All Features
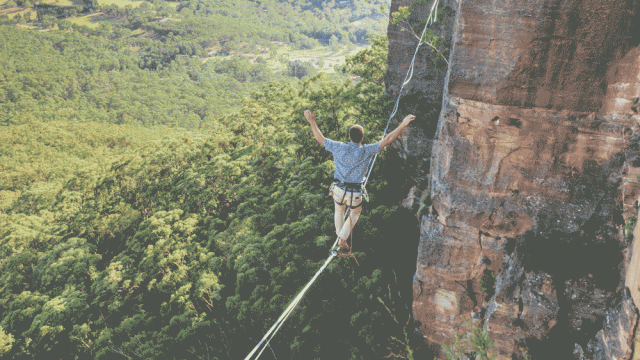
Michael Mills
Risk-based thinking—it sounds easy. How hard can it be to think about risk? But did you know that the phrase “risk-based thinking” was only invented in 2015?
Did you know that the ISO says “risk-based thinking” is one of the foundations of quality management, but never defines it? Or that it…
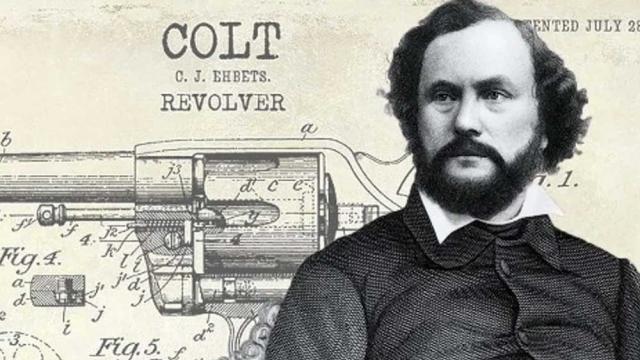
Chip Bell
Innovation is vital to the success of all businesses. Innovate or perish is the new mantra. Leaders must perpetually reinvent their processes, products, and services, because they typically have multiple competitors offering similar offerings. Only through innovation can most organizations…
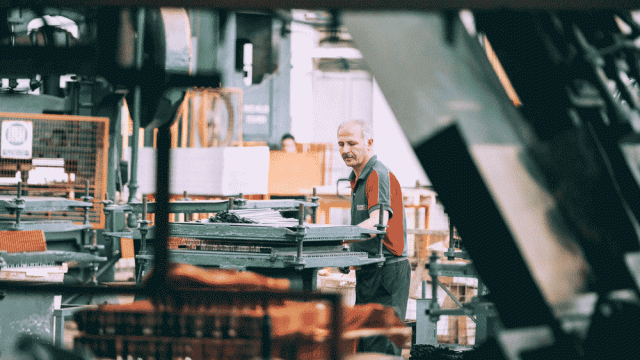
Scott Ginsberg
Manufacturers face a critical challenge: capturing, standardizing, and scaling workforce knowledge. Skilled workers are retiring, and labor shortages are persisting. Outdated, paper-based documentation can no longer keep up. These methods create bottlenecks that slow productivity and make vital…
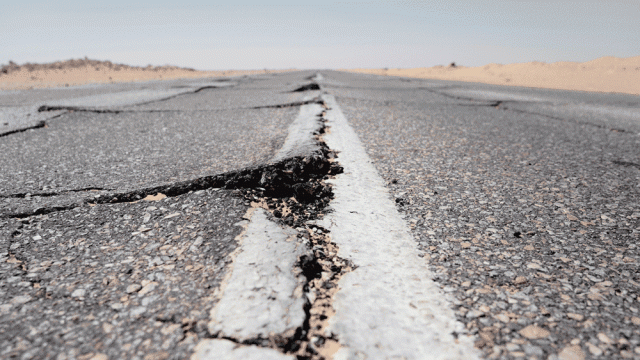
Felipe Monteiro
Global risks are rising, and many companies are struggling to adapt. The World Economic Forum’s 2025 Global Risks Report makes it clear that challenges like escalating global tensions and conflicts, climate change, economic instability, and supply chain disruptions are interconnected and build on…
