In the healthcare sector, precision isn’t just a requirement. It’s a necessity where the margins for error are perilously thin, and the consequences of inaccuracy can be grave. At the heart of this precision lies the unassuming yet critical load cell, a device whose reliability is foundational to…
All Features
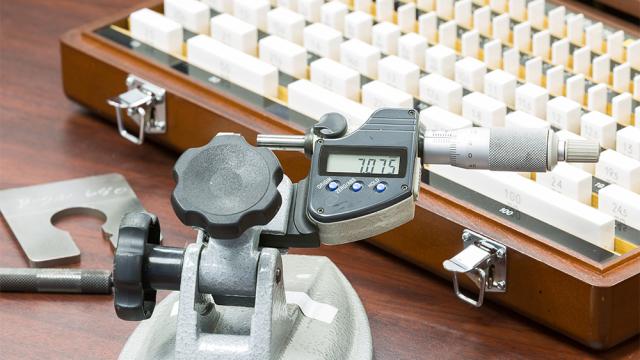
Henry A. Zumbrun
Calibration, a critical aspect of maintaining equipment precision, involves more than routine checks. It’s a complex decision-making process in which quality, lead time, and price are weighed. The belief that you must compromise on one to excel in the others is a common misconception in the…
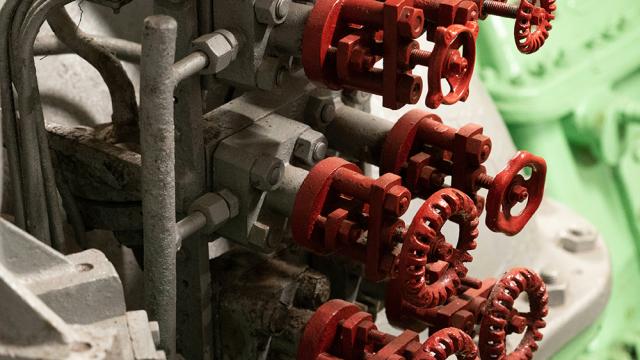
Douglas C. Fair, Scott A. Hindle
In less than two months we will celebrate the 100th anniversary of the invention of the control chart, a tool most often associated with statistical process control (SPC). Considering SPC from our modern perspective made us ask, “Is SPC still relevant?”
It’s a question asked within the purview of…
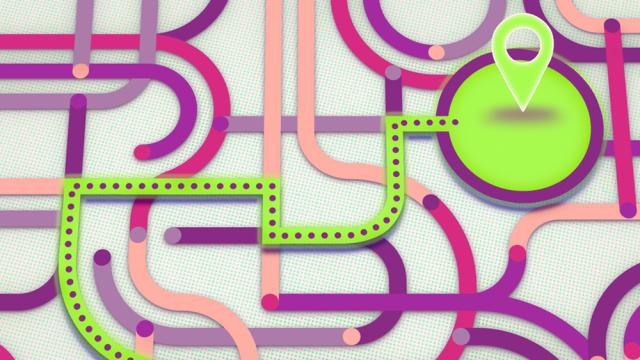
Adam Zewe
If a robot traveling to a destination has just two possible paths, it only needs to compare the routes’ travel time and probability of success. But if the robot is traversing a complex environment with many possible paths, choosing the best route amid so much uncertainty can quickly become an…
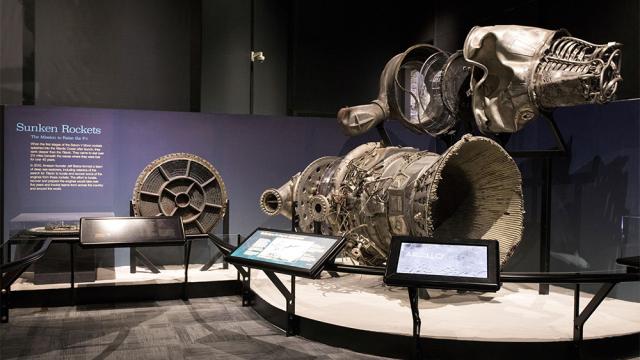
Adam Creuziger
Like many people, as a child I had dreams of flying into space as an astronaut. That interest in aerospace and space exploration has continued throughout my life.
