All Features
Tom Pyzdek
While we work to improve quality and efficiency, our leaders manage our organizations into oblivion. Literally. Something is terribly wrong. Leaders of major corporations in virtually all industries do things that cause them to, either accidentally or deliberately, destroy billions of dollars in…
Denis Leonard
A key aspect of quality management is the importance we place on employees, i.e., valuing people. We spend a significant amount of time and money officially sending this message to our team, espousing this pillar of quality. Yet, while doing this, we often directly contradict this by sending a…
Jane Martinsons
With or without health care reform, health care quality professionals know that change is already a new reality for U.S. health care, transforming the industry, their own organizations, and their professional roles on what seems a daily basis.
“With all the changes that we’re facing in health…
Jennifer Sprance
The molecular diagnostics industry is a relatively new territory that offers much promise for early disease detection and personalized patient care. When analyzing samples at the molecular level, there are serious consequences for errors, and tests must be highly accurate and precise. For example…
Steve Moore
The purpose of this article is to give you an appreciation of the Quincunx as an educational tool for teaching some of the theory behind the tools and concepts of so-called modern quality management. The Quincunx is often seen in the possession of organizations practicing in-house education of…
Florence Stone
Problem solving can take up a lot of managerial time. So it makes sense for you to resolve problems before they develop, let alone grow to affect the bottom line. As a manager, you practice preventive management for just this reason. You understand how problems often can be identified in their…
Dan Adams
If you’re like most business-to-business (B2B) suppliers, you’re probably making certain predictable mistakes that can greatly affect your ability to compete. Unless your company has smarter employees, some inherent unassailable advantage, or a markedly different approach to satisfying customers,…
Konica Minolta Sensing Americas Inc.
Alfred Kärcher GmbH & Co. KG is a global leader in the field of cleaning technology. Their innovative cleaning products are manufactured in Baden-Württemberg, continuously improved, efficiently marketed and have provided the company with continuous, organic growth. Today, almost 60 years after…
Reishauer AG is a company with a long tradition in the gear industry. Reishauer’s products range from tooth profile grinding machines, to diamond and CBN tools, which the company exports to industrial states throughout the world. Teeth on gears with a diameter of 150 mm to 1,000 mm are given their…
Bill Kalmar
Most of us, I suspect are familiar with the phrase, “Dog Days of Summer,” meaning the hottest, most sultry days of summer, typically early July through early September. Sometimes the time frame is defined as a dull lack of progress.
To the best of my knowledge, there is not a similar event in…
Dong-Yea Sheu
This article describes a novel, integrated micromanufacturing process utilizing a combination of wire electro discharge grinding (WEDG) technology and one-pulse electro discharge (OPED) to fabricate microspherical stylus tips for microcoordinate measuring machines (μCMM). With an optimal selection…
When your customers’ lives depend on your products, you take extra care in manufacturing each piece.
That’s one reason AO Precision Manufacturing LLC of Daytona Beach, Florida, pays so much attention to quality, says president Stephen Koch.
The Daytona Beach company makes the internal parts…
Measuring the sharp edges of cutting tools is a challenging process, because it involves a small radius, which requires high lateral resolution and high angles. It is also important to be able to measure a diverse range of heights. The study becomes more difficult when the surface has chipping or…
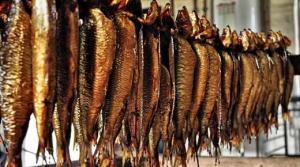
Miriam Boudreaux
The first thing you need to do when you are evaluating a potential supplier based on their ISO 9001 certificate is request that they provide you with a copy of the certificate itself. If the company is indeed certified, they shouldn't have a problem providing you with a copy of their certificate. …
The Un-Comfort Zone With Robert Wilson
In the early 1970s I was a young teenager who was completely caught up in the Zeitgeist. I admired the long-haired rebels and radicals who were engaged in protesting the establishment and developing the counter-culture. I didn’t really know what any of that meant, but to me it was all about…
Steven Ouellette
If you can’t trust your measurement system, you can’t do anything with the data it generates. Last month, in “ Letting You In On a Little Secret,” we talked about the purpose of measurement system analysis (MSA) and I gave you a neat spreadsheet that will do MSA for you, as well as some data (…
Michelle LaBrosse
With the explosion of social media, you’re hearing a lot about personal brands again. Now, the infamous “15 minutes of fame,” coined by Andy Warhol, is a reality for anyone who can upload a video to YouTube or create a blog.
However, as a project manager, when I think of personal brands, I…
Raissa Carey
W
hen I started working on this story, I had an idea in mind. Based on a report that Quality Digest Daily ran in October, “Shifts in Consumer Spending and Saving to Usher in a New Economic Era,” I wanted to investigate whether less consumer spending would, in some way, pose an opportunity for…
Matt Edison
During annual strategy meetings managers use all kinds of statistics, projections, charts, and graphs to support and defend their plans for the upcoming year. Culture, the single biggest determinant in the success or failure of a manager’s plans, rarely, if ever, makes it onto the agenda. Defining…
Angelo Lyall
Story update 1/14/2010: We substituted the word "empathize" for "sympathize."
Many organizations struggle with leadership, often puzzling over why their management techniques don’t seem to induce contribution and collaboration from their associates. The practice of management is separate and…
Michael Raphael
VA Southern Nevada Healthcare System 150-acre campus
Faro Laser Scanner LS scanning room elements
Photo of section of room
3-D scan of same room
In November 2008,…
Paul Scicchitano
If you’re like the vast majority of readers, your company has probably gotten certified to one or more management system standards because someone told you to do so.
While certification is considered to be a cost of doing business these days, companies that invest in becoming certified to a…
Bill Kalmar
Besides penning a column periodically for Quality Digest Daily, I also write for a number of other newspapers and publications. One of those columns for a paper distributed in Michigan and neighboring states is entitled, “Retired… (and lovin’ it).” But here’s the dilemma. The more I talk to people…
H. James Harrington
In the first column of this three-part series, I reviewed an interview that was conducted in 1988 with F. James McDonald, president of General Motors. In this interview he explained what GM was doing to improve quality and customer satisfaction. Typical activities that GM was involved in during…
How unique is unique? The answer to this riddle is central in determining which work breakdown structure (WBS) methodology most accurately explains project deliverables and how they should be estimated, controlled, and completed. The quality strategy used to segregate and decompose WBS…