All Features
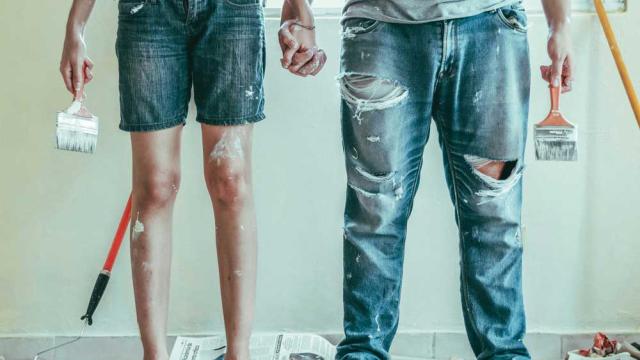
Mike Figliuolo
We’re constantly seeking ways to both improve our business but save money at the same time. That can lead to the dangerous dynamic of “I’ll do it myself.”
Doing more with less can turn us into idiots. Our hubris and arrogance puts our idiocy into action. Sorry—I got a little ranty right out of the…
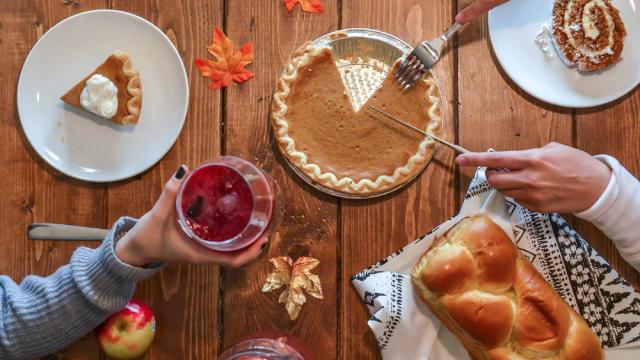
Stephen Dombroski
Thanksgiving dinner: the annual marathon of kitchen chaos, time crunches, and the occasional family squabble over cranberry sauce. For many, it’s the ultimate test of culinary coordination. But the truth is, organizing this feast has more in common with a modern production line than one might…
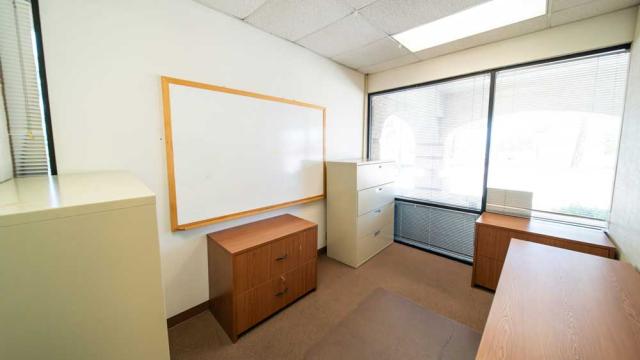
Gleb Tsipursky
In recent months, headlines have proclaimed that companies like Amazon are demanding that employees return to the office in droves, signaling the end of the flexible work era.
However, contrary to these attention-grabbing headlines, reliable and objective data from sources like the U.S. Bureau of…
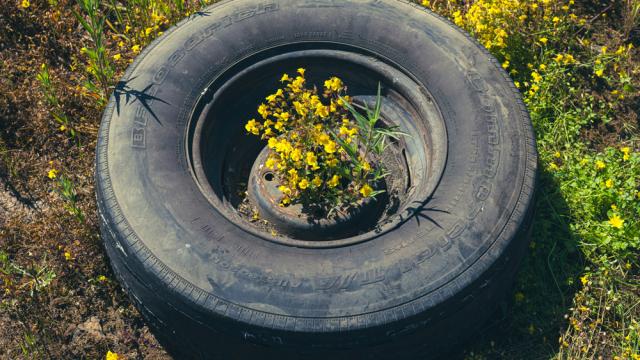
Abheek Chatterjee
Manufacturing is critical to our way of life. Without it, we wouldn’t have the supplies, food, clothing, electronics, and other things we use every day. However, manufacturing also produces waste that often ends up in landfills or oceans.
