All Features
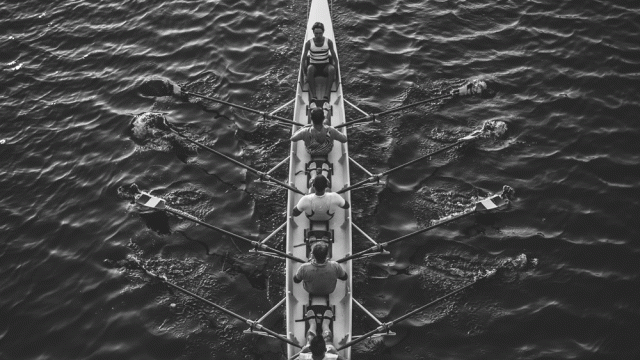
Adam Grant, Michael Platt, Jonah Berger, Jerry Wind
Nano Tools for Leaders—a collaboration between Wharton Executive Education and Wharton’s Center for Leadership and Change Management—are fast, effective tools that you can learn and start using in less than 15 minutes, with the potential to significantly impact your success and the engagement and…
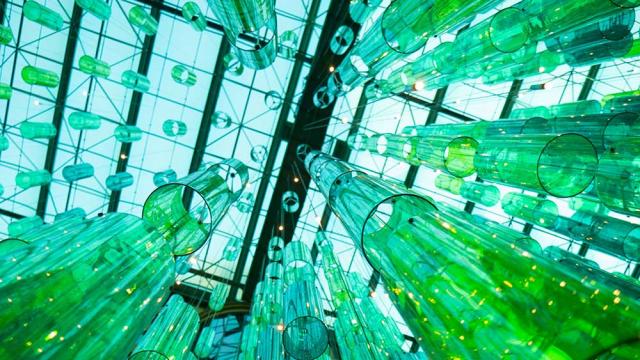
Matt Tweedy
In global manufacturing, two key goals—intertwined yet distinct—heavily dominate the industry’s agenda: addressing the growing demand for environmentally sustainable practices, and optimizing operational efficiency. With these priorities in mind, companies are seeking multifaceted solutions that…
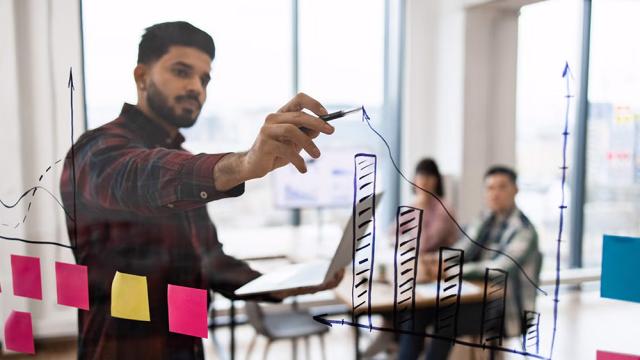
Seb Murray
New research co-authored by University of Pennsylvania academics challenges a core assumption in economics: That the most successful companies achieve their dominance purely through superior productivity. Instead, this study highlights the important role of scalability—how well firms can grow as…
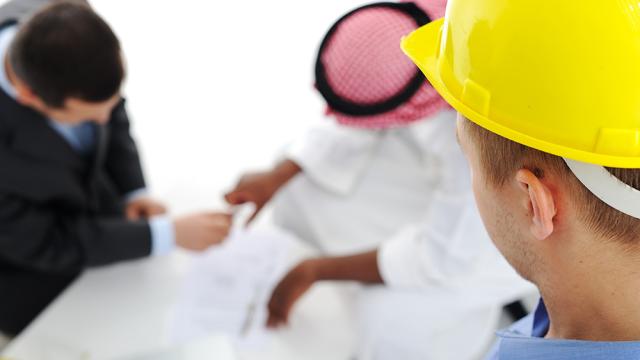
Alfredo Romero
Many marketing professionals are drawn to their field because they consider themselves more right-brained (creative) than left-brained (analytical). It’s true that success in marketing often requires imagination, creativity, and an emotional appeal to the target audience. In fact, many college…
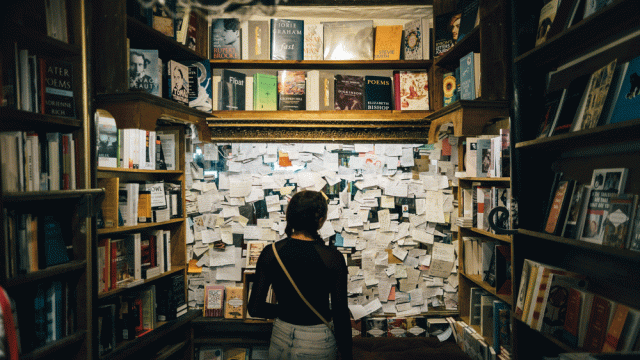
Harish Jose
Today I’m looking at the free energy principle (FEP) by the British neuroscientist Karl Friston. The FEP basically states that to resist the natural tendency to disorder, adaptive agents must minimize surprise. This has implications for the gemba, as you’ll see.
