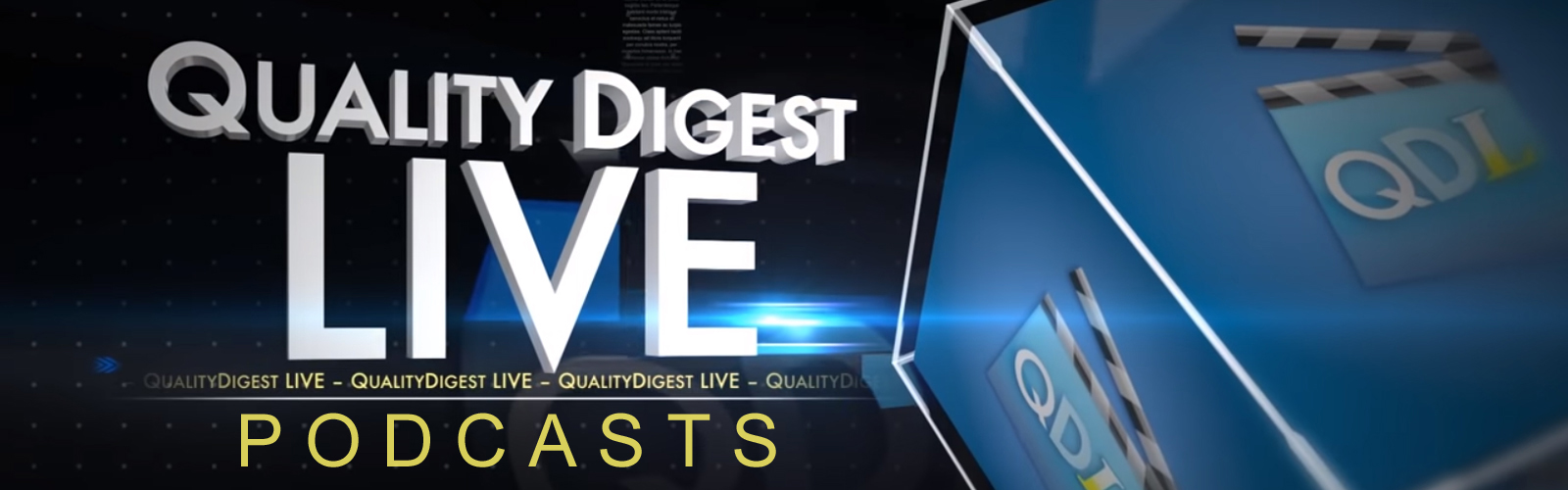
According to the International Labor Organization, around the world every day 7,600 people die from work-related accidents or diseases—that’s more than 2.78 million people every year. To address the issue, the International Organization for Standardization (ISO) has developed a standard, ISO 45001 “Occupational health and safety management systems—Requirements,” that provides organizations with a framework to improve employee safety, reduce workplace risks, and create better and safer working conditions all over the world.
Published in March 2018, ISO 45001 replaces OHSAS 18001. Companies must migrate to the new standard by March 2021. ISO 45001 is an international standard, ensuring enhanced compatibility with other standards, such as ISO 9001 and 14001. This makes it easier to implement and integrate to a management system, giving increased value for users.
A common question that arises with this and other ISO standards concerns the fact that because they are essentially process frameworks, how does one draw the connection between the framework—such as ISO 45001—and the actual nuts and bolts of one’s organization? How does one translate the guidance from clauses to, for example, lockout/tagout procedures, or when wearing steel-toed shoes should be required, or a hard hat?
…
Add new comment