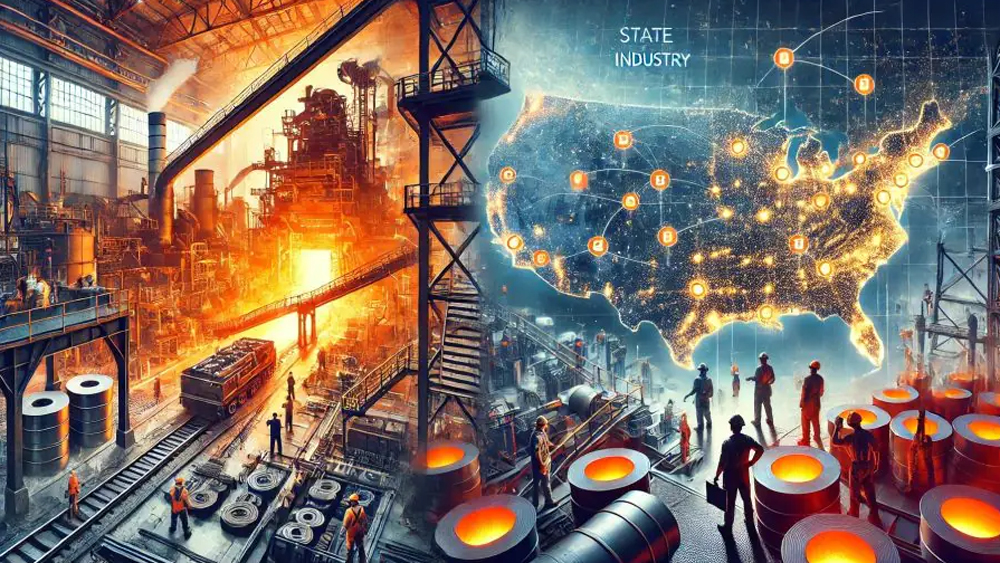
With FABTECH 2024 in Orlando, Florida, fast approaching (Oct. 15–17), many in the steel industry are expected to attend. Some will be part of the manufacturing side of the iron and steel sector, some will be involved in fabrication, and others part of steel service centers.
ADVERTISEMENT |
So, how is the industry doing as a whole as it faces a raft of changes?
• Stiff environmental regulations and responsibilities
• The arrival of artificial intelligence (AI)
• Changes in the U.S. manufacturing sector and supply chain
• Changing availability of materials
Clearly, the steel industry is experiencing a period of disruption. A great many changes have affected prices and product demand. Growth suffered badly during the Covid-19 years. World crude steel production fell badly in 2020, then rose by 4% in 2021.
…
Add new comment