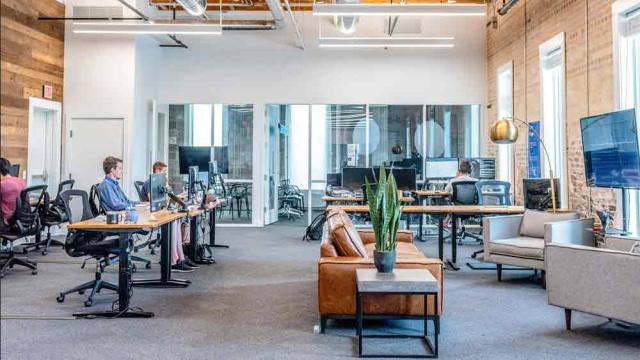
Bruce Hamilton
A few months ago I visited a potential customer, a high-tech startup, which like many Boston-area tech companies is developing astounding products that would have been considered science fiction only 10 years ago. The parking lot was half full at 8 a.m., but the entrance was locked to visitors, and…
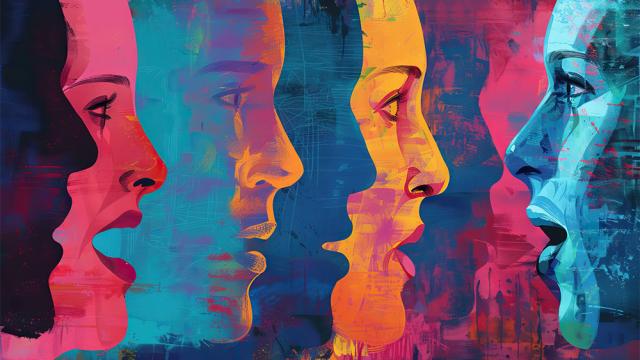
Chris Chuang
As a technology leader, I must admit that making the right investment in new innovations has its challenges. It’s easy to get caught up in the grandiose potential solutions offer, become overwhelmed by the setup, and struggle with employee adoption.
For the last decade, I’ve worked with human-…
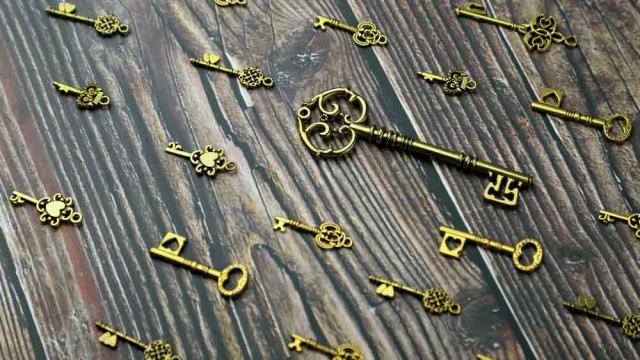
Stephanie Ojeda
Every day, quality leaders face a variety of production and process issues. Although some problems are easy to fix, others require deeper investigation, such as using a 5 Whys analysis or fishbone diagram. But then there are the stubborn, recurring issues that can lead to quality issues, increased…