A good example to explain this is…
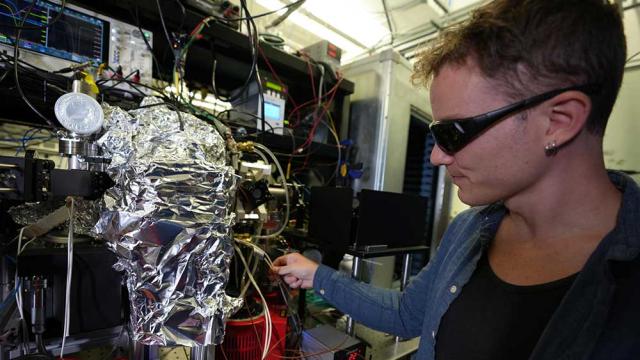
NIST
Scientists at the National Institute of Standards and Technology (NIST) have created a new thermometer using atoms boosted to such high energy levels that they are 1,000 times larger than normal. By monitoring how these giant “Rydberg” atoms interact with heat in their environment, researchers can…
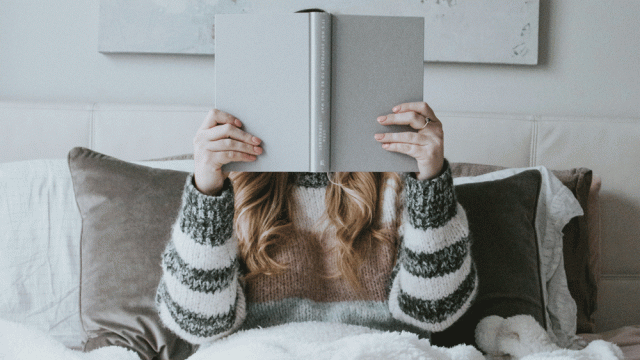
Steven Garner
In the ever-changing landscape of business management, the concept of quality has undergone significant transformations. What began as a focus on maintaining standards such as ISO 9001 and AS9100 is evolving into a more holistic approach encompassing organizational excellence. Tom Taormina’s book…
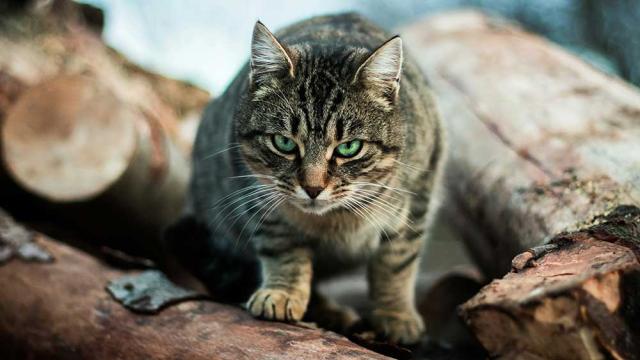
Theodore Kinni
There’s an old saw—cribbed from Plato and popularized by Douglas Adams—that those most interested in leading others are least suited to the task. That’s not entirely accurate, yet new research has found a grain of truth in this idea: Many leaders have plenty of ambition to lead, but that’s no…
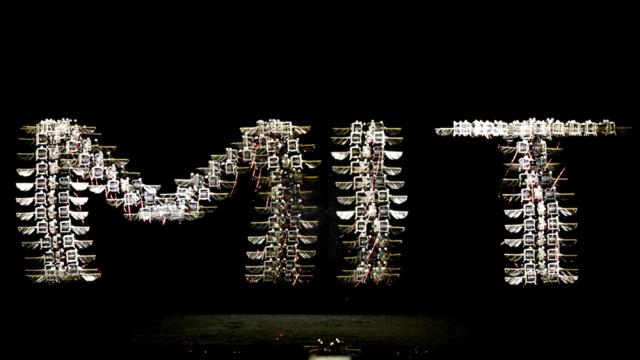
Adam Zewe
With a more efficient method for artificial pollination, farmers in the future could grow fruits and vegetables inside multilevel warehouses, boosting yields while mitigating some of agriculture’s harmful effects on the environment.