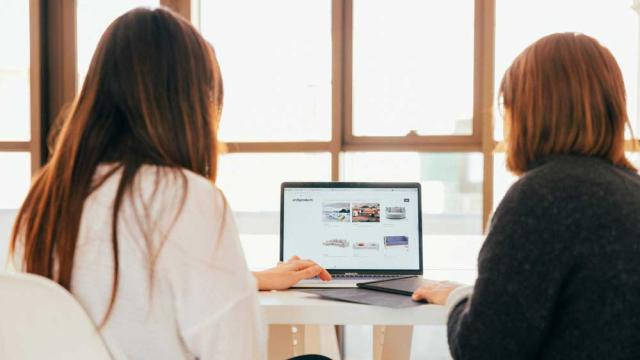
Gleb Tsipursky
One transformative strategy that can revolutionize how organizations embrace generative AI is peer mentoring. By leveraging the power of personal connections and shared expertise, peer mentoring accelerates learning, fosters collaboration, and fuels innovation. When mastering gen AI tools can mean…
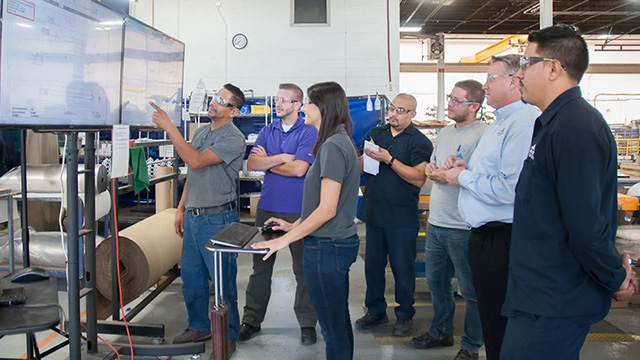
Torsten Schimanski
Workforce development is an essential yet frequently overlooked aspect of supply chain management in manufacturing. Similar to how disruptions in material sourcing or logistics can halt operations, talent shortages and skill gaps create bottlenecks that jeopardize efficiency, quality, and growth. …
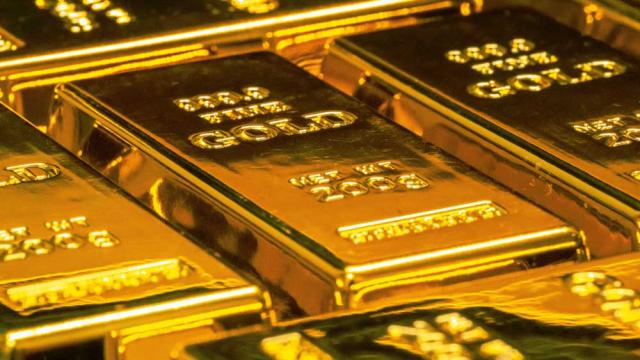
Donald J. Wheeler
Outliers are values that don’t “fit in” with the rest of the data. These extreme values are commonly considered a nuisance when we seek to summarize the data with our descriptive statistics. This article will show how to turn these nuisances into useful information.
The earliest statistical tests…
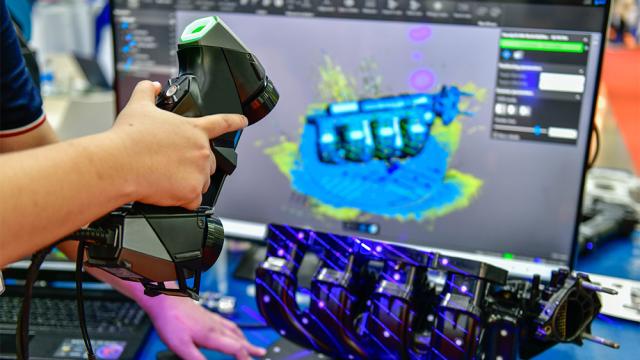
Steven Ouellette
Many industries, from aerospace to medical device manufacturing, are required to show customers, auditors, or regulatory bodies that their measurement devices are acceptable for use. But how do you prove that?
