All Features
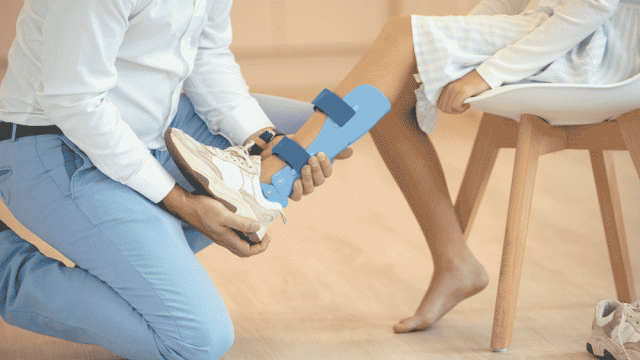
Amy Knue
Health systems across the country are unknowingly paying multiple times for the same medical equipment—once to own it, and again to rent it. The issue isn’t always an increase in clinical demand; it’s often availability and visibility to medical device inventory. The cost of these unnecessary…
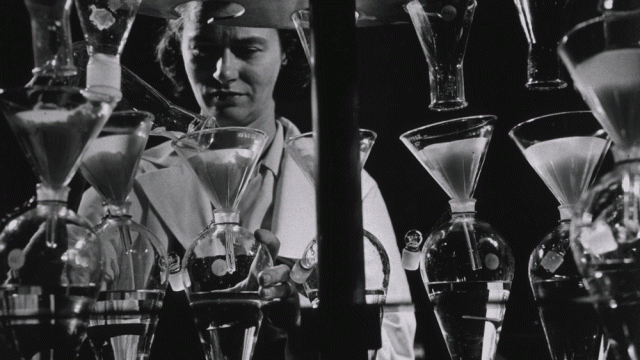
Christa Kuljian
Seven women were part of a trailblazing network of feminist scientists in the Boston area during the 1970s, 1980s, and 1990s.
Christa Kuljian is a science writer and historian of science who focuses much of her research on issues of science and society, gender, and race. She’s the author of two…
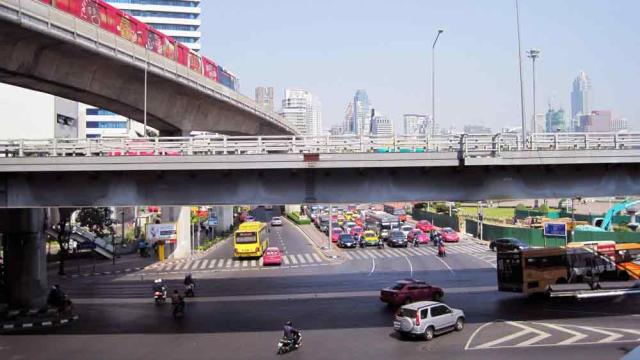
ISO
Gridlocked streets, honking horns, and polluted air—modern city life often feels like a daily battle against time and space. With half the world’s population projected to live in cities by 2050, the pressure on transport systems is reaching a breaking point. Long commutes steal hours from our day,…
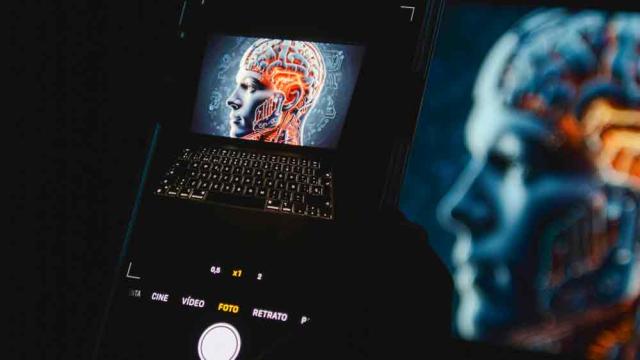
Michael McDowell
As artificial intelligence takes off, how do we efficiently integrate it into our lives and our work? Bridging the gap between promise and practice, Jann Spiess, an associate professor of operations, information, and technology at Stanford Graduate School of Business, explores how algorithms can be…
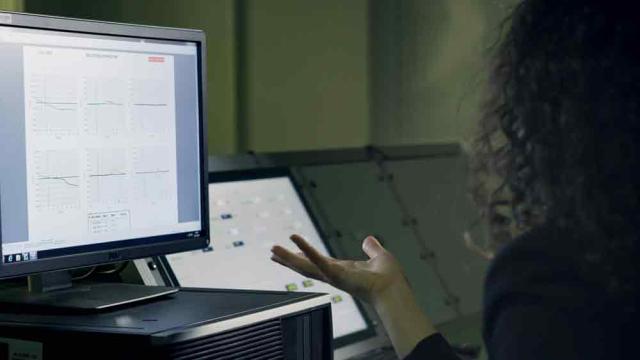
Stephanie Ojeda
Spreadsheets are usually the first tool used to manage suppliers, and the first to become a liability. Important updates get buried. Repeat supplier problems start popping up. Along the way, you start to wonder whether that cheaper vendor is really saving you money in the long run.
