All Features
Jeff Bibee
T
he complex geometries of prosthetics, implants, and specialty medical screws can be measured using typical measurement equipment with only limited success. Prosthetics and implants are becoming more and more complex and delicate. That’s why Stuckenbrock Medizintechnik , in Tuttlingen, Germany…
Georgia Institute of Technology
To improve customer satisfaction, enhance the quality of services and reduce costs, Peach Regional Medical Center has worked with the Georgia Institute of Technology to adopt process improvement techniques traditionally used by the manufacturing industry. Already, Peach Regional Medical Center’s…
Steven Wachs
The purpose of using control charts is to regularly monitor a process so that significant process changes may be detected. These process changes may be a shift in the process average (X-bar) or a change in the amount of variation in the process. The variation observed when the process is operating…
Knowledge at Wharton
The financial services sector has been a laggard in adopting lean tools and practices, perhaps because of their manufacturing origins. But those attitudes are slowly changing. As more banks discover the benefits of lean operations—such as lower costs, fewer errors, faster cycle times and far…
Michael Jovanis
Quality and IT executives alike face increasing pressure to implement technological solutions that allow the highest level of holistic control and oversight concerning the quality of their operations. This pressure is compounded by the current economic climate in which companies face constant…
Denis Leonard
Whether it’s employee or customer satisfaction, or product and service quality issues, do you really know what’s happening in your organization? What are you currently doing, or being directed to do, that doesn’t make sense and makes you feel like you are going around in circles? Yet these are…
Gain sharing and lean Six Sigma are highly complementary systems that are mutually reinforcing. While both efforts are excellent by themselves in improving productivity, quality, and a variety of other measures, they are much more powerful together. Both systems are based on the principles of…
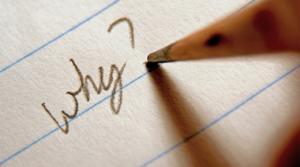
Stewart Anderson
The 5 Whys is a well-known root cause analysis technique that originated at Toyota and has been adopted by many other organizations that have implemented lean manufacturing principles. Unlike more sophisticated problem-solving techniques, the 5 Whys doesn’t involve data segmentation, hypothesis…
Joe Calloway
Right now there are potential customers for your business trying to decide whether or not to choose you. Unfortunately, most of them can’t see much difference between you and your competition. You’ve all got good quality products or services. You all seem to have competent, helpful people. It all…
Raissa Carey
Just as many industry sectors have been experiencing this year, the machine tools industry has seen a slow period in consumption and distribution of manufacturing technology.
Manufacturing technology consumption data is relevant because it provides a reliable economic indicator of how…
Davis Balestracci
Almost everyone celebrates something during the winter solstice—Christmas, Hanukkah, Kwanzaa, etc.—which inevitably includes gift exchanging. Following are some suggestions that run the gamut from technical to personal growth to just plain entertainment.
Videos/DVDs
There is a “quality”…
Aditya Bhalla
The Six Sigma journey of many organizations has morphed into “lean Six Sigma” during the past couple of years.
While the fusion of two methodologies has yielded benefits, it has also spawned a number of urban legends on the context and relevance of combining the two methodologies.
What…
The Un-Comfort Zone With Robert Wilson
“H
ola!”
“Hola. ¿Qué tal?”
“Bien. ¿ y tu?”
“Bien.”
Paul and I were 16 years old and had taken Spanish for a year. We called each other every night on the phone and spoke to each other in our new language. More than anything, we wanted to test our skill with a real Spanish-speaking…
Tim Leary
Story update 11/23/2010: A paragraph was added to the end of this case study to reflect the current state of the company's quality initiatives.
Acme Technology Services (not their real name) is a privately-held provider of technology-enabled business solutions. Acme’s retail software division…
David C. Crosby
Is anyone performing total quality management (TQM) anymore? MIL-Q-9858A? Total cost of quality (TCQ)? Pert planning? Are there any one-minute managers around? Pareto? What about “up the organization?” Value analysis? Quality is free? They were all big things—in their day.
We in the quality…
Stacey Corbin
You just finished your audit, and your registrar has handed you a brand-new certificate. Now, what do you do to make sure everyone knows about it? Most likely you’ll send an e-mail out to the entire company, prepare a press release, post an announcement on your web site, and so on. But sometimes,…
Michelle LaBrosse
We all have one hiding over there in the groan zone. It’s the unfinished project that lives in a strange sort of limbo. As Nassim Nicholas Taleb reminds us in The Black Swan (Random House, 2007), the longer a project goes unfinished, there is an exponential increase in the time to finish the…
Chet Marchwinski
Ihave had a big smile on my face for much of the last month because I’ve had the opportunity to visit progressive organizations on three continents to look at their efforts to create lean value streams.
Walking through any process, good or bad, seems to put a smile on my face for one of two…
Denise Robitaille
T
was the night before Christmas and all through the plant
Not a technician was stirring, no quality rants.
Performance charts were pinned to the cork board with care,
In hopes that, their progress, people would share.
The micrometers were nestled, all snug and encased
Protected from…
Jay Arthur—The KnowWare Man
After a meal at a local Chinese restaurant, my fortune cookie said, “If you keep too busy learning the tricks of the trade, you may never learn the trade.” When I think about how this applies to Six Sigma, it seems obvious that far too much Six Sigma training is dedicated to the tricks of the…
Cathy Sunshine
The only thing worse for companies than making bad decisions is having a deeply flawed decision-making process. Every business leader faces stressful situations that require immediate action, but the final choices can often by tainted by a destructive trio of hubris, arrogance, and denial. …
Eric Clower
The economic downturn has caused heartache, sleepless nights, fatigue, and excessive stress for many people at all levels of most companies this past year. It was no different for me. The company I work for (an aerospace component manufacturing and repair company) started seeing the downturn in…
Michael Raphael
The year 2009 contains two significant anniversaries within the scientific community: the bicentennial of Charles Darwin’s birth and the 150th anniversary of the publication of his groundbreaking book On the Origin of Species. To honor these milestones, the National…
Davis Balestracci
The economy has become a convenient excuse on which to pin the blame for everything—especially job losses. Well, in the case of quality positions, yes… and no.
A sobering thought: Will the Pareto principle (the 80/20 rule) inevitably apply to the quality profession? I think so. It’s time to “…
BSI
With security breaches on the rise, protecting your organization’s confidential and valuable information assets is one of the most important safety measures your organization can take. The issues surrounding information security involve more than just hackers and malicious software; they can…