All Features
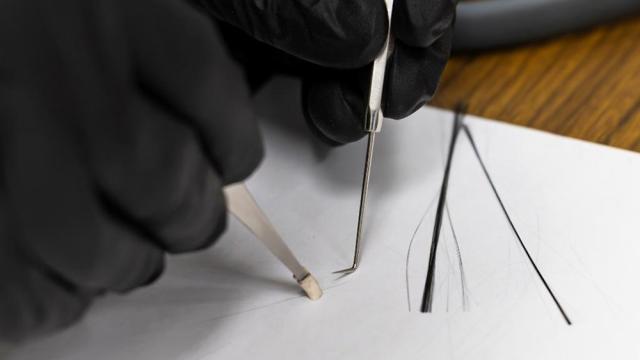
Oak Ridge National Laboratory
Stronger than steel and lighter than aluminum, carbon fiber is a staple in aerospace and high-performance vehicles. Now, scientists at the U.S. Department of Energy’s Oak Ridge National Laboratory have found a way to make it even stronger.
ORNL researchers simulated 5 million atoms to study a …
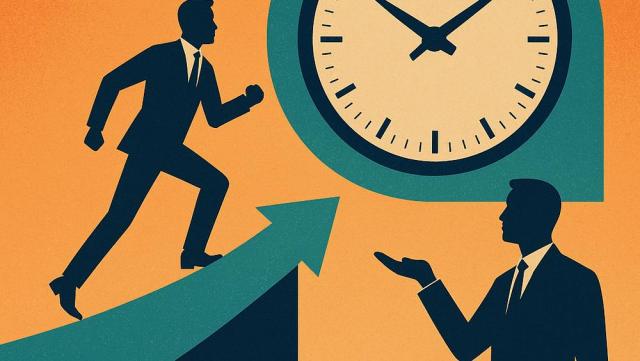
Adam Galinsky, Maurice Schweitzer
Nano Tools for Leaders—a collaboration between Wharton Executive Education and Wharton’s Center for Leadership and Change Management—are fast, effective tools that you can learn and start using in less than 15 minutes, with the potential to significantly affect your success and the engagement and…
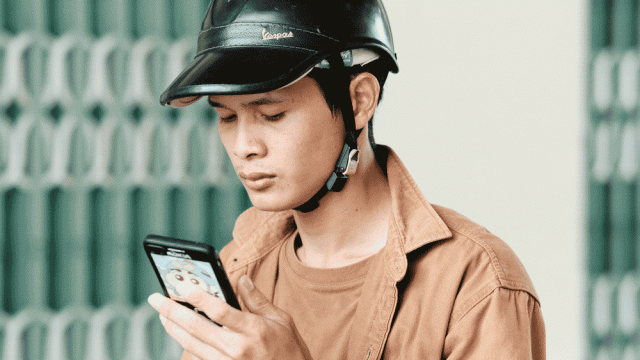
Sanath Hegde
For quality heads, compliance officers, auditors, and engineering leaders, audits have been a time-consuming, resource-intensive process, yet necessary to build resilient operations, prevent costly failures, and maintain competitive advantage.