To help make this idea a reality, MIT researchers are developing…
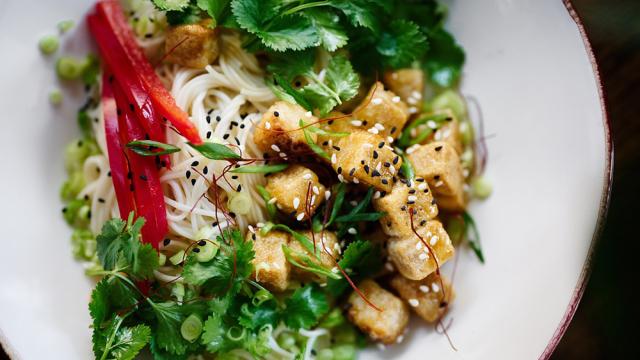
Wayne Labs
A September 2024 Gallup poll revealed that nearly 30% of U.S. adults have little to no confidence in the safety of U.S. foods at the grocery store. Considering recent recalls, is it any wonder? What good is a quality control program if it doesn’t include food safety?
Boar’s Head’s Jarratt,…
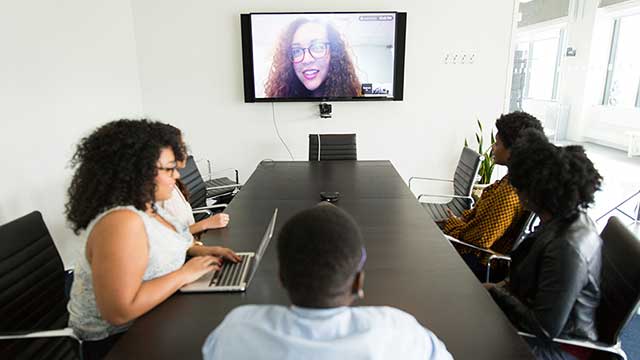
Gleb Tsipursky
The pandemic forced leaders to reconcile with the need for effective hybrid and remote team management strategies, including performance evaluations. Research has shown the benefits of moving away from large-scale quarterly or annual performance reviews. Instead, successful organizations favor…
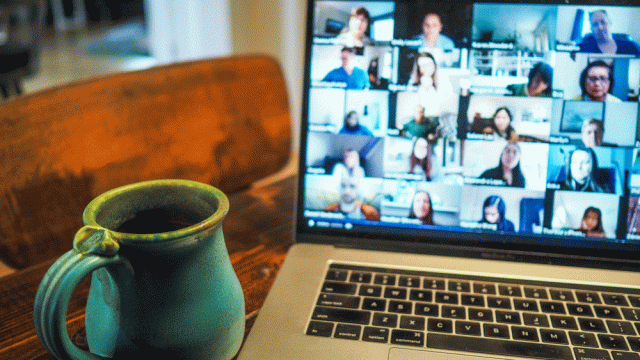
Cindy Mielke
Businesses today have more options than ever before regarding where and how they recruit new talent. Thanks to new technologies and a general shift in working cultures, organizations can now access a much wider talent pool when hiring full-time remote employees.