One of my clients needed to show the Biomedical Advanced Research and Development…
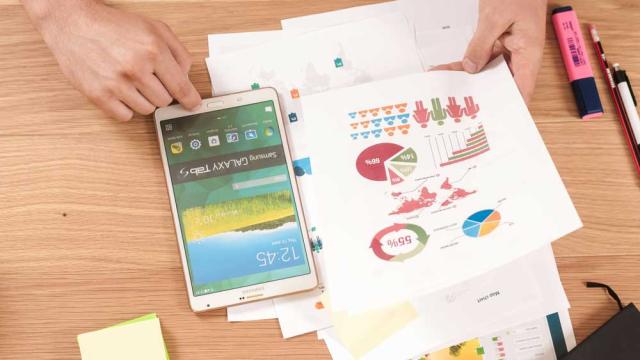
Oliver Franz
Maybe you’re pulling reports from three different platforms, trying to reconcile numbers that don’t quite match. Maybe you’re manually copying and pasting from multiple spreadsheets, hoping you didn’t introduce any errors along the way. Or maybe you’re waiting on IT to clean up, prep data, and…
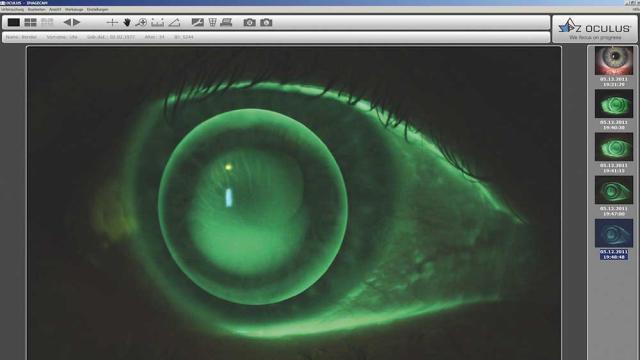
IDS Imaging Development Systems
The slit-lamp examination is one of the most important diagnostic techniques in ophthalmology. It enables a detailed examination of the anterior, middle, and posterior segments of the eye. Ophthalmologists can use it to recognize the smallest changes, anomalies, or damage. This procedure is used…
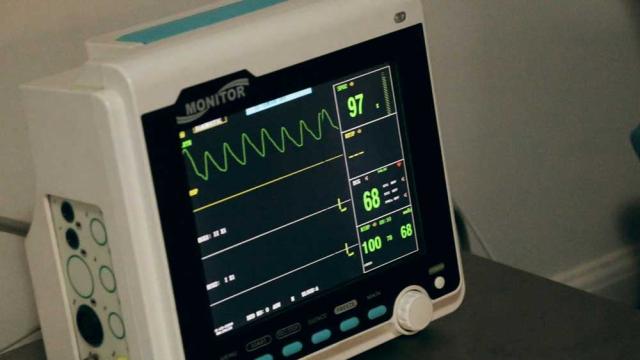
Matt McFarlane
The medical device industry is growing. Data from KPMG predict that global annual sales will rise by 5% per year to reach just under $800 billion by 2030. New technology, new opportunities, and, as always, the promise of improving patient outcomes around the world are major drivers of growth within…
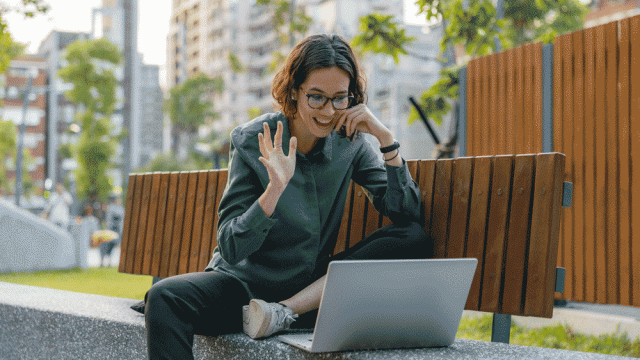
Christine Schaefer
José Pires, founder and CEO of Global Excellence & Innovation, has helped large and small organizations across multiple industries transform their leadership to achieve better results. Based on his decades of experience guiding organizations toward performance excellence, innovation, and…