The question isn’t whether to audit, but how to…
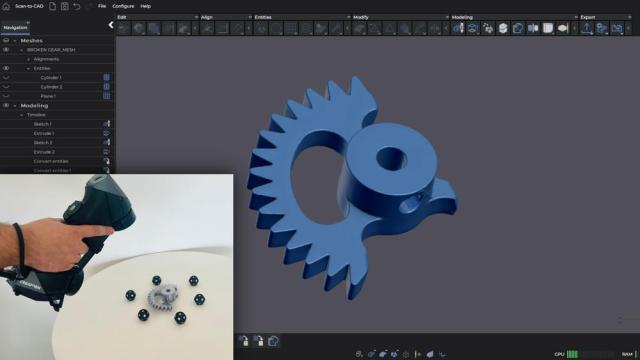
Creaform
Streamlining the transition from scan-to-CAD involves selecting the right tool set for reverse engineering. However, many software platforms force product designers to switch between multiple tools, disrupting their workflow and increasing the risk of errors. Furthermore, some advanced scan-to-CAD…
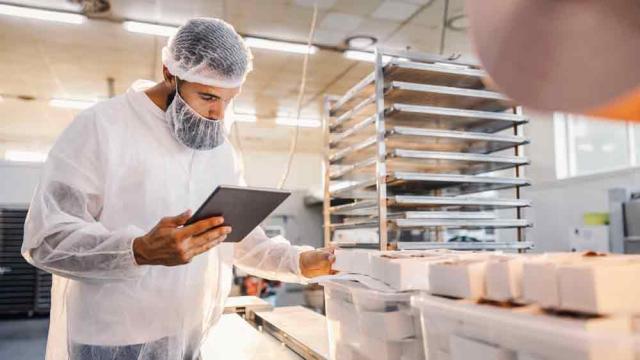
Prasant Prusty, Arundhathy Shabu
A global food safety and quality certification, BRCGS (British Retail Consortium Global Standards) initially focused on food safety but now comprises various sectors such as packaging, consumer products, and retail. It aims to ensure that businesses maintain high standards of safety and quality…
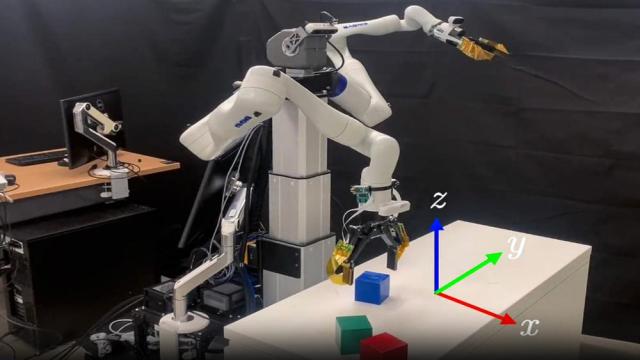
Adam Zewe
Ready for that long-awaited summer vacation? First, you’ll need to pack all items required for your trip into a suitcase, making sure everything fits securely without crushing anything fragile.
Because humans possess strong visual and geometric reasoning skills, this is usually a straightforward…
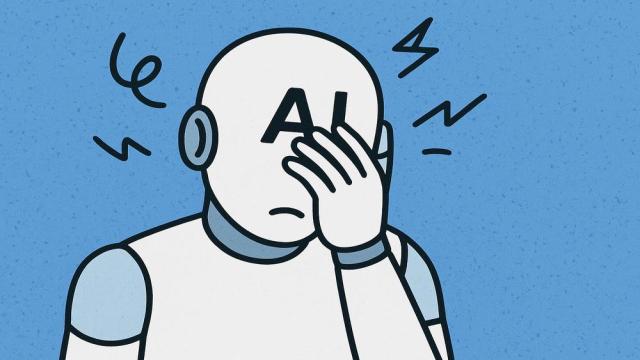
Cornelia C. Walther
On April 8, 2025, a driverless Zoox robotaxi misjudged an approaching vehicle, braked too late, and sideswiped it at 43 mph on the Las Vegas Strip.
One month later, the Amazon subsidiary issued a software recall on 270 autonomous vehicles and suspended operations while regulators investigated the…
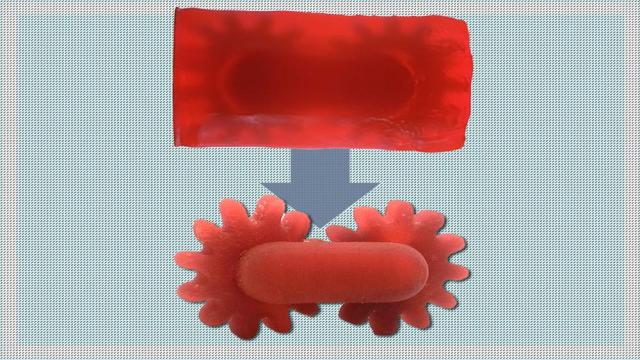
Jennifer Chu
Hearing aids, mouth guards, dental implants, and other highly tailored structures are often products of 3D printing. These structures are typically made via vat photopolymerization—a form of 3D printing that uses patterns of light to shape and solidify a resin, one layer at a time.
