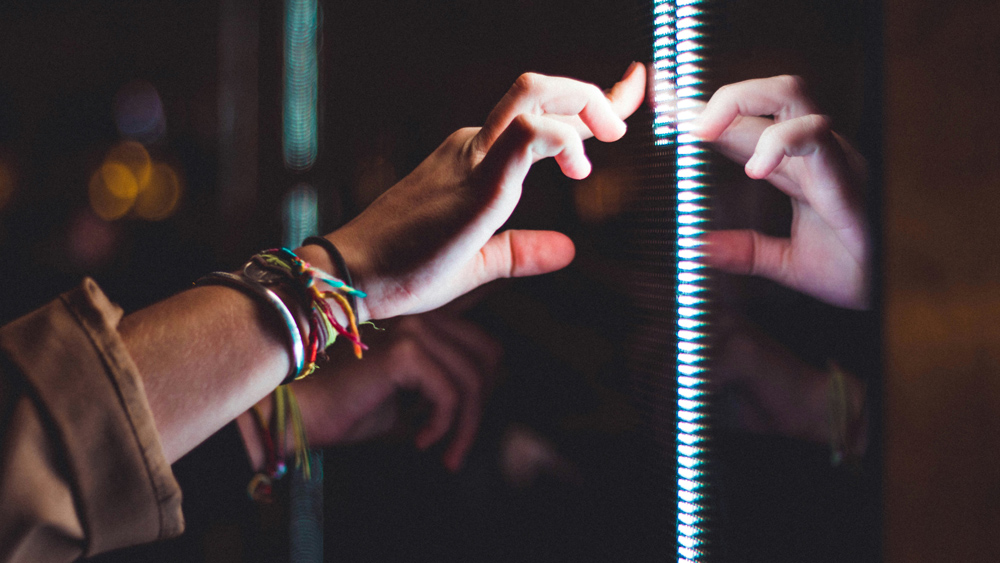
Automated processes, tactile-sensing technology, and other digital solutions can make inspections faster and more cost-effective. Photo by Killian Cartignies on Unsplash.
Metal cold-rolling is a critical process in manufacturing various steel and aluminum products. As manufacturers look for ways to modernize and streamline their manufacturing and quality control processes, digital technologies are poised to transform the metal cold-rolling industry by offering opportunities for improved efficiency, quality, and sustainability.
ADVERTISEMENT |
Ensuring consistency and quality of finished steel or aluminum plates is one of the most significant challenges that metal cold-rolling plants face due to the quality requirements of the demanding industries they serve, such as automotive, aerospace, appliance, and others. Current industry-standard inspection methods often involve dedicated infrastructure, costly equipment, or visual examination of the material, which can be subjective and prone to human error. As a result, each stop on the production line can potentially have a negative effect on the productivity and nonquality costs of a metal cold-rolling facility.
…
Add new comment