‘Why Deming? Why Now?’... Why the Need for a Different ‘Method’
During the early 1990s, I was president of the Twin Cities Deming Forum. I had a wonderful board whose members were full of great ideas. One member, Doug Augustine, was a 71-year-old retired Lutheran minister and our respected, self-appointed provocateur.
<em>Measures of Success</em>
In the foreword of Mark Graban’s book, Measures of Success: React Less, Lead Better, Improve More (Constancy Inc., 2018), renowned statistician, Donald J.
Why Variation Matters to Everybody
Quality and manufacturing practitioners are most familiar with the effect of variation on product quality, and this is still the focus of the quality management and Six Sigma bodies of knowledge.
Time to Ditch the Paper and the Spreadsheets
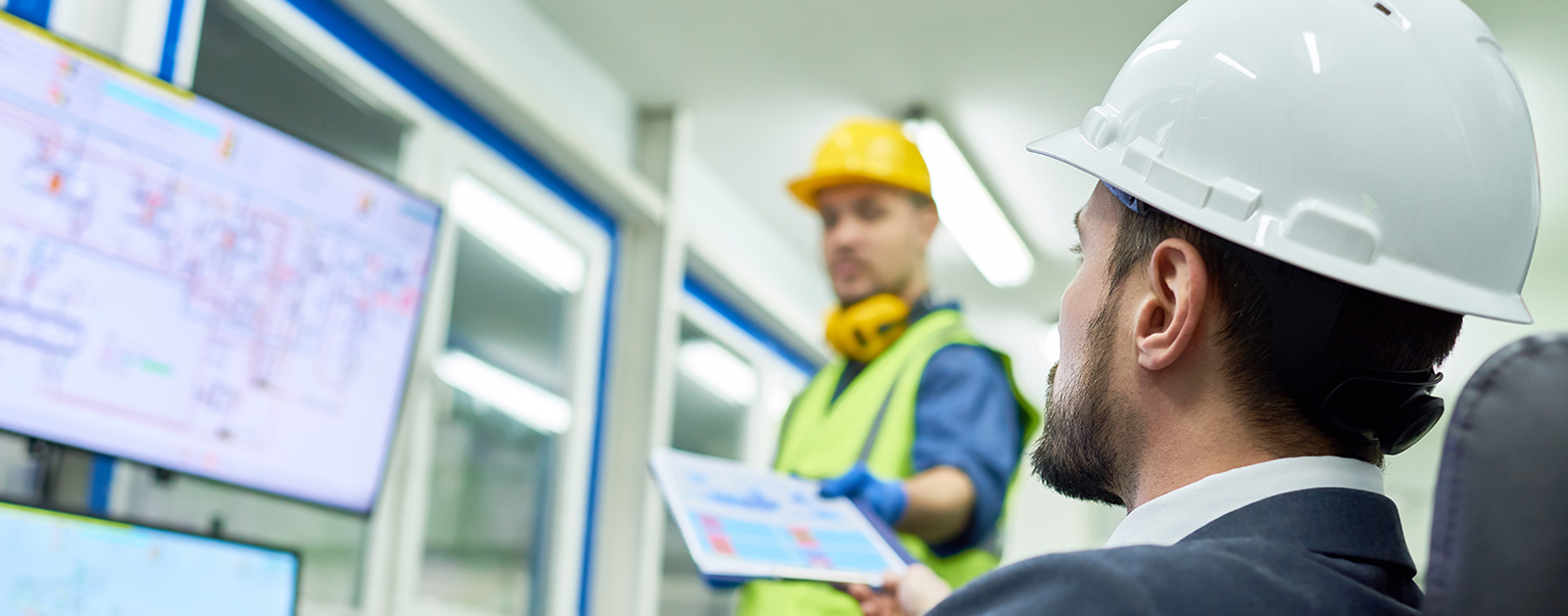
A few months back, I was reading a really good article from The Wall Street Journal, titled “Stop Using Excel, Finance Chiefs Tel
Road Trip USA: A Glimpse Inside the Car
The phrase, “Are we there yet?” has long been associated with boring summer road trips. However, a new study shatters that myth, as it shows that 69 percent of people say traveling to their destination is often as fun as the actual vacation destination.