The core…
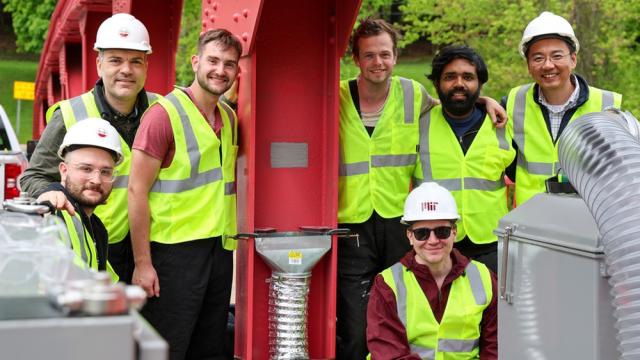
Annie Wilson
More than half of the nation’s 623,218 bridges are showing significant deterioration. Through an in-field case study conducted in western Massachusetts, a team led by the University of Massachusetts at Amherst—in collaboration with researchers from the MIT Department of Mechanical Engineering (…
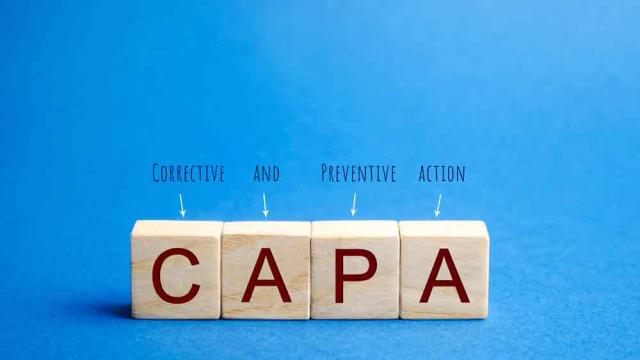
Etienne Nichols
The corrective and preventive action (CAPA) process is one of the most important elements within a medtech company’s quality management system (QMS). The goal of the CAPA system is to identify, address, and prevent systemic issues that could compromise product safety, regulatory compliance, and the…
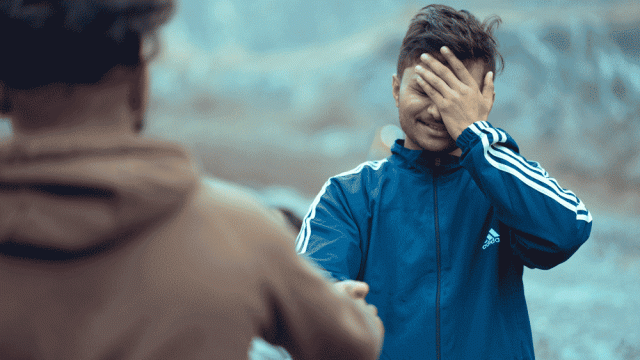
Kate Zabriskie
Ever had that moment when a project seemed crystal clear during a meeting, only to find out weeks later that everyone had completely different interpretations? It’s like playing a grown-up version of the “telephone” game where what starts as “We need this done by the end of the week” ends up being…
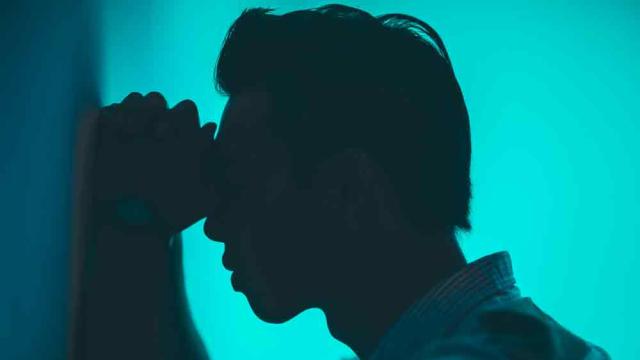
Mike Figliuolo
Most days we walk through life unaware of the conversations occurring around us. And then there are those times you overhear a conversation that stops you dead in your tracks. You have to hit rewind in your brain and ask, “Did they actually just say that?”
