All Features
When your customers’ lives depend on your products, you take extra care in manufacturing each piece.
That’s one reason AO Precision Manufacturing LLC of Daytona Beach, Florida, pays so much attention to quality, says president Stephen Koch.
The Daytona Beach company makes the internal parts…
Measuring the sharp edges of cutting tools is a challenging process, because it involves a small radius, which requires high lateral resolution and high angles. It is also important to be able to measure a diverse range of heights. The study becomes more difficult when the surface has chipping or…
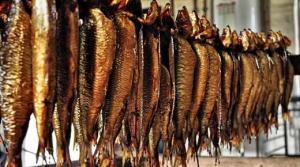
Miriam Boudreaux
The first thing you need to do when you are evaluating a potential supplier based on their ISO 9001 certificate is request that they provide you with a copy of the certificate itself. If the company is indeed certified, they shouldn't have a problem providing you with a copy of their certificate. …
The Un-Comfort Zone With Robert Wilson
In the early 1970s I was a young teenager who was completely caught up in the Zeitgeist. I admired the long-haired rebels and radicals who were engaged in protesting the establishment and developing the counter-culture. I didn’t really know what any of that meant, but to me it was all about…
Steven Ouellette
If you can’t trust your measurement system, you can’t do anything with the data it generates. Last month, in “ Letting You In On a Little Secret,” we talked about the purpose of measurement system analysis (MSA) and I gave you a neat spreadsheet that will do MSA for you, as well as some data (…
Michelle LaBrosse
With the explosion of social media, you’re hearing a lot about personal brands again. Now, the infamous “15 minutes of fame,” coined by Andy Warhol, is a reality for anyone who can upload a video to YouTube or create a blog.
However, as a project manager, when I think of personal brands, I…
Raissa Carey
W
hen I started working on this story, I had an idea in mind. Based on a report that Quality Digest Daily ran in October, “Shifts in Consumer Spending and Saving to Usher in a New Economic Era,” I wanted to investigate whether less consumer spending would, in some way, pose an opportunity for…
Matt Edison
During annual strategy meetings managers use all kinds of statistics, projections, charts, and graphs to support and defend their plans for the upcoming year. Culture, the single biggest determinant in the success or failure of a manager’s plans, rarely, if ever, makes it onto the agenda. Defining…
Angelo Lyall
Story update 1/14/2010: We substituted the word "empathize" for "sympathize."
Many organizations struggle with leadership, often puzzling over why their management techniques don’t seem to induce contribution and collaboration from their associates. The practice of management is separate and…
Michael Raphael
VA Southern Nevada Healthcare System 150-acre campus
Faro Laser Scanner LS scanning room elements
Photo of section of room
3-D scan of same room
In November 2008,…
Paul Scicchitano
If you’re like the vast majority of readers, your company has probably gotten certified to one or more management system standards because someone told you to do so.
While certification is considered to be a cost of doing business these days, companies that invest in becoming certified to a…
Bill Kalmar
Besides penning a column periodically for Quality Digest Daily, I also write for a number of other newspapers and publications. One of those columns for a paper distributed in Michigan and neighboring states is entitled, “Retired… (and lovin’ it).” But here’s the dilemma. The more I talk to people…
H. James Harrington
In the first column of this three-part series, I reviewed an interview that was conducted in 1988 with F. James McDonald, president of General Motors. In this interview he explained what GM was doing to improve quality and customer satisfaction. Typical activities that GM was involved in during…
How unique is unique? The answer to this riddle is central in determining which work breakdown structure (WBS) methodology most accurately explains project deliverables and how they should be estimated, controlled, and completed. The quality strategy used to segregate and decompose WBS…
Bill Kalmar
The year 2009—it was a year to be relegated quickly into obscurity. Nothing seemed to go right. Automotive sales were in the dumper. Home foreclosures continued to be in the news wreaking havoc on millions of people. The health care debate divided the country into vociferous groups in a verbal war…
Donald J. Wheeler
Today virtually everyone uses software to create process behavior charts, yet the available software is notoriously unreliable in terms of the way the limits are computed. This column will explain and illustrate the difference between the correct and some of the incorrect ways of computing three-…
GKS Global Services
The majority of marine vessels in service today do not have digital documentation or CAD models. Despite the fact that vessels currently under construction are designed based on 3-D data, they suffer the same lack of documentation of their true as-built geometries. Due to the inherent inaccuracy…
H. James Harrington
The world is changing so fast today that it is almost impossible to keep up with the latest trends in your own profession. If you are not spending at least two hours per day updating yourself in your chosen profession, you probably are behind the current state of the art. It has been estimated that…
Aditya Bhalla
Every organization today is in a frenzy to innovate and differentiate itself.
A realization seems to have set in that quality and low cost can no longer provide the sustainable advantage. Organizations seem to be increasingly coming around to the idea that conformance to specifications is not…
Mike Micklewright
Can you imagine producing products with a tremendous amount of variation? I’m sure many of you know this all too well. I mean, here you’re trying to produce the same products, trying to ensure consistency, and many of the products you produce have different shades of color, many function…
Jeff Bibee
T
he complex geometries of prosthetics, implants, and specialty medical screws can be measured using typical measurement equipment with only limited success. Prosthetics and implants are becoming more and more complex and delicate. That’s why Stuckenbrock Medizintechnik , in Tuttlingen, Germany…
Georgia Institute of Technology
To improve customer satisfaction, enhance the quality of services and reduce costs, Peach Regional Medical Center has worked with the Georgia Institute of Technology to adopt process improvement techniques traditionally used by the manufacturing industry. Already, Peach Regional Medical Center’s…
Steven Wachs
The purpose of using control charts is to regularly monitor a process so that significant process changes may be detected. These process changes may be a shift in the process average (X-bar) or a change in the amount of variation in the process. The variation observed when the process is operating…
Knowledge at Wharton
The financial services sector has been a laggard in adopting lean tools and practices, perhaps because of their manufacturing origins. But those attitudes are slowly changing. As more banks discover the benefits of lean operations—such as lower costs, fewer errors, faster cycle times and far…
Michael Jovanis
Quality and IT executives alike face increasing pressure to implement technological solutions that allow the highest level of holistic control and oversight concerning the quality of their operations. This pressure is compounded by the current economic climate in which companies face constant…