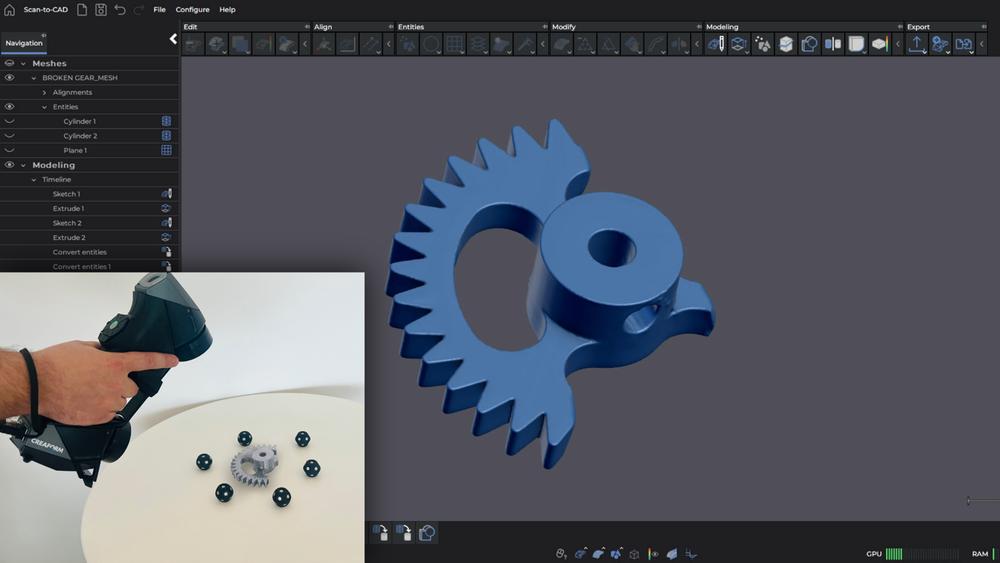
Creaform
Streamlining the transition from scan-to-CAD involves selecting the right tool set for reverse engineering. However, many software platforms force product designers to switch between multiple tools, disrupting their workflow and increasing the risk of errors. Furthermore, some advanced scan-to-CAD tools come with a steep learning curve, which can slow adoption and make reverse engineering less accessible to general users.
ADVERTISEMENT |
What happens when a reverse-engineering process starts with noisy or incomplete data?
Raw scan data (e.g., point clouds or triangular meshes) often contain noise or gaps that must be cleaned or interpolated. Otherwise, poorly processed data can lead to inaccuracies in the CAD model or add unnecessary complexity to the design. When scan data have excessive noise and low resolution, extracting key features—such as planes, cylinders, or holes—becomes more difficult. Product designers must manually re-create these features in CAD software, a process that’s time-consuming and prone to guesswork, approximations, and errors.
…
Add new comment