Ever have one of those moments? Clearly,…
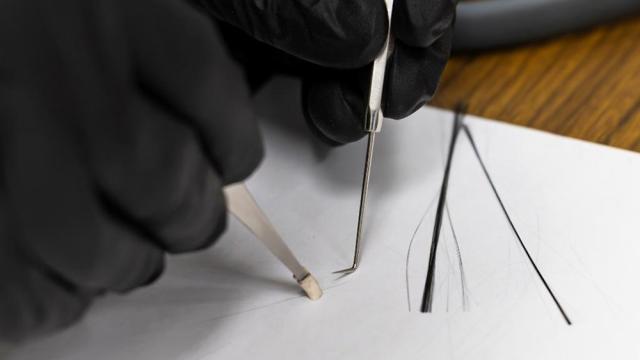
Oak Ridge National Laboratory
Stronger than steel and lighter than aluminum, carbon fiber is a staple in aerospace and high-performance vehicles. Now, scientists at the U.S. Department of Energy’s Oak Ridge National Laboratory have found a way to make it even stronger.
ORNL researchers simulated 5 million atoms to study a …
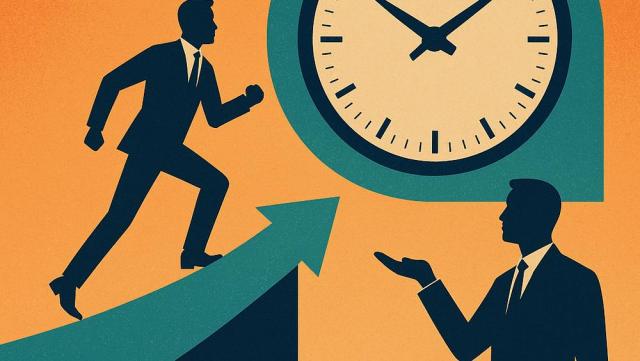
Adam Galinsky, Maurice Schweitzer
Nano Tools for Leaders—a collaboration between Wharton Executive Education and Wharton’s Center for Leadership and Change Management—are fast, effective tools that you can learn and start using in less than 15 minutes, with the potential to significantly affect your success and the engagement and…
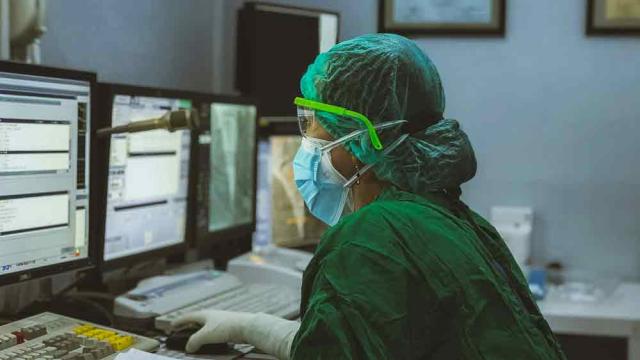
Stephanie Ojeda
Many companies are still clinging to paper-based and unconnected electronic processes, despite the clear disadvantages. Without modern tools like QMS software, these organizations risk compromising product quality, falling behind in compliance, and ultimately losing competitive ground.
In contrast…
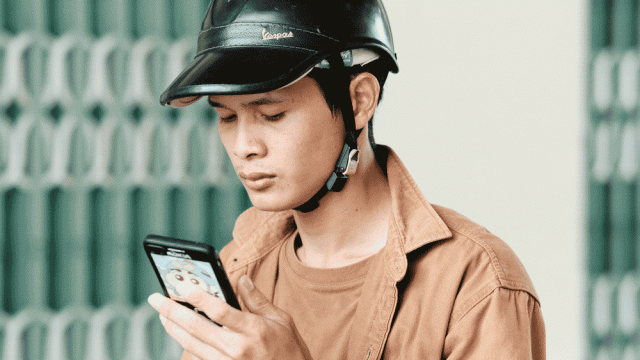
Sanath Hegde
For quality heads, compliance officers, auditors, and engineering leaders, audits have been a time-consuming, resource-intensive process, yet necessary to build resilient operations, prevent costly failures, and maintain competitive advantage.
