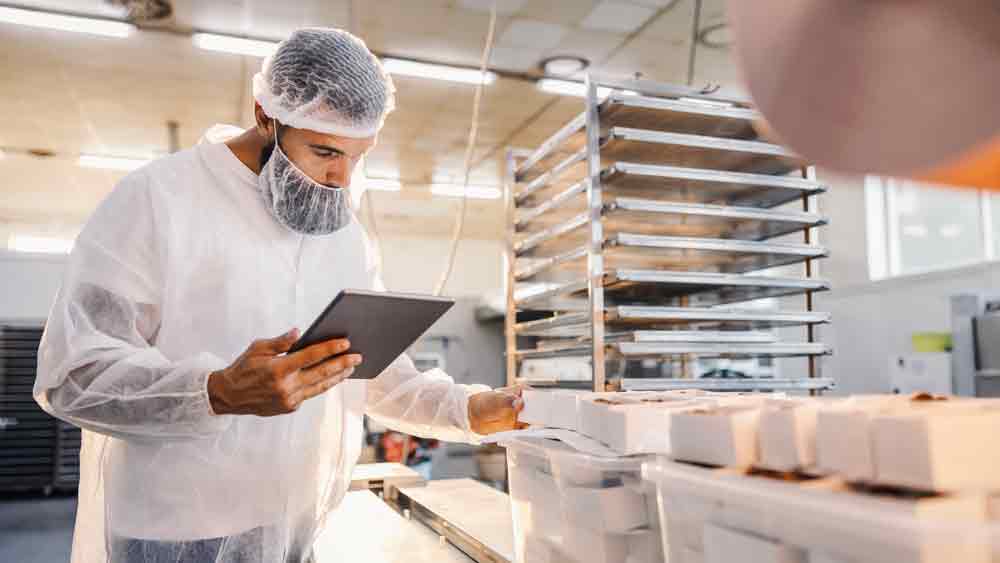
dusanpetkovic / iStock
A global food safety and quality certification, BRCGS (British Retail Consortium Global Standards) initially focused on food safety but now comprises various sectors such as packaging, consumer products, and retail. It aims to ensure that businesses maintain high standards of safety and quality throughout their operations, from production to distribution.
ADVERTISEMENT |
Established in 1996 by the British Retail Consortium (BRC), BRCGS sets benchmarks that help companies maintain the integrity of their supply chains, safeguard consumers, and protect brand reputation. These standards are developed in collaboration with industry experts, retailers, manufacturers, and certification bodies, and are aligned with the Global Food Safety Initiative (GFSI), ensuring global applicability and acceptance.
…
Add new comment