Looking at natural ecosystems provides a different…
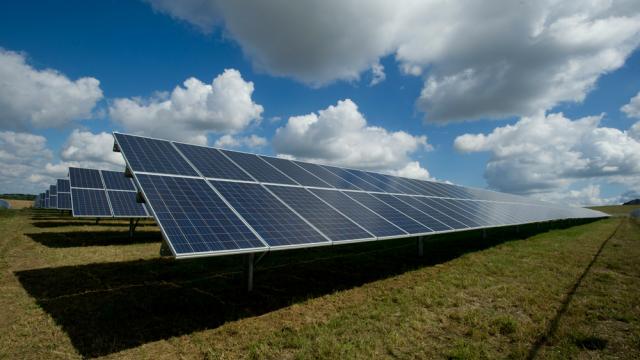
ISO
The clock is ticking. Our planet is heating up, and with every passing day the stakes rise. Wildfires, floods, and storms are no longer distant headlines; they’re unfolding right on our doorstep. Humanity stands at a crucial turning point. But amidst the climate crisis, a powerful ally emerges from…
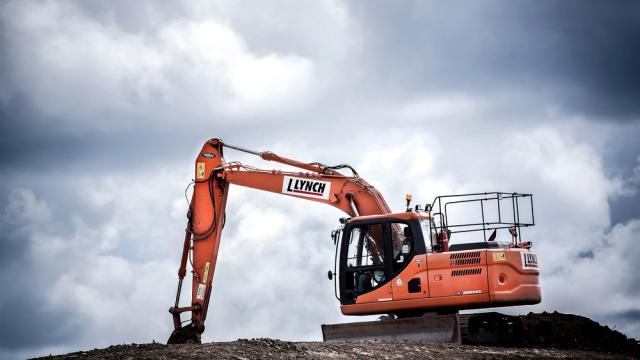
James Chan
Construction is an asset-intensive industry. Companies depend on building equipment, power tools, construction vehicles, and all heavy machinery for essential functions like excavation, construction, and demolition. This equipment must always be kept in safe, proper, and optimal working order so…
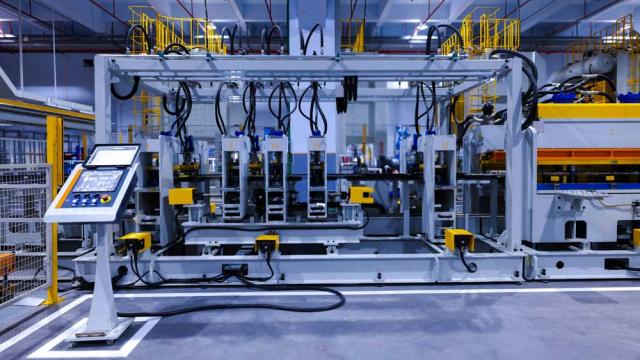
George Thuo
Data breaches and cyberattacks are things that small to medium-size manufacturers think won’t happen to them. Yet, according to the Verizon 2023 Data Breach Investigations Report, 43% of all cyberattacks are conducted against small businesses.
If that doesn’t grab your attention, consider this…
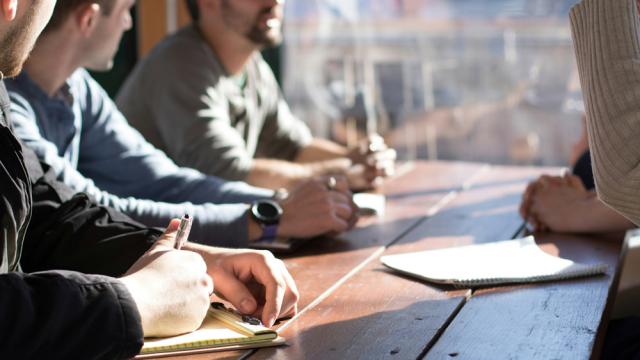
Enoch Li, Derek Deasy
Leadership happens in groups, as does most work. Without followers, who and what are we leading? Given that, leaders must understand what groups need if they want to maximize performance. Although most leaders should be familiar with executive coaching on an individual basis, they might know less…
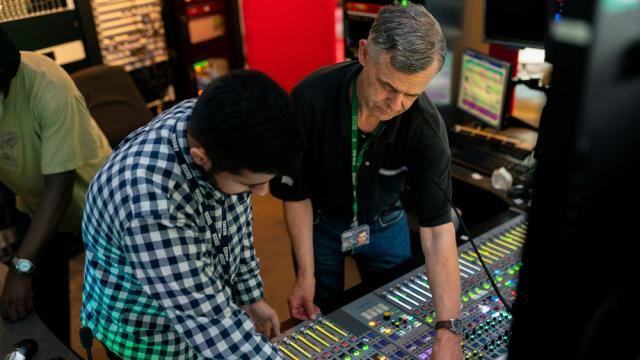
Courtney Kinkade