So when my colleague Tim Foecke, who was working at the National Institute of Standards and Technology at the time, invited me to…
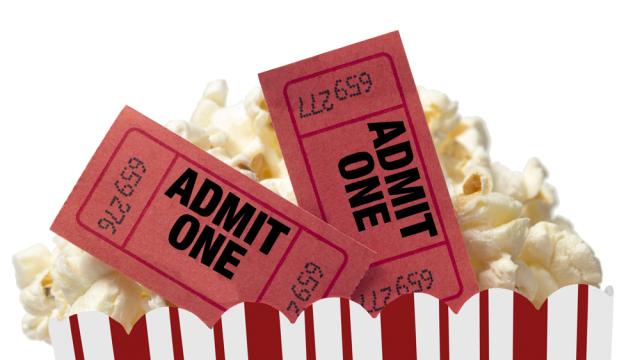
Ben P. Stein
Many critics and movie fans alike name 1981’s Raiders of the Lost Ark as one of the best films of all time. But watching the movie as a 12-year-old, I didn’t realize that it has what some consider to be a major flaw, pointed out in a 2013 episode of The Big Bang Theory.
As the argument goes,…
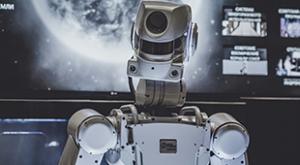
Matthew Greenwood
The next frontier for industrial digitization and automation is the convergence of artificial intelligence (AI) and machine vision.
AI-powered machine vision promises to transform the way industrial manufacturers conduct their business, according to experts at a recent webinar hosted by the…
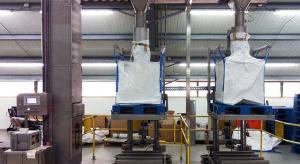
Del Williams
Manufacturers in the food and beverage sector continually seek methods to boost their operational efficiency and are prepared to invest in superior machinery when the expected returns justify the expenditure. However, the potential advantages of upgrading bulk bag filling systems are frequently…
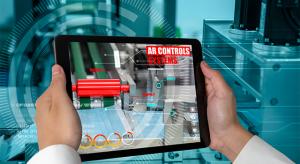
Jamie Fernandes-ETQ
Generative AI took the world by storm in 2023, from the classroom to the film studio, and the writer’s bench to the White House. Enterprises and creative industries worked to figure out how to leverage it in their operations, while classrooms and government entities struggled to govern its use.
In…
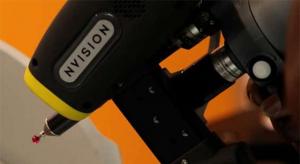
NVision Inc.
Air conditioning is hotter than ever—hot as in demand, a must-have, a comfort most of us want, and, with higher-trending temperatures generating heat-related health issues, one that many can no longer live without.
NVision, a leader in 3D noncontact optical scanning and engineering, has worked…
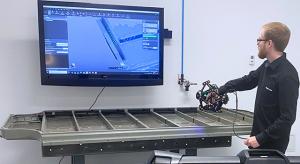
Patrice Parent
Battery trays are structural elements that enclose and safeguard the battery modules and their supporting electrical and thermal management systems. Battery modules must precisely fit into the battery tray, which must fit seamlessly within the vehicle's chassis.
Variations in tray dimensions can…
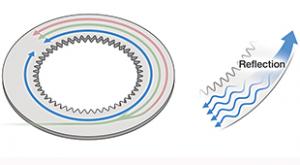
NIST
In research, sometimes the bumpy path proves to be the best one. By creating tiny, periodic bumps in a miniature racetrack for light, researchers at the National Institute of Standards and Technology (NIST) and their colleagues at the Joint Quantum Institute (JQI), a research partnership between…
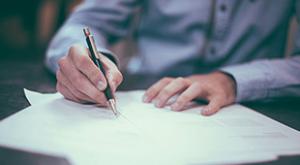
Donald J. Wheeler
Clear thinking and simplicity of analysis require concise, clear, and correct notions about probability models and how to use them. Here, we’ll examine the basic properties of the family of gamma and chi-square distributions that play major roles in the development of statistical techniques. An…
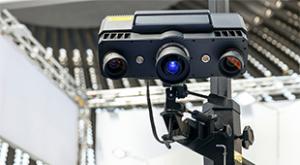
Miron Shtiglitz
The main benefit of deploying artificial intelligence (AI) for quality inspection is a significant improvement in defect detection. However, the data generated and stored by inspection systems have the potential to deliver additional benefits, including major improvements in yield.