The process…
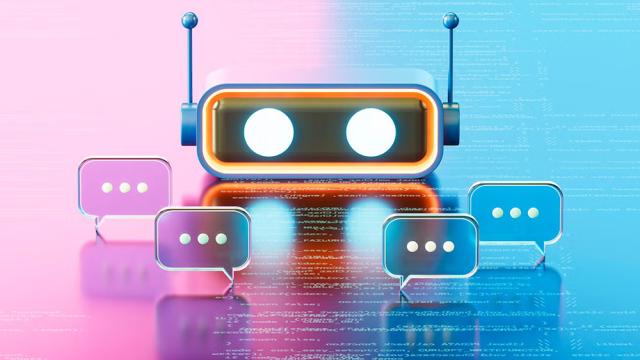
Angie Basiouny
Chatbots are everywhere. A fast-growing communication channel for brands, AI-powered chatbots are being deployed by companies to handle everything from booking travel to refunding purchases to helping shoppers choose the right outfit.
When done right, they can drive sales and provide positive…
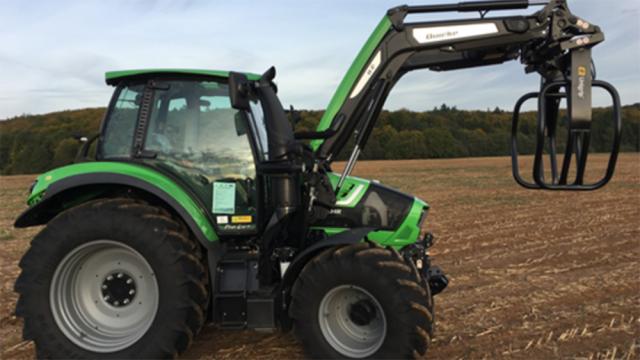
Creaform
Ålö Agricultural Machinery (Ningbo) Co. Ltd., a wholly owned subsidiary of Ålö, is a leading manufacturer of loaders and implements for agricultural tractors.
With production facilities in four countries, and customers in more than 50, Ålö holds approximately 30% of the world market for tractor…
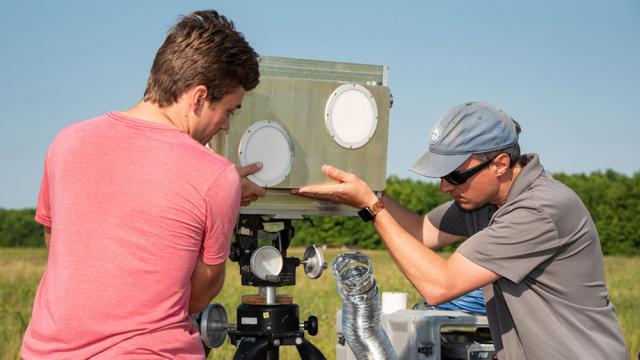
Ariana Tantillo
A team from MIT Lincoln Laboratory has built and demonstrated wide-band selective propagation radar (WiSPR), a system capable of seeing out various distances at millimeter-wave (mmWave or MMW) frequencies. Typically, these high frequencies, which range from 30 to 300 gigahertz (GHz), are employed…
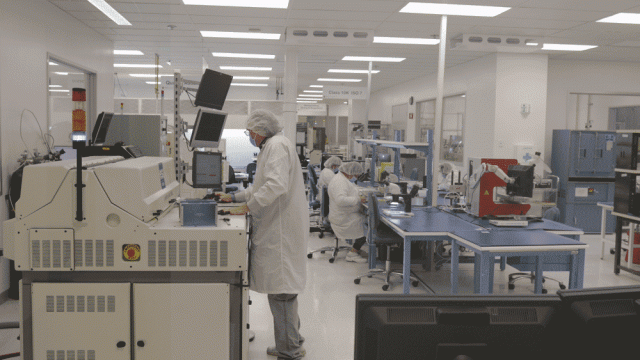
Annette Aquino
To meet the precise requirements associated with semiconductor manufacturing, integrated circuit (IC) packaging and assembly providers must navigate complex quality certification processes, such as those for the well-known ISO 9001 and ISO 13485 standards. Another important certification for…