At a time when Americans already owe more than $1.6 trillion in student loans, and the cost of college continues to rise, some young people are defying the traditional route of a four-year degree. Established professionals looking for a career change aren’t necessarily going back to college.…
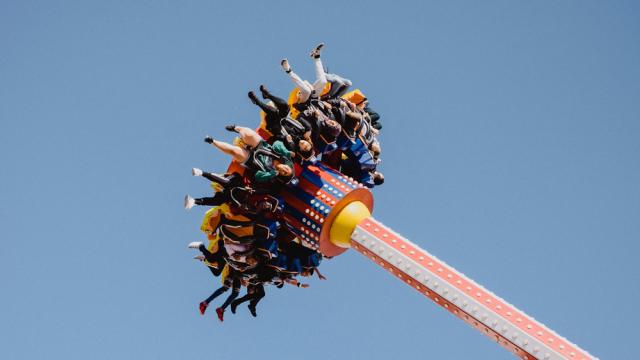
Mike Figliuolo
I recently went to Kings Island amusement park with the kids. Beyond experiencing the thrill of $9 sodas and wicked awesome roller coasters, I learned a few things about professional development while I was there.
Some of you love roller coasters, and some of you hate them. I used to hate them,…
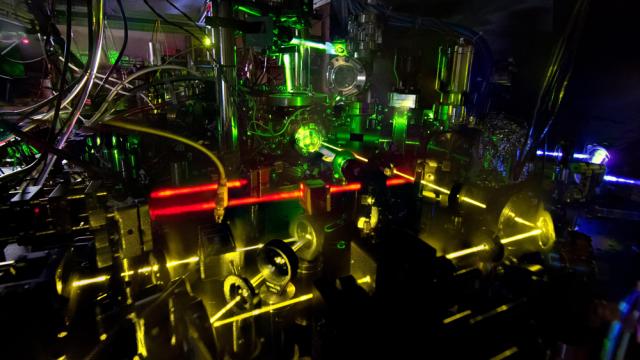
Gabriel Popkin
Time: We all have a sense of it, an innate feel for it. We see it and use it every day. If you’re like me, the first thing you do in the morning is check the time on your phone to see if you need to get out of bed or if you can close your eyes and catch a few more z’s.
Once you’re up and moving,…
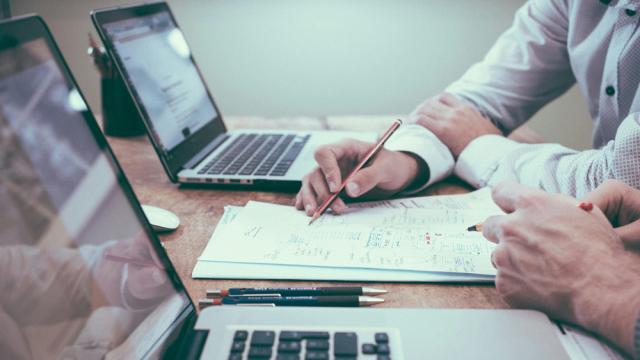
Donald J. Wheeler
An engineer once told me, “I work on project teams that have an average half-life of two weeks, implementing solutions with an average half-life of two weeks.” Time after time, and in place after place, our improvement efforts often fall short of expectations and fade away. In this article, I will…
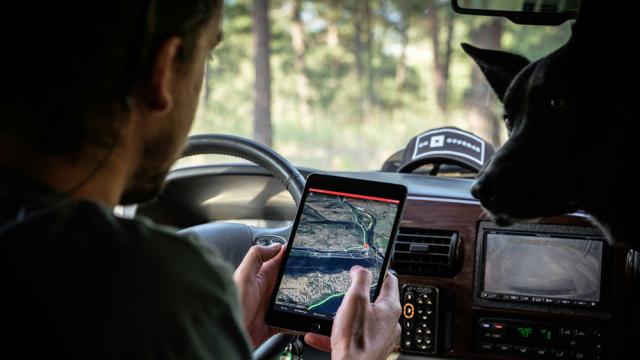
Adam Zewe
Large language models can do impressive things, like write poetry or generate viable computer programs, even though these models are trained to predict words that come next in a piece of text.