The question isn’t whether to audit, but how to…
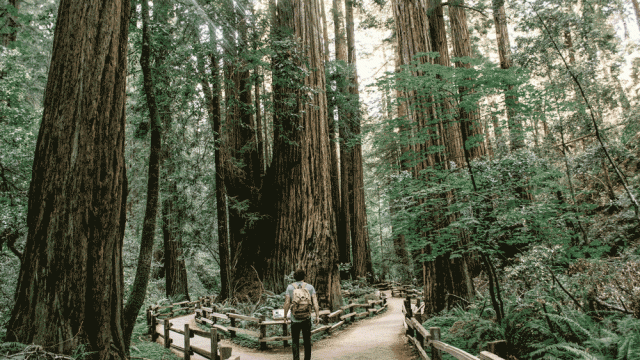
Harish Jose
In this article I’m exploring the need for ethics in systems thinking using the ideas of Heinz von Foerster and Russell Ackoff. The two come from different traditions within systems thinking. Von Foerster comes from physics and second-order cybernetics, and Ackoff from operations research and…
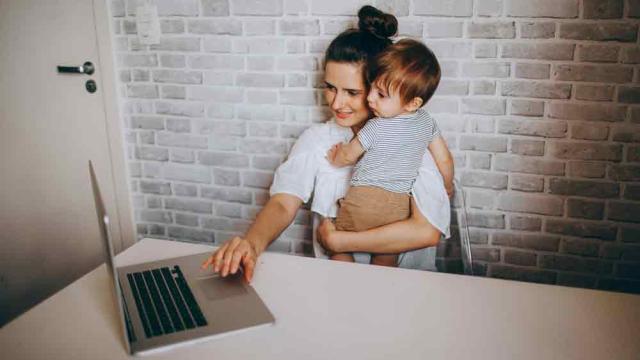
Gleb Tsipursky
As companies and government agencies push forward with return-to-office (RTO) mandates, they risk exacerbating a workplace problem that many have failed to address adequately: gender discrimination.
New research from the University of Toronto’s Rotman School of Management highlights how in-person…
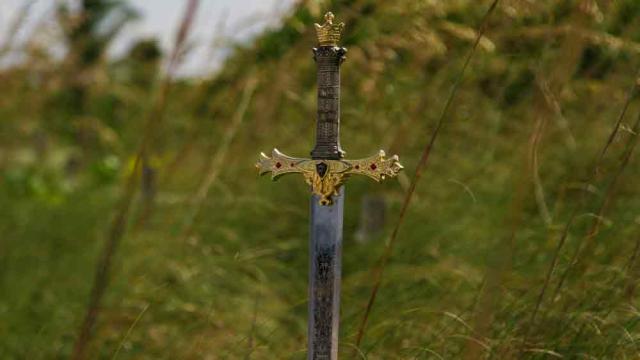
Mike Figliuolo
I love passionate people—people who throw themselves into their work with every last bit of energy they have. To them, everything about their work is important. It’s serious business, and they drive hard to form the world in an image they’re proud of.
However, with passion comes peril. If…
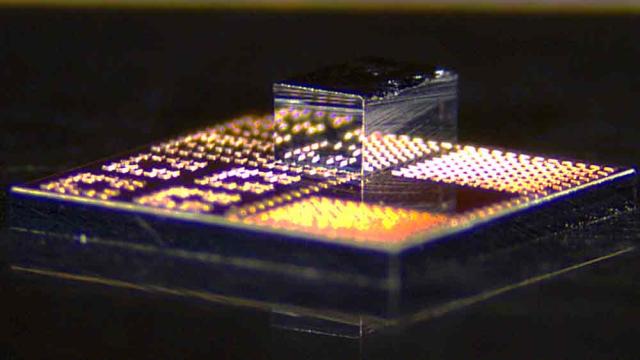
Adam Zewe
The advanced semiconductor material gallium nitride (GaN) will likely be key for the next generation of high-speed communication systems and the power electronics needed for state-of-the-art data centers.