However, with this added hiring…
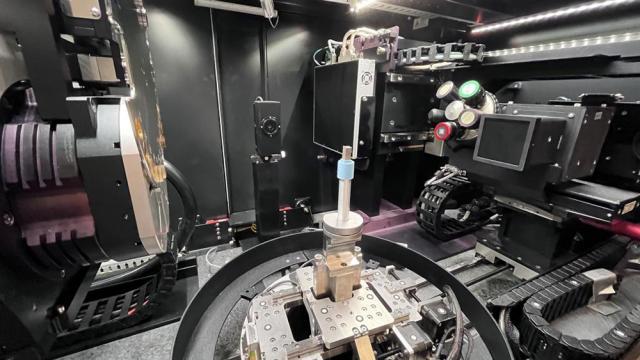
S. Heather Duncan
Idaho National Laboratory (INL) uses a software algorithm that Oak Ridge National Laboratory (ORNL) developed to check for flaws in additively manufactured components. This is part of the process of identifying promising metals and alloys for 3D printing the next generation of nuclear reactors. …
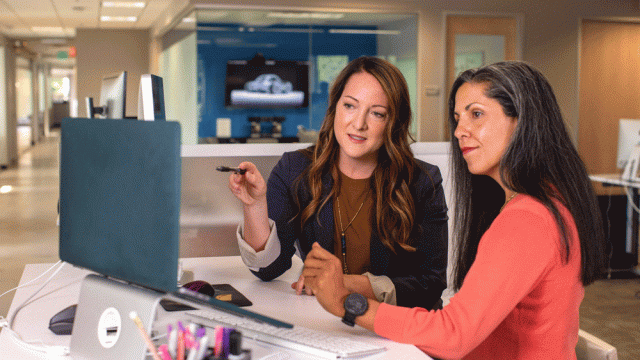
Derek Deasy, Enoch Li
Having a coach these days is almost a given, an essential part of any senior executive’s career portfolio. But while some leaders swear by their coaches, others just can’t seem to find the “right one.” What causes these wildly different experiences?
While there are multiple approaches and…
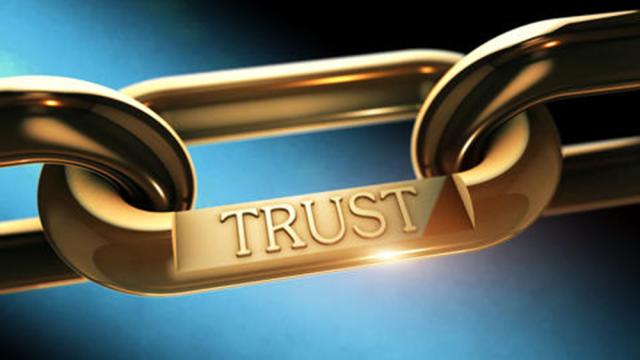
NIST
Without us realizing it, metrology and its associated standards and services play a big role in our daily lives. We buy groceries that are weighed or measured. Prepackaged products are weighed or measured during production. Medicine at the pharmacy is measured to make sure it contains the right…
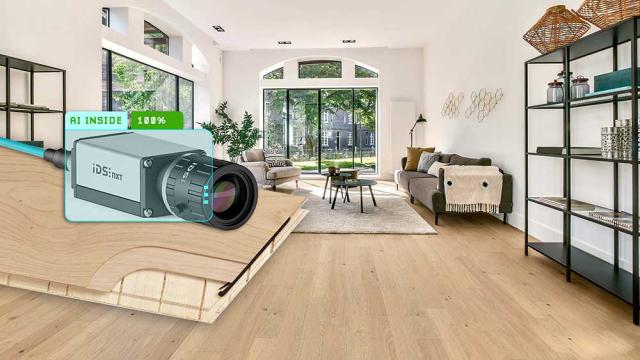
Sabine Terrasi
It creates a warm and inviting atmosphere. Its natural grain and color tones have a lively effect and add character to a room. We are talking about classic wood flooring—usually laminate, and optionally with a click system for easy installation.