Such surprising capabilities can make it seem like the models are implicitly learning general truths…
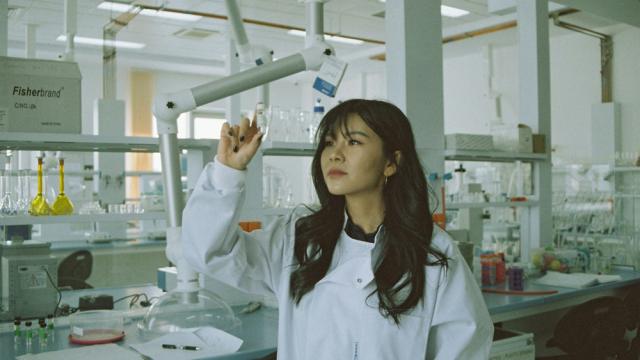
Ronald Cowen
Even before Shamir Maldonado-Rivera graduated from the University of Puerto Rico in 2019 with an applied physics degree, she had already picked out her dream job working with semiconductors.
The only problem was that she lacked the hands-on experience.
Her university studies hadn’t given Maldonado…
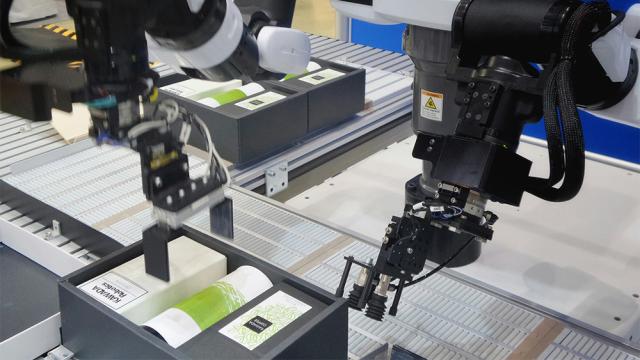
Lauren Priddey
In the process of aerosol filling, precision and safety are crucial, given the complex nature of handling pressurized products and ensuring quality control at every stage. Traditionally, robots have been employed to automate several parts of production. But the introduction of collaborative robots…
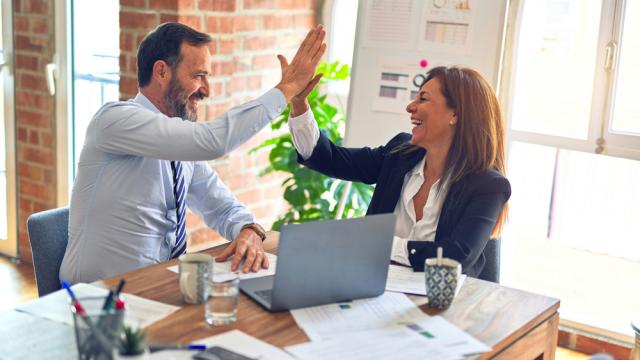
Megan Wallin-Kerth
The opening line on the Systematic QMS website is “Welcome to Systematic Quality Management Systems Inc. Where Service Is Our Passion!”