Making Sense of Data: How to Go About It?
I recently got hold of the set of data shown in figure 1. What can be done to analyze and make sense of these 65 data values is the theme of this article. Read on to see what is exceptional about these data, not only statistically speaking.
Forecasts Before the Storm
The Atlantic hurricane season is now upon us, and the National Oceanic and Atmospheric Administration (NOAA) has just released its 2018 seasonal hurricane outlook which calls for a slightly above average season.
Predictable
Quality is related to processes.
It’s More Than the Mean That Matters
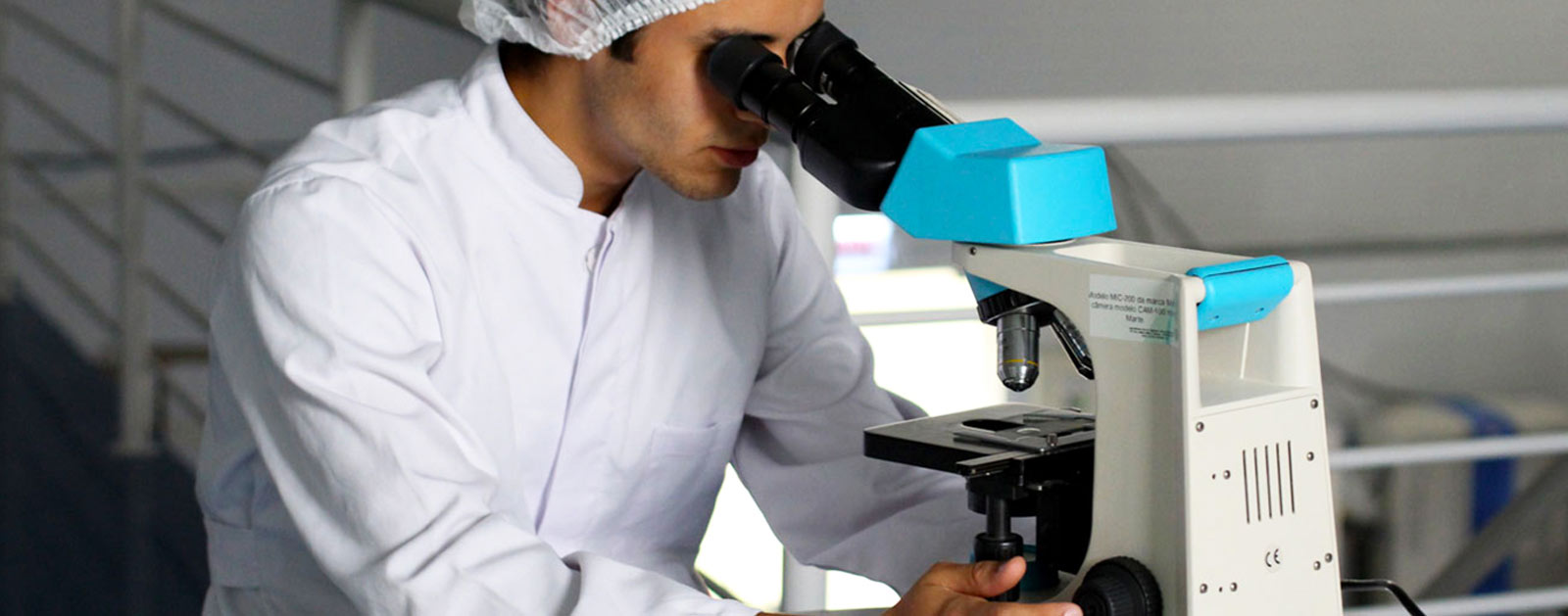
Confidence intervals show the range of values we can be fairly, well, confident, that our true value lies in, and they are very important to any quality practitioner. I could be 95-percent confident the volume of a can of soup will be 390–410 ml.
Pagination
- Previous page
- Page 15
- Next page