All Features
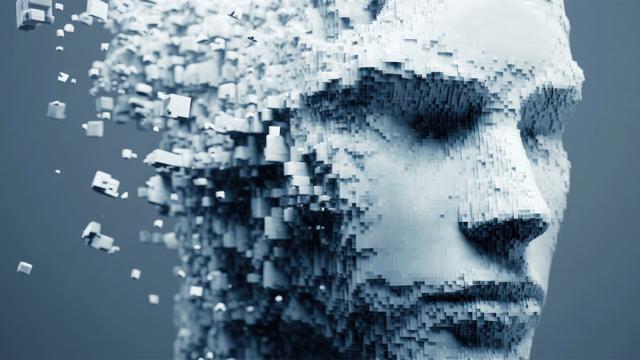
Christopher Dancy
Despite the important and ever-increasing role of artificial intelligence in many parts of modern society, there is very little policy or regulation governing the development and use of AI systems in the United States. Tech companies have largely been left to regulate themselves in this arena,…
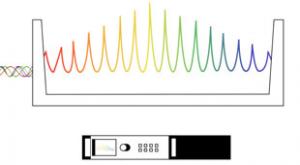
NIST
An improvement to a Nobel Prize-winning technology called a frequency comb enables it to measure light pulse arrival times with greater sensitivity than previously possible—potentially improving measurements of distance along with applications such as precision timing and atmospheric sensing.
The…
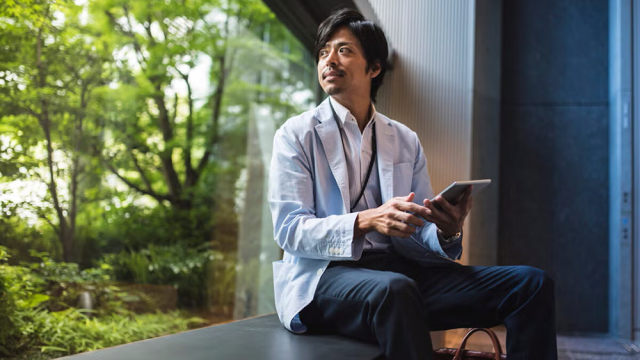
Leeza Garber, Allison Jegla
In late spring 2022, the U.S. Securities and Exchange Commission (SEC) charged an elite investment adviser for “misstatements and omissions” about environmental, social, and governance (ESG) considerations related to its managed mutual funds. This same financial firm has also faced myriad…
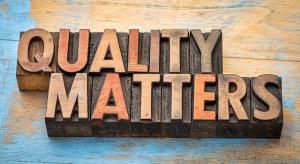
Jeff Dewar
This is the fourth installment of a five-part series.
As detailed in our third installment, ASQE is a new legal entity connected to the ASQ we all know and love. It’s a trade organization to which organizations, rather than individuals, can belong. Current membership is about 180 organizations,…
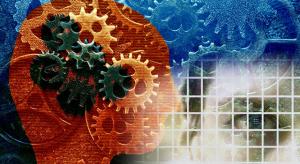
Dirk Dusharme @ Quality Digest
Every company wants to succeed, but not all can say they meet the current requirements to do that. More than a focus on capital, business plans, or staff, a successful business in 2022 must operate digitally. Yet for the 45 percent of small and medium-sized businesses (SMBs) that still rely on…
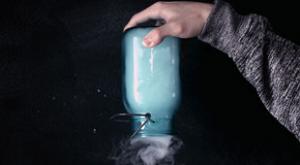
David Isaacson
In 1982, when asked about the state of the company’s Xenix operating system, a Microsoft engineer reportedly called it “vaporware“ to indicate that the operating system had really not yet materialized. Unfortunately, the term stuck for this and many other premature software launches.
It’s not only…
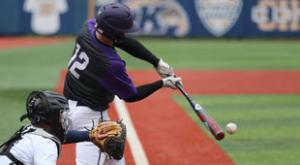
Mark Hembree
‘Anyone can hit a home run if they try,” said the great Ty Cobb at the end of the deadball era as Babe Ruth rose to fame in the 1920s. Cobb was unimpressed by Ruth, the Sultan of Swat. “It’s a brute way to approach the game.”