The warm tone and promise to provide excellent, tailored customer service while delivering a very technical cloud-based quality management system is refreshing…
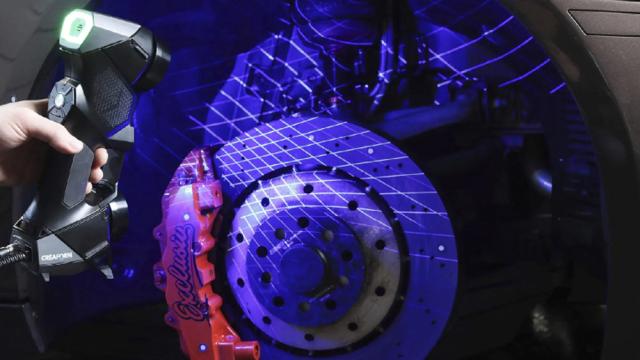
Creaform
In today’s market, it seems like all 3D scanners have similar specifications, as if manufacturers look at their competitors’ data and use the same numbers. Data sheets, marketing videos, and even product appearances all look comparable, making it difficult to distinguish quality based on technical…
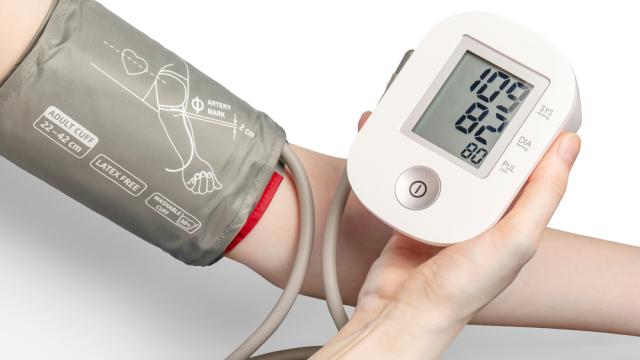
Chris Rush
While clinical trials are the gold standard for generating clinical data to use as evidence of your medical device’s safety and effectiveness, they are by no means the only way to gather clinical evidence.
Real-world data (RWD), which typically come from routine healthcare delivery or…
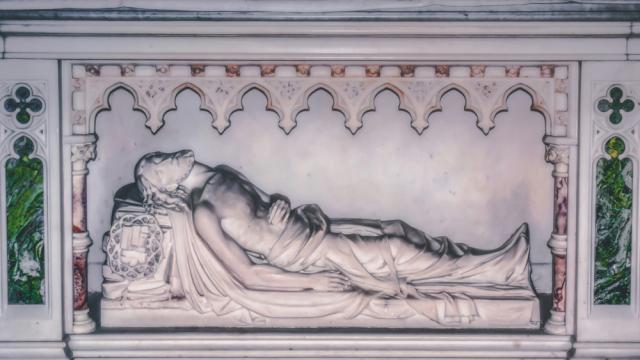
Mike Figliuolo
Leadership is perilous territory. People’s lives are at stake (sometimes literally). Although avoiding the following seven deadly sins won’t guarantee you’ll be a great leader, succumbing to them will guarantee you’ll have a significant learning moment. (Translation: You’ll fail miserably, but…
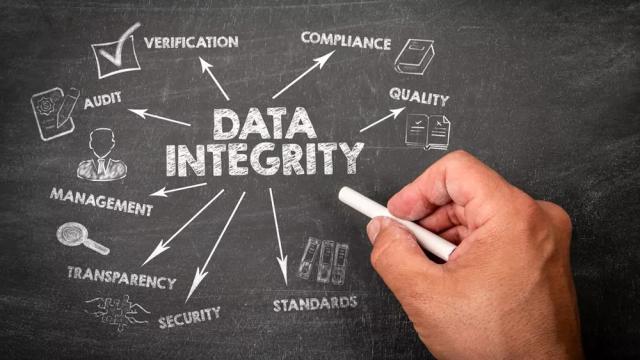
Stephanie Ojeda
In the highly regulated world of life sciences, data integrity isn’t optional; it’s essential. The ALCOA principles—attributable, legible, contemporaneous, original, and accurate—provide a foundational framework for ensuring data are reliable and trustworthy.