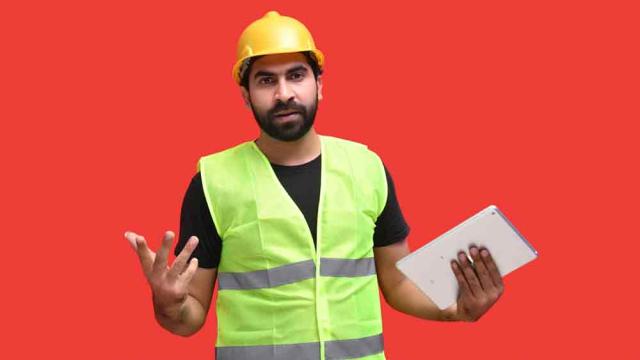
ISO
Occupational health and safety (OHS) is often brushed aside as a checkbox exercise—something assigned to compliance officers or forgotten in day-to-day operations. But this mindset comes at a cost. Every year, millions of people suffer injuries, illnesses, or worse, simply because their workplace…
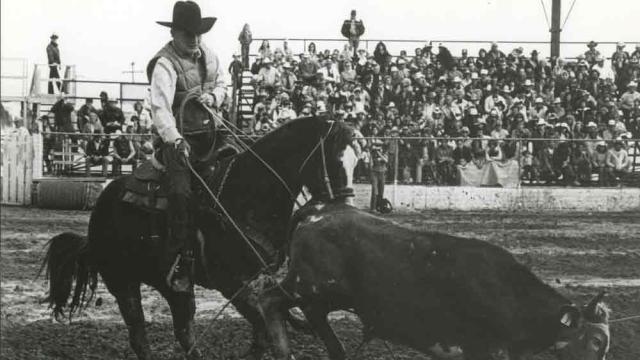
Harry Hertz
A little enjoyment is always important. I recently read a blog post titled 15 Facts That Will Make You Laugh.
A few of those facts were:• There is a Welsh town with a 58-letter name:Llanfairpwllgwyngyllgogerychwyrndrobwllllantysiliogogogoch.• You used to be able to send children by mail in the U.S…
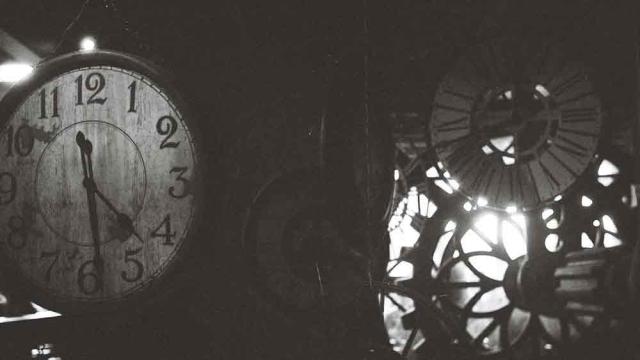
Dr. Scott Davis
Imagine what life would be like without GPS, something you use all the time without thinking about where it came from.
NIST’s atomic clock research helped bring us GPS, which has had more than $1 trillion dollars in economic impact.
This is just one of the many scientific breakthroughs to come out…
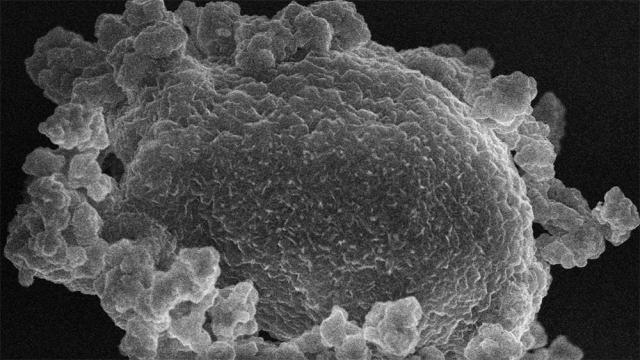
JoAnna Wendel
A common lithium salt has revealed new possibilities for manufacturing cheaper, longer-lasting battery materials.