In 2019, Major League Baseball (MLB) seemed to prove Cobb’s point as big…
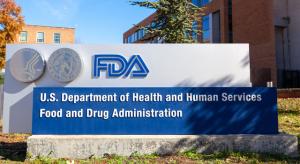
Grant Ramaley
The FDA Quality System Regulation (QSR) 21 CFR Part 820 was written in 1997 to harmonize with ISO 13485:1996. The goal was to relieve some of the burden of manufacturers having to meet two different criteria, the FDA’s and ISO 13485.
But by 2003, ISO 13485 had changed so significantly that the FDA…
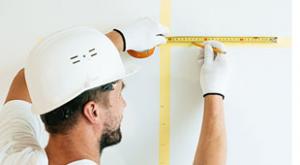
NIST
You need to measure length accurately to do things like make a dress, build a house, survey a plot of land, or determine if the home team made a first down on the football field. These length measurements and many others are often made with the help of a measuring tape. The major companies that…
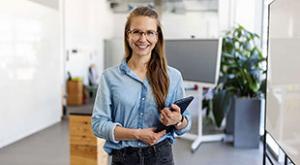
ISO
Standards are not for just the minority of businesses with thousands of employees. According to the World Bank, micro, small, and medium-sized enterprises (MSMEs) make up more than 90 percent of all companies and account for up to 70 percent of total employment. In developing countries, small…
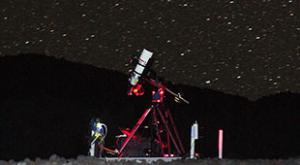
Steven Brown
One of the unexpected rewards of working at NIST has been the opportunity to see other disciplines through the NIST prism of measurement science and standards. By working with NASA scientists, astronomers, oceanographers and geologists, I’ve had the opportunity to witness the lives of scientists in…
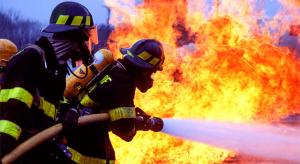
Kath Lockett
‘Firefighters are heroes.” We hear it all the time, from children, the media, and young people looking for a rewarding career. It’s probably something you’ve said or thought yourself at one time or another. These brave men and women put their own safety on the line every day to protect their…
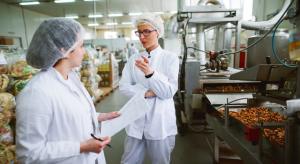
Ann Brady
Safer food, better health: This was the theme of World Food Safety Day (June 7, 2022), and it’s obvious, is it not, that access to safe food is vital for life and health? The challenge in today’s world is how to achieve this. Global food systems, already under pressure before the pandemic, are now…
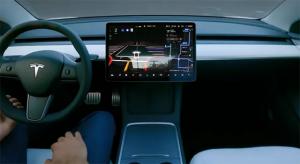
Hayder Radha
It’s hard to miss the flashing lights of fire engines, ambulances, and police cars ahead of you when you’re driving down the road. But in at least 11 cases from January 2018 to July 2021, Tesla’s Autopilot advanced driver-assistance system did just that. This led to 11 accidents in which Teslas…
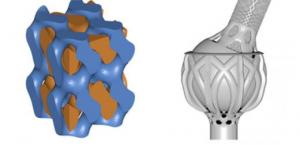
Jonathan Griffin
Since the 1940s, engineers have used a common design language—a set of definitions, symbols, and practices—to draft engineering drawings that can serve as clear manufacturing blueprints or inspection checklists.