Unfortunately, the high cost of GaN and the specialization required to incorporate this…
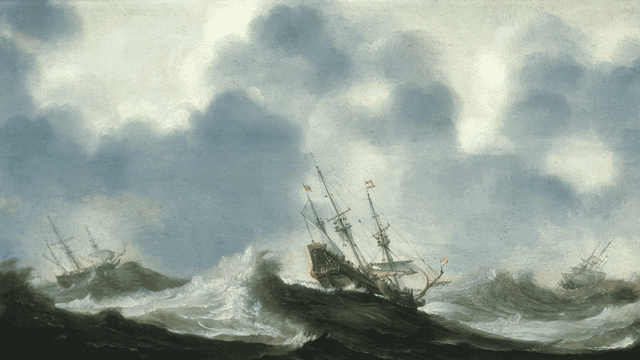
Maartje van Krieken
The storm isn’t coming: It’s already here, and many leaders are realizing they’re sailing without instruments. The current business climate is a storm of volatility, uncertainty, complexity, and ambiguity. Strategic plans become outdated overnight. Decision-making feels like a risk. And yet…
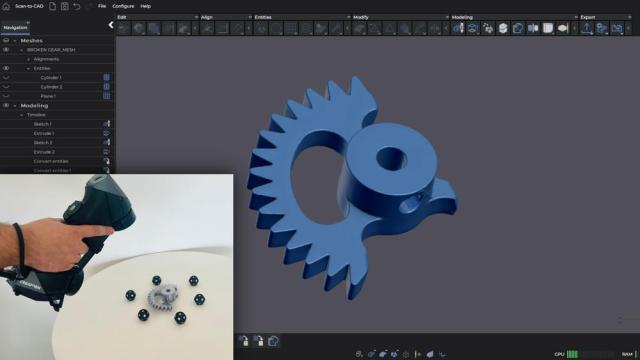
Creaform
Streamlining the transition from scan-to-CAD involves selecting the right tool set for reverse engineering. However, many software platforms force product designers to switch between multiple tools, disrupting their workflow and increasing the risk of errors. Furthermore, some advanced scan-to-CAD…
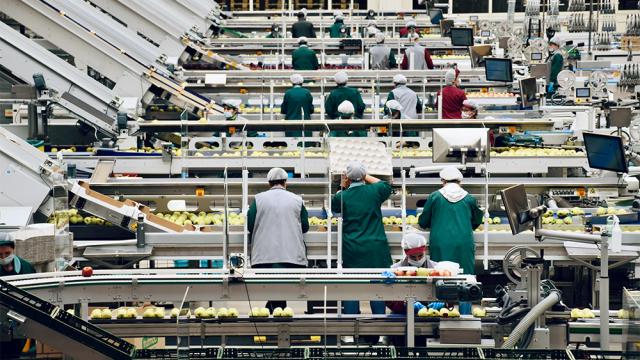
Christoph Dorigatti
When Henry Ford introduced the moving assembly line in 1913, manufacturing changed forever. Today, it stands on the edge of another revolution—one powered by AI, automation, and sustainability. Ford’s innovation paved the way for transformation. Those who embrace the future now will define…
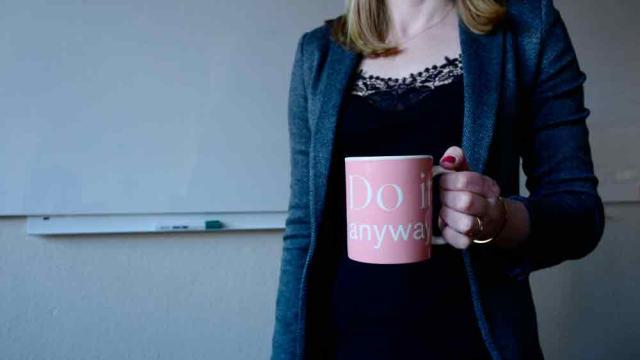
Audrey Kim
As if occupational hazards like “mansplaining” and “he-peating” weren’t bad enough, women in leadership positions often find it hard to get respect. “Women play an unfair game,” says Alison Fragale, a professor at the University of North Carolina’s Kenan-Flagler Business School. “But that doesn’t…