The discovery centers on sublimation, a commonly known process whereby, under the right conditions, a solid turns directly into a vapor. Sublimation is what creates the tail of a comet…
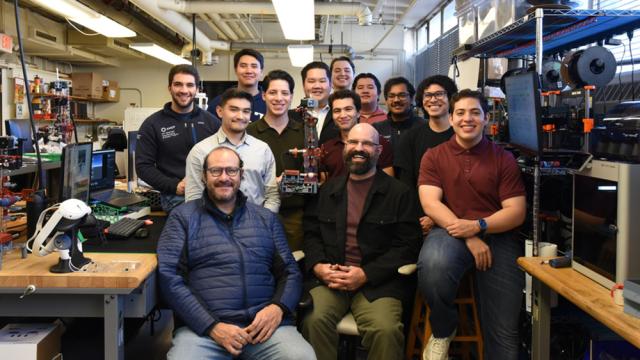
Stefanie Koperniak
For more than a decade through a collaboration managed by MIT.nano, MIT and Tecnológico de Monterrey (Tec), one of the largest universities in Latin America, have worked together to develop innovative academic and research initiatives with a particular focus on nanoscience, nanotechnology, and,…

Creaform
Hawthorne High School of Manufacturing & Engineering in Los Angeles is not your typical high school program. Led by program coordinator Lucas Pacheco, it’s a hub where young minds are immersed in advanced manufacturing and engineering design courses. With a hands-on curriculum covering multi-…
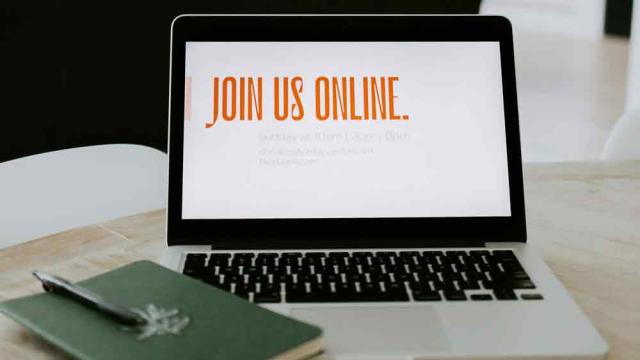
Quality Digest, Donald J. Wheeler
Dr. Donald J. Wheeler has been one of Quality Digest’s most highly read authors for decades. His teaching on the use of control charts in industrial settings has long been considered the gold standard. He has conducted more than 1,100 seminars in 17 countries on six continents, and his books have…
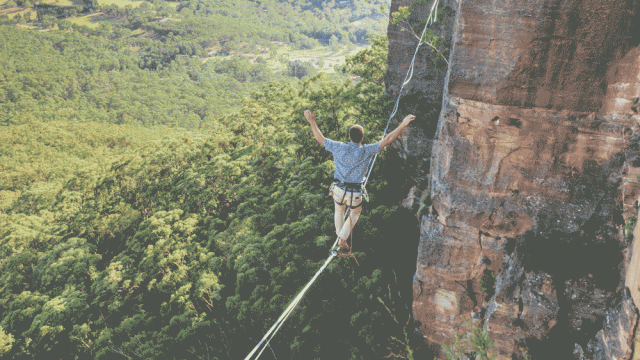
Michael Mills
Risk-based thinking—it sounds easy. How hard can it be to think about risk? But did you know that the phrase “risk-based thinking” was only invented in 2015?
