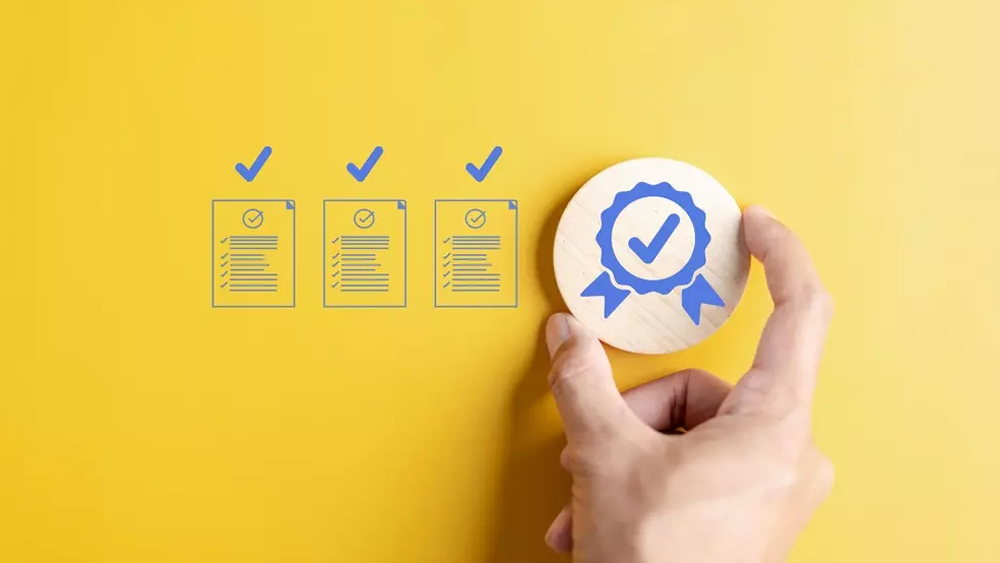
How can a quality manager secure stakeholder engagement and hold individuals accountable for the quality of their work throughout the corrective and preventive action (CAPA) cycle?
ADVERTISEMENT |
With the burden of quality and compliance on their shoulders, it can be tempting for a quality manager to gather information from the necessary stakeholders and then move forward with each stage of the CAPA process on their own.
But the strategy of CAPA in a silo typically backfires as stakeholders see the quality manager as solely responsible for addressing or preventing an issue. More effective is a collaborative approach where stakeholders understand quality is an enterprisewide responsibility, and therefore they must play active roles in the process.
Stakeholders who have “skin in the game,” who work together with the quality manager to provide input on the CAPA process and help carry it through to completion, are more likely to have a sense of ownership.
…
Add new comment