Content by Ryan E. Day
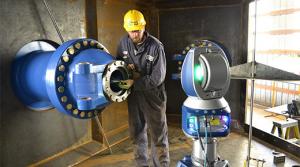
Tue, 09/19/2017 - 12:02
Sponsored Content
Headquartered in the little Hamlet of Deming, Washington, Canyon Hydro builds hydroelectric systems producing anywhere from 10 kilowatts up to 25 megawatts. In business for more than 40 years, Canyon Hydro has gained wide…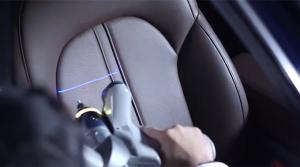
Solving the Inspection, Data-Gathering BottleneckTS Tech uses blue laser ScanArm technology from FARO to improve quality and throughput
Mon, 08/21/2017 - 12:02
Sponsored Content
For growth-minded organizations like TS Tech, global supplier of automobile seats and interiors, “the way we’ve always done it” is rarely good enough. As a tier-one supplier to major automotive OEMs, TS Tech always has an eye out…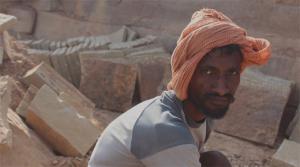
Mon, 08/14/2017 - 12:01
What do cocoa, socks, and smartphones have in common? If you guessed risk of slavery in the manufacturing supply chain, you are correct. Does your organization have an international supply chain? Then it’s at risk. What are you doing to address the…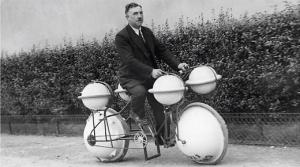
Thu, 08/10/2017 - 12:03
Innovation within industry is a must to improve processes, products, and customer experience. Although some innovations, like Amazon’s floating distribution center, seem implausible, other sci-fi technology is already revolutionizing and redefining…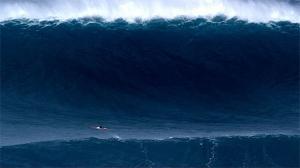
Thu, 07/13/2017 - 12:03
If necessity is the mother of invention, disruption is the mother of re-invention. But what do the terms “disruption” and “reinvention” really mean? Shane Cragun and Kate Sweetman tackle both questions in their book, Reinvention: Accelerating…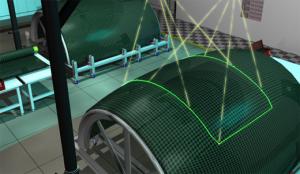
Mon, 06/19/2017 - 12:02
Sponsored Content
Building airplanes and spaceships poses some of the most unique engineering and manufacturing challenges mankind has ever encountered. Fortunately, you don’t have to build rockets to benefit from rocket science. Manufacturers of…Thu, 06/01/2017 - 12:03
I remember my first trip to Michigan in 2012. I was covering the Ford Motor Co.’s annual Trend Conference and had the opportunity to meet Alan Mulally, who gave a compelling presentation explaining the vision, strategy, and implementation of the…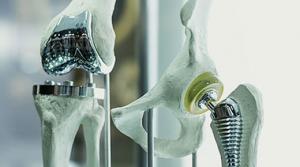
Tue, 05/30/2017 - 12:02
Sponsored Content
Founded in 1927 to produce aluminum splints—cutting edge at the time—Zimmer Biomet is a medical device company commanding second place in the entire world’s overall orthopedic market share. The organization’s stated purpose is to…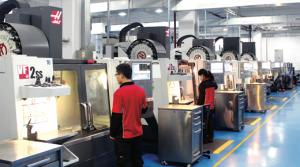
Tue, 05/16/2017 - 12:03
During the 1950s, W. Edwards Deming championed quality management philosophies that helped Japan develop into a world-class industrial center. In 1954, Joseph M. Juran was invited to lecture by the Union of Japanese Scientists and Engineers. His…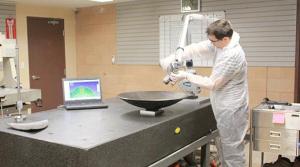
Mon, 05/15/2017 - 12:01
Sponsored Content
Everyone in manufacturing has heard about the fantastic properties of composite materials, but if you’re not involved in satellite communications (SATCOM), you’ve probably never heard of Eclipse Composites. If you are into SATCOM…