Did you know that the ISO says “risk-based thinking” is one of the foundations of quality management, but never defines it? Or that it…
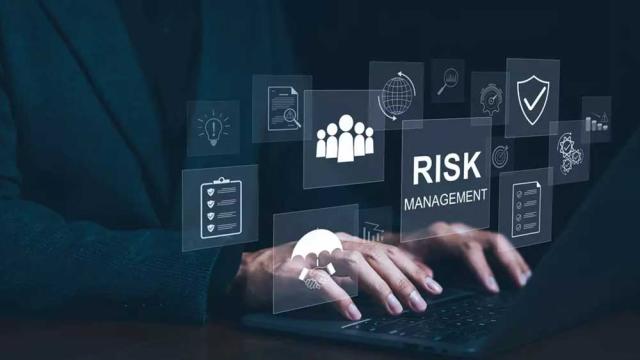
Stephanie Ojeda
Quality risk management (QRM) has become a crucial tool for ensuring regulatory compliance worldwide. It plays a central role in ISO management system standards and regulations, as well as the EU Medical Device Regulation (MDR/IVDR), FDA 21 CFR 820, and ICH Q10 in the pharmaceutical and biotech…
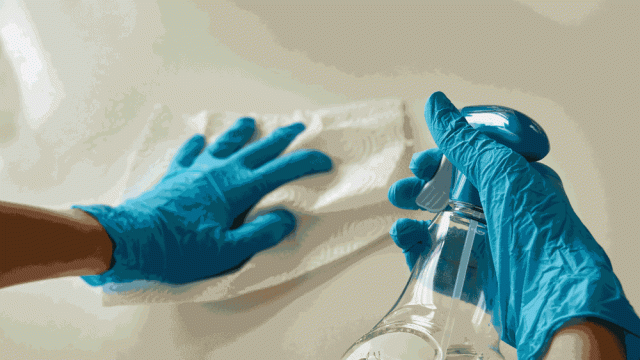
Saurabh Joshi Shripad
Established pharmaceutical facilities play a pivotal role in public health by ensuring the safety and efficacy of the medications they produce. This critical responsibility demands strict adherence to the Code of Federal Regulations, including 21 CFR 211.67—“Equipment cleaning and maintenance,”1,2…
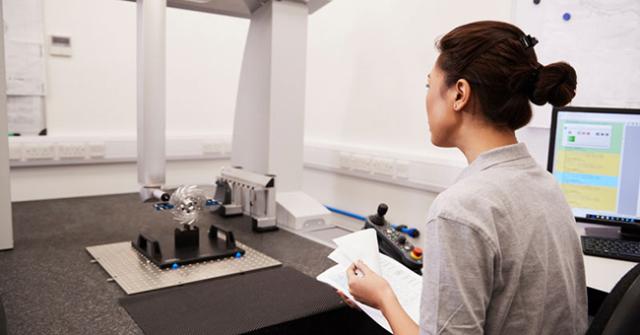
Creaform
Quality control (QC) teams need reliable results they can trust to make informed decisions and address manufacturing challenges. This is why they rely on the coordinate measuring machines (CMMs). However, a CMM’s speed is often a limitation, making the idea that routine quality control can be…
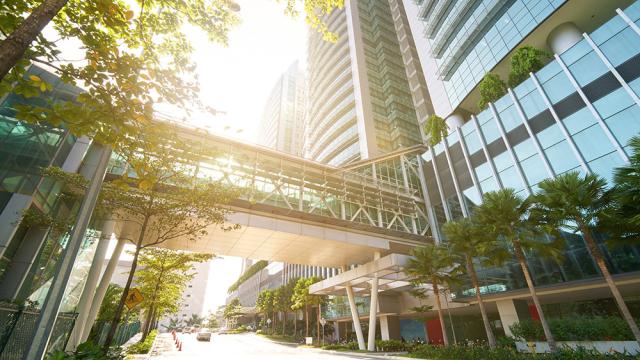
Ben Eidlisz
A safe work environment will foster productivity, reduce hazards, and enhance overall work morale. Keeping your team and assets safe requires implementing the right policies, medical necessities, vigilant oversight, ongoing assessments, and proper training.
As the COO of DUSAW, making smart locks…
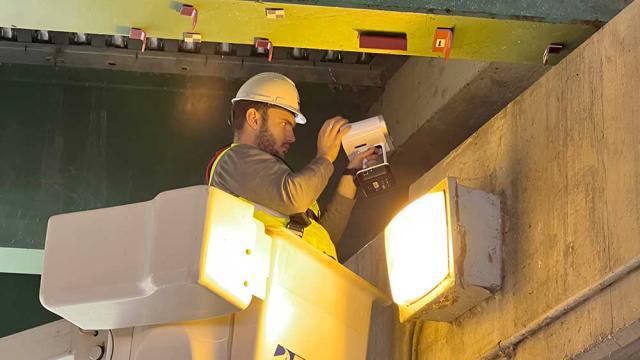
Sergey Sukhovey
The collapse of Baltimore’s Francis Scott Key Bridge in March 2024 was the consequence of a long-standing problem: the fragility of aging infrastructure. As reconstruction gets underway on an estimated four-year timeline, the disaster reflects the urgent need for better bridge inspection nationwide…