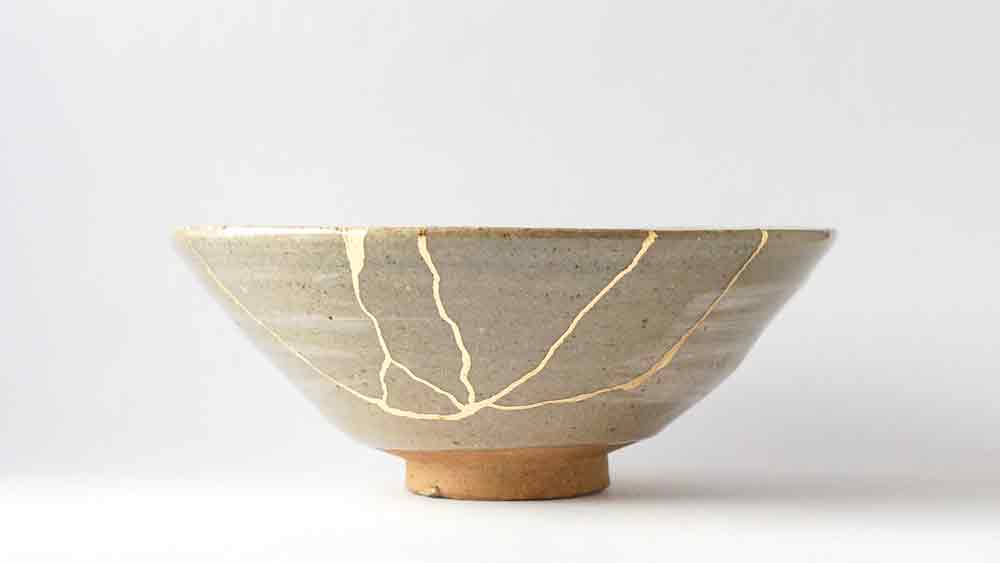
Marco Montalti/iStock
In today’s competitive manufacturing landscape, resilience is the new quality. And one of the most powerful lessons in resilience doesn’t come from a factory—it comes from an art form.
ADVERTISEMENT |
In the Japanese tradition of kintsugi, a broken ceramic bowl is not discarded or disguised. It’s repaired—carefully and visibly—with lacquer mixed with gold. The cracks aren’t hidden. They’re honored.
The result? A vessel that’s more beautiful and more valuable because of its history.
Manufacturing might seem far removed from this philosophy. But kintsugi offers a compelling leadership lens that reframes how we handle breakdowns in systems, teams, and culture, especially in our pursuit of quality.
Turning bottlenecks into breakthroughs: A paper mill’s journey
A Midwest paper mill was stuck. Persistent delays in the finishing department meant late orders, ballooning WIP, and a culture of blame. Leadership could have defaulted to top-down control with more rules or more meetings. Instead, they chose transparency.
…
Comments
Key to a Quality Culture
I love this article. Responding to mistakes with respect (kintsugi) builds a culture of trust and ownership. A quality culture can only thrive if founded on respect. Otherwise, team members won’t engage and drive real continuous improvement (kaizen).
Kintsugi & Kaizen
Thank you — I’m so glad this resonated with you. And I like the way you've captured it: respect isn’t just a nice-to-have, it’s the foundation for any real culture of quality. This creates an environment where employees feel safe to engage, share, or improve, in addition to coming up with 'supposedly outrageous ideas' providing a different perspective. You might have noted that in something I've written about earlier on 'Thinking Fridays'.
It’s interesting how both kintsugi and kaizen ask us to view imperfection not as a failure, but as a starting point for deeper value. I appreciate your thoughtful reflection. Would love to hear any thoughts / stories you'd like to share.
Kintsugi
I watched as a stocker bumped a bottle off a shelf in my favorite grocery store. It was impressive how he moved quickly to a spill control station and took charge of warning signs and spill control. I told him "Your professionalism shows in how you respond to a problem".
Kintsugi - how we respond4
What a great example, Mike; thank you for sharing. With it you capture the heart of Kintsugi thinking: it’s not about avoiding every crack, but how we respond when they appear.
And it is in the Response that we see Professionalism, and org culture. I appreciate this perspective, and would love to hear more.
Kintsugi - A way to improve
Dear Akhilesh
it was so refreshing to read your article which forces the reader to look within how we can learn from apparent failures and come out even stronger.
The examples given are very simply put but carry a deep meaning and rewards. The principle can be applied equally to broken relationships too.
keep it up AG
sach
Kintsugi application to relationships
Thank you so much, Sach — I’m really glad the piece resonated with you. And although I did not view it from that angle, I agree completely: the mindset behind Kintsugi applies just as much to relationships as it does to systems or processes. In fact I recall there was a movie that applies similar concepts (not specifying Kintsugi though) to mend broken relationships. Perhaps you recall and can share. It will also be terrific if you have seen the thought applied somewhere . Look forward to hearing more.
Sometimes the most meaningful growth comes not from avoiding fractures, but from how we choose to repair and rebuild, and we see some of this in mending the political divide among classmates. I truly appreciate your kind words and encouragement.
Relationship Movie Example of Kintsugi
Akhilesh,
While I may be wrong, I think "When Harry Met Sally" may fit the relationship angle of Kintsugi. I'm sure most of the readers have seen the 1989 movie by now, but if not, their relationship starts off "broken," like the pottery. Over time, they keep interacting with each other by chance, and (spoiler alert) they end up together, stronger than before.
Perhaps there are other movie examples, but this one is a "classic."
Ken, Thank you for expanding…
Ken, Thank you for expanding on the concept. And it is your kind of thinking that expands on the idea of renewal AND internalizes it for the individual (thinking of an application /issue / situation in one's own environment (personal or professional).
It'll be interesting to see if any other reader shares another movie examples. Feel free to reach out to me on Linkedin and/or leave a note there.
Kintsugi
The art of repairing what is broken and successfully making it work better is inspiring.
Your application of Kintsugi in a larger scale is brilliant.
B
Thank you, Bharati — I…
Thank you, Bharati — I really appreciate your kind words. I find Kintsugi inspiring not just as an art form, but as a mindset: the idea that repair can lead to renewal, and even improvement.
I’m glad the larger application resonated with you — it’s a perspective I believe many organizations can benefit from.
Add new comment