Although this system still works well for many traditional manufacturing methods, it…
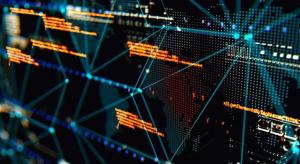
Lily Chen, Matthew Scholl
In our connected, digital world, cryptographic algorithms are implemented in every device and applied to every link to protect information in transmission and in storage. During the past 50 years, the use of cryptographic tools has expanded dramatically, from limited environments like ATM…
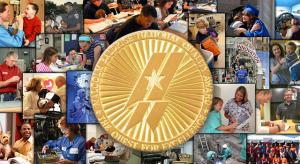
In an open letter, Bob Fangmeyer, director of the Baldrige Performance Excellence Program, wrote that the Baldridge Award process would be suspended this year. The reasons and future plans are outlined in the letter shown below.
Dear Friend of Baldrige,
I am writing today to provide an important…
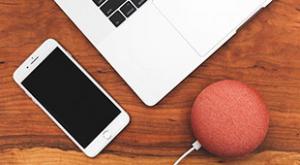
NIST
Smart sensors play a critical role in smart grids, supporting bidirectional flows of energy. Such sensors are needed for real-time monitoring of energy flow; controlling power generation, transmission, and distribution to customers; and protecting the overall power systems.
However, the…
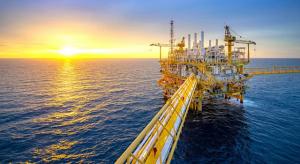
Marc Lepere
As the war in Ukraine rages, finance professionals on Wall Street and in Europe recently attracted outrage by suggesting that investing in arms manufacturers should be treated as ethical investing. In the fight against tyranny, they argued that such an investment “preserves peace and global…
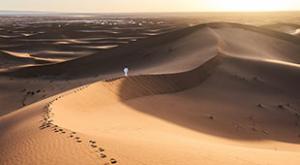
ISO
After lengthy wrangling, the 2021 COP26 climate summit ended with 197 parties agreeing to the new Glasgow Climate Pact. It will get countries to strengthen their CO2 emissions-cutting targets for 2030 by the end of next year, and formally recognize the need to reduce global greenhouse gas emissions…
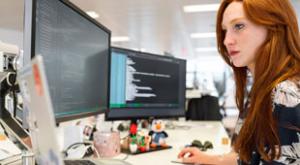
Wade Schroeder
On May 12, 2021, President Biden signed the Executive Order on Improving the Nation’s Cybersecurity. Among other items in the order was a requirement that every vendor that supplies the federal government with software must provide a software bill of materials (SBOM) with their product.
Given that…
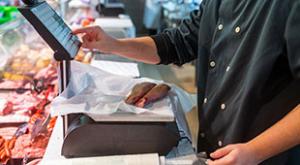
NIST
Whether it’s bananas, olives, potato salad, or cereal, many products are priced according to their weight. That weight is likely determined on a scale tested and certified by a specially trained state or local inspector. Weights and measures underpin approximately half of the United States gross…
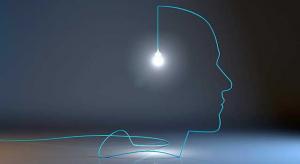
Barnaby Lewis
Harran blinks in the sunlight, adjusting his eyes. He’s an inquisitive child, enthusiastic for all things new, yet still he struggles to understand what he’s looking at. A man is pressing marks—triangles or wedges—into a piece of clay, explaining that in this way he can speak to people, even when…
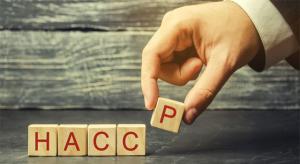
Bill Marler
Although the announcement, “FDA Proposes Changes to Food Safety Modernization Act Rule to Enhance Safety of Agricultural Water Used on Produce,” is a bit to fully digest in one sitting, I’m intrigued by the FDA’s focus on pre-harvest risk assessment of water risk as opposed to water testing for…
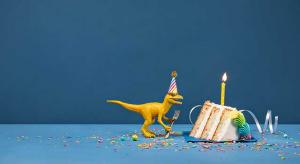
Mike Richman
It’s hard to fathom that Quality Digest, a little Northern California media company respected by all and beloved by many, turned 40 in November 2021. For a human being, 40 may be the new 30, but it’s still just creeping up on middle age. For a small business, on the other hand, 40 years is…