Anyone working…
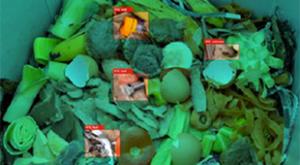
Silke von Gemmingen
Smart waste management is one of the core tasks within smart cities, i.e., those urban areas in which innovative technologies and data-driven solutions are used. They aim to improve residents’ quality of life, minimize environmental impact, and use resources more efficiently. Conserving resources…
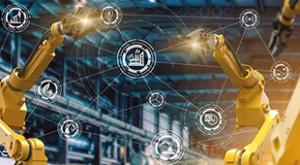
Creaform
End-to-end manufacturers are companies that lead products through the entire manufacturing process, from design to customer delivery. Unlike businesses that manufacture their products with a segmented manufacturing process, end-to-end manufacturers have complete control over the different parts of…
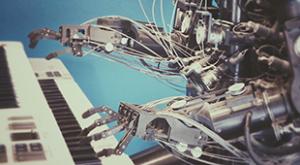
Eric Whitley
High-precision manufacturing is critical in industries where even the slightest deviation can lead to significant consequences. It encompasses processes that demand the utmost accuracy, often in sectors like aerospace, medical devices, and electronics. Precision is important due to its direct…
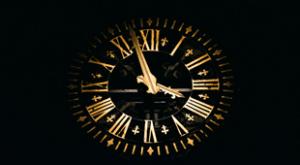
Andrew Novick
While people around the country are preparing champagne and getting ready to watch the ball drop on New Year’s Eve, I’m closely monitoring our clocks at the National Institute of Standards and Technology (NIST).
We actually monitor them every nanosecond of every day, not just on New Year’s Eve.…
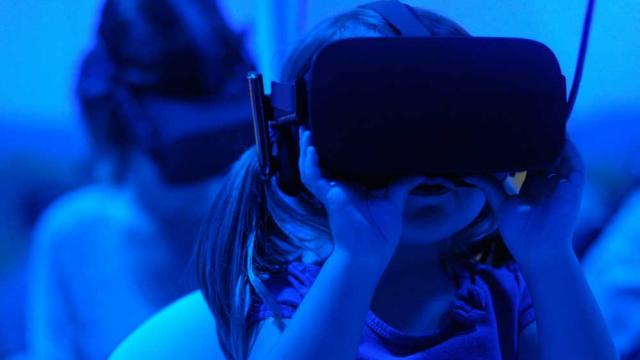
Jason Walker
As the manufacturing industry continues to grapple with labor shortages, potential shifts in government policies could further intensify these challenges in 2025. This heightens the urgency for manufacturers to meet demand while navigating an unpredictable future.
One area where this is…
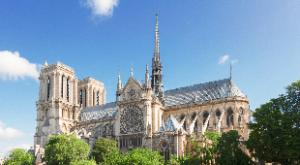
Industrial Inspection and Analysis
Unlike the traditional engineering process of designing a part, product, or component from the ground up, many times in life we need to start with an existing item and work backward to solve a problem. It’s a process known as reverse engineering, and it begins by obtaining accurate data about the…
Chris Caldwell
The quest to optimize equipment efficiency, ensure consistent quality, and lower operational costs while empowering a stronger workforce continues to permeate the industrial landscape. While challenges persist, the transformative potential that high-performance robotic automation is bringing to…
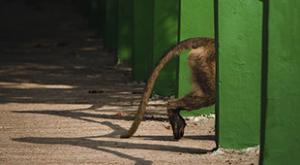
Donald J. Wheeler
When do we need to fit a lognormal distribution to our skewed histograms? This article considers the basic properties of the lognormal family of distributions and reveals some interesting and time-saving characteristics that are useful when analyzing data.
The lognormal family of distributions…
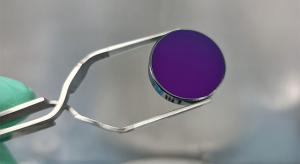
University of Vienna
In the field of high-performance mirrors, everyone chases the impossible: coatings with perfect reflectivity. In the visible range of wavelengths (i.e., between 380 nm and 700 nm), advanced metallic mirrors achieve reflectivities as high as 99%, which means 1 photon is lost for every 99 reflected.…
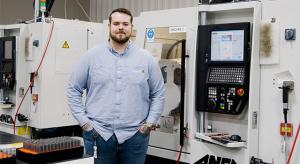
Russell Riddiford
Whether you use a lot of cutting tools or sometimes find yourself desperately lacking the right tool, you’ve probably considered making your own—or at least sharpening your worn tools. But how do you decide if taking tool grinding in-house is the smart decision? It’s a question GKN Aerospace Engine…
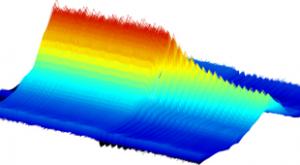
NIST
From monitoring concentrations of greenhouse gases to detecting Covid in the breath, laser systems known as frequency combs can identify specific molecules as simple as carbon dioxide and as complex as monoclonal antibodies with unprecedented accuracy and sensitivity. Amazing as they are, however,…