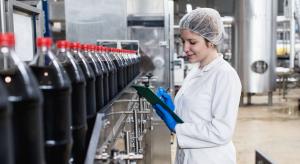
Wed, 09/30/2020 - 12:02
In order to best illustrate how enterprisewide SPC software can help address shop-floor problems and then funnel the captured data to the corporate level where strategic issues can be analyzed, here is a case study of a hypothetical manufacturing…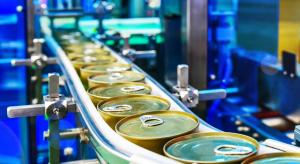
Mon, 09/28/2020 - 12:01
If you're involved in business you know: Strategy matters. Your strategies guide you to reach your objectives. Behind every successful business are purposeful strategies. Then again, as Alvin Toffler said, “The absence of strategy is fine if you don…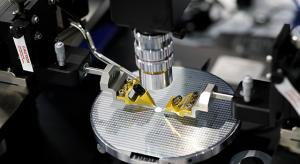
Thu, 07/30/2020 - 12:03
Every so often an event, invention, or idea is so momentous it changes the face of entire industries. In some ways, the global response to Covid-19 has been such an event. In the case of metrology, however, it has only underscored that the…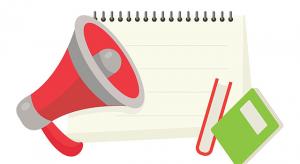
Fri, 06/26/2020 - 18:07
Writing a press release is easy. Writing a great press release takes some thought. And great press releases can draw more potential customers into your sphere of influence. Fortunately, writing great marketing copy isn’t all that complicated.…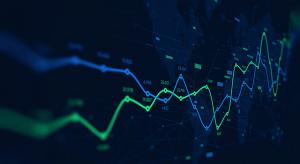
Tue, 06/23/2020 - 12:01
An organization can achieve great results when everyone is working together, looking at the same information generated from the same data, and using the same rules. Changes can be made that affect a company’s bottom line through operational…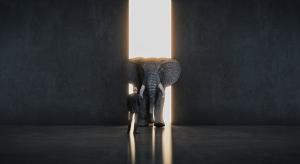
Mon, 06/22/2020 - 12:03
It’s no secret that manufacturing companies operate in an inherently unstable environment. Every operational weakness poses a risk to efficiency, quality, and ultimately, to profitability. All too often, it takes a crisis—like Covid-19 shutdowns—to…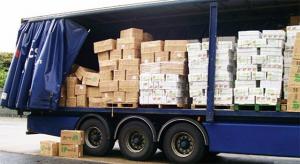
Tue, 06/02/2020 - 12:03
The Covid-19 pandemic is disrupting business across the globe, and supply chains are being stressed to their limits by sudden and drastic increases in online commerce. As organizations strive to continue delivering physical product, the industrial…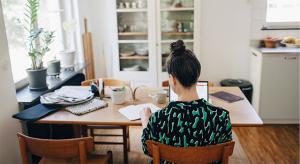
Wed, 05/13/2020 - 12:03
As shelter-in-place orders make work-from-home (WFH) the new normal, some organizations are struggling with the transition to working as a remote team. But there are companies that have been doing so for quite some time, and we can benefit from…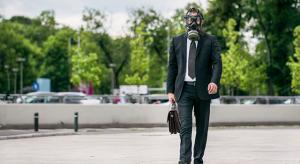
Thu, 04/02/2020 - 12:03
Although Covid-19 shelter-in-home edicts usually use the terms “essential” and “nonessential,” most business owners think of doing business as essential for survival. Many organizations don’t have the resources to temporarily suspend business. They…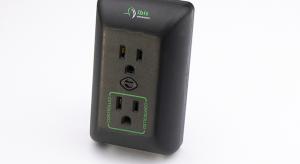
Tue, 03/31/2020 - 12:03
The internet of things, or IoT, is a phenomenon that merges real-life devices with online control. Think smart home systems or maybe the FordPass Connect app. The manufacturing industry has already begun to leverage this idea to monitor heavy…