Content by Ryan E. Day
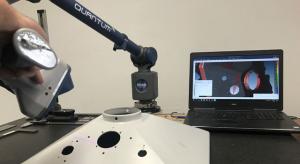
Wed, 07/17/2019 - 12:03
Industrial Custom Products (ICP) is a world leader in prototyping, developing, and manufacturing high-quality OEM and custom thermoformed and vacuum formed plastic components, as well as die cut and dieless knife-cut parts. What makes ICP unique…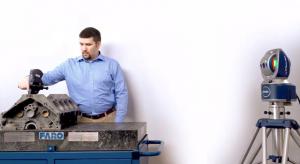
Wed, 06/19/2019 - 12:03
Midwest Metrology Solutions (MMS) is a company in Indiana that provides onsite precision measurement services using state-of-the-art metrology equipment and software. With an extensive knowledge of geometric dimensioning and tolerancing (GD&T),…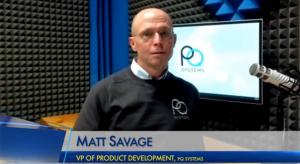
Tue, 05/28/2019 - 12:01
Current business conversation often focuses on data and big data. Data are the raw information from which statistics are created and provide an interpretation and summary of data. Statistics make it possible to analyze real-world business problems…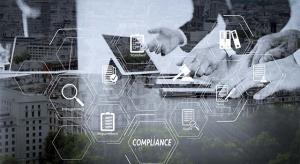
Tue, 05/21/2019 - 12:02
In the article, “ANSI’s Role in the Wide World of Standards,” (Quality Digest, March 12, 2019), we looked at where standards originate and how companies are involved in developing them. In this article, we’ll outline four points that can help your…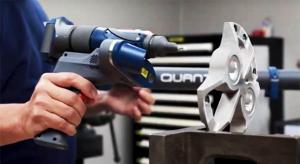
Wed, 05/15/2019 - 12:02
Brodie International provides liquid flow-meters and equipment for the petroleum and industrial markets. The company specializes in producing high-precision meters and valves that are used in the custody transfer of petroleum products.
The challenge…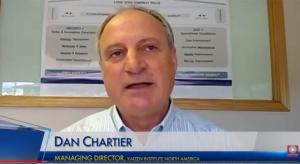
Tue, 05/07/2019 - 12:01
Most of us have heard of kaizen—continuous improvement of philosophy and methodology. In business, this involves all employees working to improve a company's processes to lean it out, to run with less waste. But most of us who are familiar with…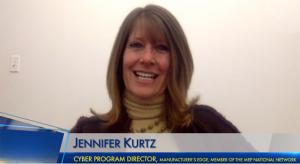
Thu, 05/02/2019 - 12:00
More and more, manufacturers are becoming the target of hackers, but what can they do about it, if anything? It seems every month, maybe even every week, we hear about some sort of data breach or cyberattack. Think Facebook, Google, and Marriott. As…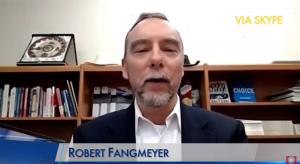
Fri, 04/19/2019 - 09:38
If you have worked in the quality field for anytime at all, you have probably heard of the Malcolm Baldrige National Quality Award—it’s the highest level of national recognition for performance excellence that a U.S. organization can receive. The…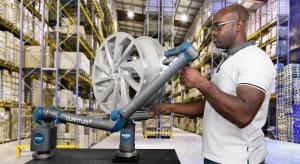
Wed, 04/17/2019 - 12:03
If your manufacturing organization is going to grow, you know you need an inspection solution beyond the capabilities of micrometers and calipers. You know you need to gather more data in a faster and more reliable manner. It’s time to invest in a…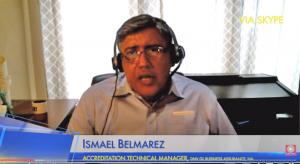
Tue, 04/16/2019 - 12:00
According to the International Labor Organization, around the world every day 7,600 people die from work-related accidents or diseases—that’s more than 2.78 million people every year. To address the issue, the International Organization for…