Scheucher Holzindustrie GmbH, from Mettersdorf,…
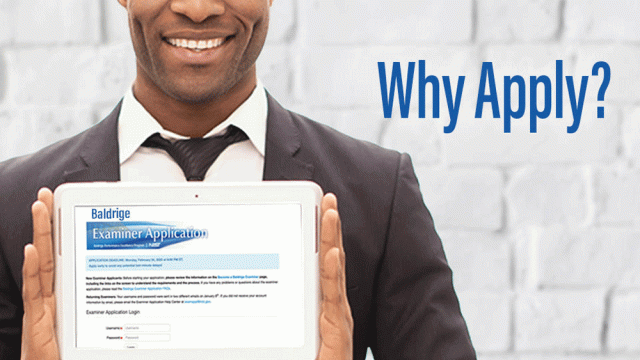
Christine Schaefer
In a recent blog, I provided many reasons to apply to be a 2025 Baldrige examiner. The benefits of serving in this volunteer role were conveyed by three highly experienced Baldrige examiners with career expertise from the business, K-12 education, and healthcare sectors. Each served as an…
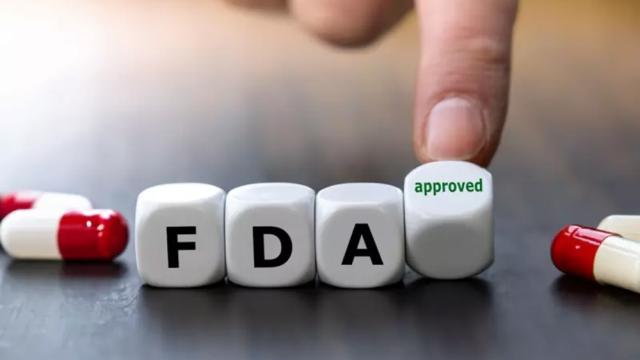
Stephanie Ojeda
The U.S. Food and Drug Administration’s inspections and subsequent actions all come down to product quality. Quality system failures result in noncompliances that FDA inspectors target during their inspections. If there is any doubt that a manufacturer’s product is safe and effective, it is the…
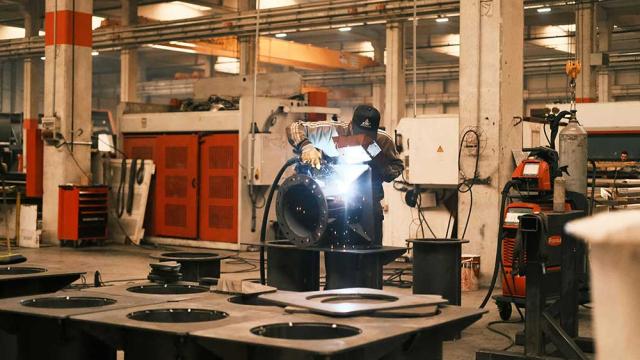
Akhilesh Gulati
Paul was sitting in his office staring at production numbers from the past quarter. Despite having a great team, strong customer demand, and state-of-the-art equipment, the factory’s performance wasn’t meeting expectations. There was a bottleneck in the assembly line—a critical chokepoint that was…
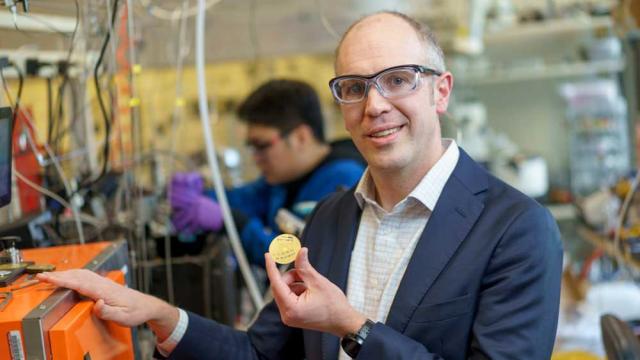
Anne Trafton
For many industrial processes, the typical way to separate gases, liquids, or ions is with heat, using slight differences in boiling points to purify mixtures. These thermal processes account for roughly 10% of the energy use in the United States.
