All Features
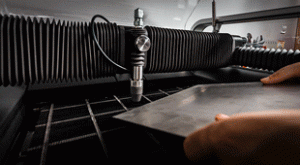
Nisan Lerea
Quality assurance and quality control (QA/QC) are a continual part of any manufacturing process. No matter how many times your factory has executed the same procedure, you must regularly perform quality checks to maintain the same quality level of your process. Quality control on a manufacturing…
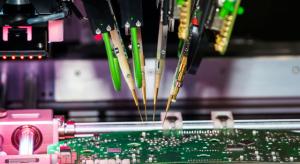
Emily Newton
The demand for printed circuit boards (PCBs) will only increase until a superior technology comes of age. The global market for PCBs could rise to $72.3 billion by 2026. PCBs have become essential everywhere, from infrastructure to consumer products.
The overwhelming demand for PCBs for the…
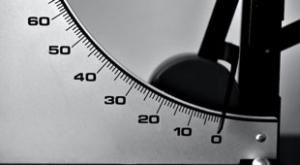
Bryan Christiansen
An important part of production is to carefully monitor and control temperature, speed, volume, weight, or mass. To ensure these measurements are always accurate, manufacturers need to calibrate their equipment and instruments regularly.
Devising a proper equipment calibration schedule can be a…
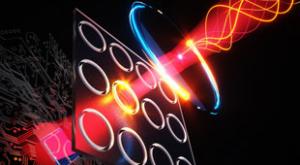
David L. Chandler
Terahertz radiation, with wavelengths that lie between those of microwaves and visible light, can penetrate many nonmetallic materials and detect signatures of certain molecules.
These handy qualities could lend themselves to a wide array of applications, including airport security scanning,…
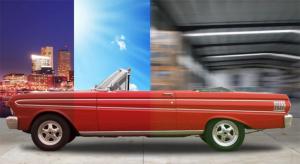
Tim Mouw
Metallized substrates such as two-piece metal packaging are expensive to produce, and they make print color-control challenging. Although many in the metal decorating sector are hesitant to embrace color measurement, it’s the fastest, most accurate, and cost-effective way to produce consistent…
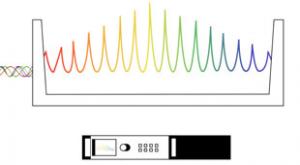
NIST
An improvement to a Nobel Prize-winning technology called a frequency comb enables it to measure light pulse arrival times with greater sensitivity than previously possible—potentially improving measurements of distance along with applications such as precision timing and atmospheric sensing.
The…
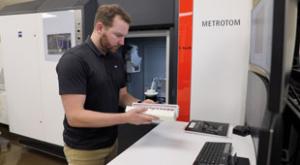
S. Heather Duncan
A new deep-learning framework developed at the U.S. Dept. of Energy’s Oak Ridge National Laboratory is speeding up the process of inspecting additively manufactured metal parts using X-ray computed tomography, or CT, while increasing the accuracy of the results. The reduced costs for time, labor,…
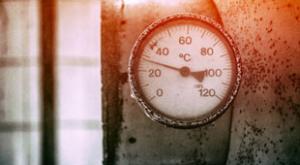
Elizabeth Benham
Calling all teachers, parents, and students. It’s easy to learn the metric system—or, as it’s more formally called, the International System of Units (SI). Explore these top 10 tips for teaching the SI. Let’s begin the countdown with....
10. Make it fun!
Integrating metric measurements into play…
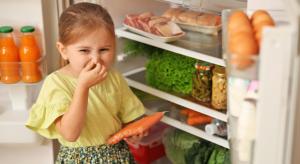
Mara Strenger, Svenja Kloss, Markus Schmid
When looking in the fridge, you notice a package of minced meat sitting at the back of one of the shelves, totally forgotten. A check of the best-before date reveals it had expired two days earlier. Like so many consumers, you feel an internal struggle emerging: risk food poisoning or discard a…
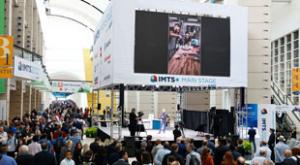
Mark Hembree
Many trade shows have disappeared or diminished in recent decades—but not the International Manufacturing Technology Show, a biannual event held every even-numbered year in Chicago, this year from Sept. 12–17. In its 33rd year, IMTS was of sufficient scope to take up nearly half of McCormick Place—…
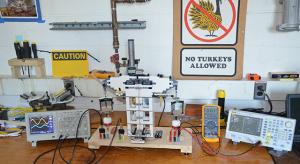
Leon Chao
I am 100 percent a millennial (lol), which—according to the Merriam-Webster dictionary—means I’m a “person born in the 1980s or 1990s.” To me, being a millennial means belonging to a cultlike group within a large population of present-day wannabe-adults for whom seemingly arbitrary words like…
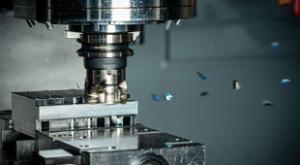
Bryan Christiansen
CNC (for computer numerical control) machines have made manufacturing easier, faster, and more precise. Supported by the development of IoT technology, the CNC machine market is set to experience significant growth. With that in mind, this seems like a great time to discuss the intricacies of CNC…
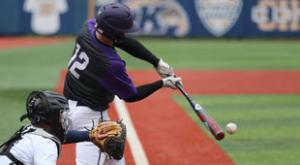
Mark Hembree
‘Anyone can hit a home run if they try,” said the great Ty Cobb at the end of the deadball era as Babe Ruth rose to fame in the 1920s. Cobb was unimpressed by Ruth, the Sultan of Swat. “It’s a brute way to approach the game.”