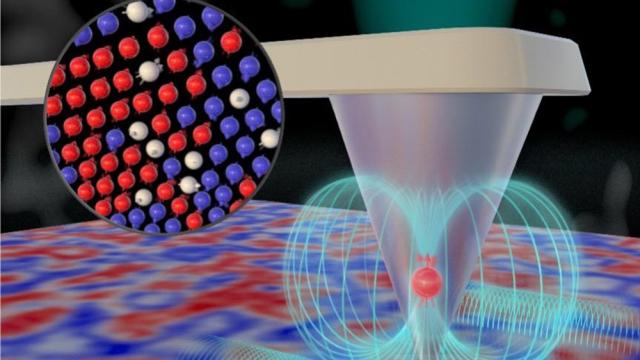
Oak Ridge National Laboratory
Working at nanoscale dimensions, billionths of a meter in size, a team of scientists led by the U.S. Department of Energy’s Oak Ridge National Laboratory (ORNL) revealed a new way to measure high-speed fluctuations in magnetic materials. Knowledge obtained by these new measurements, published in…
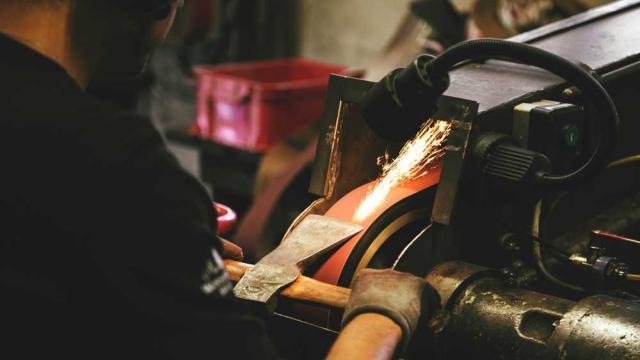
Mark Hembree
Some people don’t feel like they’re working unless their hair’s on fire. Somehow, they think it’s admirable to be feverish at a frenzied pace, breathless and full of urgency, turning tasks in record time and pushing the team to accelerate. Surely others will take notice and marvel at such hard work…
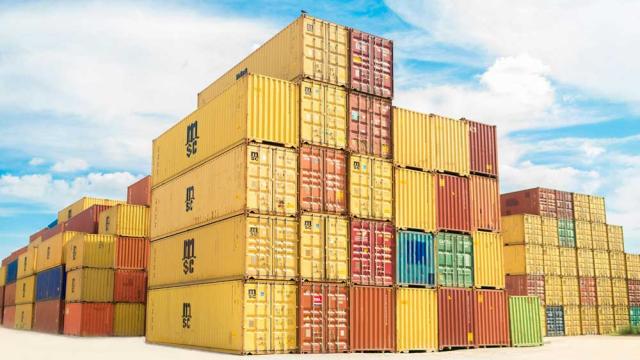
Angelina Rivera
Manufacturing is a fast-paced, constantly evolving, and dynamic environment, and the supply chain is at its heart. For small and medium-sized manufacturers (SMMs), navigating the complexities of the supply chain often feels like a high-stakes balancing act. From juggling fluctuating material costs…
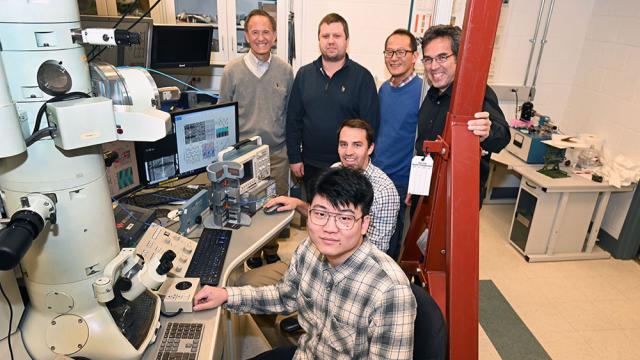
Laura Mgrdichian-West
One major category of the next generation of energy-efficient microelectronic devices and information processing technologies will likely be based on “spintronics,” which leverages both an electron’s charge and its spin—the tiny “up” or “down” magnetic moment carried by every electron. Now, a…
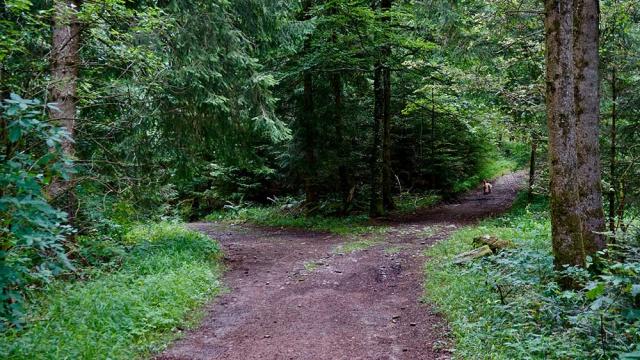
Mike Figliuolo