MIT chemical engineer Zachary Smith wants to…
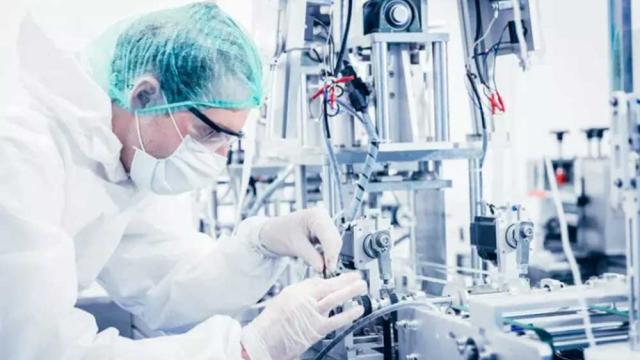
Stephanie Ojeda
In April 2018, the U.S. Food and Drug Administration (FDA) approved the first artificial intelligence-powered diagnostic system, a software program used to detect diabetes-related vision loss.
Since then, the industry has seen explosive growth of AI in medical device manufacturing, which is…
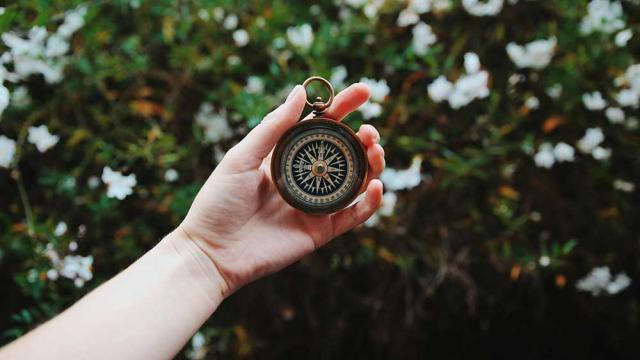
Mike Figliuolo
For me, the future is all about learning and teaching. Learning new ideas or disciplines fascinates me. Interconnecting those experiences and disciplines and creating new ideas to share with others through teaching is even more exciting. And the more I teach, the more I learn from my class…
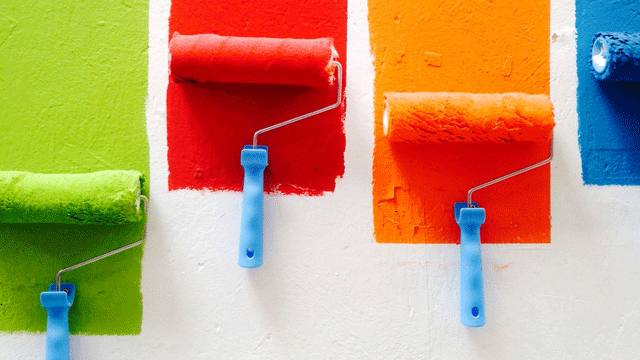
Jones Loflin
I enjoy painting, and I’ll admit that I’m not the neatest painter out there—I get a lot on me. And I’m not the fastest painter either, but I feel like I do a pretty good job. One of the tools that helps me improve my painting skills is painter’s tape (the blue stuff is my favorite). It enables me…
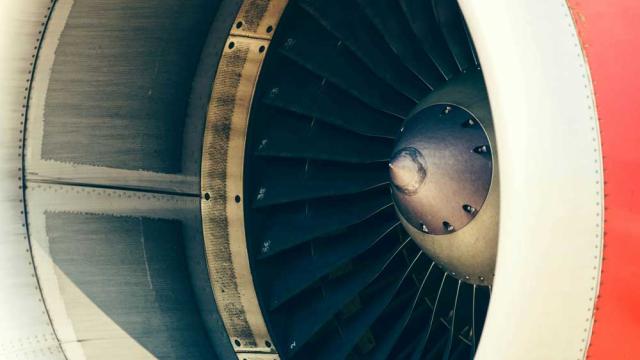
Brian Hughes
We live in a world where problems aren’t just growing—they’re evolving into ever-more complex challenges. During the 20th century, we pushed the boundaries of innovation, creating complicated systems that demanded structured problem-solving approaches. Techniques like 5 Whys and the Ishikawa…

Ariana Tantillo
On June 18, 2023, the Titan submersible was about 90 minutes into its two-hour descent to the Titanic wreckage at the bottom of the Atlantic Ocean when it lost contact with its support ship. This break in communication set off a frantic search for the tourist submersible and five passengers on…