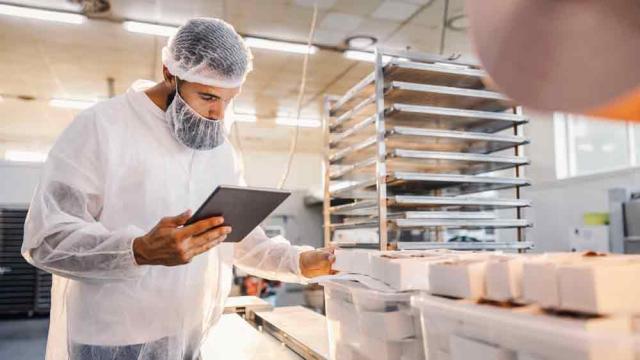
Prasant Prusty, Arundhathy Shabu
A global food safety and quality certification, BRCGS (British Retail Consortium Global Standards) initially focused on food safety but now comprises various sectors such as packaging, consumer products, and retail. It aims to ensure that businesses maintain high standards of safety and quality…
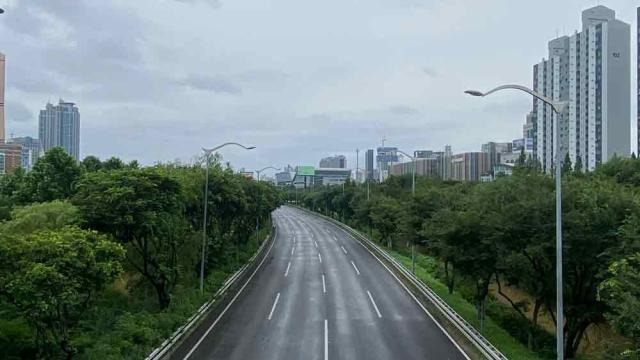
Gleb Tsipursky
The world has shifted in remarkable ways, and flexible work is an undeniable force reshaping professional life. But do remote and hybrid arrangements help the environment or lead to unintended consequences? A new study by Mark Ma at the University of Pittsburgh, Betty Xing at Baylor University, and…
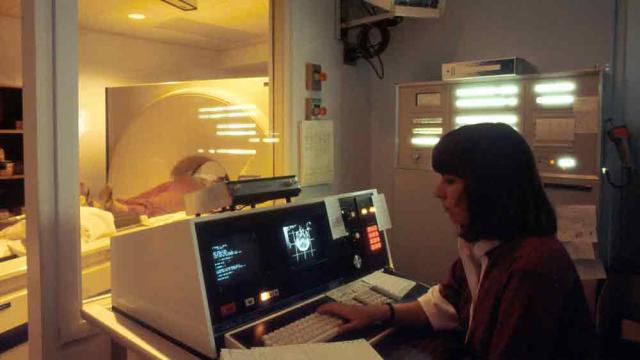
Etienne Nichols
As part of its effort to address the changing landscape around artificial intelligence (AI) in medical devices, the U.S. Food and Drug Administration (FDA) has recently released two new guidance documents on artificial intelligence-enabled device software functions (AI-DSF): • “AI-enabled device…
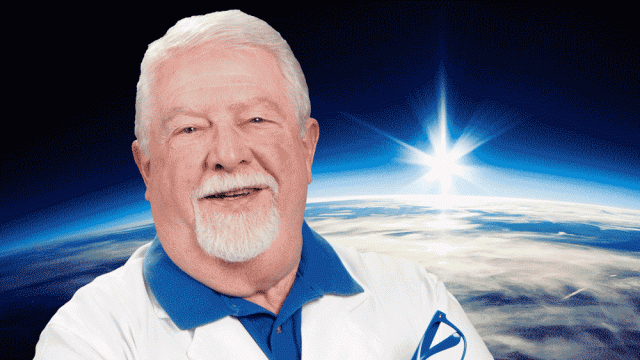
Jeff Dewar, Steven Garner, Quality Digest
Tom Taormina, CMC, esteemed quality consultant and long-time contributor to Quality Digest, has passed away. He is survived by his wife, Midge, and their three children. Recently, Taormina was working with Quality Digest and a consortium of others to design a certified training program for quality…