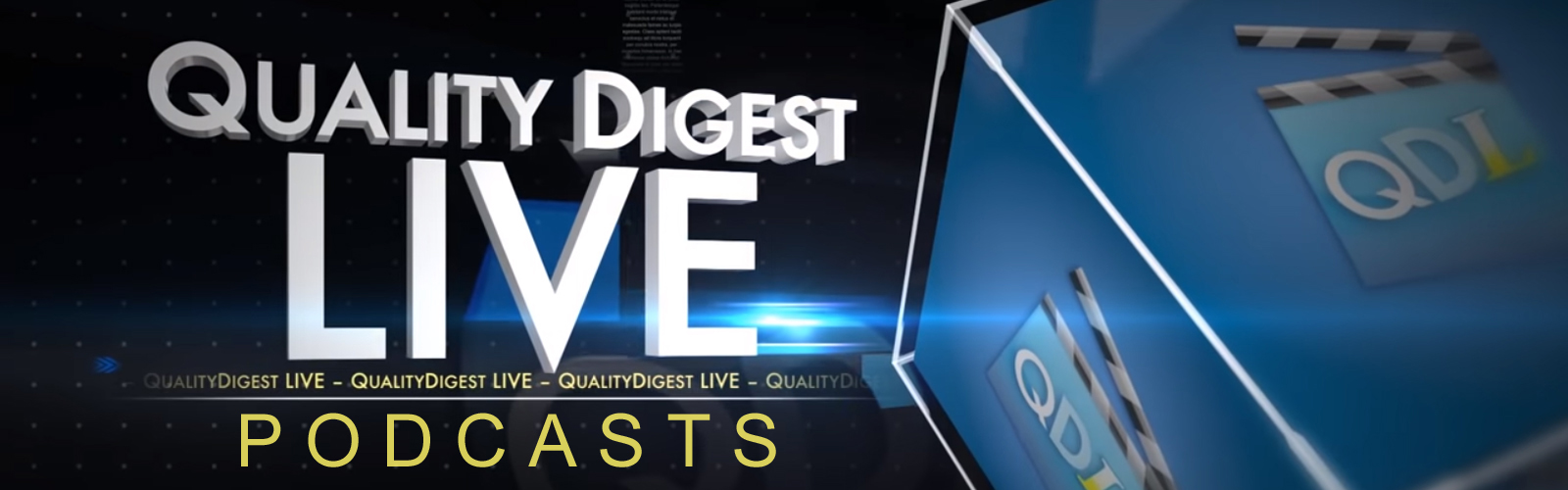
If you have worked in the quality field for anytime at all, you have probably heard of the Malcolm Baldrige National Quality Award—it’s the highest level of national recognition for performance excellence that a U.S. organization can receive. The award focuses on performance in five key areas and it is not easy to achieve the Baldrige award.
The current criteria are very thorough, and implementation is all-encompassing. As you might imagine, the audit is also very thorough. Now, when most people hear, “Baldrige program,” what they think of is, “Baldrige award.” But there's a lot more to the Baldrige Program and it goes way beyond just the award.
“We are just about ready to celebrate our 2018 Baldrige award recipients in a couple weeks,” says Robert Fangmeyer, Director of the Baldrige Performance Excellence Program at the National Institute of Standards and Technology. “On April 7, 2019, we will have our annual awards ceremony, the 31st award ceremony for the Baldrige award, and we will be honoring five organizations from four different sectors. That will be followed by our quest for excellence conference which runs from Monday to Wednesday.”
…
Add new comment