A leader’s daily decision checklist is daunting: From hiring or firing to major business changes, every judgment call carries with it some level of risk. A bad choice could result in a toxic hire or a new product launch that crashes and burns. Perhaps more frightening is this: One poor decision…
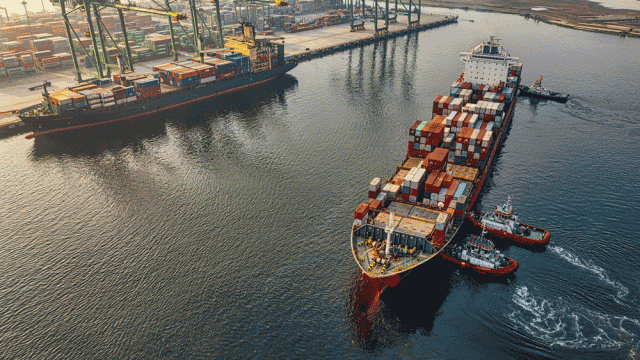
Jonathan R. Todd
Geopolitical risk is emerging as one of the greatest challenges facing domestic and international business today. It has risen from a boardroom issue to one drawing the awareness and attention of both personnel and the general public. These days everyone knows the word “supply chain” and has some…
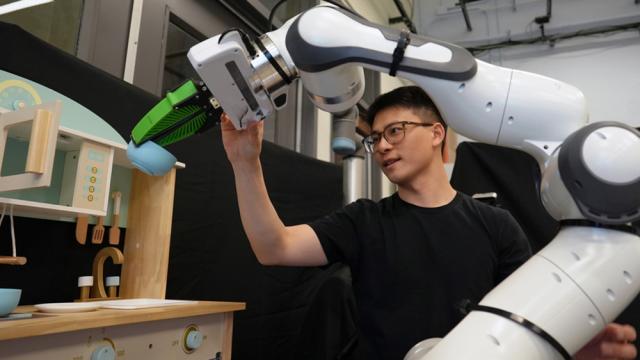
Adam Zewe
Imagine that a robot is helping you clean the dishes. You ask it to grab a soapy bowl out of the sink, but its gripper slightly misses the mark.
Using a new framework developed by MIT and NVIDIA researchers, you could correct that robot’s behavior with simple interactions. The method would allow…
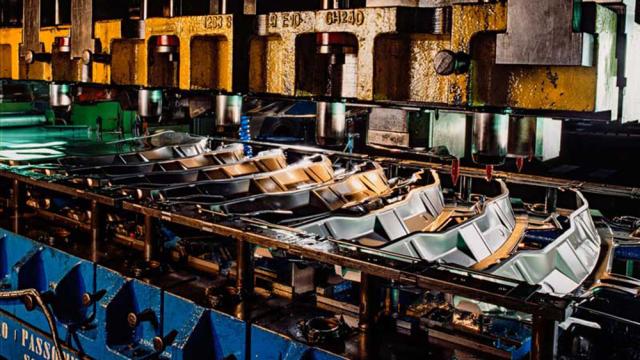
Creaform
Each type of part presents its own set of inspection challenges. This is especially true for sheet metal parts that are made of various entities, each with different positioning and dimensioning tolerances, and variable thickness gauges and sizes. These features can be inherently laborious to…
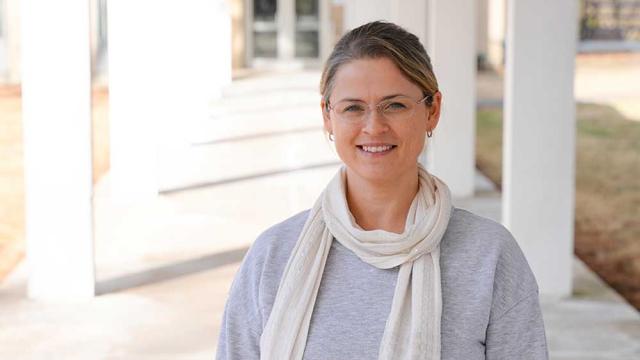
Justyna Zwolak
I previously wrote a blog post about Ada Lovelace, often celebrated as “the world’s first computer programmer.” While I genuinely enjoyed crafting that piece, I wished for the opportunity to write about a scientist who is much closer to my heart: Maria Skłodowska-Curie. She has always been and…
