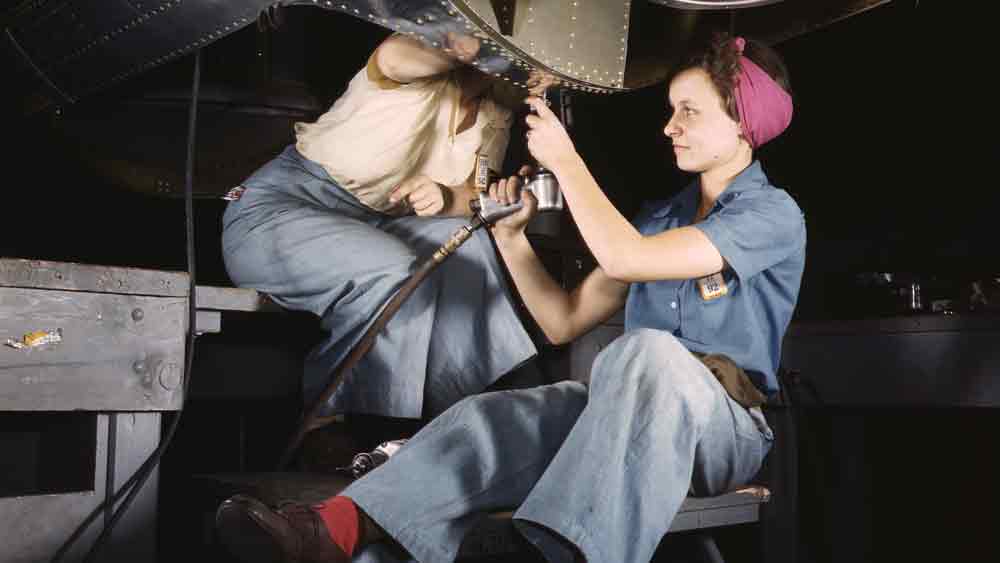
U.S. Library of Congress
Working on a bomber, Douglas Aircraft Co., Long Beach, California, 1942.
The Chinese character for crisis means “danger” and “opportunity,” and tariffs have created a supply chain crisis throughout the United States. Paul Roberts of the Seattle Times reports that fewer ships are arriving in Seattle: “Fewer ships coming into the U.S. means companies can’t get components. Retailers and consumers can’t get products.” Regardless of whether one agrees with the tariffs, the die has been cast.
ADVERTISEMENT |
This is far from the first time the United States has had to step up to a crisis, as we did when we led the world to victory during World War II. Likewise, Japan helped meet the Covid-19 challenge when a plant had to multiply its output of protective garments a hundredfold without adding people or significant capital investment. Manufacturers have the means readily at hand to deal with this latest crisis. All we need is the will to use it.
…
Comments
Tarrifs
Good take on this by Mr. Levinson. I would add that, for many things, low wages are no longer a big advantage for China. With the added shipping cost, that should almost be a wash. I have seen some very automated factories in China that are shipping products to the United States. Government cost that is added to the cost of doing business in the United States needs to be lowered. Some tariffs on China are needed just to overcome their currency manipulation and other governmental type subsidies for manufacturing in China. I have been converted to a Fair Trade proponent.
Uncomfortable Truths About Offshoring US Manufacturing
Agreed we have what we need, except maybe the will to make it happen. As I discuss in my Linked In post, greed and failure of leadership led to offshoring some 30-40 years ago. Can our leaders behave differently this time? The challenges facing manufacturing will require collaboration across sectors, discipline and courage to address - for years, perhaps decades.
One of your best columns
Bill, you've beautifully captured the essence of the problem and the challenge. I love the Henry Ford quote. It's exciting to see how quickly American manufacturers are changing their ways.
Thank you!
Thank you!
Add new comment