In 2019, Major League Baseball (MLB) seemed to prove Cobb’s point as big…
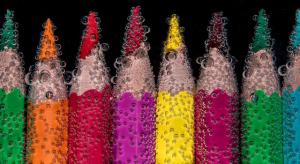
Tim Mouw
According to autolist.com, more than 80 percent of cars produced today are white, black, or some shade of gray. It’s not necessarily because bright and bold colors are more difficult to produce and match than their grayscale counterparts. They just take longer to get through the inspiration and…
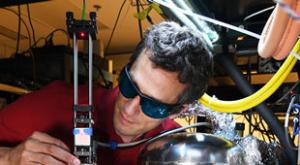
NIST
A novel, quantum-based vacuum gauge system invented by researchers at the National Institute of Standards and Technology (NIST) has passed its first test to be a true primary standard—that is, intrinsically accurate without the need for calibration.
Precision pressure measurement is of urgent…
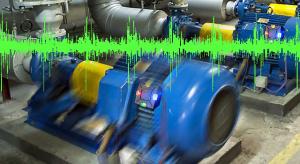
Prashant Kapadia
Workforce scarcity and remote employment made it challenging to maintain industrial machinery during and after the Covid-19 epidemic. With the global industrial automation market expected to nearly double in the next six years, maintaining an increasing number of assets will result in more…
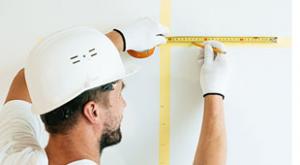
NIST
You need to measure length accurately to do things like make a dress, build a house, survey a plot of land, or determine if the home team made a first down on the football field. These length measurements and many others are often made with the help of a measuring tape. The major companies that…
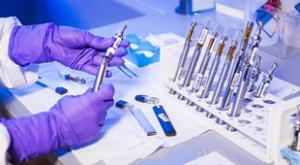
Mike John
This article has been republished with permission from Medical Plastics News.
While ISO 13485 sets the standard for quality management systems (QMS) in medical device manufacturing, metrology is often treated as an afterthought and used simply to validate products and detect defects at the end of…
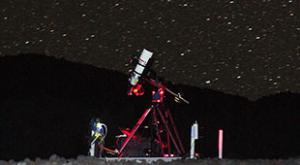
Steven Brown
One of the unexpected rewards of working at NIST has been the opportunity to see other disciplines through the NIST prism of measurement science and standards. By working with NASA scientists, astronomers, oceanographers and geologists, I’ve had the opportunity to witness the lives of scientists in…
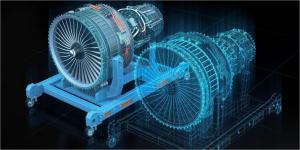
engineering.com
Unlike a biological or identical twin, a digital twin does not have a universally accepted definition. In application, a digital twin will mean different things to different industries. On an assembly line, a digital twin of a robot may look identical to the physical robot, especially if it is…
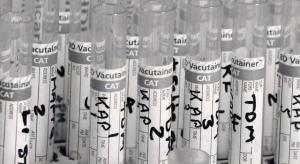
Kari Miller
Quality management is essential to the growth and performance of any organization. It’s a valuable resource in the effort to ensure that products and services satisfy the highest quality requirements and deliver positive customer results.
Pharmaceutical manufacturers must ensure that the…
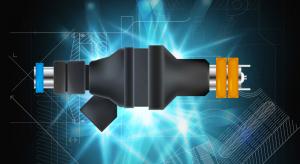
Samuel Lesko
The manufacturing and production industries have rapidly evolved during the past 10 years, faced with significant challenges both in finding resources to run production and in manufacturing under tighter tolerances for surface texture and 3D feature dimensions.
The strict tolerances required in…
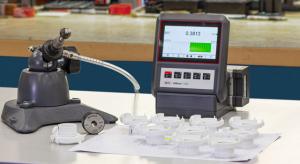
Anil More
Air gauge measuring devices have given highly reliable and precise measurements since the 1940s. As the name suggests, an air plug or air ring gauge is a gauging probe that uses metered air under controlled pressure to sense the back pressure generated as it impinges on the surface of the part…
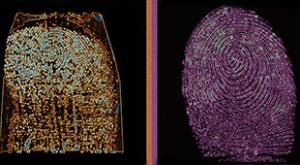
Greg Fiumura
After wading through airport security and a turbulent trans-Atlantic flight, the last thing I wanted was more friction arriving back in the USA. However, I was looking forward to using Global Entry, a voluntary Department of Homeland Security program that, after a thorough background check, allows…
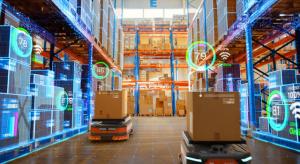
Albert Rees, Joe Vernon
The pandemic had many consequences for manufacturing companies, the most prevalent being supply chain disruption. In light of these disruptions, it is paramount that organizations establish robust and reliable operations to ensure productivity targets are met—especially as consumer demands continue…