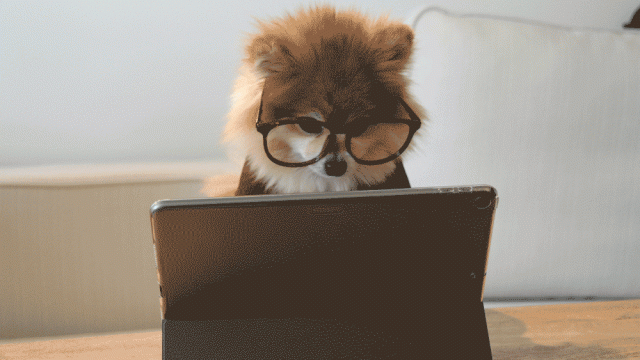
Maria DiBari
This current job market is plagued by fake job postings that have been misleading American job seekers, wasting their time and distorting employment data. These deceptive listings—often created to collect résumés, inflate company growth metrics, or manipulate job market statistics—erode trust in…
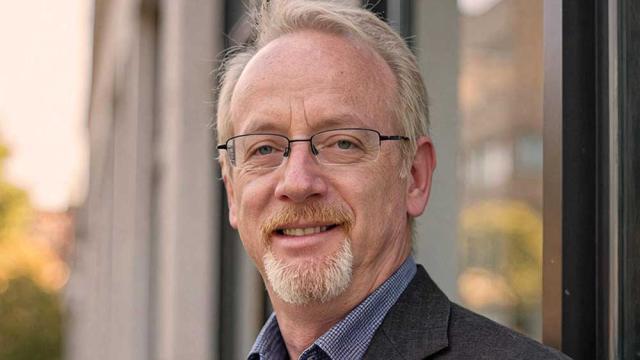
Christine Schaefer
With the right approach, artificial intelligence isn’t “just a tool.” It can be “a real-time decision-making partner”—one that “empowers the workforce, making knowledge more accessible while ensuring that organizations have faster and smarter operations.” So says Ron Norris, retired director of…
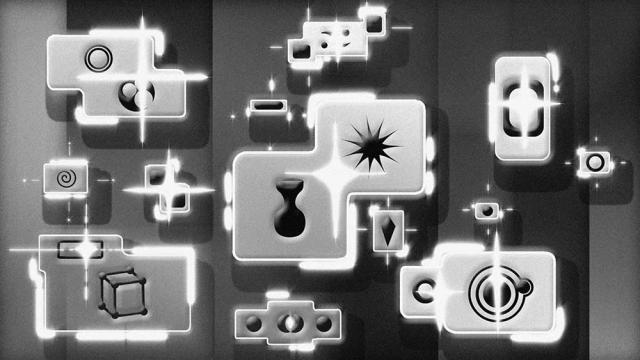
Gleb Tsipursky
In the current professional landscape, idea generation is revered as a hallmark of creativity and innovation. Organizations celebrate those who can generate new and groundbreaking concepts, often overlooking the subtler art of idea curation.
However, the rapid advancement of generative AI is…
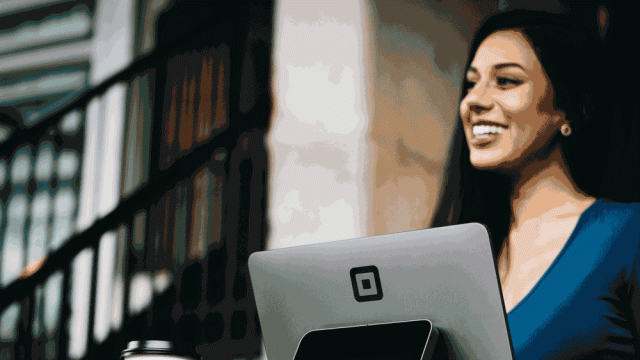
John Tschohl
I ’ve been skiing in Vail, Colorado, one of the best skiing areas in the world, for more than 50 years. George Gillett Jr. acquired the resort in 1985. But when I first met him in 1978 and asked him what he does, he said, “I am in customer service.”
Gillett is out of that business now. And though…