With the rise of digital…
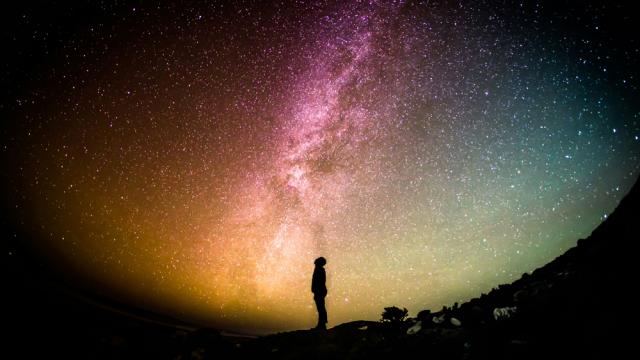
Harish Jose
In this article, I look at the idea of “sweeping-in” in systems approach. Sweeping-in can be described as the process of opening up the inquiry of a system by expanding its boundaries. Philosopher and systems scientist C. West Churchman discussed this process in several works, including Thought and…
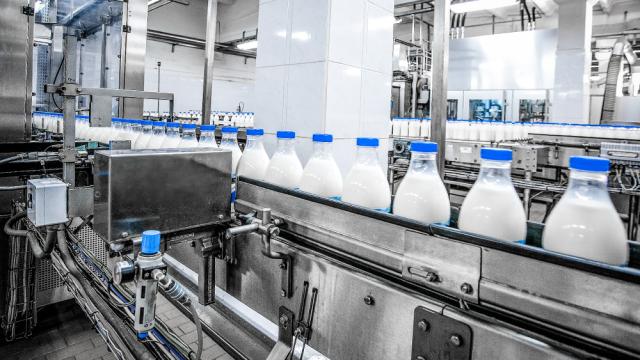
Johan Sjöberg
As dairies scramble to meet sustainability targets ahead of the first year of responding to the European Union Corporate Sustainability Reporting Directive, the significant losses in push-out processes have been identified as low-hanging fruit by many companies.
From 2025, listed companies in the…
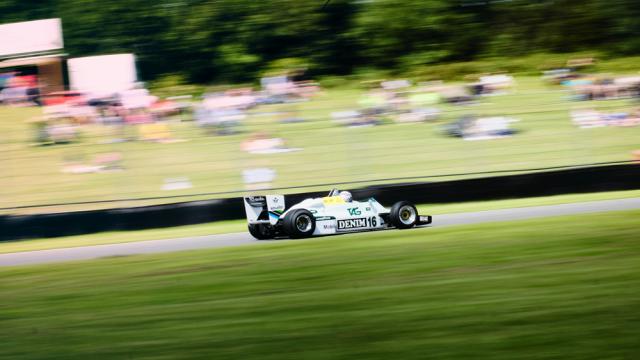
John Tschohl
Speed is one of the most strategic elements a company can use to attract and retain customers and drive its revenues.
What do I mean when I talk about speed? In this context, speed means dramatically reducing the amount of time needed to complete a task by altering factors such as empowerment,…
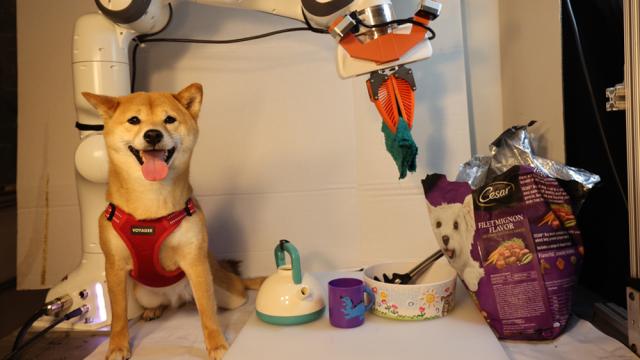
Adam Zewe
In the 1960s cartoon series The Jetsons, Rosie the robotic maid seamlessly switches from vacuuming the house to cooking dinner to taking out the trash. But in real life, training a general-purpose robot remains a major challenge.
Typically, engineers collect data that are specific to a certain…
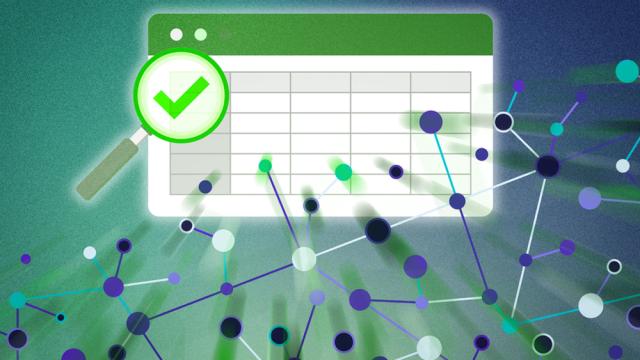
Adam Zewe
Despite their impressive capabilities, large language models (LLMs) are far from perfect. These artificial intelligence models sometimes “hallucinate” by generating incorrect or unsupported information in response to a query.
Due to this hallucination problem, an LLM’s responses are often verified…